Home-built overseeder improves grass in hard-to-reach fields
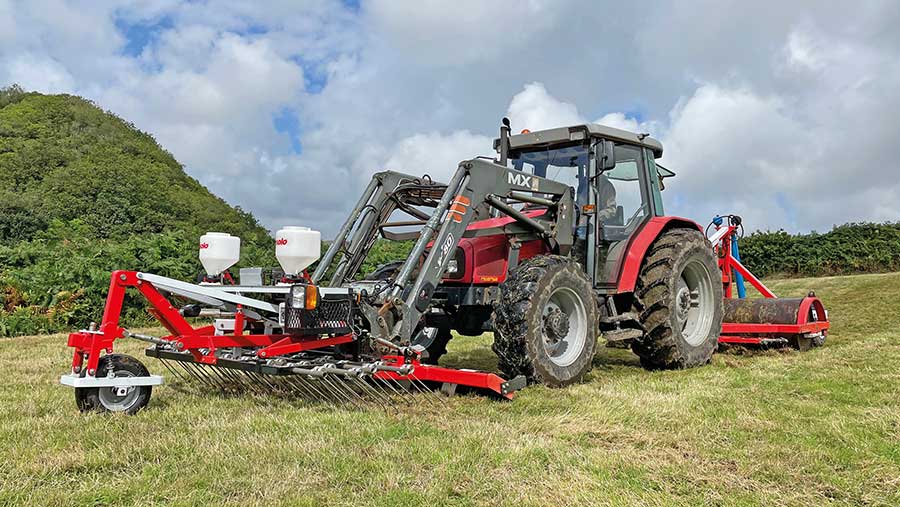
Keen to improve grass quality for his pedigree Dexter suckler herd, Cornish farmer and contractor John Phizacklea built a single-pass overseeding outfit that is manoeuvrable enough to work in his patchwork of small, steep paddocks.
The aim of the project was to create a machine that could, in one operation, tease dead grass out of the turf, create some tilth, spin on grass or clover seed and roll – all without breaking the bank.
To keep the cost down, he made the seeding element out of a pair of Solo hand-cranked garden seeders that he converted to electric drive.
These are substantially cheaper than agricultural models, but have a surprisingly accurate metering system with adjustable drop point.
See also:Â Devon contractor develops combination roller seeder
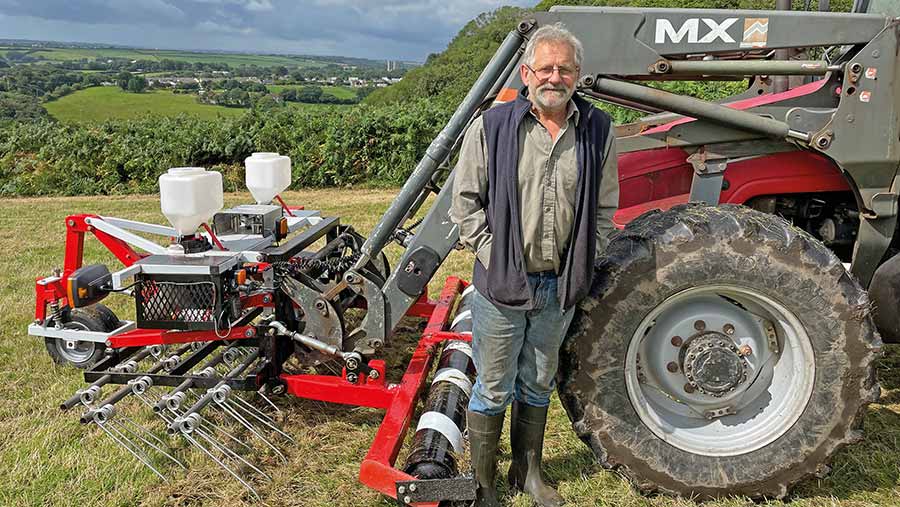
John Phizacklea © James Andrews
Below these he incorporated four rows of adjustable spring tines to harrow the seed in and added a small roller to give some consolidation.Â
As Mr Phizacklea travels on narrow lanes and tracks between local farms in the St Austell area, he needed the outfit to be compact.
