Dutch dairy saves time with powered silage clamp cover rollers
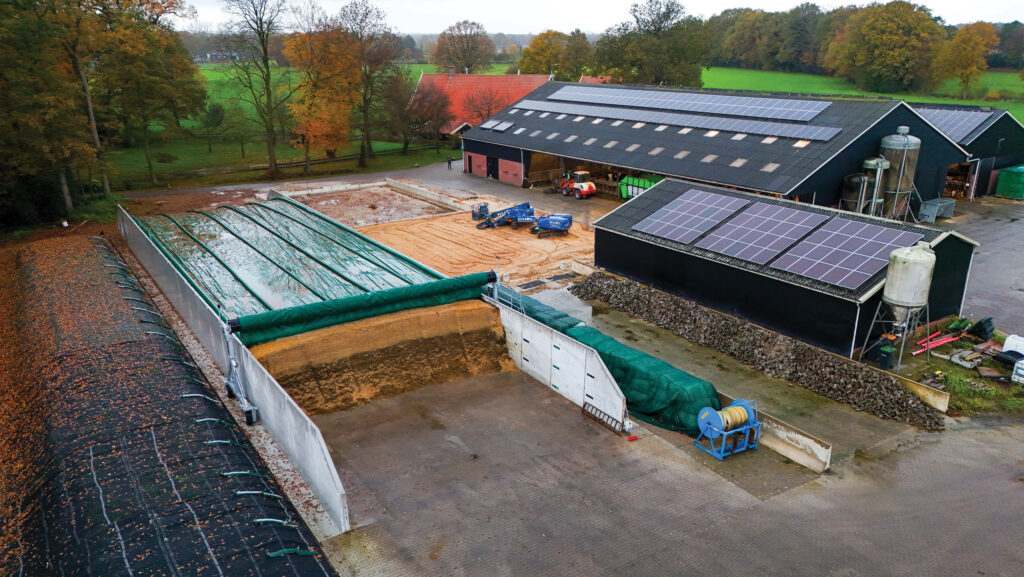
There can’t be many jobs in farming more dreaded than sheeting and unsheeting silage clamps, with mere mention of the task sending friends and family scuttling off to other “more important” jobs.
Wrestling with slippery, skanky plastic, gravel bags and tyres filled with rat urine and rancid rainwater doesn’t hold much appeal, especially given that it invariably takes place the wrong side of midnight just as a gale blows in.
Doing it once a year is bad enough, let alone three or four times when multiple cuts are to be piled into one pit.
So imagine the misery of pulling sheets on and off eight or nine times in a season, which is not uncommon practice in parts of the Netherlands and Germany where grass is cut every few weeks through the growing season and layered, lasagne fashion, into a single clamp.
See also: Complete guide to silage clamp compliance
What is a lasagne clamp?
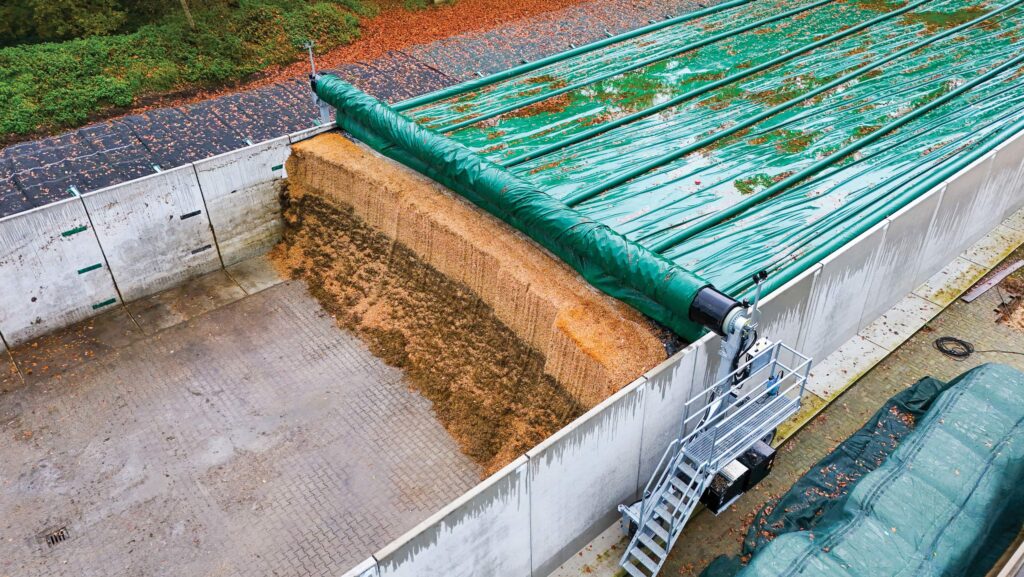
© Nick Fone
Many dairy farms in northern Europe employ a multi-cut approach to silage making, with everything layered into a single clamp.
