Ultimate guide to buying a round baler 2025
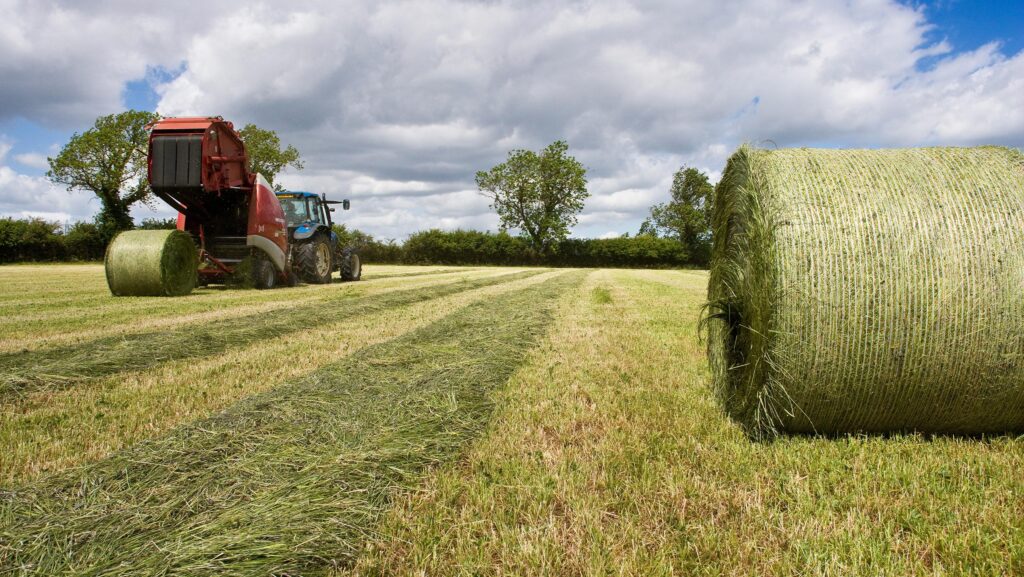
Tougher build and technology updates for faster and easier working are among the features of the latest round balers and baler-wrappers featured in our 2025 Ultimate Guide.
We look in detail at 11 models and you can download the complete guide below.
See also: Driver’s view: JS Haddy’s John Deere C441R Maxicut
Round and square baler specs
Download the complete 2025 guide to round and square balers
Case IH
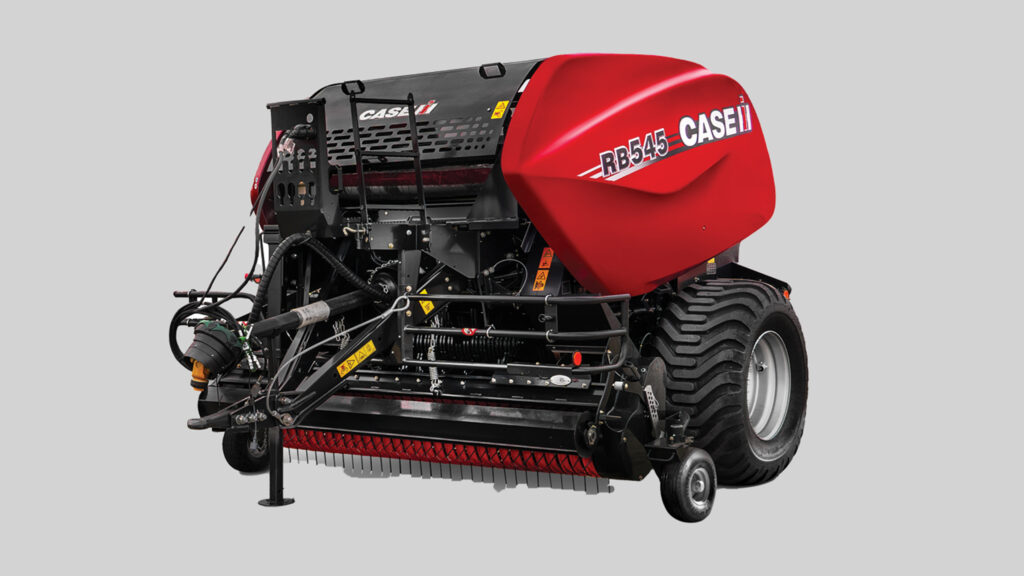
RB545 © Case-IH
Uprated chains and sprockets for the main drive, both bale chamber sections and the intake rotor drive aim to further improve the durability of Case IH RB545 and RB545 Silage Pack balers.