For this reason, he settled on a 2.5m working width – roughly the same as his Massey Ferguson 4255 – and decided to attach the implement to his MX front loader, rather than the rear linkage.
Mounting to the loader added to the complexity of the build, but it means he is able to lift it over hedges when negotiating tight entrances.
Having the seeder positioned at the front also gave him the option of using it in tandem with one of his previous inventions – a wheeled ballast roller with a set of hydraulically adjustable tines fitted just in front.
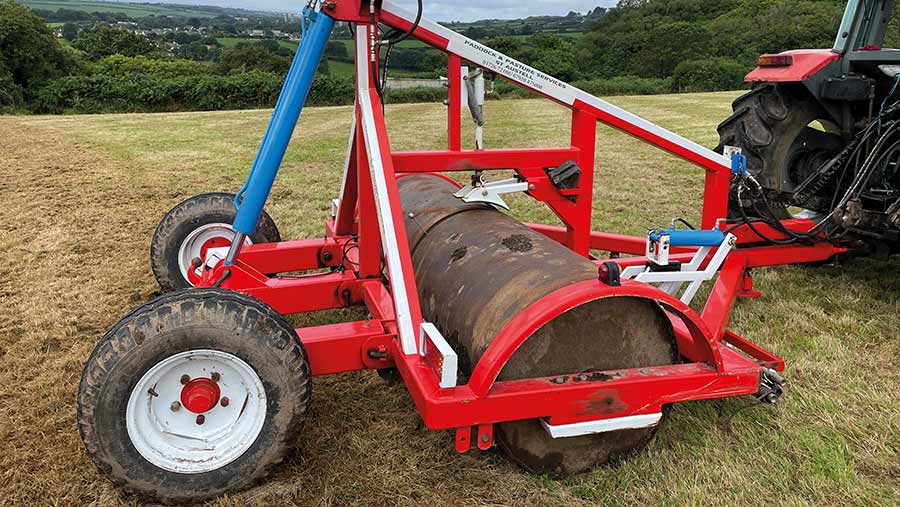
© James Andrews
As a standalone machine, this is useful for pulling the thatch out of pastures before rolling, but for the reseeding operation it helps rake over and press to give good seed-to-soil contact. The tines can also be lifted out of work if he just wants to roll the seed in.
Bad vibrations
Due to the amount of movement at a loader headstock when driving, Mr Phizacklea knew he had to build some form of suspension into his implement to avoid shocks affecting the spread pattern.
This meant fabricating a damped table for the seeding units to sit on, as well as a leading front wheel with suspension.
As a classic motorcycle restorer – who has several of his past projects displayed in the National Motorcycle Museum – he turned to bike components for this task, in the form of inexpensive mini moto coil-over shocks.
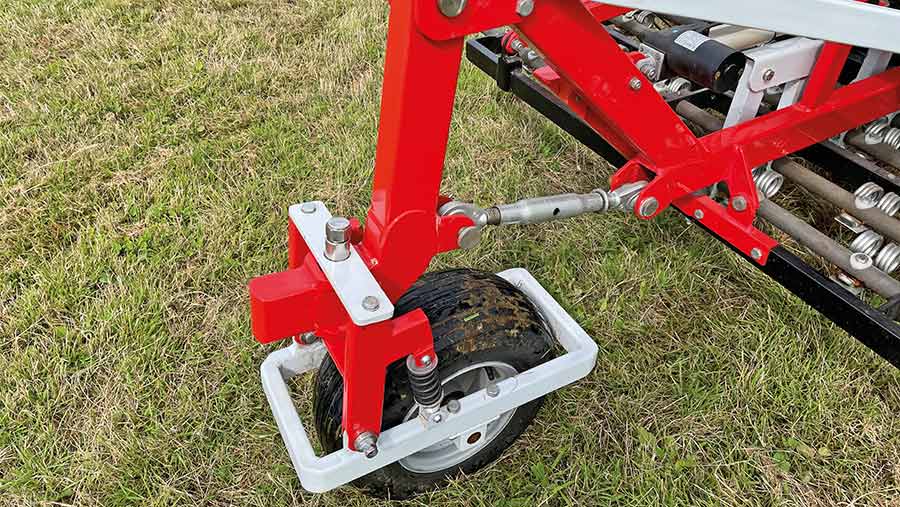
© James Andrews
Converting to electric
With the seeding table isolated from the worst vibrations, he could set about converting his pair of ÂŁ80 hand-cranked Solo garden seeders to electric drive.
