Tips for buying a second-hand New Holland square baler
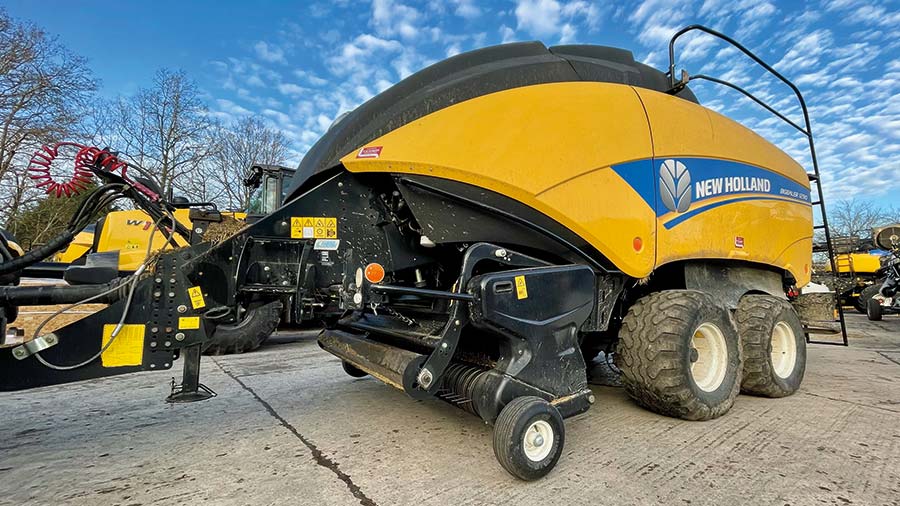
New Holland has a long history in the big square baler game, having launched its iconic D1000 four-stringer in 1987 and followed it up six years later with the equally popular D1010 – claimed to be the world’s first square baler with a silage-friendly chopper unit.
These first yellow-liveried (and later red) machines were developed and built at Zedelgem in Belgium, but their success spurred the company on to gain traction in North America and, unsurprisingly, everything was that little bit bigger on the other side of the pond.
In 1978, Hesston unveiled its debut big square baler – a six-string monster with a 120cm-wide, 127cm-tall chamber.
See also: Guide to buying a used hill-sider combine
Against the European four-stringers that were starting to come out of the woodwork (most notably from Vicon and Welger) in the 1980s, these behemoths offered a significant step up in capacity.
A decade later, the management at New Holland had bought into that idea, entering a marketing agreement with the Kansas-based big baler builder that was to last for three decades, despite Agco taking ownership of Hesston in 1991.
Alongside this rebadging arrangement for 4×4 Hesstons, New Holland’s Zedelgem engineering team was also busily working away on its own Europe-specific five- and six-stringers, albeit designed to produce flatter, rectangular-profile packages.
Introduced in 2001, the BB950 and BB960 were unusual in being five-string machines that pump out 120x70cm and 120x90cm bales, respectively.
With the aid of its US partner, the company ended up with a pretty comprehensive line-up, from 80x70cm four-stringers up to 120x127cm Hesstons.
As a result, there is a wide range of second-hand options out there for anyone looking into used New Holland square balers.
To get some advice on what to look out for on what are arguably some of the most popular machines in this area (alongside MF-branded Hesston products), we visited New Holland’s leading UK hay and forage dealer TH White.
Overall condition is the first thing to take into account and a baler that has obviously spent a good bit of its life outdoors won’t have fared well.
Although contractor-owned machines might have higher bale counts, they may well have received more thorough servicing.
Ideally, hitch the baler up to a tractor with the control box, hydraulics and pto all connected to ensure everything is functioning as it should. Then work through the baler methodically, from front to back.
