Driver’s view: Claas Cemos Automatic
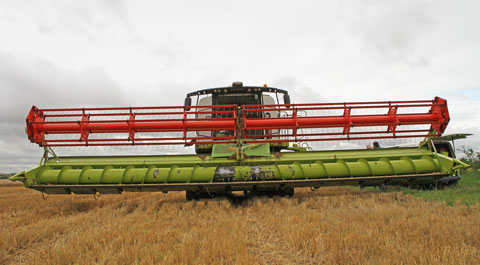
When it comes to technological changes – and the last few years have seen more than a few of them – it’s fair to comment that John Hawthorne is certainly prepared to give them a try.
Based at Flawborough, Notts, a mixture of owned and contract farming provides him with 1800ha (4500 acres) of arable ground on which he grows oilseed rape and wheat in about equal amounts.
Over the years he has been quick to adopt GPS tractor guidance, variable rate seed and fertiliser, nitrogen sensing and so on, so when Claas suggested he might wish to trial its new Cemos Automatic combine harvester controller there was little surprise in knowing he was keen to discover get what it had to offer.
“The combine harvester is a machine which needs to be set up carefully to achieve the best results in specific conditions,” he says. “And, while most operators will make adjustments for a crop say, at the start of the day, there are usually few further adjustments made as the day progresses and conditions change.”
The Cemos Automatic control system, which is an option for the company’s 700 Series combines, is a development of the Cemos system introduced by Claas a couple of years ago.
By making recommendations for certain setting changes within the combine the system offered the potential to maximise output, in respect of crop types and crop conditions.“We had our first Cemos system fitted to a Lexion 770,” he says.
“It was a useful aid which would suggest changes that could, for example improve throughput or sample quality. The onus, in the main, was on the operator to say ‘yes or no’ to a suggested change although, once made, the results could be compared with the previous settings.
Mr Hawthorne comments that one of the key advantages of the Cemos system was the encouragement it gave to operators to consider making changes during the day and help ensure the performance of the combine was maintained.
There was, however, one major input though which was not linked directly to the Cemos system and this was the cruise control which was activated by information supplied from the grain loss monitors and the returns monitor.
“There was clearly room for some improvements to be made which could not only instigate beneficial setting changes automatically but could also bring the cruise control into the equation,” he says.
Mr Hawthorne first encountered the Cemos system on a Lexion 770. “It was a useful aid which would suggest changes that could, for example improve throughput or sample quality.
The onus, in the main, was on the operator to say ‘yes or no’ to a suggested change although, once made, the results could be compared with the previous settings.
Mr Hawthorne comments that one of the key advantages of the Cemos system was the encouragement it gave to operators to consider making changes during the day and help ensure the performance of the combine was maintained.
There was, however, one major input though which was not linked directly to the Cemos system and this was the cruise control which was activated by information supplied from the grain loss monitors and the returns monitor.
“There was clearly room for some improvements to be made which could not only instigate beneficial setting changes automatically but could also bring the cruise control into the equation,” he says.
The Cemos Automatic control system, which is an option for the company’s 700 Series combines, is a development of the Cemos system introduced by Claas a couple of years ago.
By making recommendations for certain setting changes within the combine the system offered the potential to maximise output, in respect of crop types and crop conditions.
Driver’s Verdict
There is little doubt that Cemos Automatic has the potential to maximise the output of a combine and, to be fair, when you consider the cost of modern combines, it will be useful after all these years to have a system which enables them to achieve what they are designed to do. John Hawthorne
The arrival on the farm of a pre-production Lexion 780 (albeit with 770 decals) brought with it the new Cemos Automatic system for testing and appraisal – the system is designed to monitor performance and make changes automatically so that output is always maximised.
“In many ways, the system is a balancing act in that the sieve settings, the air volume, the returns’ percentage, the forward speed, the acceptable losses, the grain sample and all other key settings need to be juggled to produce an overall optimum combination,” explains Mr Hawthorne.
“And the system, after starting off with default settings in respect of crop type, weather and crop conditions, continues to try new settings and discover those which work to improve output.”
He adds that the system appears to learn as it goes along and continually fine tunes the operation during the day to accommodate changes in temperature, grain moisture, straw condition, and so on.
“There are four modes,” he says. “There is the ‘maximum throughput’ mode, for which the system makes settings to maximise the throughput of the crop; the ‘high threshing quality’ mode, which aims to produce the cleanest sample; the ‘fuel efficiency’ mode, which in essence means the speed control of the rotor which has an effect on straw quality; and then there is the ‘balance’ mode, which aims to provide the best of all worlds as permutations of the other mode settings.”
When combining, the Cemos Automatic display screen can be set to reveal the adjustments being made as the machine works. Some changes, he points out are clearly not favourable and revert to their previous stetting.
“Successful operation of the system depends on it receiving the right information from the sensors and making the correct degree of correction, should it be needed,” he says.
“When we first started in the oilseed rape, the grain loss monitors were clearly too sensitive and that led to the speed of the combine being reduced dramatically – to the point we switched into manual control. On one occasion in wheat, the system decided to close up the sieves too much with the result that there was so much grain being sent to the returns there was a big overload and the returns elevator drive was damaged.”
Mr Hawthorne believes that Claas currently has the Cemos Automatic about 85% right and is optimistic that the company’s specialists, who continue to work to update programmes, will produce a system which he looks forward to using.
“There is little doubt that Cemos Automatic has the potential to maximise the output of a combine and, to be fair, when you consider the cost of modern combines, it will be useful after all these years to have a system which enables them to achieve what they are designed to do,” he says.