Buying a trailed forage harvester – the options
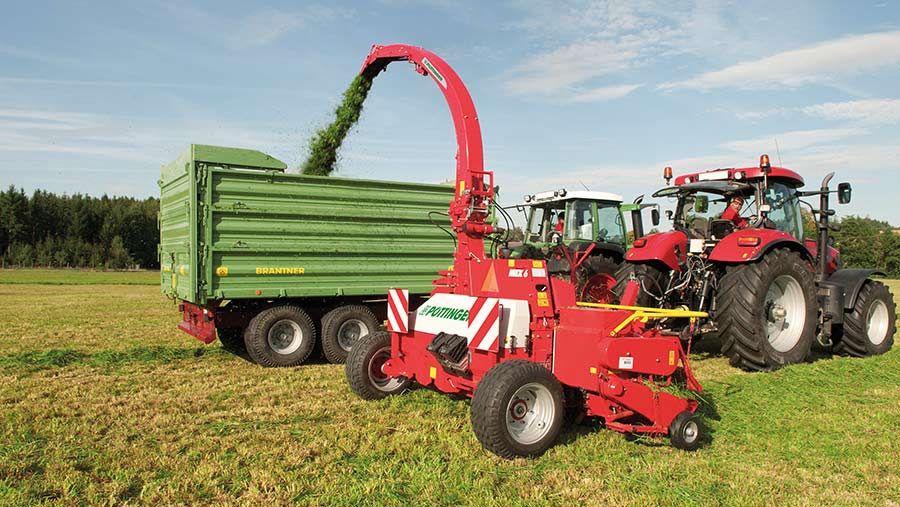
A new wave of precision chop forage harvesters could reinvigorate the market for trailed models, even now that most established manufacturers have abandoned production of their designs.
For many producers, the distinctive whining thrum of a forage chopper at full chat is an appealing sound that characterises the annual ritual of bringing in the grass harvest.
These days, the work will more often than not be carried out by a contracting team with a hugely powerful self-propelled machine at its heart.
See also: High-hour Horsepower: 26-year-old forager still going strong in Herefordshire
With unparalleled output and work rate, first and second cuts can be picked up, chopped and packed into a clamp while the weather holds.
But for farmers with a strong independent streak or whose scale and accessibility makes a self-propelled operation less attractive, using a tractor-powered forager still holds some appeal.
“Medium-sized dairy farms concentrating on producing top-quality silage like to have more control over their cutting date.
“So the typical customer for a Kongskilde FCT 1060 would be a farmer who needs to be flexible to make silage when the crop is ready without having to wait for a contractor,” says Neil Bodymore, Kongskilde specialist at New Holland.
“The higher-performance FCT 1260 MD also caters for such producers, as well as small-scale contractors not wanting the outlay and running costs of a self-propelled harvester, but who require good chop quality.”
He suggests that they have an advantage during “snatch-and-grab” harvests, when being lighter allows them to travel when other silage machinery can’t, and with reduced soil compaction.
Second-hand self-propelleds and forage wagons
Another option for large-scale producers is to go down the self-propelled route with a used example.
Although Mr Bodymore reports that delays at a critical time caused by breakdowns that need expensive repairs to put right has resulted in noticeable back-tracking on this approach.
“Sales of our trailed forage harvesters have remained fairly steady, with a slight increase over the past four years,” he says.
“That’s also because some forage wagon users have moved back to trailed harvesters for a more uniform chop and easier compaction, which make the most of silo capacity with less waste.”
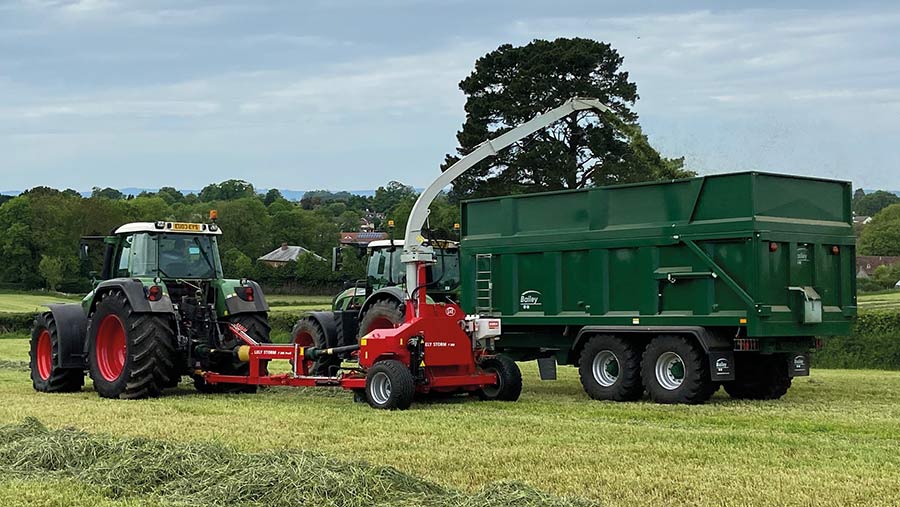
The Lely Storm flywheel-type chopper is no longer in production © Lely
There has been significant uptake of silage wagons as a no-rush, one-operator cut-and-haul solution that eliminates the need for a team of tractors and drivers, and which can be competitive on output over relatively short field-to-clamp hauls.