Greased bushings in various locations add to the updates package, while 38% faster tailgate opening speeds up bale discharge a tad.
Designed for farmers and contractors producing more than 7,000 silage bales a year, the machines form 1.22m wide, 1.25m diameter bales.
18 steel rollers now have a re-profiled surface to increase grip for reliable bale rotation and are mounted on auto-greased bearings.
Refreshed bodywork styling also heralds a more efficient rotor scraper and the option to fit a 1,000rpm pto gearbox.
On the bale wrapping Silage Pack version it is now tilted upwards slightly for improved shaft alignment.
Claas
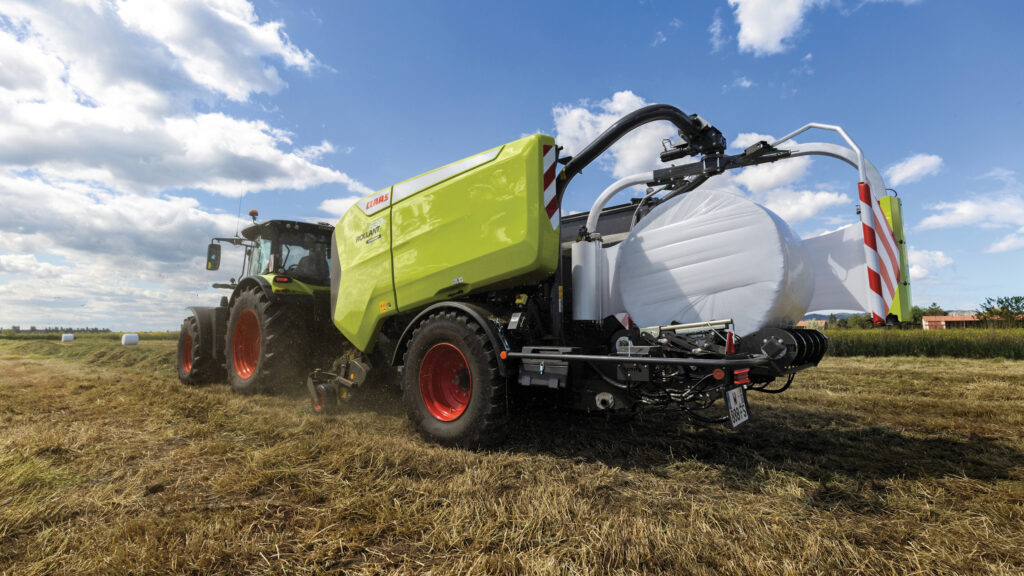
Rollant 630 Roto Cut Uniwrap © Class
Out go the Rollant 454 baler, the 455 baler and baler-wrapper, and into the Claas range comes the Rollant 630 Roto Cut Uniwrap baling and wrapping combination.
It has a number of beefed up components and other enhancements.
Unlike the 400 series machines producing bales of 1.2m diameter, the newcomer turns out slightly larger versions of 1.25m to 1.35m.
They use 16 steel rollers again and with the MPS (maximum pressure system) option creating denser packages of wrapped forage.
The MPS setup has three bale chamber rollers mounted on a frame that can be pivoted down into the void.
Once big enough, the bale then pushes them up as it grows to create a denser profile, heavier bales, and fewer bales per field.
At the front, the new 2.1m Multiflow pick-up with 1.9m raking width has five cam-controlled tine bars with reduced friction losses, trimming power requirement by some 20%, according to Claas.
Plastic strippers are now fitted for quick and easy maintenance access or replacement.
Thereafter crop is taken in by the familiar Roto Cut rotor equipped with 8mm double tines arranged in a spiral and forcing material across up to 25 knives.
A drop-floor aims to avoid intake blockages or at least make clearing them easier.
Drive chains subject to the greatest wear have been upgraded and wrap around larger diameter gears.
Guides on either side of the chain-tensioning wheels aim to prevent chains from slipping or shifting.
A larger oil container allows longer periods between refills for the auto lube system.
This can be complemented by an auto greasing system for the wrapping table, which has a stronger frame, rotates faster and comes to a stop more gently.