PTO
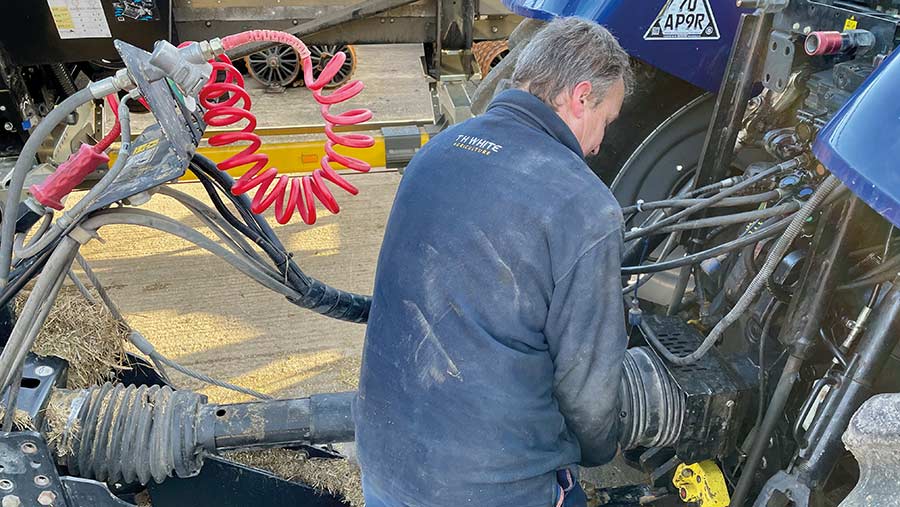
© Nick Fone
The two shafts that transmit drive from the tractor to the flywheel and plunger gearbox take a hammering because of the angles they run at, as does the centre support bearing.
Despite having a CV joint at the front end, the vibration generated when turning tightly means the UJ bearings and shaft guards have a hard time.
It’s not unusual to replace them every season, adding £400 to your annual running costs. Adjusting drawbar height to correctly match the tractor will help reduce the strain.
Interestingly, switching to a ball-and-spoon hitch shortens the drawbar, bringing the front CV joint into line with the hitch pivot point.
Because they then swivel in line around the same axis, the vibration generated during headland turns isn’t nearly so acute and, consequently, shafts and guards last much longer.
New Holland’s latest generation High Density balers use a mid-mounted step-up gearbox to keep the shafts running straight as they change level from the tractor to the flywheel.
Gearbox
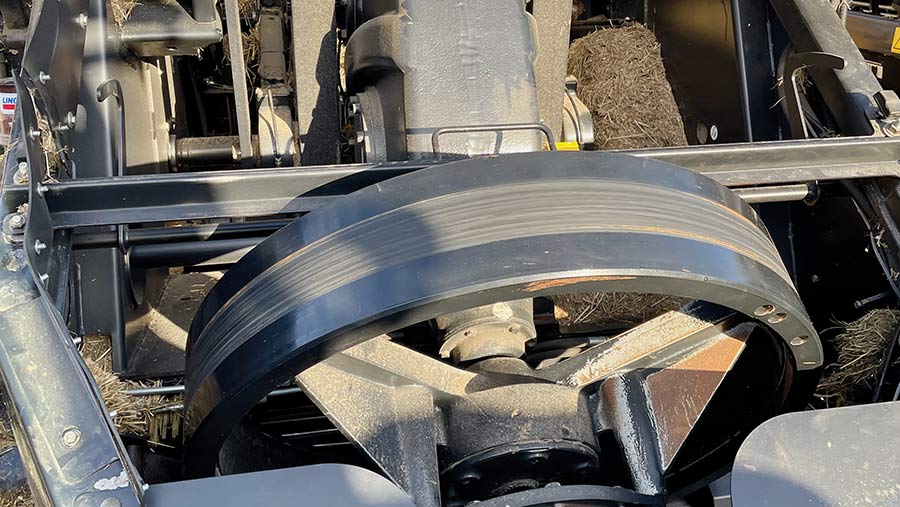
© Nick Fone
The main gearbox on these big balers is a beefy lump for a reason. They tend to be pretty bulletproof – TH White’s main baler man Pete Francis hasn’t replaced one in his 35 years of working on New Holland machines.