This trend, supported by progressive improvement in terms of the pick-up, intake and crop-slicing performance, has hastened the decline in the use of pto-powered forage harvesters.
Trailed forager options
Yet examples of elderly drum-type precision chop machines from Claas, John Deere and New Holland can still be found lifting swaths, even though production ended some years ago, and the same is true of the more prevalent disc- or flywheel-type chopper-blower foragers.
Main players include the Kverneland Ten-X, killed off in 2006; Lely’s Storm, a development of the Mengele SH40N that failed to survive Lely’s grass equipment sell-off to Agco in 2017; and the Pottinger Mex, which it made in Mex VI form until 2019.
Richard Parris of machinery dealership Parris Tractors near Taunton, Somerset, is disappointed that the Lely Storm is no longer in production, having purchased the last machines to be built.
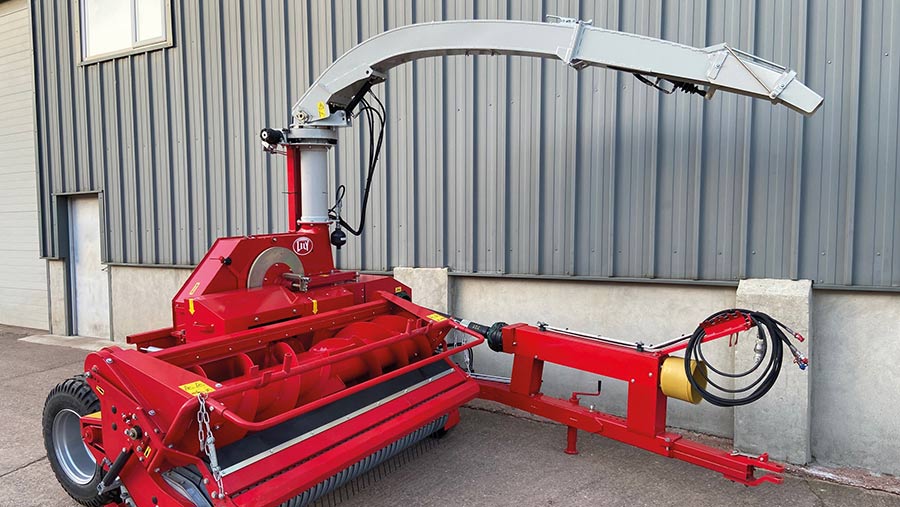
Last off the line – Parris Tractors bought the final batch of Lely Storm P 300 forage harvesters and has sold all but one © Lely
“We bought 14 of them in two batches and sold almost all of them in the past six months – at £39,500 with a metal detector, and £32,500 without,” he says. “We’ve just one left in the yard.”
Most went to farmers in south-west England and Cumbria, where steep ground and restricted access along narrow lanes and in tight yards make access difficult for forage wagons, let alone the size of equipment operated by most contractors.
Mr Parris describes the Storm as “a fantastic machine that Lely had taken to another level of performance, with a wider, modern pick-up, larger-capacity chute, a bigger power band and so on, which meant you could put a 250-300hp tractor on the front and really get the best out of it”.
“If Agco turned it into a Fendt product, I think it would sell because it’s a good match for their high-power tractors.”
John Ayre at Alkmonton Tractors near Ashbourne, Derbyshire, also laments the machine’s passing as someone who became a nationwide specialist for the Mengele design.
“We still get farmers phoning for a new forage chopper, but now all we can offer are thoroughly refurbished versions of the SH40N and the Lely Storm,” he says.
“We’re always interested in good examples for refurbishment and still have access to parts, as well as our own spout liners, paddles and the chopping disc barrel.”
With the departure of these models from the market, only the Kongskilde precision choppers originally developed by JF are available as new-build machines in UK.
Kongskilde
The sole tractor-powered precision chop forage harvester range on sale in Britain comes from Kongskilde Agriculture, having first been introduced under the JF name.
Kongskilde acquired JF in 2011 and was itself bought by CNH Industrial for New Holland in 2017.
The business supplies a number of grass products, such as mowers, tedders and rakes in New Holland colours, while retaining the complete range under the Kongskilde brand for distribution through other dealer networks.
All three of its trailed forage harvesters have mechanical drives, with improvements over the years – and especially with the 2012 introduction of the 60-series – including load-sensing hydraulics and electrohydraulic control of all functions from one switch box.
The current chopping cylinder is heavier than earlier versions, with increased flywheel effect and greater airflow for better crop-discharge performance.
They retain a multiblade chopping cylinder design intended to minimise the extent of knife damage should some hardware be ingested, as well as the unique upward cutting action concept.
