Big tub grinders: UK options, costs and user verdicts
As more dairy and beef producers have been convinced of the advantages of pre-chopping straw before putting it into a mixed forage ration, competition for sales of large-capacity tub grinders has heated up.
The ultra-simple Roto Grind was the first tub grinder to enter the market, later followed by the Haybusters, with their ability to produce a finer end result thanks to the use of a hammer mill with interchangeable screens of different sizes.
More recently, Teagle Machinery has challenged the duopoly of these two US-built grinders with the Tomahawk C12 Calibrator, and it was joined in 2019 by the Welmac Straw Buster, sourced from China.
See also: Guide to buying used paddle-type feeder wagons
The aim of all these tub grinders is to process straw into a relatively fine material of consistent length for inclusion in cattle feed.
Straw can be used in this way to control energy intake in dry cow rations, and so reduce the risk of milk fever, and in milking cow rations to stimulate dry matter intake.
A fine chop length allows thorough incorporation with forage as the material is prepared in a total mixed ration mixer-feeder so that “picky” cattle are less able to select the more palatable ingredients.
Further work potential for contractors operating these machines include grinding hay for rations, coarse milling of straw for bedding and fine milling of cereal grains and maize kernels.
Milling as an alternative to rolling not only results in an ingredient that is easily incorporated into a feed, but is said to be a useful measure against starlings picking out grains.
Duratech Industries Haybuster H-1030 Big Bite
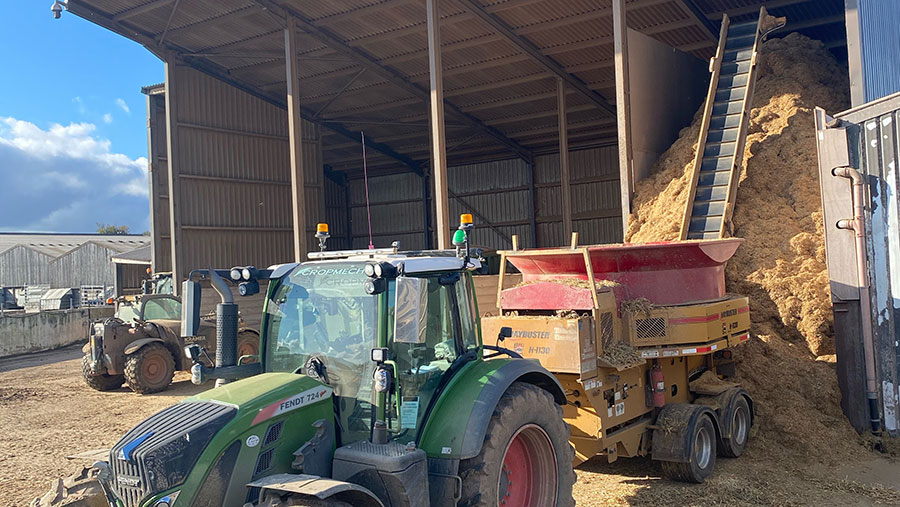
Haybuster H-1130 © Cropmech
The Haybuster H-1030 is one of four pto-driven tub grinders distributed for Duratech Industries in the UK by Enegis, based in Stratford, Warwickshire.
The H-800 with impeller and chute discharge is the baby of the range, while the “professional” models start with the H-1000, which Enegis says is commonly used by contractors offering a mobile straw processing service.
Those looking for greater performance now typically upgrade to the H-1030.
The larger machine has a heavier-duty (but no bigger) hammer mill and hydraulic, rather than mechanical, drive to larger-diameter augers beneath the mill feeding a longer, wider conveyor.