Also part of the upgrades package is a toughened chassis with 20% thicker steel profiles, running on larger wheels with up to 600/55 R26.5 tyres.
Fendt
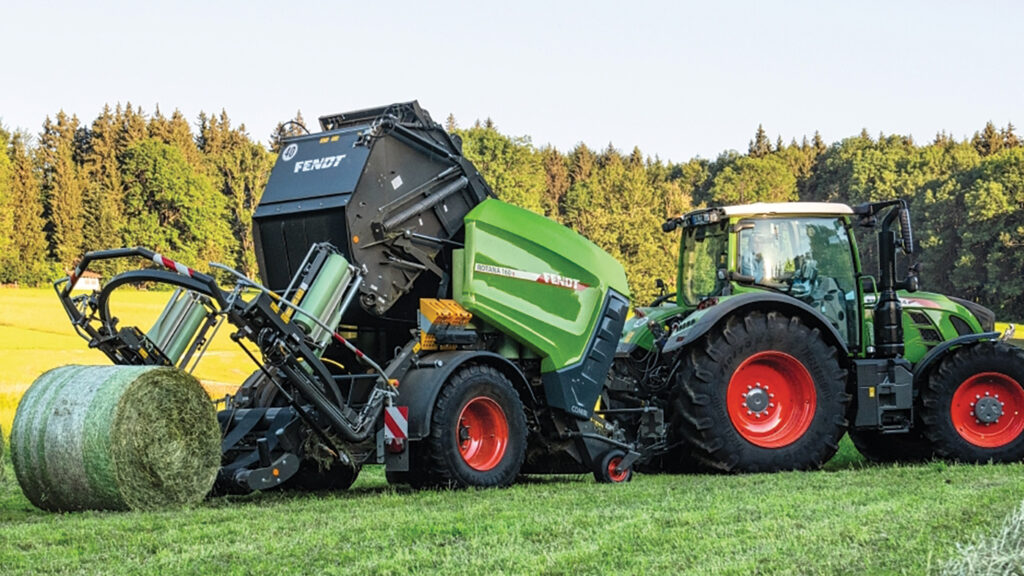
Rotana 160 V Combi © Fendt
Film binding, as an alternative to securing newly-made bales in plastic netting, has been extended to Fendt’s Rotana 160 V Combi.
The machine forms bales of 0.7m up to 1.6m diameter using three rollers and four belts.
The system, already available for the fixed chamber Combi baling and wrapping machines, stretches the film by a pre-determined amount regardless of the diameter of the film roll.
This helps it to achieve consistent “stickiness” and binding quality.
Film binding is reckoned to add to the oxygen exclusion performance of film wrapping and can save up to 3m of film per bale, says Fendt.
It also simplifies sorting and storage of materials for recycling since only one type of plastic is involved.
Net and film rolls are carried in a three-roll magazine for quick change-overs between the two – to meet different preferences or when switching from grass to straw baling, for example.
Also new is a “speed tailgate” option that can be engaged to open and close the rear section of the bale-forming clamshell faster.
It’s also available for all Combi and crop slicing Xtra balers in the Rotana range, with the potential to produce up to 30 more bales a day.
Other updates for these versions include manually or hydraulically folding pick-up support wheels instead of the previous detachable design, and automated dry matter control.
The latter feature weighs and measures the moisture content of each bale.
It then alters the diameter between 1.05m and 1.35m to maintain a consistent dry matter in each bale for greater accuracy in trading and feeding forage.