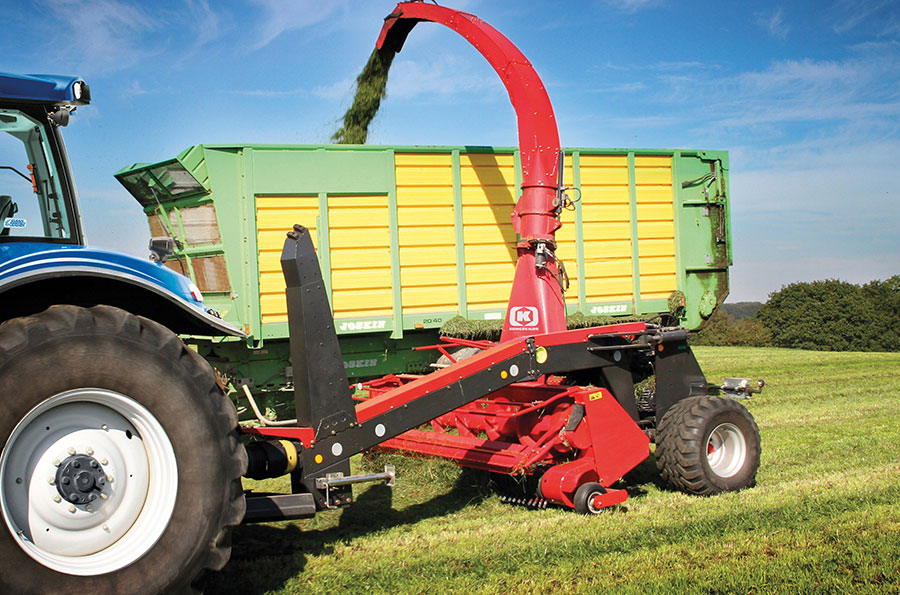
Kongskilde FCT cylinder-type choppers – such as the FCT 1460 MD – are the only trailed harvesters available new in the UK © Kongskilde
Kongskilde engineers reckon this is worth as much as 25-50% greater capacity over other cylinder choppers of equivalent size because of the way processed material is projected straight into the discharge chute, rather than being propelled around the underside of the chopper housing.
Individual blades across the 720mm- and 900mm-wide cylinders are arranged in staggered rows to form a helical pattern.
There are 24 on the 720mm-wide cylinder installed in the FCT 1060, which is capable of handling up to 190hp from the tractor pto, and the FCT 1260 with a maximum power input rating of 280hp.
The same power limit applies to the range-topping FCT 1460, which sports a 900mm-wide chopping cylinder with 40 blades and a wider pick-up at 3.1m – but with a transport width of 3.57m, this model is even less wieldy on the road.
While the FCT 1060 is equipped with a 2.1m pick-up (or a 1.8m down-size option), the FCT 1260 gets a 2.65m pick-up reel, metal detector and a standard chute to which an extension for side loading can be added, or a foldable chute that includes the extension.
New Holland says the FCT 1060 with integral metal detector is currently the bestseller in the UK and Ireland – as well as throughout Europe and beyond – but the FCT 1260 MD is becoming more popular and is expected to take over that position in the coming years.
Kongskilde forage harvesters |
||||
Model |
FCT 1060 |
FCT 1060 MD |
FCT 1260 MD |
FCT 1460 MD |
Power min/max |
120hp/190hp |
120hp/190hp |
140hp/280hp |
200hp/280hp |
Configuration |
Right offset |
Right offset |
Right offset or in-line |
Right offset or in-line |
Cylinder width |
720mm |
720mm |
720mm |
900mm |
Knives |
24 |
24 |
24 |
40 |
Pick-up width |
2.1m/1.8m |
2.1m/1.8m |
2.65m |
3.1m |
Metal detector |
No |
Standard |
Standard |
Standard |
Weight |
2,300kg |
2,300kg |
3,600kg |
3,750kg |
Transport width |
3.30m |
3.30m |
3.30m |
3.57m |
List price |
£49,120 |
£58,429 |
£79,984 |
£86,827 |
Chute extension* |
£811 |
£811 |
£811 |
£811 |
Foldable chute |
£2,795 |
£2,795 |
Standard |
£2,900 |
Note: *Chute extension for side loading; included in prices for foldable chute |
Krone
In a surprise development, it turns out that Krone is trialling a new tractor-powered forage harvester.
The first Krone prototype is designed for use on a tractor with reverse-drive facilities, such as a 500hp Claas Xerion Trac VC; Fendt 900 and 1000 Varios with up to 517hp; and Valtra’s S-series with Twintrac option.