Vital stats: Haybuster H-1030 Big Bite
•OutputUp to 15t/hour
•Tractor power150-315hp (pto)
•Hydraulics Independent
Tub
• Loading height 2.79m (H-1000 2.44m)
• Width Base 2.43m; circular – 3.10m across, 3.10m front to back (H-1000 3.05m, H-1130 3.43m)
• Depth 1.13m (H-1130 1.27m)
• Drive Hydraulic
• Control On-board Wachendorf A35 load monitor and tub speed/direction controller; records individual job and total hours worked
Hammer mill
• Length/diameter 1,092mm/660mm installed on 76mm bearings (H-1000 1,130mm/660mm, H-1130 1,270mm/660mm)
• Hammers 64 case-hardened, four-way reversible, running at 2,140rpm (H-1130 88 hammers)
• Drive Tractor pto, eight belts
• Access Tub tilts to 90deg using hydraulic cylinder (H-1000 access panels)
• Screens Two quarter circle sizes from 2.1mm to 200mm
• Screen change Unlatch and lift out; no on-board storage
Discharge
• Augers Two 304mm diameter, hydraulic drive (H-1000 two 228mm augers, mechanical drive)
• Elevator 609mm x 6.40m, hydraulic drive (H-1000 457mm x 6.10m, mechanical drive, H-1130 7.92m)
• Max height 4.50m (H-1000 4.19m, H-1130 5.64m)
Transport dimensions
• Length/height 5.89m/3.07m (H-1000 6.14m/2.43m, H-1130 6.59m/3.21m)
• Weight 6,032kg (H-1000 4,100kg)
• Tow speed Various options
• List price £73,300, including screens; options include grain milling hopper £1,150, additional screens £280-£350
• Other models H-800 75-130hp £31,500; H-1000 100-140hp £57,800; H-1130 up to 315hp £82,500; H-1130 Electric £148,730
• Manufacturer/distributor Duratech Industries/Enegis
The H-1030 also has a tilting tub structure for access to the mill, its drivetrain and the lift-out quarter circle screens.
This feature is shared with the range-topping Haybuster H-1130, which has a larger tub and a longer 88-hammer mill for increased output, and is unique in the Haybuster range in being available with electric motor drive as an alternative to the tractor pto.
In addition to straw, the machines can be used for grain milling once the optional in-tub hopper has been installed.
Case study: Haybuster H-1130 – Cropmech
When Mark Stevens and his son, Elliot, decided to add straw processing to the services offered by Cropmech from their base in North Devon five years ago, they went for the top-end machine in the Haybuster range.
“The objective was to get more winter work, and one attraction of straw processing is that it’s not weather dependent,” says Elliot Stevens.
“It’s turned out better than expected, with a steady workload through the summer, as well as being very busy in winter.”
To reliably and legally cope with journeys of 30-40 miles, the Haybuster’s standard single-axle running gear has been replaced with dual commercial axles, suspension and air braking.
It’s hauled and powered by a 246hp Fendt 724, which is just fine for delivering an average output of more than 10t/hour, says Mr Stevens.
“We’re using four sets of screens with different size combinations – a 50mm and 75mm pairing being the most commonly used for processing straw for inclusion in rations,” he adds.
“A 30mm/45mm combination is preferred by some customers for feed and also for bedding, and we sometimes pulverise the straw through 8mm and 12mm screens for spreading into cubicles from a sand dispenser.”
A pairing of 2mm and 3mm screens is used at the Cropmech base when grinding grain and maize to a very fine crumb at about 40t/hour for use in rations where starlings are a problem.
“Unlike roller milling, which crushes the kernels and leaves large pieces that the birds can pick out, reducing grains to a fine meal makes it more difficult and reduces losses. There can also be advantages in the diet when feeding ground grain as opposed to rolled grain in certain livestock mixes.”