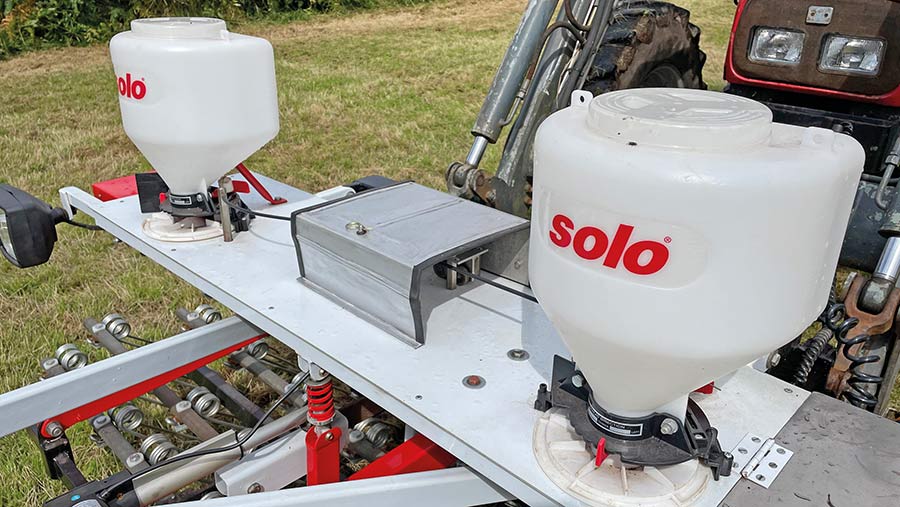
© James Andrews
This involved removing the hand cranks and fashioning a driveshaft between the motors and gearboxes.
Each unit was given its own motor, mounted safely under the seeding table, and he used flexible drive couplings from radio-controlled cars to prevent shocks damaging the gearbox.
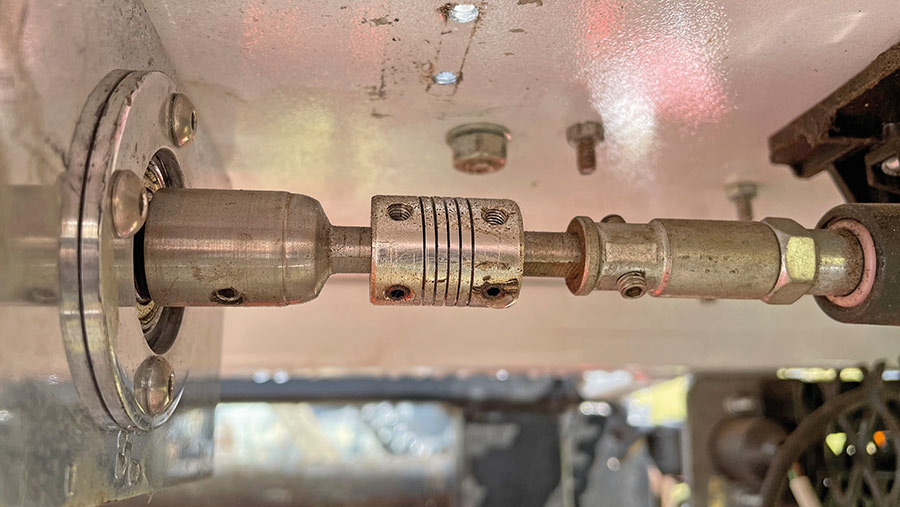
© James Andrews
He also added a variable-speed controller to the circuit that allows disc speed to be adjusted to suit different seeds.
