Bedfordshire farmer fits combine with fire protection kit
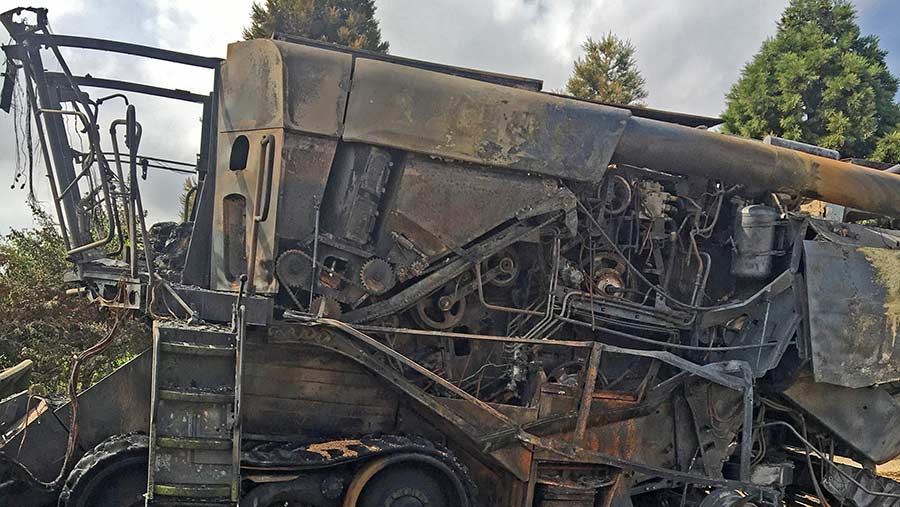
After losing 3ha of wheat, several rows of straw and a combine to fire, grower Simon Bath decided to protect himself for future harvests.
In addition to built-in fire safety features, he set about fitting a fire-suppression system to a new Lexion 750 TT.
Find out how to find a good system, how to install it and what the costs involve.
See also: Combine harvester fires: Why do they keep happening?
Farm facts: PC Bath, Roxton Park, Roxton, Bedfordshire
- Farming 400ha arable
- Cropping Wheat, oilseed rape (final year), barley, beans
The fire incident
By the time Simon Bath realised a fire had broken out in his combine, there was nothing he could do to stop it.
After glancing in the mirror and spotting flames flickering in the swath behind him, he quickly lifted the header and dashed to the edge of the field, hoping to save as much crop as possible.
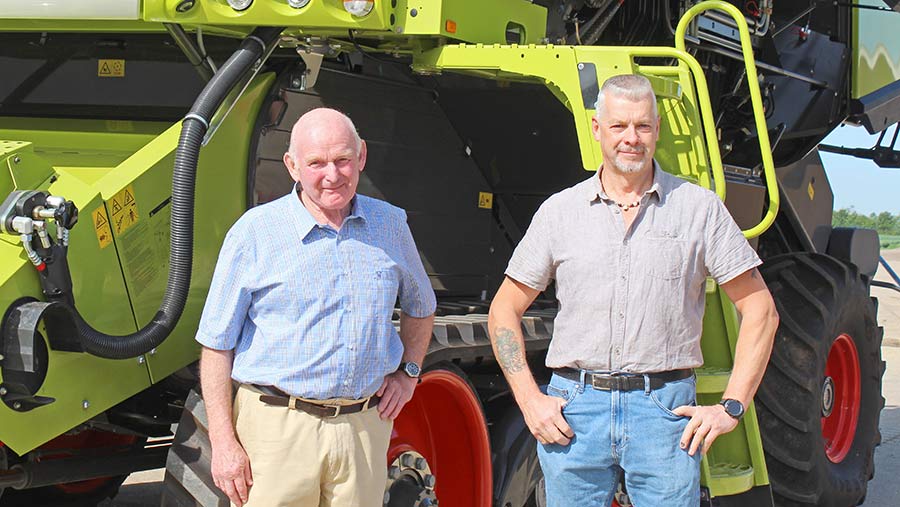
Simon Bath and Kevin Futter
But by the time he got there, the Claas Lexion 750 Terra Trac was engulfed. Gusts of wind were blowing the flames past the cab door too, so he had to wait for a lull before he could escape.