Burrows Enterprises Roto Grind Model 760
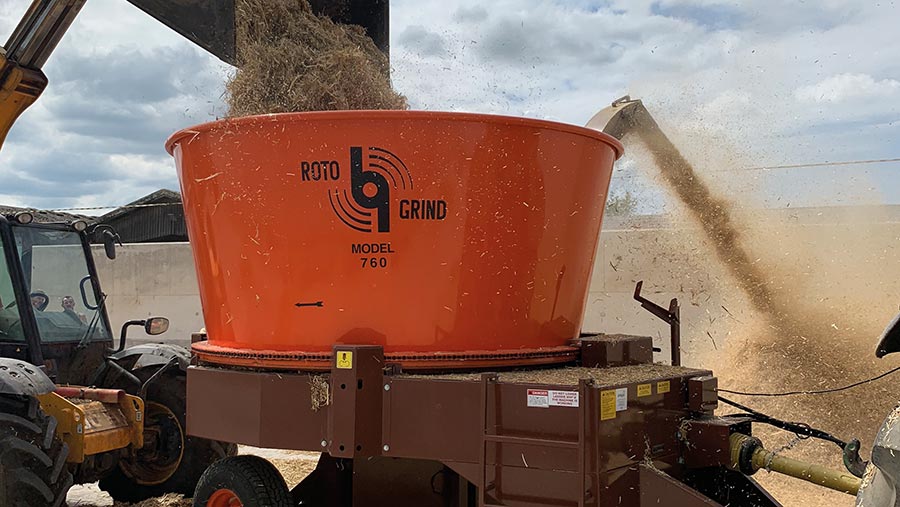
The Burrows Roto Grind has a narrow but large diameter mill that also ejects processed material though the adjustable discharge spout © Enegis
Simplicity is one of the appealing characteristics of the Roto Grind, as the machine has very few moving parts.
Apart from the rotating tub, there is just the hammer mill, which also provides the impetus to discharge processed material up the chute, while direct pto drive eliminates belts, chains or a gearbox. It is also comparatively light at about 1.6t.
Roto Grind Model 760 specs
• Output5-30t/hour
• Tractor power 70-200hp
• Hydraulics Tractor
Tub
• Loading heigh 2.59m
• Width Base 2.28m; circular 2.74m across and front to back
• Depth 1.30m
• Drive Hydraulic
• Control On-board electronic governor stops tub if tractor engine speed is pulled down excessively
Hammer mill
• Length/diameter 180mm/1,320mm
• Hammers 24 in six rows, 330mm (280mm swing), tungsten carbide faced and four-way reversible, running at 1,100rpm
• Drive Direct from tractor pto
• Access Opening panel
• Screen None; five adjustable shear plates
• Screen change Not applicable
Discharge
• Augers None
• Elevator None; impeller and chute with adjustable spout
• Max height 3.0m
Transport dimensions
• Length/height 4.39m/2.58m
• Weight 1,587kg
• Tow speed Various options
• List price £24,300; options include grain grinding hopper £1,240
• Other models Model 1090 170hp+ £26,300
• Manufacturer/distributor Burrows Enterprises/Enegis
The Roto Grind’s mill is narrow, with only four swinging hammers in each of the six rows – 24 hammers in total – because unlike other grinders, it is set at 90deg to the tub.
The amount of “bite” is regulated by an adjustable riser on the tub floor, so there are no bars overhead, and there are also no screens beneath the mill to regulate the size of material produced.
Instead, the hammers work in conjunction with five individually adjustable shear plates that project into the first half of the mill housing.
Easy cleaning and plug clearance are said to be among the advantages of this design, but Enegis acknowledges that it does limit how fine the end result is compared with a machine equipped with screens.
Case study: Roto Grind – NW Straw Grinding
Lancashire-based NW Straw Grinding has five Roto Grind machines, all uprated with modifications to meet the higher capacity demands of a contracting service.
“We started straw grinding five years ago and bought our first three Roto Grind machines within eight months, such was the demand from the many dairy farms in our area and further afield,” says Guy Hall.
“To get the output we need and a consistent product, we replace the standard adjustable shear plates with thicker, more durable ones and fit them securely into the mill housing. That allows us to put plenty of horsepower on the front to keep the hammers working effectively and consistently.”
One machine is used full-time for straw grinding, with a second brought into play to cope with demand peaks, accounting for about 80% of total workload, visiting four or five farms a day.