Using calibration trays, he experimented with the disc revolutions per minute until he got the right setting for each type of seed he plans to use.
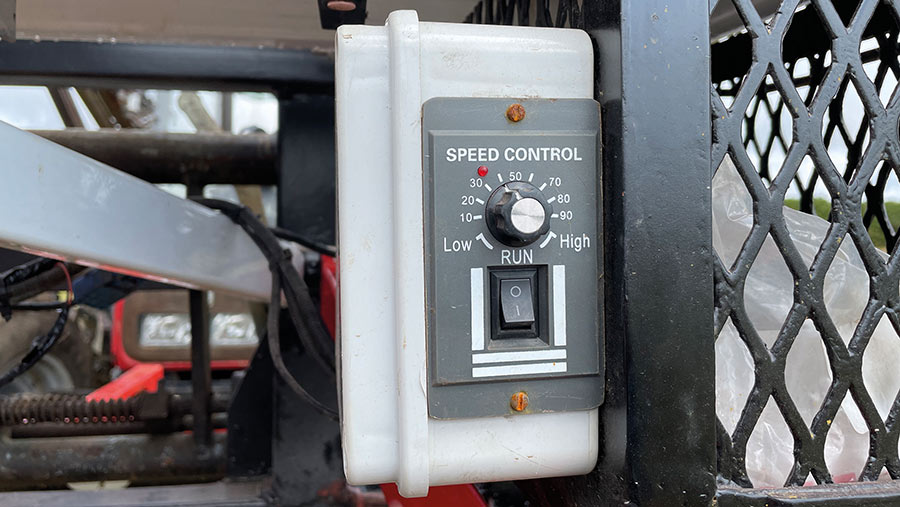
© James Andrews
To give an accurate spread pattern, Mr Phizacklea also positioned the seeders so they have a double overwrap.
The shutters on each of the seeders have been converted for electric actuation, too. To do this he fitted a motor with position sensor between the two units and ran a cable to the shutters.
Using a simple control box in the cab, he is able to open them to a pre-defined setting so the correct rate is applied.
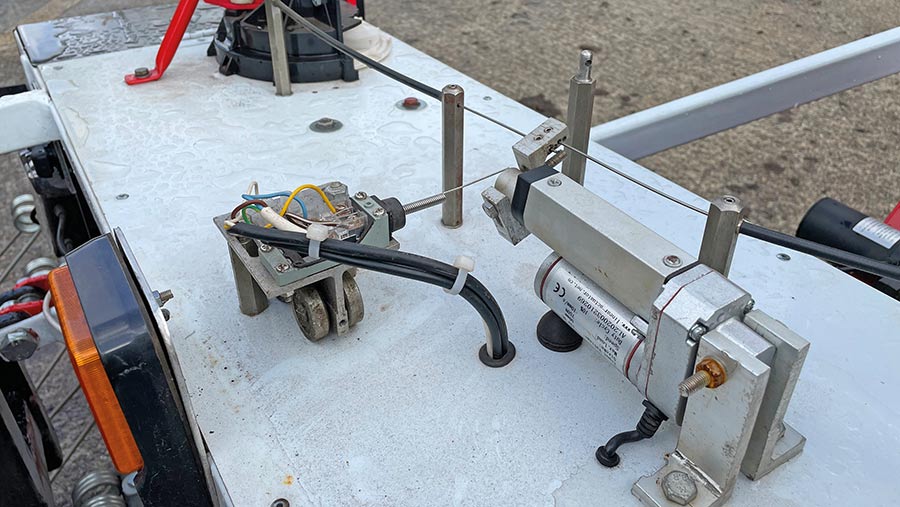
© James Andrews
This means he can leave the discs running while he’s turning on the headlands and switch the seed flow on and off. A light is wired into the circuit so he can see when the shutters are open.
Initially, the shutters were opened manually at the start of the job and the discs were switched on and off to start and stop seeding.
This did work, but it created a puff of seed each time they were started, which resulted in thick patches of grass or clover.