Typically this means that bulkier, high energy spring grass goes in at the bottom, with later season, higher protein cuts getting layered on top.
In between, there might also be a strata of wholecrop cereal silage and if there’s maize in the mix it’ll generally end up on top.
The advantage of this approach is that everything grown through the year is accessible as it’s fed out, with the result that the ration is kept consistent as that season’s silage is used up.
But there is a downside: the pit has to be un-sheeted and re-covered repeatedly, hence the developments of automated gantries to do the job.
The mechanical option
No surprise, then, that numerous inventive farmers and enterprising engineers from both nations have come up with innovative ways to mechanise the job.
Typically employing a gantry-type arrangement, these automated clamp cover rollers will wind up and re-dispense plastic sheets, preservative “cling-film” and heavy mesh covers in one swipe.
Electric or hydraulic motors power the winding mechanism and propel the machine along. Some are fitted with an on-board petrol power pack while others have a mains feed and trailing extension lead.
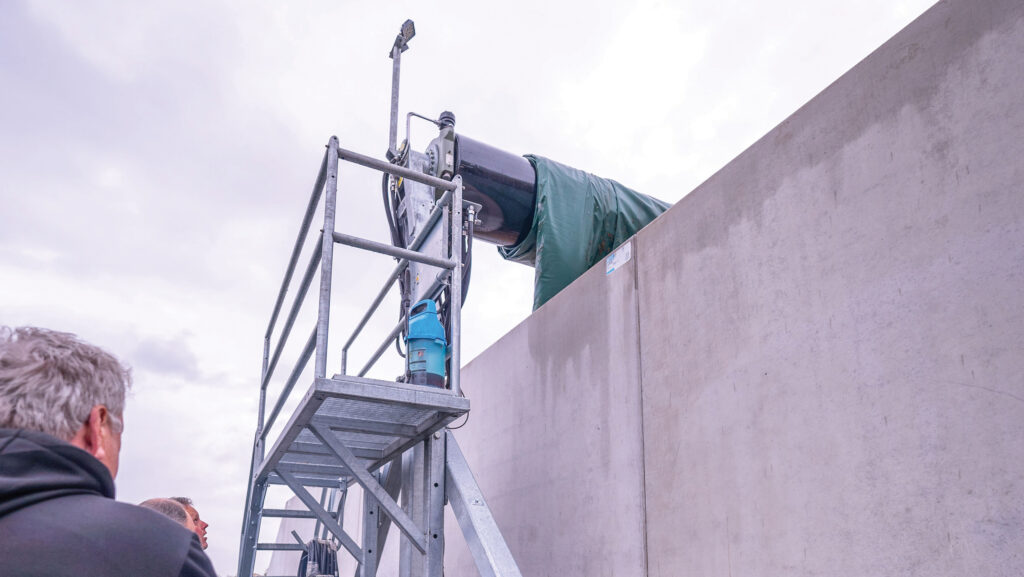
© Nick Fone
These gantries either run railway-style along the top of concrete clamp walls, or straddle the heap with their wheels on the deck outside the panels.
While the former needs to be lifted on and off with a loader before the buckrake can move in, the latter design means the machine can generally be trundled out of the way when the pit is being filled and wheeled back into place when it’s time to cover it over.
The biggest bonus of all systems is there isn’t an effluent-filled tyre, split gravel bag or heavy rubber mat in sight.
Instead, they tend to use water-filled sausages integrated into the top cover sheet, running the length and breadth of the clamp to keep things airtight.
When it’s time to unsheet ready for the next cut, the liquid (often saltwater to avoid freezing) is pumped out into a storage tank.
With the new crop in the pit and the sheet rolled back over, the lay-flat pipes are then re-filled. As the silage is fed out daily the unit is rolled back little by little and a small amount of liquid is vented from the pipework.