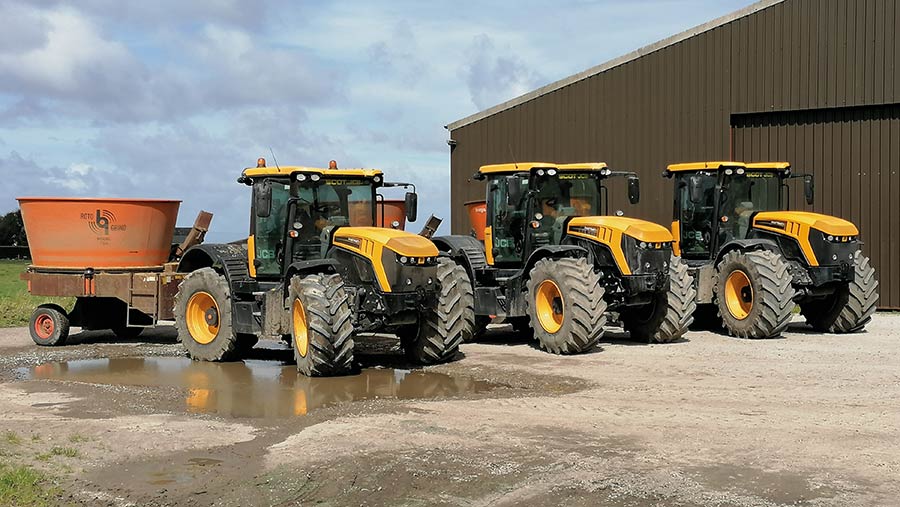
Roto Grind and Fastracs in the yard at Guy Hall’s NW Straw Grinding © NW Straw Grinding
Another pair have been modified to grind fodder beet, sugar beet and yard muck for an AD plant, which makes good use of blades worn down on straw grinding, and the fifth is a back-up machine.
A trio of JCB Fastrac 4000-series tractors tuned to 246hp provide pto drive and quick journeys.
“The Roto Grind is simple, compact and very light, so it’s easy to tow. However, we have bent the odd axle,” says Mr Hall.
“In ideal conditions with nice brittle wheat straw we can get up to 15t/hour with our modified machines but, like any other grinder, damp straw makes the job harder and slower.
“We’ve also done some grain and maize grinding with good results,” he adds.
Teagle Tomahawk C12 Calibrator
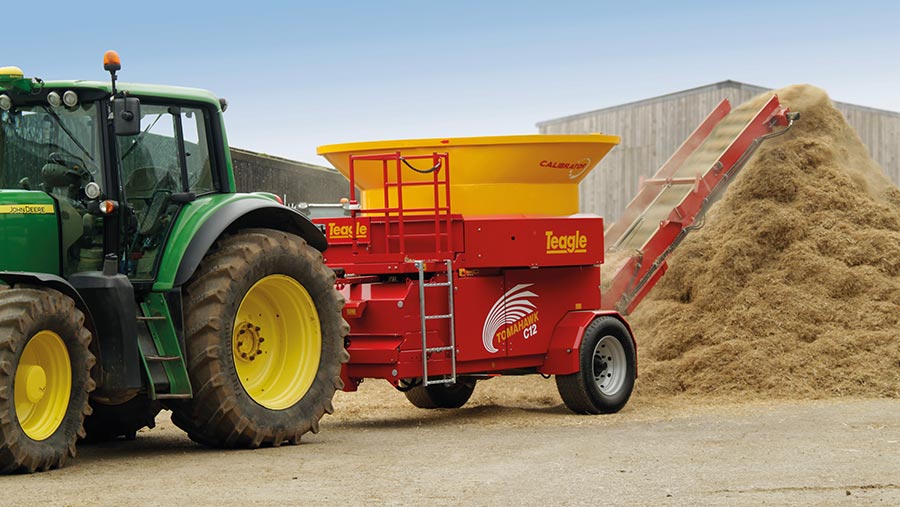
Teagle’s Tomahawk C12 Calibrator has interchangeable screens pulled from the rear of the machine at ground level © Teagle
Cornwall-based Teagle Machinery pitched into the tub grinder market for the first time in 2017 with the Tomahawk C12 Calibrator.
This trailed machine is considerably bigger than any of the firm’s traditional bedding/feed straw processors and is aimed at contractors as well as 600-plus dairy herds.