A fire crew arrived 20mins later – they had just finished dealing with a large stubble fire started by a baler a few miles away – by which time all they could do was work to contain the blaze.
Farm manager Kevin Futter, a farmworker and a neighbour also set to work with cultivators to prevent the fire spreading through the crop.
Three hours later, the combine had burnt out completely, taking about 3ha of wheat and several rows of straw with it.
All this took place on 24 July 2018, and with the bulk of harvest still to come, there was a fairly urgent need to source another machine.
Thankfully, the Baths’ dealer, Oliver Agriculture, stepped in and sent a demonstrator 750 Montana just three days later.
But keen never to see a repeat of this event, Mr Bath and Mr Futter decided their next combine should be as well protected as possible.
Fire-suppression system
The replacement machine – a brand-new Lexion 750 TT – has various design tweaks to prevent fire-friendly dust and chaff collecting, and Claas voluntarily fitted an additional system to automatically blow debris away.
This is connected to the combine’s built-in compressor and has jets positioned in the engine bay and above the transmission. It’s timed to deliver a stiff puff of air every time the unloading auger is pushed out.
Even so, the pair thought they should go a step further and fit a fire-suppression system to stifle any future blazes should they take hold.
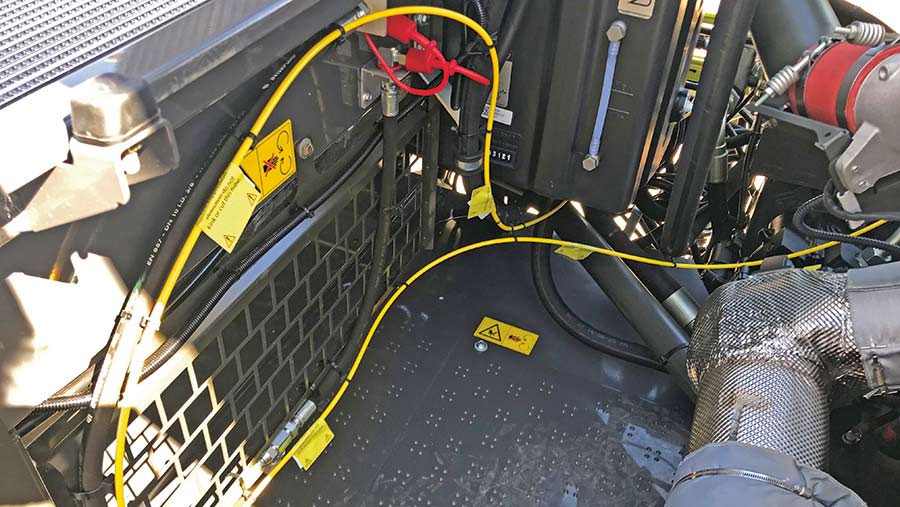
The fire detection tubing
The idea came largely from an early Firetrace device they had had on a Claas Dominator in the early 1990s. “It wasn’t particularly brilliant and used to leak fluid, but the concept was good, and they have come a long way since then,” says Mr Futter.
This original system was little more than a single tube running around the machine that was connected to an extinguisher and filled with pressurised fire suppressant.
When the pipe was exposed to excessive heat or a flame, it would burst and release the liquid in that area. If the flames had spread beyond this immediate area it was of less help, though.
Some of latest systems get around this problem by using separate lines for detecting and extinguishing the fire.
The detection tube is filled with a pressurised inert gas, and when this comes into contact with fire or temperatures of more than 200C, it ruptures.
The pressure of the gas in the system then drops rapidly, triggering the fire suppressant.