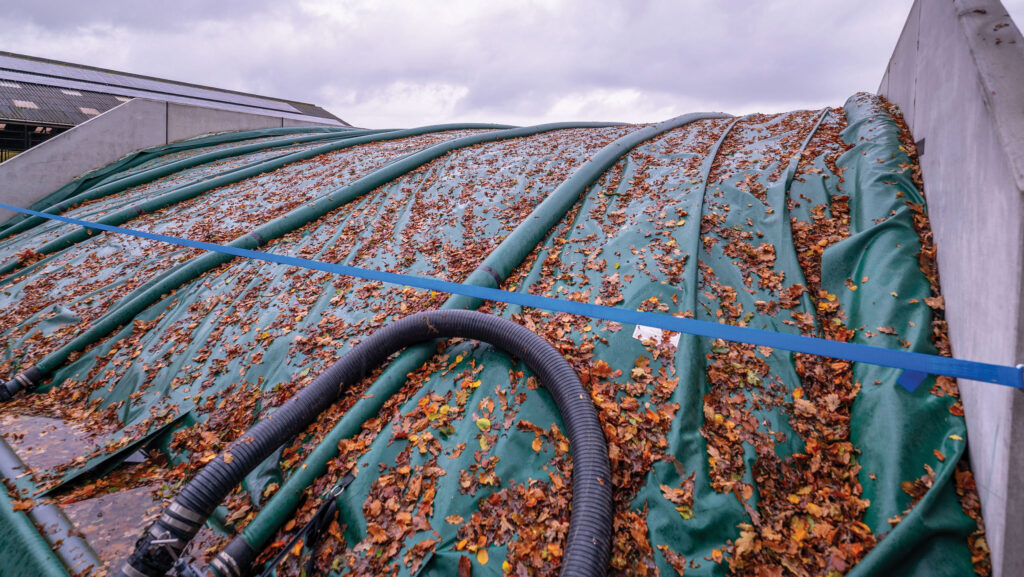
© Nick Fone
Installation job
Dairy farmer Jeroen Groeneveld, based close to the Netherland’s eastern border with Germany (at approximately the same latitude as Birmingham), invested in just such a setup a little over a year ago.
When planning a new silage clamp he had enlisted the advice of Dutch concrete panel specialist Bosch Beton.
It offers all manner of precast concrete products including silage pit walls up to 5m high, and also has Agridek automated clamp covers in its armoury.
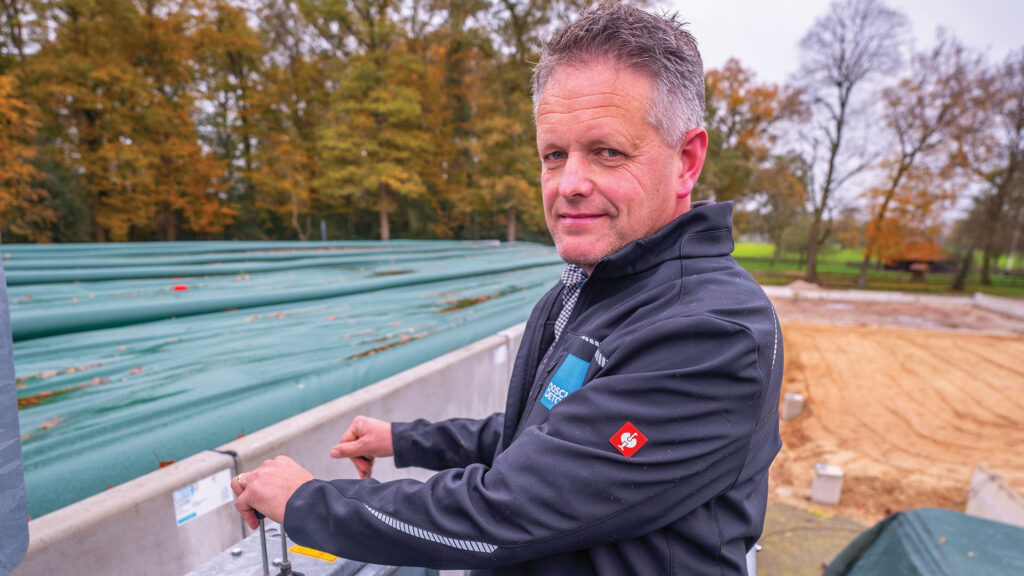
Jeroen Groeneveld © Nick Fone
Farm facts: JA Groeneveld, Lattrop-Breklenkamp, eastern Netherlands
- Farmed area 75ha
- Cropping Grass leys 62ha, maize 13ha plus another 15ha for youngstock
- Livestock 170 milking cows – Holstein x Montbeliard x Viking Red x Jersey averaging 8,500 litres/year at 3.7% protein and 4.8% butterfat
- Staff Jeroem, Angelique and Wessel Groeneveld
Machinery
- Milking robots 2014 three-box GEA system
- Tractors Fendt 514 and Case IH Farmall 105U
- Loader Schaeff SKL 834 artic wheeled loader
- Feeder Strautmann 2401 twin-auger mixer
- Forage wagon Deutz-Fahr FE742 (used in combination with Kuhn GMD front-mower for zero-grazing)
“For years we have been using a multi-cut lasagne layering approach with our silage clamp – everything in one pit for consistency and for efficiency in feeding out,” Jeroen says.
