Pottinger rake skid increases forage quality for Gloucestershire farmer
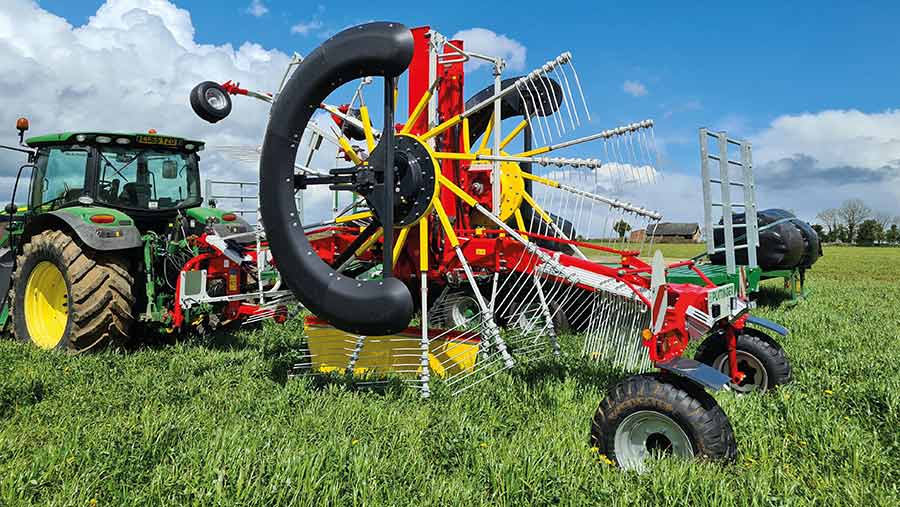
Punctures are a pain at the best of times and, after his old 7.5m Lely twin-rotor rake tallied 18 of them in a single season, Cotswold farmer Simon Best decided to take some action.
The rake was chopped in two years ago, replaced by Pottinger’s centre-swath Top 842C with the quirky addition of plastic skid units in place of the regular rubber tyres.
See also: Grass merger options grow as farmers seek rake alternative
These “glide bars” comprise five 15mm-thick replaceable plastic plates formed into a C shape under each rotor, spreading the weight evenly across terra firma to reduce forage contamination by maintaining a consistent working height.
As a result, they have slashed downtime and increased work rates, with Mr Best now comfortably covering 8ha/hour.
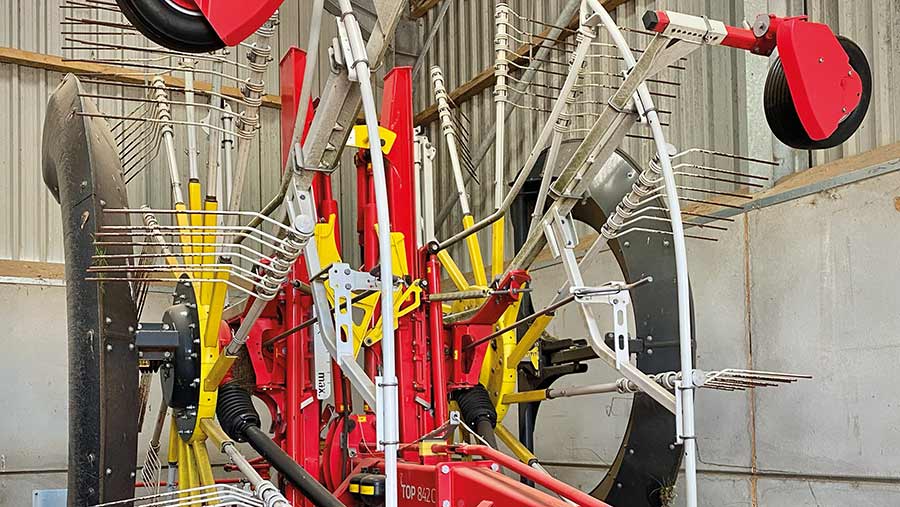
Pottinger TOP 842C rake © MAG/Oliver Mark
This extra speed has come in handy, as a large proportion of the farm’s 450ha of grass – harvested as hay, haylage and silage – is sold directly to the equine market, where customers can get particularly sniffy about quality.