Dethatching
Underneath the seeders, he fitted 48 double tines over four rows that pull the dead thatch out of the grass and harrow the seed in.
These are attached to a linkage so their working angle can be adjusted to suit the conditions.
This is also controlled electrically using a 12V, 6,000Nm linear ram that can be activated from his in-cab control box.
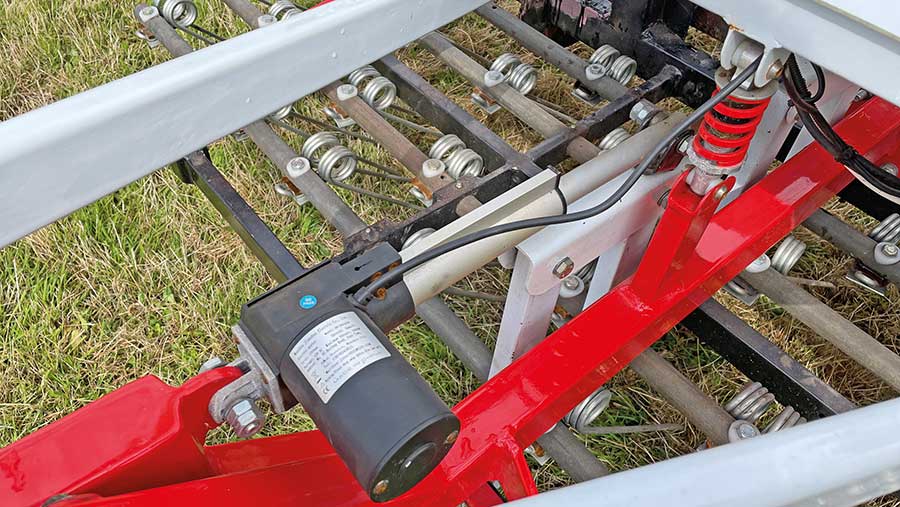
© James Andrews
The final part of the system is a 12in flat roller mounted at the rear that consolidates the surface. This was fabricated out of a length of old, heavy-gauge tube and it has a scraper to keep it clean.
The implement runs on the front wheel and rear roller, so Mr Phizacklea can lower the loader fully when putting it into work – each of these has screw linkages for setting the height and getting it to run level.
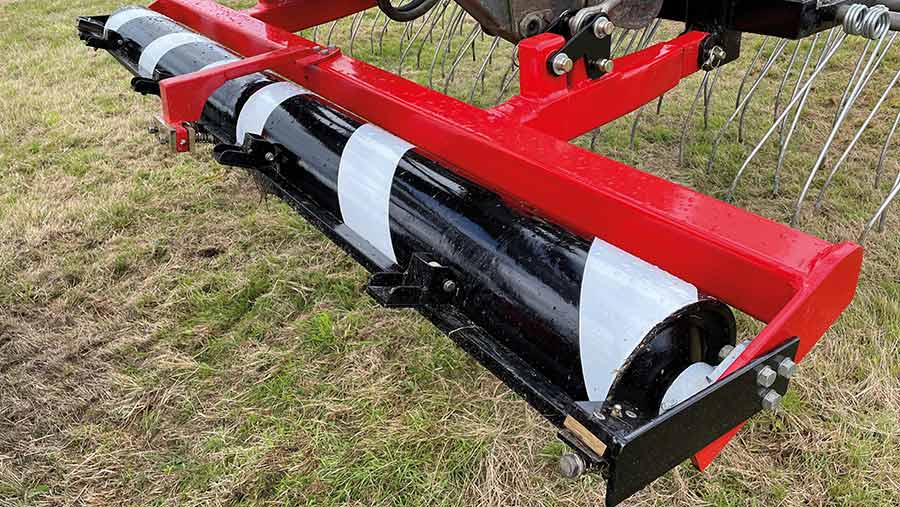
© James Andrews
Finishing touches included adding a compartment to house six-pattern test trays, a test tube kit and a digital weigh scale for calibration. He also gave it a two-pack paint finish.