Goweil
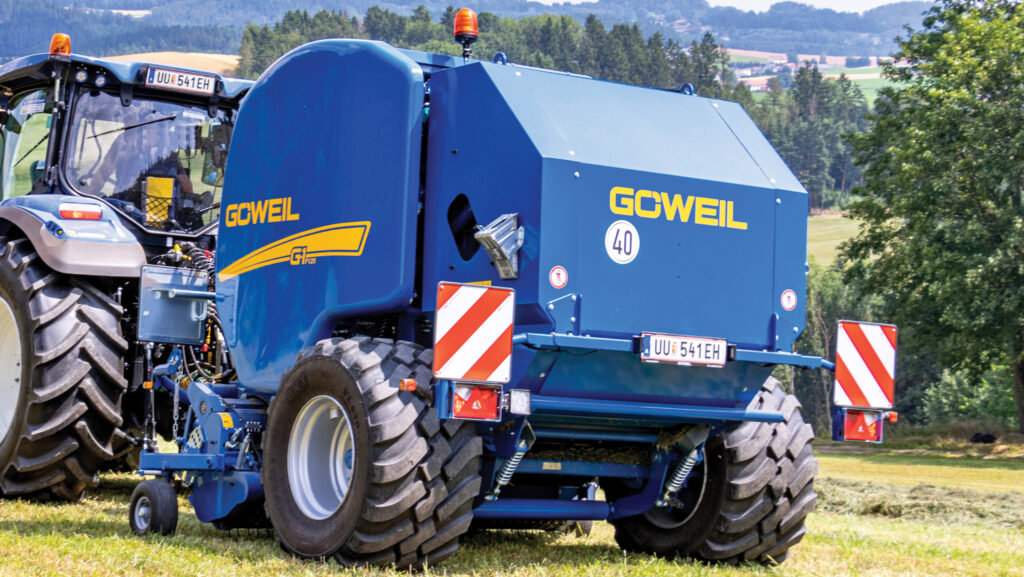
G-1 F125 © Goweil
A new listing in this year’s Ultimate Guide is Austrian manufacturer Goweil.
It has now appointed distributor GCB Agricultural Machinery, run by an ex-Lely sales manager with experience of Goweil’s “conversion” for adding a wrapper to a round baler.
Today, the firm produces its own round balers and fully integrated baler-wrappers, which produce 1.25m diameter packages of silage, straw, hay and so on using 18 steel rollers.
The G-1 F125 and its Kombi sibling are built to a heavy-duty specification.
It features 4mm (rather than typically 3mm) steel for the rollers, 60mm (instead of 45 or 50mm) double roller bearings for the majority of those rollers, and 65mm versions for the two driven rollers.
Up front, there is a double roller swath press, a six-bar pendulum pick-up reel with plastic strippers and a powered paddle roller overhead.
An over-shot six-star “V” rotor of 570mm diameter then pulls material into the intake throat and a bank of up to 30 crop slicing knives, which can be replaced using a spare knife bar on the baler.
Auto Flow Control is an anti-blockage system.
When a potential clog-up is detected, the intake paddle roller briefly switches from mechanical to hydraulic drive.
This keep material flowing while a section of the upper portion of the intake throat opens upwards to create added clearance over the rotor.
The lift door also opens if the rotor itself is overloaded, with the knives withdrawing automatically at the same time to clear the way.
An aggressively profiled starter roller gets material tumbling and the fledgling bale turning.
Once complete, the tailgate is opened and closed manually or under automatic control via isobus, which is another standard feature.
Auto (or manual) binding initiation for net or film is standard and a dual binding mechanism is available to apply two layers simultaneously or to apply net or film if frequently changing crops or preferences.
Kubota
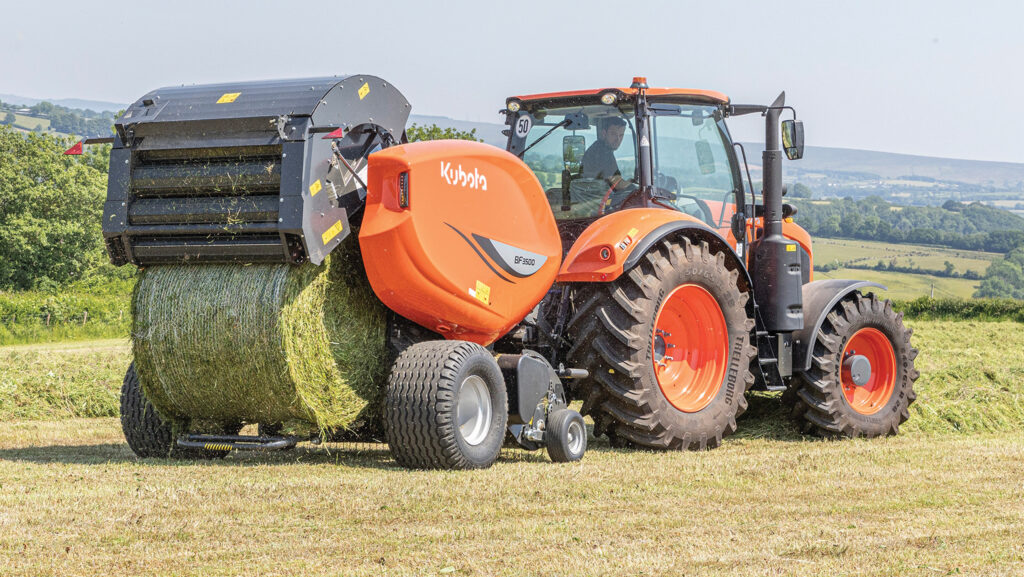
BF-3500 © Kubota
With isobus electronics now available on Kubota BF 3500 roller balers, users can take advantage of the TechnoPack.