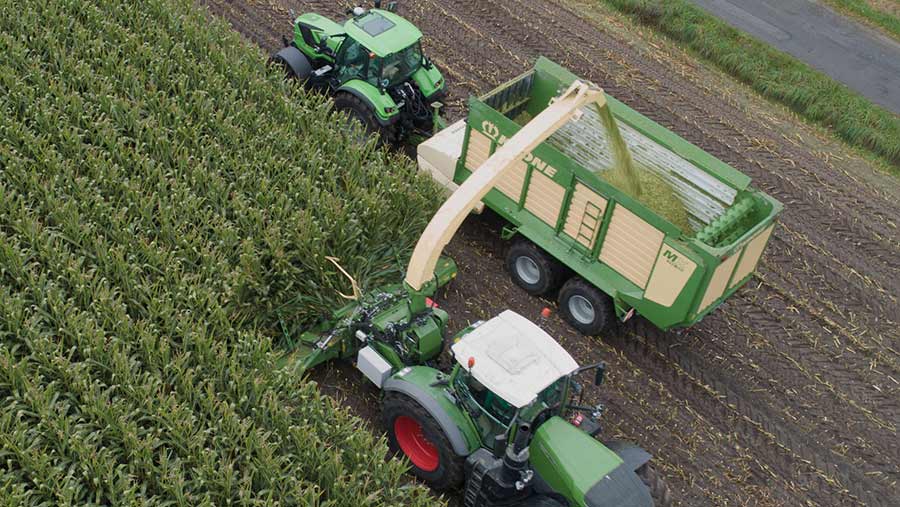
Krone is looking to re-enter the tractor-powered forage harvester market with this prototype machine for reverse-drive power units © Krone
The prospective new chopper is thought to use the 630mm-wide, 660mm-diameter full-width blade drum from Krone’s smaller Big X self-propelled harvesters and is targeted to perform at least as well as the 460hp Big X 480 in terms of output, fuel consumption and chop quality.
Like the self-propelled machines, the prototype has hydraulic drive to the pick-up, direct-cut disc mower and six- to 10-row maize cutting attachments, as well as to the pre-compression rollers.
Krone emphasises that the project is at an early stage and is keen to get feedback and opinions from farmers and contractors via its krone.de global website.
Lacotec
Lacotec already builds a reverse-drive forage harvester, primarily with maize in mind, as it features a disc-type kernel processor. However, it can be removed for chopping grass.
The machine had a challenging UK debut at the Bath and West Grassland event in 2012, recalls UK agent Matt Noble at Somerset-based Noble Machinery.
“Lacotec built its own pick-up, but in Germany grass crops tend to be relatively light compared with the big swaths commonplace in the UK and Ireland and the grass just didn’t flow in very well,” he says.
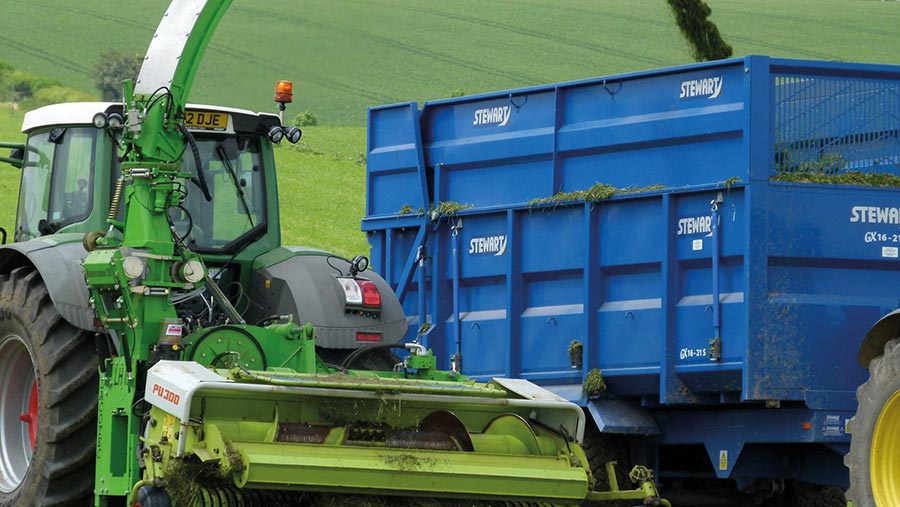
Lacotec builds a few examples of its LHII chopper designed for the biggest reverse-drive tractors © Lacotec
“It was a shame, because in other respects it’s a high-performance machine that’s more like a self-propelled chopper in terms of specification and features.”
Lacotec actually builds its own host vehicle – the 446-550hp Raptor with stepless gearbox to create a self-propelled outfit – but, for the most part, the LHII chopper is on reverse-drive tractors that can make the most of its 500hp input capacity.
The machine has pto drive to the disc-type chopping assembly, which is available in 10- and 14-blade configurations for grass, maize and wholecrop, plus belt and pulley drive to the 220mm disc cracker when fitted.
A built-in metal detector, automated knife grinding and shear bar adjustment, and Isobus connectivity are all part of the package, with adapters to operate with four- to six-row maize headers and grass pick-ups from other manufacturers.
“You don’t have the power losses you get with a trailed forage harvester because of the direct-drive configuration, and it’s easier to move around on the road mounted on a tractor,” says Mr Noble.
“There are several out in various countries and it has tremendous performance potential but, as a small family company, Lacotec doesn’t have the resources to build a batch of machines in the hope of getting some sales. You’re probably looking at £80,000-£100,000 each because of the low volume and high specification.”