“But it’s a real pain repeatedly having to pull back the sheets and then re-cover the pit. Some seasons we’ll do it seven or eight times.
“So when an automated clamp cover was suggested I was very interested. The €70,000 (£60,000) price-tag initially seemed steep but if you look more broadly at the labour savings over a 10-year period, it actually isn’t that expensive.”
Like many other dairy farmers in the area, Jeroen aims to cut his grass at optimum digestibility, which can mean harvest intervals are as little as a month when growth rates are at their peak.
Although his 170 milkers spend some of their time outside, for a great part of the year they are fed a mix of silage and freshly cut grass.
Silage making is done by a local contractor with either a self-propelled forager or forage wagons.
Previously, loose sand was used to weigh the covers down and it was a marathon effort to get the drive-through clamp unsheeted in good time for the arrival of the first load.
Now, the water is pumped out of the heavy top sheet, the clamp covers are rolled up as one and the self-propelled gantry wheels itself out of the way of both wagons and buckrake.
The whole process generally takes less than half an hour.
“It was always a job everyone dreaded and inevitably there was a tendency when we came to sheet the clamp down to be economical with the sand as we knew we’d be lifting the covers again very shortly,” Jeroen says.
“With the water ballasting system the sheets always have an even weighting right across the top of the clamp.
“Before, we’d accept a level of wastage on the shoulders but now there’s not a spot of spoilage.”
One of the key elements of this is a heavy liquid-filled sausage positioned laterally across the pit, directly over the fresh clamp face.
It maintains weight on the sheets right to the front, stopping them lifting and allowing air ingress over the top layer.
As the silage is used and the Agridek unit winds up the sheet, this heavy sausage lazily rolls back to sit snugly at the point where the covers turn upwards to be wound onto the clamp-wide roller.
There is one restriction with the setup: the clamp cannot be over-filled.
The set height of the gantry means there’s very little opportunity to build skywards in a good growing season, with the 3m-high panel walls typically resulting in a silage density of about 280kg/cu m dry matter.
For comparison, that figure drops to 230kg/cu m with 2m-high walls and 180kg for mushroom-style field heaps.
It is possible to get more than 320kg/cu m with 4m high panels – pushing the old “sky’s the limit” efficiency argument.
Contractor feeding
While Jeroen has his own 24cu m Strautmann feeder wagon and Schaeff loading shovel, these are no longer employed on frontline duties.
Instead, a local contractor comes in once a day with a self-propelled RMH mixer to feed the farm’s cross-bred cows.
Impressively, the job of loading, mixing and dispensing the ration takes just 10 minutes, with a premix of straights and minerals left in a strategic heap right in front of the clamp face.
That’s the old Strautmann’s only job these days – it is run up once a week to mix up rape meal, caustic oats and beet pulp.
Having everything in one place for loading means the job is done quickly, keeping costs as low as possible.
The daily rate for the feeding service is calculated on a time plus fuel basis. Burning diesel at a rate of 0.62 litres/min, the RMH wagon is charged at about €45-50 (£38-43) a day – a figure that Jeroen believes cannot be bettered in-house.
Keeping turnaround times as brief as possible is also critical from the contractor’s point of view.
With two self-propelled rigs out every day, the business services some 30 herds, totalling more than 4,000 cows, across a 20km wide area.