It features moisture-sensing plates located in the lower part of the bale chamber.
These provide real-time measurement of moisture levels in the incoming material.
The percentage is displayed on a third-party or in-house IsoMatch Tellus isobus terminal, with the average for the bale as a whole shown during the binding sequence.
For operators working in catchy conditions, the moisture measurement and display helps them decide whether crops are fit for baling.
The TechnoPack also includes a bale ramp-triggered alert notifying that the discharged bale is clear of the tailgate.
Also available (for an unlock fee) is the TIM (tractor implement management) isobus function, which is also now available on the variable chamber BV 5200 Plus balers.
TIM enables a baler to take charge of certain functions on a TIM-enabled tractor, reducing the number of individual control inputs to produce each bale from as many as 10 to just two.
The Kubota version is conceived by Kverneland Group mechatronics engineers.
It slows the tractor to a halt and initiates binding, opens and closes the tailgate, and accelerates the tractor to working speed once the operator has set it in motion.
Reduced fatigue and the potential for increased throughout over long working days are chief benefits claimed for the system.
Kuhn
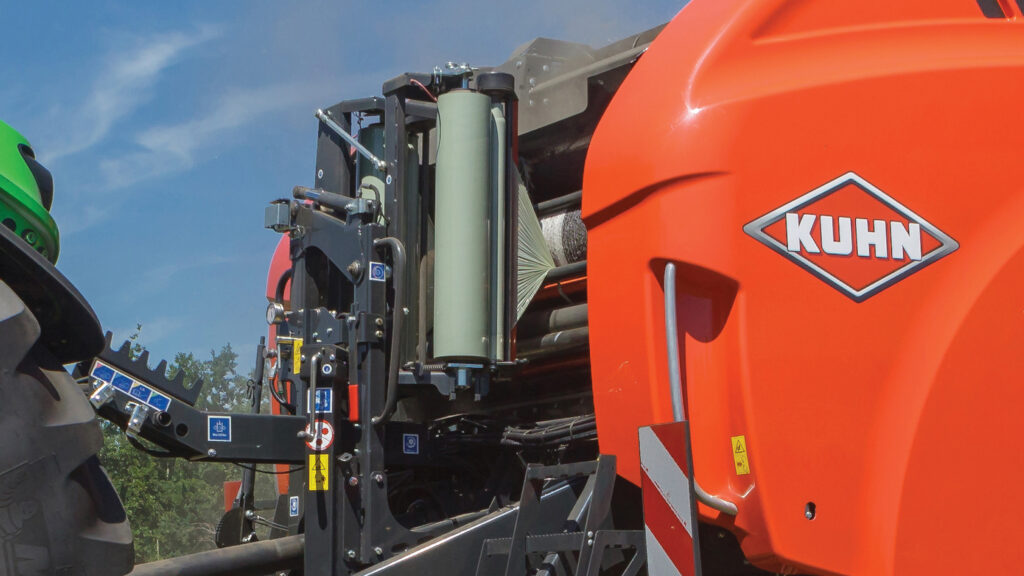
FB-3130 Twin-reel film binder © Kuhn
Film binding as an alternative to net is a new option for Kuhn’s FB 3130 roller-type round baler.
The Twin-reel system is unusual in deploying two 750mm rolls of film instead of a full-width roll.
One advantage is that replacements are lighter and easier to lift into position.
A higher stretch ratio provided by dispensers of the type used for bale wrapping result in the cost of film being up to 37% less.
The system is already established on the FB 3135.
Both machines produce a 1.25m diameter bale using 18 steel rollers.
The FB 3130 can be had in non-cutting Optifeed guise and with a 14-knife Opticut system.
The FB 3135 is Opticut only with a choice of 14 or 23 knives.
All versions are equipped with Kuhn’s Integral Rotor.