The company says consistent chop length, durability and easy operation were among key design objectives; the last of those led to the development of a Bluetooth-connected control pad that can be used in the loader cab to remotely monitor and control the Calibrator.
An on-board power management system automatically regulates tub rotation speed to keep the hammer mill (supported on rubber isolation mounts) and its 56 two-way reversible tungsten carbide tipped hammers spinning at peak efficiency.
The knives work in conjunction with two quarter-circle screens available in sizes from 13mm to 125mm.
The screens can be reversed or exchanged without clambering on to the machine by undoing four bolts and sliding out the frame on which they are mounted at the rear.
Tomahawk C12 Calibrator specs
• Output Up to 11t/hour
• Tractor power 120-200hp
• Hydraulics Independent
Tub
• Loading height 2.37m
• Width Base 2.20m; lozenge 2.20m across, 3.00m front to back
• Depth 1.10m
• Drive Hydraulic
• Control Remote (Bluetooth) electronic load monitor and tub speed controller
Hammer mill
• Length/diameter 1,136mm/693mm installed on rubber isolation mountings
• Hammers 56 in eight rows, tungsten carbide tipped hammers, two way reversible, running at 2,000rpm
• Drive Tractor pto, eight belts
• Acces Hinged covers
• Screen Six quarter-circle sizes from 13mm to 125mm
• Screen change Unbolt and slide-out lengthways to the rear; on-board storage for four spare sections
Discharge
• Augers None
• Elevator 610mm x 5.00m (up to 6.60m), hydraulic drive
• Max height 4.20m
Transport dimensions
• Length/height 5.97m/3.20m
• Weight 5,760kg
• Tow speed 40kph
• List price £71,650, including two screen sections; options include additional quarter screen £370-£665, trailer filling deflector £255, hopper for grain milling £6,050-£6,620.
• Other models None
• Manufacturer/distributor Teagle Machinery
Up to four spare screens can be stored in an enclosed compartment.
Unlike other tub grinders of this type, there are no transfer augers beneath the mill because material falls directly on the elevating conveyor, which unfolds and can be positioned at a 40deg angle to build a 4.20m-high stockpile – or fill a trailer using the optional deflector.
Other options include an in-tub hopper that equips the machine for milling wheat, barley, beans and maize, with screen sizes from 3mm to 10mm available.
An access ladder and railed viewing platform are located ahead of the tub, which is lozenge-shaped to minimise transport width.
The Calibrator has a contractor-friendly commercial axle as standard, with tyres and brakes that permit a 40kph travel speed between locations.
Case study: Teagle Tomahawk C12 Calibrator – Sampson Agricultural Services
Existing customers urged Mark Sampson to get into straw processing from his base in south Devon and he liked the idea of a service that would provide some winter work.
Three years later, he now has a good client base for processing jobs that range from coarse straw milling for inclusion in dairy cattle diets to ultra-fine processing for bedding cubicles and milling wheat, barley and maize.
His Tomahawk C12 Calibrator was ordered without seeing an example of the manufacturer’s first large-scale processor.
“I wanted a mechanically simple machine that would be easy to service and repair with readily available parts if we needed them, and of a size that wouldn’t be a problem on narrow lanes,” says Mr Sampson.