Elho
At Elho, the new Cobra forage harvester is already a commercial product that has been on sale for about a year in Finland, but will be rolled out further afield once Covid travel restrictions are eased.
Enquiries from other Nordic countries were expected, says the company, but interest from Australia, Canada and mid-Europe has been more of a surprise, given the machine is optimised for grass harvesting. The UK importer is Shutts Farm Machinery, based in Derbyshire.
Product development manager Johan Löfbacka says the firm chose to look at a precision chop design to exploit the higher-powered tractors now being used by a growing number of farmers and contractors.
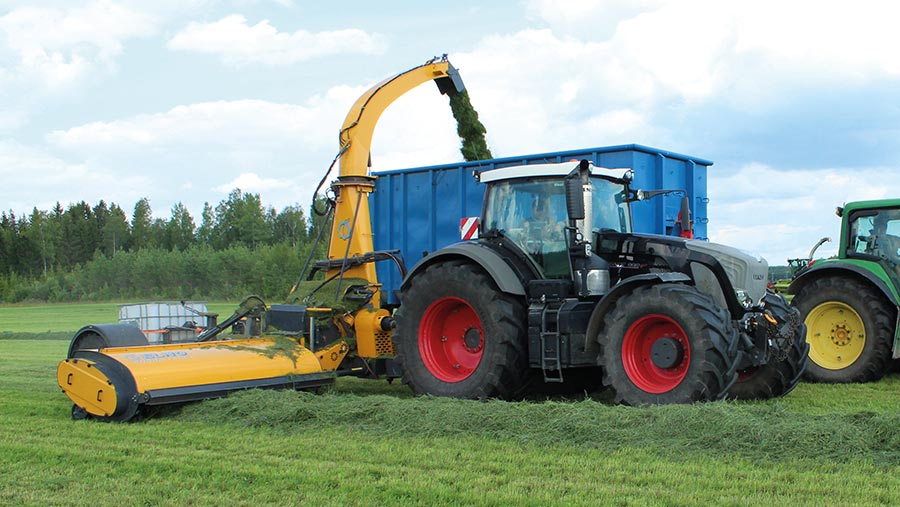
The Elho Cobra departs from conventional trailed chopper design in several respects © Elho
The resulting machine has some notable differences from what has gone before, including a chopping cylinder bigger than any self-propelled can boast. It is driven directly from the tractor pto, achieved by installing the cylinder at 90deg to the direction of travel.
“If you look at a woodchipper, you can see where the inspiration came from for driving the chopper directly rather than through a gearbox,” says Mr Löfbacka.
“There is a power saving of about 3-6% with this arrangement, but the biggest saving is in the cost of manufacturing and parts, because when you want to work with a 400hp tractor, a gearbox and other power transmission components are very expensive.”
Alternative design
As a result of the orientation of the chopping cylinder, incoming grass must turn through 90deg before being delivered to the intake compression rollers.
This is done by twin transverse augers positioned at the back of the mechanically driven 3m-wide pick-up, which itself differs from the norm.
For one thing, it is fully enclosed; for another, the reel is formed with multiple rows of tines in a helix arrangement with no stripper bands – a setup already used for the company’s swath-conditioning tedder.
“A traditional pick-up is designed to handle delicate crops gently, but you don’t need to handle grass gently when it is going to be chopped up a few seconds later,” says Mr Löfbacka.
His response to prospective customers who point out that the enclosed design means they cannot keep an eye on the pick-up is that they don’t need to: “It doesn’t block and it’s fully enclosed, so you don’t get any losses from there.”
Similarly, when potential operators notice that the layout of the machine, with the chopping cylinder tucked close behind the tractor, precludes loading to the right, he also has an explanation.
“We provide a camera mounted on the end of the spout that gives a good view into the trailer on a screen in the cab, and even if you look to the left, you can’t easily see the discharge point because it’s so close to the tractor.”
In addition to direct-pto drive to the chopping cylinder, the Cobra needs a 160-litre/min oil supply from the tractor, mainly for the hydraulic drive to the feed rollers.
This, it’s claimed, makes it easy to adjust chop length and to put the rollers into reverse to clear a blockage – an eventuality that a load-monitoring system aims to avoid in the first place.
It alerts the operator once a certain load factor has been reached and a second trigger point automatically stops the entire intake system while lifting the pick-up at the same time to prevent it bulldozing the swath.