This has crop-gathering auger flights at each end of the double-tine intake rotor instead of employing separate stub augers as most other machines do.
Massey Ferguson
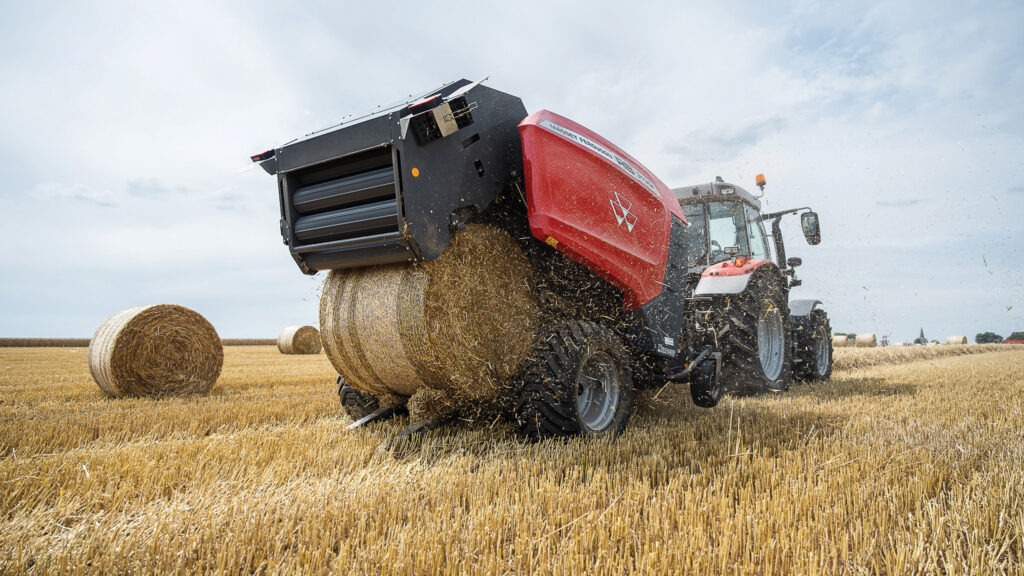
RB 3130F © Massey-Ferguson
Film binding to simplify in-field logistics, and sorting and storing of plastics for recycling, is now available on Massey Ferguson variable bale size RB Protec baler-wrappers.
Faster tailgate operation has been introduced on all but the Classic versions of MF’s fixed- and variable-size balers and baler-wrappers.
This is reckoned to add up to 6% or an extra four bales an hour to their output potential.
All models in the range can be equipped with an auto tailgate function when optional isobus electronics are added to the specification to reduce the operator workload a tad.
The weighing and moisture metering features can be had as standalone features rather than part of a package as previously.
There is also a new Bale Control Pro system running through the MF Fieldstar 5 touchscreen terminal as a replacement for the E-Link Pro controller.
This provides increased functionality as well as a higher-resolution display.
An added attraction of the film binding option is that it includes MF’s Rapid Reload mechanism.
This features a revolving storage system giving quick access to three rolls of film or a combination of net and film enabling operators to switch from one to another when required.
Binding the bale with film rather than net can reduce the number of film layers added to the bale on Protec wrapping balers.
When it comes to using the bales, there is only one type of film to store for recycling.
McHale
The introduction of four new fixed bale size models comprising the F5 series completes McHale’s wide-ranging updates to its entire line-up.
Like the V6 and V8 series variable bale-size machines and the Fusion baler-wrappers, the newcomers feature McHale’s Profi-Flo pick-up designed for improved crop flow into the intake area.
There is a choice of five-bar cam-operated or six-bar camless versions – both 2.1m wide and with stainless steel bands.
These are positioned ahead of the new Adaptive Intake, which automatically adjusts to the volume of the incoming crop.
This combination increases throughput potential, reckons McHale, while enabling the baler to cope better with uneven, lumpy swaths.
Isobus electronics feature for the first time on the company’s fixed chamber balers, having previously been rolled out on the “V” and Fusion machines.
It is not available on the non-chopping F5-540,.
However it is an option on the chopping F5-550, and is standard on the F5-560 and F5-560 Plus (which can bind with film instead of net) to include automated tailgate opening and closing.