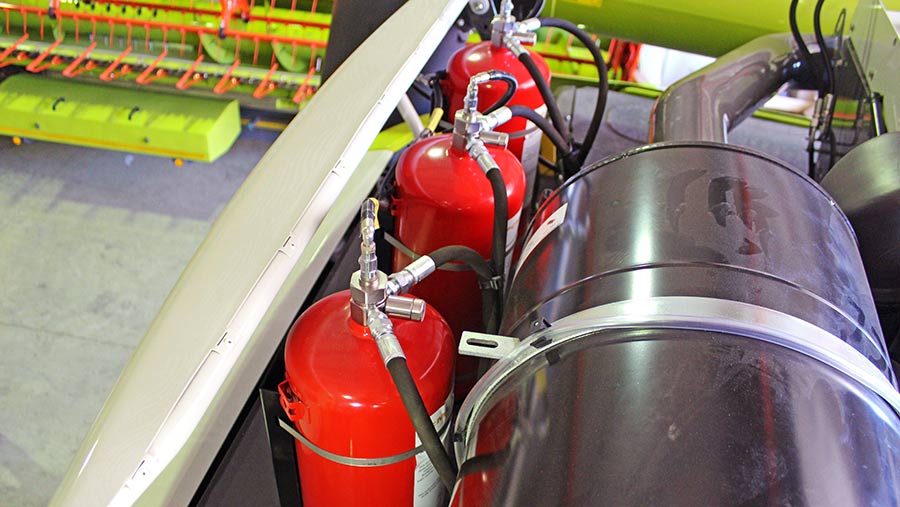
The extinguisher tanks
This surges through another network of pipes, with spray nozzles positioned in all the high-risk areas. These pipes are also fire resistant, so they will keep working when subjected to heat and flame.
These days, the main fire suppressant recommended for combine harvesters is monoammonium phosphate powder. This is because it will quickly snuff out almost all types of fire, such as fuel, chemical and electrical.
Foam is also sometimes added as a secondary suppressant, timed to release once the powder tanks are empty. As well as helping quash any remaining signs of combustion, it cools the area and prevents it reigniting.
Frontline machinery
- Tractors Challenger 765C, John Deere 6830 and 6820
- Combine Claas Lexion 750 with 9.3m header
- Cultivation kit Kverneland Stubble Finisher, Vaderstad Rexius Twin, Vaderstad Opus
- Drill Vaderstad Rapid
- Sprayer Househam Air Ride with 30m booms and 3,500-litre tank
- Fertiliser spreader Amazone ZA-TS Hydro Profis
- Telehandler JCB 541-70 Agri Super
Finding the right system
Mr Futter’s search for a company capable of installing such a system returned just two results: Firetrace, the maker of the original system they had in the 1990s, and a recent start-up called PCML Group.
Both companies prepared quotes, but Mr Futter preferred the system being offered by PCML Group.
This was largely because it could cover almost all areas on the machine at risk of fire with a single system, while Firetrace needed to fit two.
It was also offering a dual-powder and foam setup for less than Firetrace’s foam-only option. “This was the first system they’d installed on a combine, so they did give us a particularly good deal,” he says.
After putting pressure on Claas to make the machine more resistant to fire, Mr Futter also got some extra discount to cover the cost of installation. “To be honest, I think all manufacturers should fit devices like this from the factory.”
The quote for the Firetrace setup came in at £5,358 and PCML’s system was about £4,000, though this includes a healthy discount.
Installation
Mr Futter worked with Paul Townsend from PCML Group to make sure the system covered all the areas most at risk.
The cause of the fire on the last combine was never pinpointed, but Mr Futter reckons it could have been a high-pressure diesel or oil leak on the left side of the machine. “It seemed to start there and the fact that it spread so violently means it’s unlikely to have been dust and chaff,” he says.
“We blow the combine off with a hydrovane compressor every day, so there wouldn’t have been much debris there anyway.”