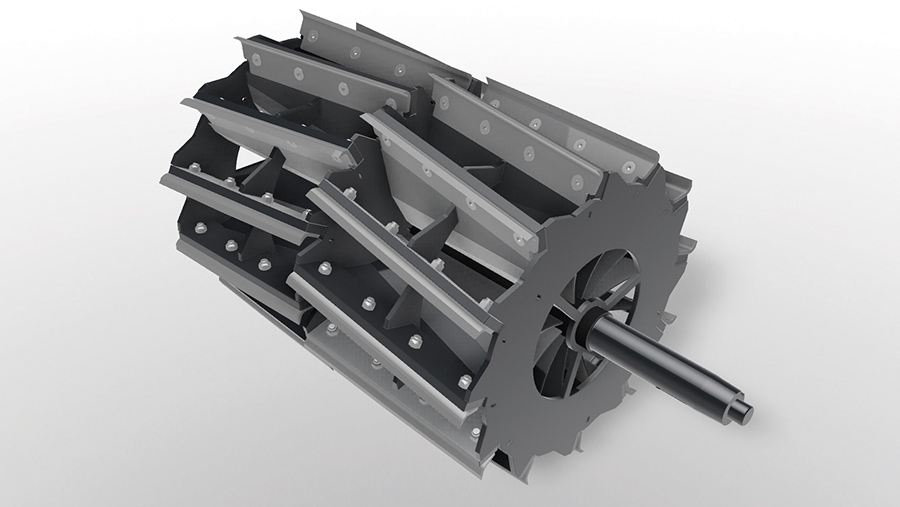
Mammoth chopping cylinder of the Elho Cobra outguns even self-propelled choppers in terms of width and diameter © Elho
The Cobra’s mighty pto-driven chopping cylinder measures 1,000mm wide and 770mm in diameter, which comprehensively trumps self-propelled machines constrained by the space available between the front wheels.
New Holland’s Forage Cruiser comes closest at 884x710mm (or 690mm depending on the cutterhead installed), while the John Deere 9000-series is next “best” at 850x670mm.
Elho’s cylinder has 16 rows of half-width blades arranged in a staggered chevron formation with paddle sections designed to generate plenty of airflow to keep the chopped material moving.
“The machine needs at least 250hp, but if you put it on a 400hp tractor, we are confident you would get the same level of performance as a self-propelled machine with the same power,” says Mr Löfbacka.
In addition to the trailed Cobra 7710T with its stabilising telescopic axle, there is also a version that integrates the harvester with a trailer for a single-operator chop-and-haul approach reminiscent of the Teagle Toucan and others that preceded today’s heavy-duty, fine-chopping forage wagons.
Ivarssons & Metsjo
Ivarssons & Metsjo, a Swedish manufacturer, builds its take on a trailed forager because it remains a popular format among Nordic farmers, says Loa Ivarsson.
The firm uses Kongskilde precision chop harvesters, with most models arranged in-line so the tractor straddles the swath.
But on the new Harvester 1360 and 1460 models, the chopping unit is turned through 90deg and fed by a 3.1m-wide offset pick-up capable of handling wider, fuller swaths of forage.
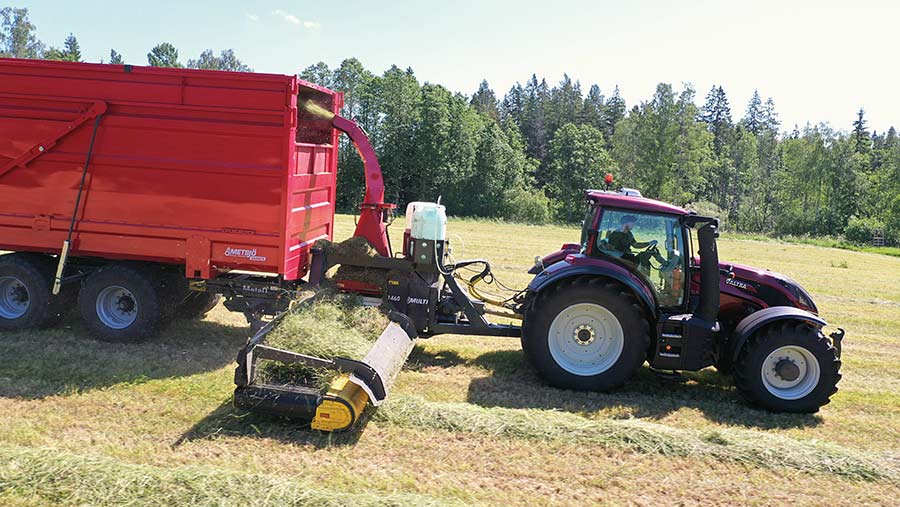
A Roc belt merger forms the pick-up on the latest combined chopper/trailer unit from Metsjo © Metsjo
Two pick-up types are employed – the Harvester 1360 has a Metsjo construction using a conventional stripper tine reel and single auger driven by an on-board hydraulics system.
The Harvester 1460 has a belt-merger unit from Italian manufacturer Roc driven by the tractor hydraulics.
Both fold up for a transport width of 2.55m, and while the 1360 costs and weighs a little less but takes more power, the heavier and more expensive 1460 has a built-in metal detector and requires a flow-controlled double-acting oil supply from the tractor.
Since the company’s trailers have interchangeable bodies or hook-lift mechanisms, the more costly chassis and running gear can also be used for other purposes with the chopper removed.
North American options
In North America, traditional dairying areas are keeping sales of pull-type forage harvesters going – albeit in dwindling numbers – to retain independence and save costs over contractor charges, says Brad Wenger, product marketing manager at New Holland.
“Since 2017, the North American market for pull-type choppers has dropped from about 400 units to half that, largely because it has become increasingly difficult for the traditional small family farms that use them to make money from dairy.