New Holland
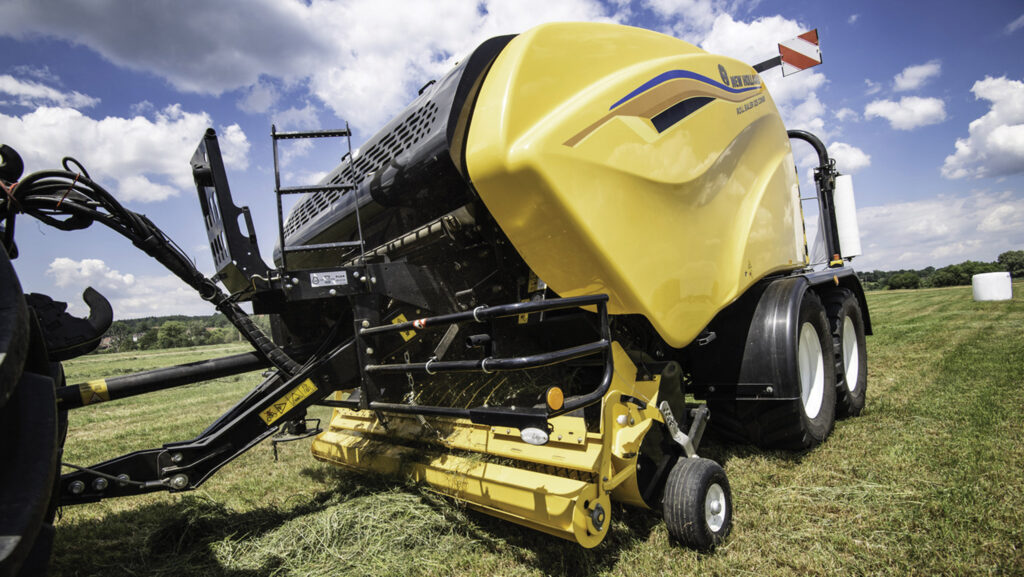
Roll Baler 125 Combi © New Holland
With refreshed bodywork styling giving a sleeker appearance, the New Holland Roll Baler in standalone and Combi baler-wrapper guises has been given a work-rate boost.
This is delivered by the simple expedient of speeding up tailgate opening and closing by some 40%.
The fixed chamber machines producing bales 1.22m wide and 1.25m diameter, have also been toughened up with higher-grade chain drives.
These feature in key areas such as the intake rotor and bale chamber for greater durability and reliability, especially when working in heavy crops.
Re-positioning the gearbox slightly eases the pto shaft universal joint angle and there is now a 1,000rpm pto option for both versions.
The addition of a scraper to guide material off the intake rotor is designed to prevent “back-feeding” and thereby minimise power consumption.
Detail changes have upgraded the drop floor mechanism’s durability, strengthened the connection between the Combi’s baler and wrapper structures, and reduced accumulation of dust and debris.
Both wrapping and non-wrapping versions of the Roll-Baler 125 are equipped with a 20-knife CropCutter slicing mechanism.
This works in junction with a 470mm diameter feed rotor fed via a 2.3m-wide five-bar double cam pick-up reel.
Bales are formed by 18 steel rolls, with tailgate latches holding the opening section firm until bales are fully formed.
Pottinger
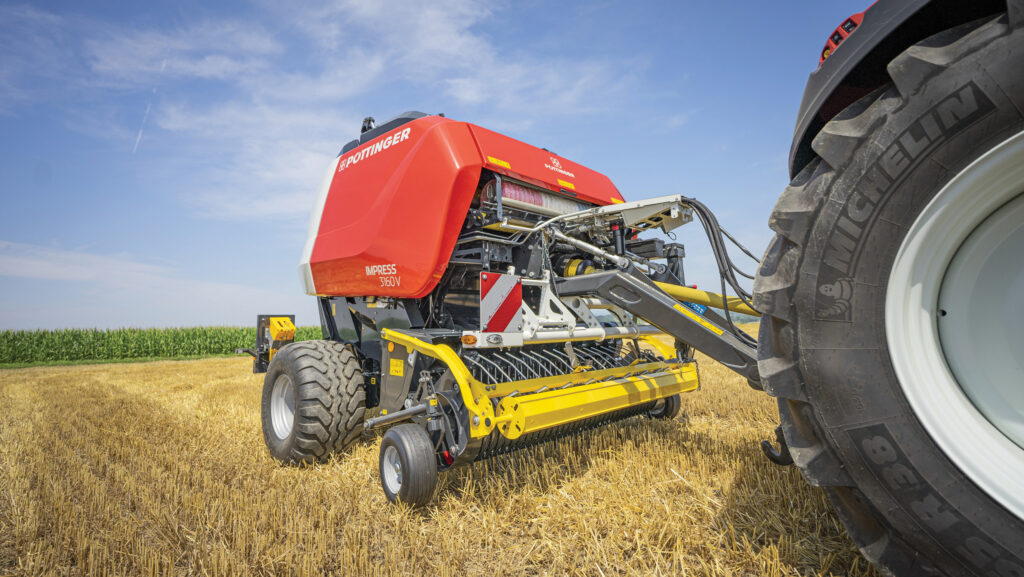
Impress 3160V © Pottinger
Previously optional on base and Master-spec models, all Pottinger Impress balers now come with isobus electronics as standard.