Some new metal was used in the construction, but the main frame was fashioned out of a middle partition from a Rice horse box and the stem for the front wheel came from a Triumph Tiger Cub motorbike.
The project was put together over the winter of 2020 and it cost a total of ÂŁ1,600 to build.
Rear ballast roller with tines
Often, the seeder gets used in conjunction with a ballast roller and tine harrow combination that Mr Phizacklea made the previous season.
This started out life as a leaky 30in Grays roller that weighs about 3.5t when filled.
He fixed the leaks, built the rollers into a new 100mm box-section frame and added a set of rear wheels with a hydraulic ram so they can be lifted on the road.
Because he works on steep banks, he also incorporated a hydraulic brake. As each of the rollers was some way off round, he came up with a nifty self-aligning linkage so the shoes always stay in contact.
In front of the roller, he added a twin row of Joskin scarifier tines that have adjustable working angle and the ability to be lifted out of work when required.
Using the overseeder
It was completed in time for spring 2021 and was put to work stitching red and white clover into grass, patching thin areas and reseeding where a pipe had been put in one of Mr Phizacklea’s customer’s fields.
It has worked well in all these situations and the seeds established well. It often gets used as a single-pass machine, but occasionally he runs through with the tines first to create some tilth, before going back to spin the seed on and harrow it in.
“The beauty is that it can be used in lots of different situations, and I don’t need to come in with other implements,” he says.
“The fact that I can lift it over hedges also means I can get into fields that wouldn’t be possible with a front linkage.”
That said, he has also fitted front linkage brackets should he want to use it on one in the future.
Despite its success, there were a few teething problems to iron out.
Firstly, the cheap Chinese motors he used to power the discs weren’t up to the job and he went through five pairs before going in search of something better.
Fitting some high-quality industrial motors solved the problem.
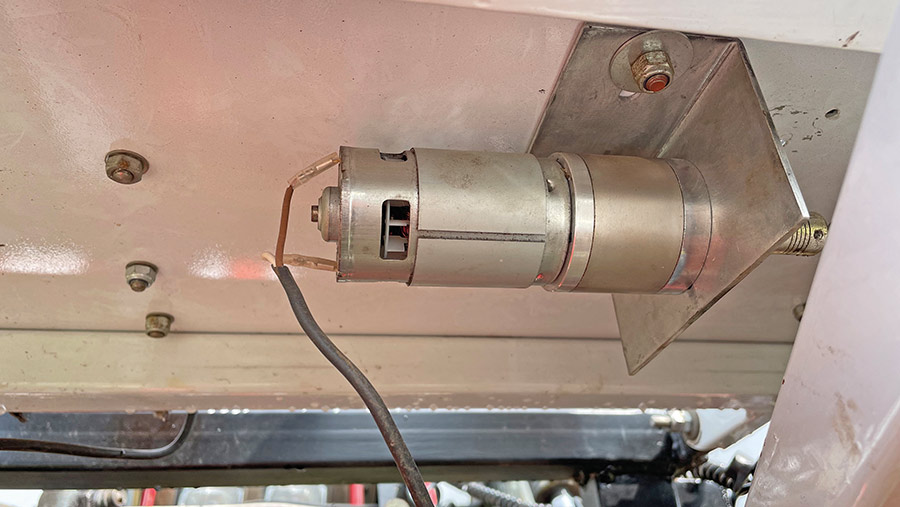
© James Andrews
Also, despite all his suspension, vibrations were still being transferred from the roller to the frame. This was interfering with the spread pattern and caused a few cracks to develop.
The problem was solved by replacing the standard roller bushes with rubber isolastic versions and reinforcing the frame.
He also halved the spring on the seeding table shock absorber to make it more reactive.
Although the Solo seeders give a good spread pattern, the small 9kg hoppers mean they can only seed 0.6-0.8ha of grass to a fill.
To increase its working area, Mr Phizacklea plans to build a bulk hopper with chutes feeding into each unit.
This will allow him to carry out larger reseeding projects without having the faff of continually stopping to fill up the hoppers.