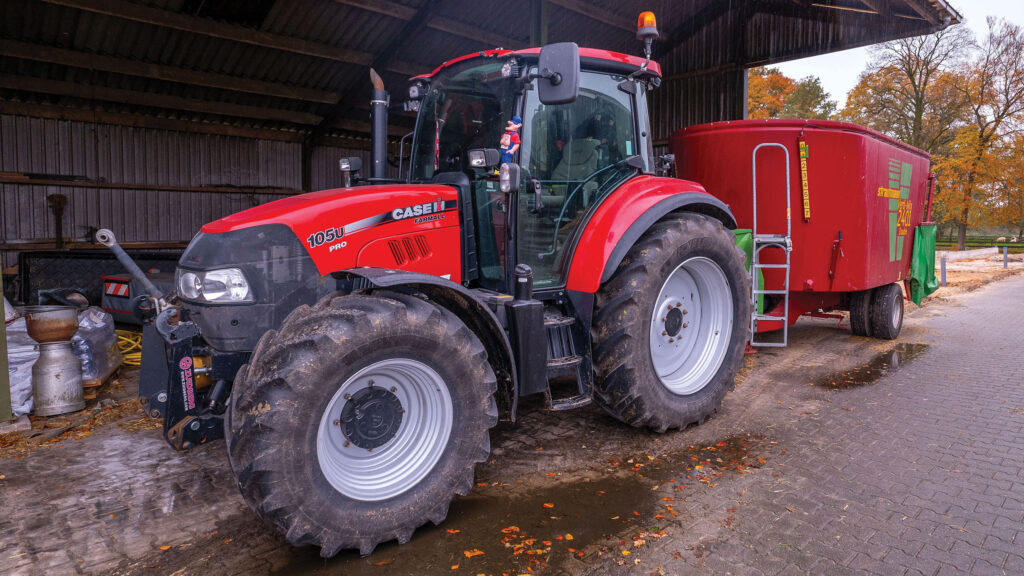
© Nick Fone
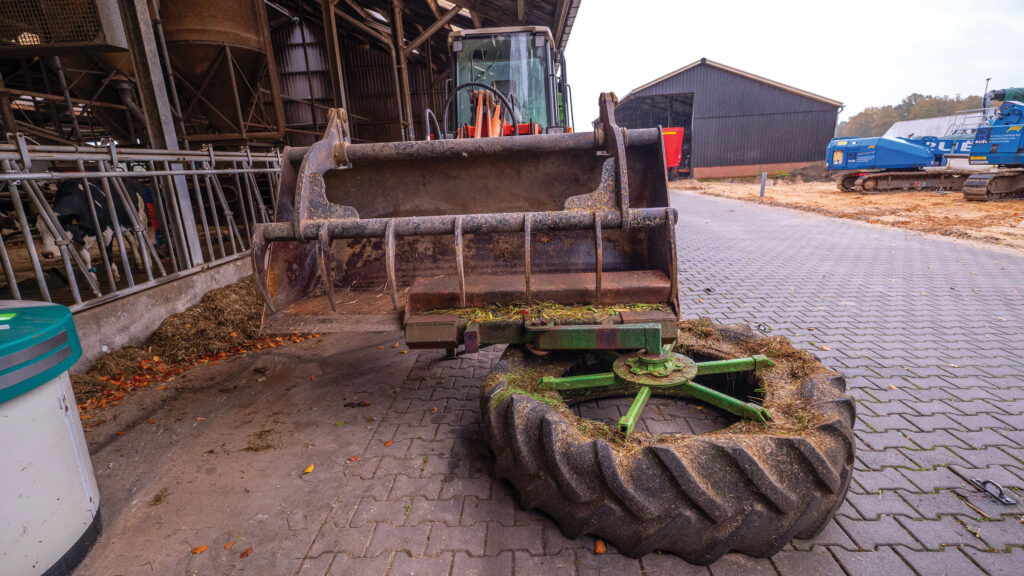
© Nick Fone
Typical autumn ration
- Fresh grass 11kg
- Grass silage 19kg
- Maize 15kg
- OSR meal 0.5kg
- Caustic oats 1.5kg
- Beet pulp 0.75kg
- Concentrate at robot fed to yield
Phosphate quotas
Dutch dairy farmers are required to buy phosphate quotas based on the volume of milk they produce.
While many focus on producing as much liquid as possible, Jeroen reasons that he’s better to aim to maximise milk solids, hence the mix of cross-bred cows.