This provides touchscreen convenience for in-cab adjustments and monitoring of the baling process.
The isobus connection can be made with a touchscreen terminal already installed on the tractor.
Or a choice of three Pottinger displays giving different levels of functionality and screen size, and a choice of touchscreen plus buttons or touchscreen-only operation.
The Impress balers’ main novelty is the up-and-over crop flow arrangement, which takes the incoming swath over rather than under the 650mm diameter intake rotor.
An overhead bank of crop-slicing knives that can be pulled out to one side in a cassette for maintenance or replacement.
Vicon
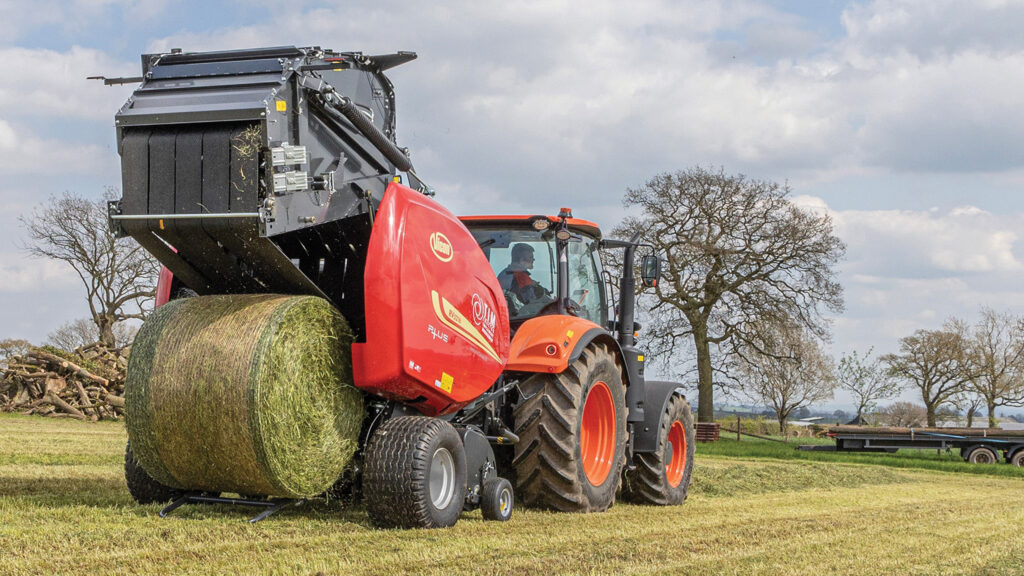
RV 5216 Plus © Vicon
Operators of the latest-spec FixBale 500 single bale size and RV 5200 Plus variable size balers can now enjoy a less tiring workload if TIM has been added to the options list.
TIM (tractor implement management) is an isobus application that takes command of selected functions on the tractor to automate them.
On the Vicon machines, the system is set up to provide a pre-programmed deceleration rate before bringing the tractor to a halt.
After this it initiates net binding, and opens and closes the tailgate once that process is complete.
Slope detection aims to prevent the tailgate opening where it is considered unsafe; that gives the operator the opportunity to manoeuvre the baler into a more secure location to drop the bale.
Normally, however, once the tailgate has been closed, the operator need only acknowledge a request to re-start.
TIM then responds with a pre-programmed rate of acceleration to the required speed.
On TIM-equipped RV 5200 Plus balers, an optional Techno-Pack can be added for bale moisture measurement.