“We need to be bang on with our timings to ensure the product is green and dust-free if we’re to hit the £70-£80/t premium.
“The market is fickle, competitive and a lot about looks – at least compared with livestock farmers that will take a bulk load without complaint – so we can’t afford stoppages at key times, particularly when the weather is against us.”
Farm facts
Bennetts Farm, Leighterton, Gloucestershire
- Farm size 50ha home farm, plus nine further sites on a mix of farm business tenancies and contract farming agreements
- Grass 365ha hay, 160ha haylage and 605ha silage (spread over three or four cuts)
- Livestock 80-head Aberdeen Angus suckler herd
“Flat tyres were a real bugbear with the old Lely, mainly caused by hawthorn hedges along the headland boundaries, but it was also struggling to keep comfortably ahead of the baler.”
A four-rotor rake would have solved that, if it wasn’t for the small, narrow country lanes and dozens of sub-3ha fields that make up Mr Best’s acreage.
Instead, he tried a few twin-rotor options. “I demoed the Kuhn, but it was too basic and didn’t seem particularly strongly built, and Krone’s version, which was a good rake and had a decent control box.”
Pottinger Top 842C
- Working width 7.7-8.4m
- Rotor diameter 3.7m
- Tine arms a rotor 13
- Price paid £24,000
But a conversation with Cambridgeshire farmer Andrew Lawman, who had a Flowtast-equipped model at the time, sealed the deal for Pottinger, and a £24,000 order for a Top 842C went into Newman Enterprises in Wootton Bassett.
This model has since been upgraded to an 882C to produce a wider swath that better suits big baler and forager pick-ups.
Quicker and cleaner
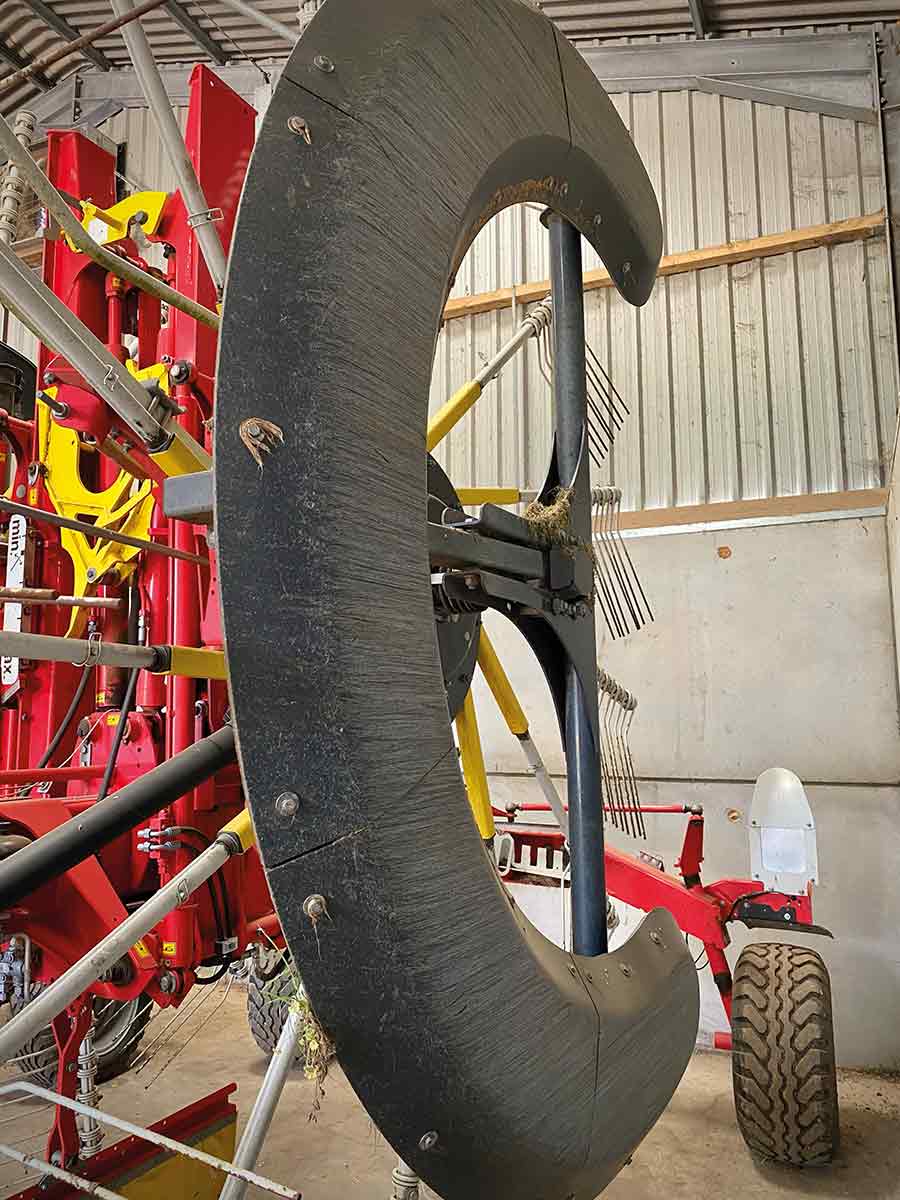
© MAG/Oliver Mark
The major benefit of the Flowtast system is its ability to hug the ground and follow contours, even over the ridges and furrows of the rougher hay ground around Bennetts Farm.
This is helped by an accumulator system above each rotor, with adjustable damping set by altering the oil pressure on both sides.
“I tend to set it at the mid-point of Pottinger’s suggested pressure range, which covers most eventualities.
“It holds the rotors firmly against the ground, spreads the weight better than wheels when the going is soft, and we can comfortably run at 14-16kph without missing any grass.”