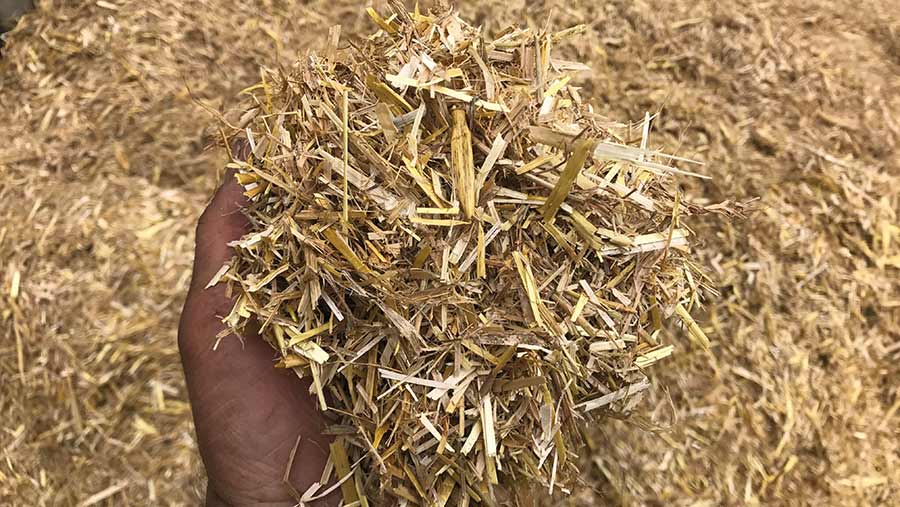
Teagle’s different screen combinations allow easy adjustment of straw length © Sampson Agricultural Services
“The Tomahawk seemed to fit the bill – and since getting it, we haven’t looked back; I think the only thing we’ve had to repair is a burst hydraulic hose and the use of standard bearings and other components means we can source replacements very easily.”
Also, extending the discharge conveyor beneath the mill to eliminate the augers found on other machines keeps the drive layout simpler, he adds.
Although the C12 is occasionally operated on a 250hp Valtra T234 and even a 165hp Valtra N174, a 275hp John Deere 6250R is mostly used to ensure there is plenty of power in reserve when presented with less-than-ideal materials.
“If you have nice, dry, brittle straw, you can get a decent work rate without too much power, but if you are processing damp straw using a fine screen, you really need plenty of grunt to keep up the throughput,” says Mr Sampson. “It’s all about horsepower.”
As his client base has increased, so has the variety of end products required and the number of screens employed.
“We mainly use six or seven different sets, typically producing 25mm material for dairy cattle diets, although more customers are asking for a finer product put through a 15-20mm screen. We’re also getting down to a combination of 4mm and 6mm screens to produce a really powdery material from a mix of wheat and oilseed rape straw for bedding cubicles, which users say their cows really like.”
Since adding the optional grain hopper, milling wheat and barley to add to total mixed rations, and also grain maize through 6mm and 8mm screens for a customer preparing home-grown feeds, has increased his processing hardware collection, some of which at least can be stored on the machine.
“Teagle’s slide-out design makes changing screens a five-minute job – undo a couple of bolts, pull out the rack through the back of the machine, undo another four bolts and you’re away,” Mr Sampson explains.
“It’s a bit of a dirty job, so we have a compressor and air tank on the tractor to get rid of the worst of the dust, but making the screens so accessible is a great idea in my view.”
Welmac F-1050 Straw Buster
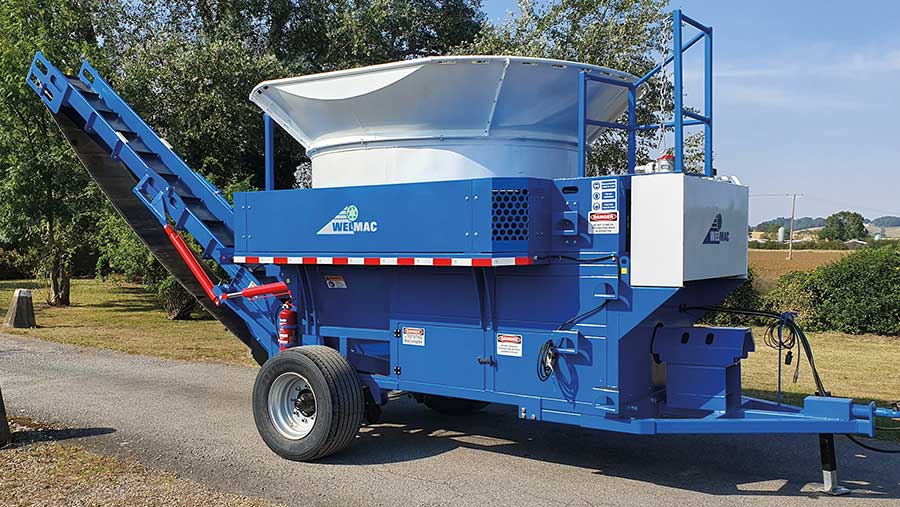
The Welmac F-1050 Straw Buster sports eight rows of tungsten carbide grit edged reversible blades on its 640mm-diameter mill © Welmac
A tilting tub assembly, lifted by a hydraulic cylinder and secured by a lockout bar, gives access to the hammer mill and driveline on the Welmac F-1050 Straw Buster.