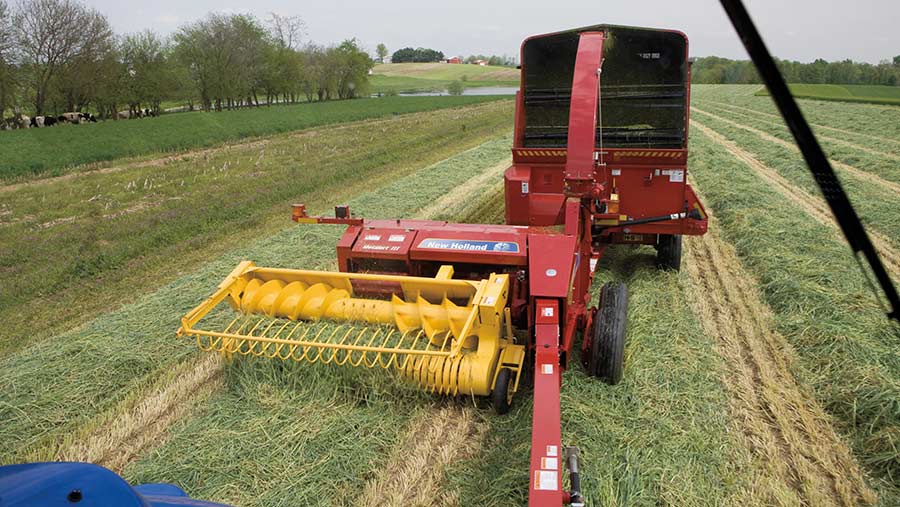
CNH continues to build ‘traditional’ pull-type forage harvesters in the US, like the NH FP230 © New Holland
“They like the simplicity of our FP230 and FP240 pull-type choppers because, with dealer workshop technicians charged out at $100-$120 (£70-£85) an hour, they want to look after their machines themselves.
“With at least one 180-300hp tractor on these farms for cultivations work, they certainly have enough power available and there are also a lot of farms with these machines that still use silos for fodder storage.
“Filling those is a slower process than packing a silage floor bunker, and that doesn’t suit a custom operator [contractor].”
The forage choppers built at the CNH factory in New Holland, Pennsylvania, where the equivalent Case-IH FHX300 is also made, have barely changed in the past two decades, except for the installation of electric controls.
A 1.94m-wide swath centre-gathering pick-up feeds a pair of chain-and-sprocket-driven compression rollers ahead of the 533mm-diameter cutterhead. It is run at 850rpm and carries 12 full-width knives in a spiral arrangement.

Forage chopped on the Case-IH FHX300 is transferred by transverse auger to a separate blower © Case-IH
From there, a single transverse auger takes the chopped material to a dedicated blower on the drawbar side of the machine, which is often used to propel the forage into a bed conveyor unloading into a hay cart towed behind.
Maximum input power for the two models is 225hp and 300hp, respectively.
Dion-Ag
Canadian manufacturer Dion-Ag has a different outlook on the trailed forager market and aims to attract customers by developing new machines with increased performance and modern controls.
At its Boisbriand works in Quebec, the company manufactures three models available with conventional 2.15m or 2.75m swath pick-ups and 2.2m and 2.9m row-free maize cutters.
The two Dion-Ag Scorpion models have 12 full-width blades in a spiral layout on the drum and are sold through dealers in Canada, the US and Australia.
The 2430 model incorporates John Deere’s Duradrum segmented blade chopping cylinder and is built exclusively for Deere dealers worldwide.
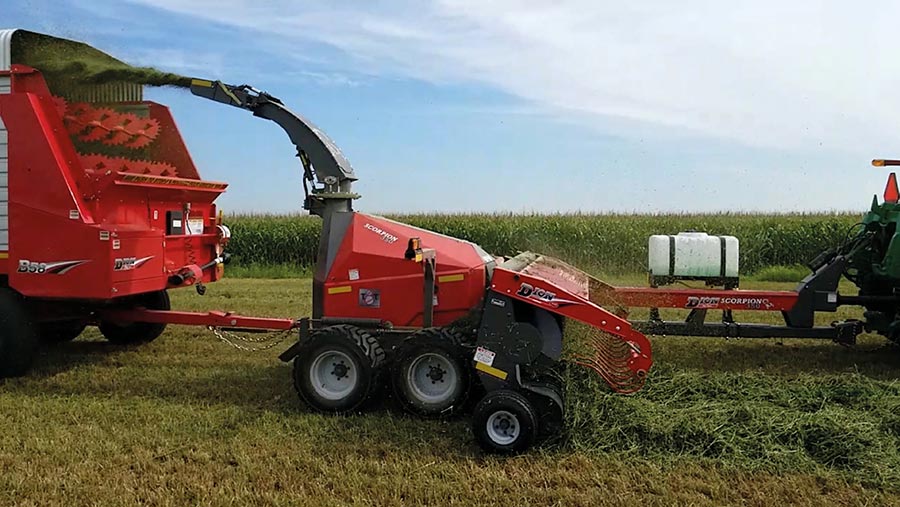
Canadian manufacturer Dion-Ag set out to modernise pull-type chopper design with the Scorpion 350s © Dion-Ag
All three machines run on tandem axles and fat tyres both sides to spread their weight.