Rotor speed can also be tweaked to suit the conditions. Typically, it’s set at 540rpm for a wet and heavy first cut of silage, but it can be wound down to just 350rpm for a light crop of organic hay.
The other upshot of the hydraulic pressure system is that the tines don’t have to be set particularly low, he says.
“We apply muck to the grass destined for silage, so avoiding scraping the ground too much minimises the risk of any remnants being swept up and mixed in.
“We’re also on thin Cotswolds brash soil, and our equine customers wouldn’t take kindly to much stone contamination in the forage.”
Though the large footprints of the skids tend to keep the rotors on an even keel, each one also has an offset front jockey wheel.
These are rarely in proper contact with the ground – they look almost brand new after two seasons’ work – but prevent the tines digging in should the rotor dive into a particularly deep hollow.
Longevity
Mr Best was initially dubious about how long the plastic skids would last, but they are showing little sign of wear – bar the odd stone scrape – after 2,400ha on some pretty abrasive ground.
“They should manage at least a couple more years before any of the sections require replacement.
“Based on that, and the fact that I’ve had zero downtime so far, not even a broken tine, the rake may well end up doing seven or eight years with us.”
The only downsides relate to the controls, with Mr Best having opted for an otherwise basic spec with pull cord-activated diverters rather than a fancier in-cab box.
With three double-acting spools plumbed into the tractor and two diverters to manage independent rotor lift, swath width, skid pressure and the folding mechanism, this choice has added a bit of extra faff.
“I did have the option of electronic controls, but I wanted to use the spools to keep things simple in the cab.
“I might be paying the price for that decision now though, as the sequence for diverting the hydraulics is a fiddle and operators that use it less regularly can waste five minutes working out what’s what.
“Annoyingly, the diverter blocks are also fitted at the back of the rake, which means the cords often get covered in hay and that makes them harder to use.”