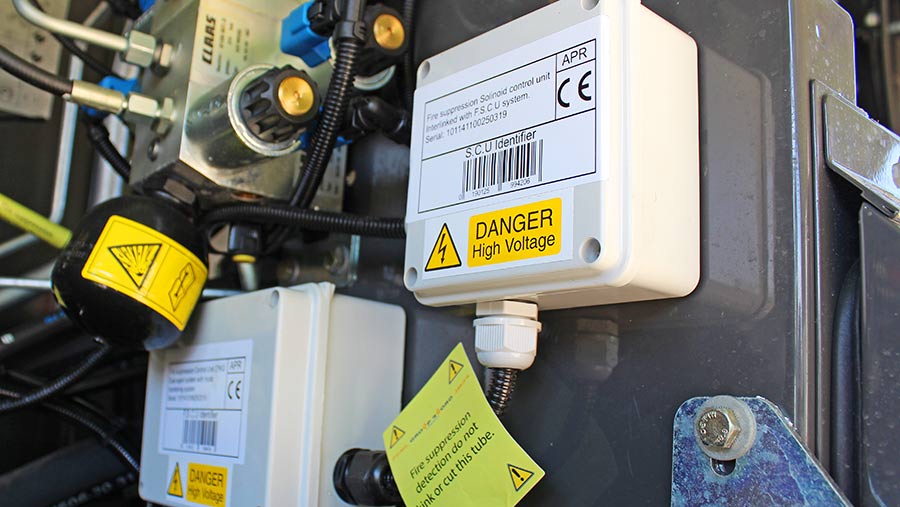
The fire suppression control unit
Most of the pipework runs around the engine bay, exhaust and cooling system, but there is fairly comprehensive coverage down the left-hand side too, where the bulk of the electrical and hydraulic systems are located.
The right side of the machine is at lower risk, so doesn’t have any detection tubing, but it does have one spray nozzle mounted high to cover the whole area.
There is also a single jet trained on the transmission – an area where Mr Futter has seen small, smouldering fires break out before.
In the cab, PCML fitted a trigger that allows the driver to activate the system manually. This unit acts as an alarm to inform the driver if the system has detected a fire.
When the system does go off, it releases the two 9kg tanks of powder first. When these have run out, a single 9kg tank of foam is released. It can be tricky to find a neat spot to mount the tanks, but the Lexion has a space just the right size behind the air cleaner.
There is also an automatic kill switch for the engine and a battery isolator.
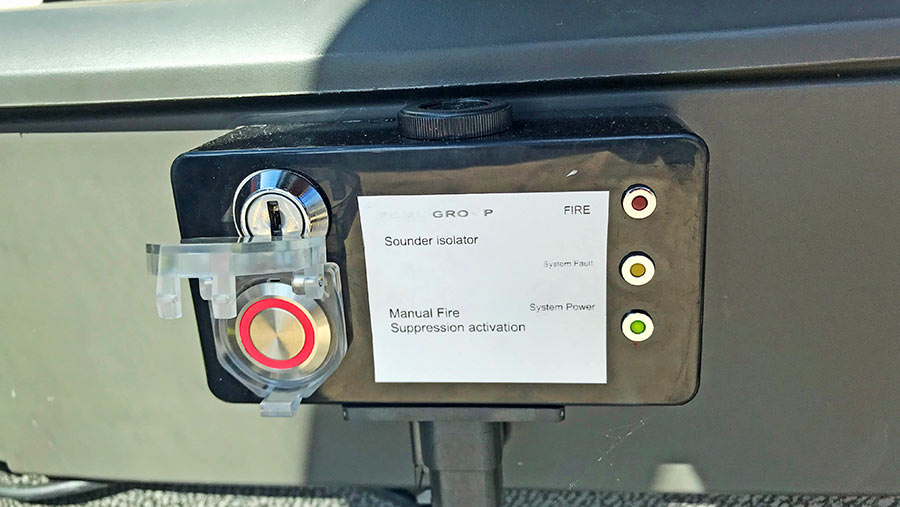
Manual trigger and alarm
Servicing requirement
The system doesn’t require much maintenance, but like all fire extinguishers, it should be serviced once a year. Generally this costs about £175.
If it’s activated, it can also be recharged at a cost of about £1,700. This involves replacing the ruptured section of detection tubing, flushing through the system and fitting new tanks.
Insurance
Simon Bath approached the farm’s insurer, the NFU, to see if their premium could be discounted as a result of the system being fitted. However, as it’s still unproven, he wasn’t offered a reduction.
As for the burnt-out machine, the firm was very fair and offered them a good market value for it. “It was only five years old, though, and as we had just made the last payment, we were hoping for a couple of years of slightly cheaper combining,” he says.