The machine, manufactured for Welmac in China, has an electronic controller to set the hydraulically driven tub’s rotation speed, with pto speed monitoring for automatic regulation that helps maintain efficient operation.
The 920mm-long, 640mm-diameter mill has a bolt-in grate to support bales as they are processed and the 64 tungsten carbide grit hammers work in conjunction with a choice of rigidly mounted quarter-circle screens that lift out after unbolting.
Processed material is carried away from beneath the screens by two augers to the 535mm-wide, 5.80m-long elevating conveyor, which unfolds from above the tub to a maximum discharge height of 3.60m.
Welmac F-1050 Straw Buster vital stats
• Output Up to 15t/hour
• Tractor power 120-250hp
• Hydraulics Independent
Tub
• Loading height 2.82m
• Width Base 2.28m; top of flair 2.90m; 3.30m front to back
• Depth 1.29m
• Drive Hydraulic
• Control On-board electronic pto load monitor and tub speed controller
Hammer mill
• Length/diameter 920mm/640mm installed rigidly on 75mm bearings
• Hammers 64 in eight rows, tungsten carbide grit edged, reversible four ways, running at 1,800rpm
• Drive Tractor pto, eight belts
• Access Hydraulically tilting tub assembly
• Screens Quarter circle available in a number of sizes
• Screen change Unbolt, lift out; no on-board storage
Discharge
• Augers Two 280mm diameter, hydraulic drive
• Elevator 535mm x 5.80m, hydraulic drive
• Max height 3.60m
Transport
• Length/height 6.02m/3.30m
• Weight 5,500-5,900kg
• Tow speed 40kph
• List price £38,500-£43,000, including four quarter-circle screens; options include commercial suspension axle, super-single tyres
• Other models None
• Distributor Welmac
The tub – which is circular or with trimmed sides to meet transport width restrictions – and the augers and conveyor are all driven by hydraulic motors supplied by an on-board system independent from the tractor.
Hand- and footholds provide access to the railed upper bodywork and oil tank.
Case study: Welmac F-1050 Straw Buster – F A Priday & Sons
A cancelled order and a chance encounter at the Lamma show in January brought the F-1050 Straw Buster to Richard Priday’s contracting yard in Gloucestershire.
The machine was being shown at the event for the first time, and Mr Priday liked what he saw.
“We hadn’t gone to the show looking for a machine like this, but it seemed to have all the good points and some better features than the old tub grinder owned by a customer that we were operating,” he says. “We decided to take advantage of the opportunity.”
Having been delivered at the beginning of February, the machine was approaching 200 hours by early September, processing straw to add to rations on dairy units up to 30 miles away from home.
“It tows well enough, but could do with axle suspension to make things a bit easier on the machine,” says Mr Priday.
“In fact, the harsh ride resulted in some cracking on the elevator, which is suspended over the tub.
“We had a local engineer fabricate a cradle arrangement that now supports the folded end section like the booms on a sprayer, with the first section locked vertically in place.”
Features that get a firm thumbs up include direct hydraulic drive to large augers that take processed material away from the spacious area beneath the mill and the ease of changing the screens.
“The whole tub structure tilts upwards on a hydraulic cylinder and you then just lean over and pull the screens out.”
“The replacements drop into position and closing the tub locks them in place; it’s a simple arrangement, like the machine overall.”
A pair of 40mm screens is proving the most popular with large dairy units, but 50mm is available for producers and their nutritionists who want some a little coarser, as well as 30mm where a finer finish is required, and 20mm if there is demand for grain processing.
“We’ve used the Straw Buster with a 170-180hp tractor, but the 200hp John Deere 6210R we run on it now is about right to maintain a consistent result when you’ve got damp bales,” Mr Priday reports.