New tedder joins the ranks
Impressed with Pottinger’s build quality, a new trailed 12m Hit 12.14T tedder joined the outfit this spring to work alongside an existing 8.8m Malone, providing significantly more grass-turning capacity.
Mowing is also completed in-house, with both a John Deere trailed and a Pottinger front-and-rear combination, allowing the cutting and processing of grass to be as perfectly timed as possible.
“I like to get the size and shape of the swath row just right to suit the baler, whether it be tall and wide for decent air flow through the hay – baled by a local contractor’s two 120x90cm New Holland HDs – or narrow when we’re running the small conventional baler. Either way, this rake will do the job well.”
Bennetts Farm Shop
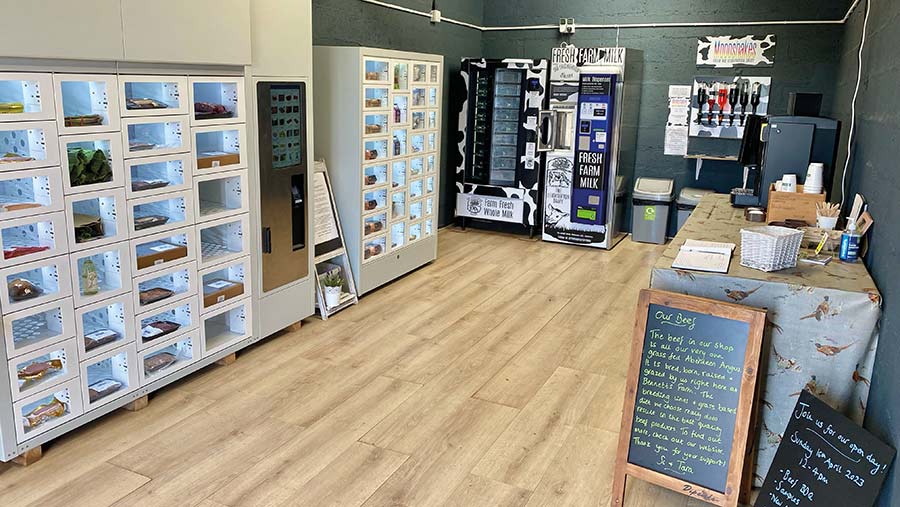
© MAG/Oliver Mark
A portion of the grass at Bennetts Farm is reserved for the 80-strong Aberdeen Angus suckler herd.
Almost all of the offspring are taken through to finishing, and one-third of these animals – two a month – are now butchered to spec for an on-site farm shop. This was set up a year ago by Mr Best and his wife Tara, who were keen to add value to their business.
With plenty of big enterprises of this type already established in the surrounding area, they decided to sell direct to consumers by investing £30,000 in a novel vending machine.
Originally designed for warming noodles in Korea and Japan, the system was adapted for refrigeration by a firm in Italy and brought to the UK by a Scottish importer.
Visiting customers can fill a virtual shopping basket with the products on offer and pay by card, after which the various compartment doors will open to allow for the chosen products to be retrieved.
As a result, no one need man the shop during its open hours (8am to 6pm, seven days a week), and a smartphone app pings whenever something is sold – at which point the locker can be restocked.
“It’s a relatively low-risk way of adding value to our beef,” says Mr Best. “We’re getting between £9,000 and £10,000 an animal, minus butchery, packaging and marketing costs, versus £1,800 to £2,000 for the fat cattle we send through the usual channels.
“We’re not promising to stock everything – our system suits open-minded shoppers that aren’t turning up to buy something specific – but we do try and follow seasonal trends.”
The shop also stocks a range of products from other local, independent producers, including butter, cheese, pork and vegetables, plus pasteurised milk from a dairy farm in the village.
The couple is now planning to add a frozen section, initially with an honesty card payment system as a freezer version of the vending machine is currently only in prototype form.