A straight-through crop processing design, with forage passing between the compression rollers, chopper housing and blower without changing direction, is in contrast to harvesters with separate chopping and blowing installations.
The Scorpion 350 is the flagship machine – it can take 350hp at the pto and is said to be capable of delivering more than 130t/hour.
While the 2430 and Scorpion 300 have multi-speed gearbox drive to the feed rollers and conventional electric controls, the Scorpion 350 has hydraulic feed roller drive that uses the tractor’s “power beyond” circuit for cutterhead load monitoring and infinite chop length adjustment.
At the heart of the Scorpion models is a 560mm-diameter chopping cylinder driven at 1,033rpm through a 300hp-capacity 90deg bevel gearbox to get 22% more cuts a minute than a more common 850rpm system.
A belt from the bevel gearbox output shaft drives a hydraulic pump and motor that, through a twin-output gear case, runs the upper and lower compression rollers.
Dion-Ag points out that infinite feed roller speed adjustment can offer a wider range of chop lengths than mechanical drive using gearboxes, and gives greater control when reversing the feed rollers to clear a plug.
Speed sensors on the feed rolls and cutterhead provide blockage warnings, while sensors also watch overbelt drives to detect slippage.
And in addition to Dion’s metal detector, the Scorpion 350’s monitoring system activates an emergency stop if it detects a stone or other non-metal debris by monitoring the height of the top front feed roller and its rotation.
In the cab, the operator is provided with a Isobus information display, while up to four remote cameras can be installed to provide remote viewing assistance from the spout and other areas of the harvester.
Fliegl trials hybrid harvesting concept
A different concept that aims to combine the lower chopping power requirement of a forage wagon with the greater output of a full silage-making team is being developed by German trailer maker Fliegl.
The Büffel (Buffalo) has a pick-up reel and crop-slicing system like a forage wagon, but also a side elevator for unloading the small body – of 10cu m capacity on the prototype – to provide buffer storage during trailer changeovers or when picking up in awkward corners.
The idea is that the machine can work continuously in all situations without interruption as two or more trailers haul grass from field to pit.
Nick Dale, Fliegl UK sales and service manager, says: “With each practical test of the system, the demands on the machine increase, so there has been a period of development since it was first seen in 2017.
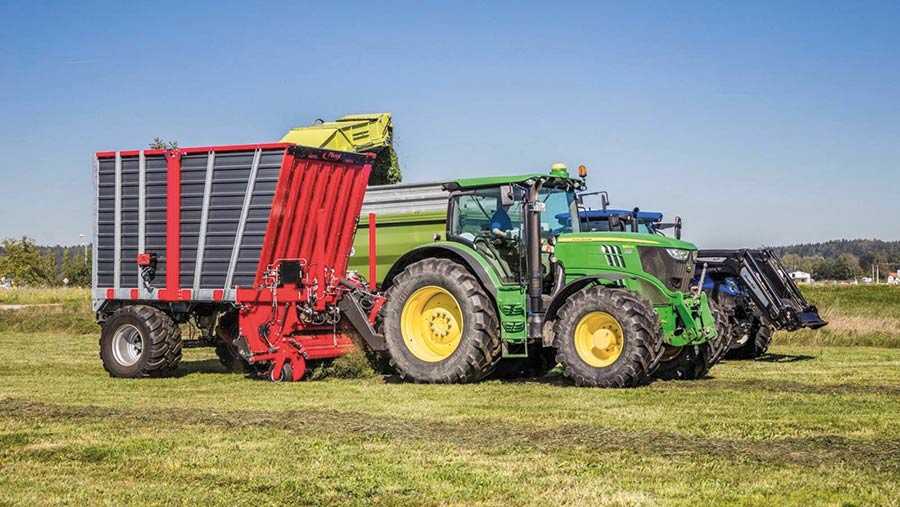
The Fliegl Buffalo aims to combine the low-power requirement advantages of a forage wagon with the output of a multi-trailer system © Fliegl
“It is now in the final test phase and, from May onwards, will be harvesting first-cut grass at various locations throughout Germany to prove its abilities to potential customers and dealers.”
In earlier trials, Fliegl engineers have recorded harvesting rates of about 130t/hour with a 200hp tractor up front.
Continuous operation is made easier for operators by “magic eye” sensors that prevent the unloading elevator running when there is no trailer present or even when there is a trailer present but it is out of kilter. This avoids dumping grass on the ground or on the tractor.
At 8t, the machine is a relative lightweight and an axle extendable by 90cm is said to give good lateral stability on sloping ground.
Fliegl engineers reckon in particularly steep or soft parts of fields it would be possible for the machine to retrieve grass and unload into trailers on more level ground. An overall length of 6m makes the outfit pretty manoeuvrable, too.