Packer drive clutch
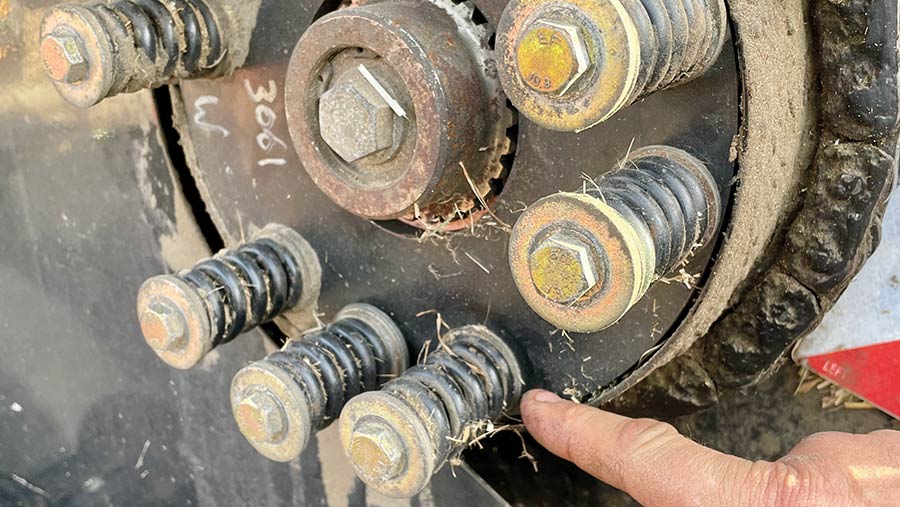
© Nick Fone
The packer drive clutch runs on a sealed bearing, which will probably fail at some point. The only way to diagnose whether it’s on the way out is to run the baler up and listen carefully.
The clutch’s phosphorus bronze friction plates tend to only wear out if the machine has done a lot of silage work and the first indicator of trouble will be interrupted pick-up drive when under load.
As a short-term measure, any slack can be taken up by packing out the clutch springs with washers.
The drive chain tensioner on a standard machine uses a threaded adjuster with coil spring damper.
On ‘Packer Cutter’ models there’s a bigger clutch pack with a rubber block damper for the tensioner – often this doesn’t provide enough give and the chains have a tendency to snap if the baler is pushed too hard.
Pick-up
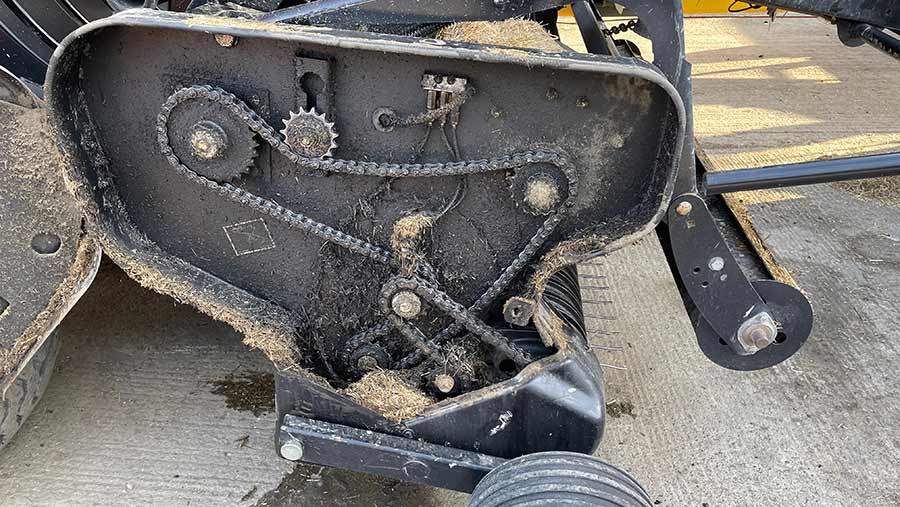
© Nick Fone
While New Holland four-stringers are generally equipped with 1.96m-wide pick-ups, six-string models get either a 2.23m- or 2.35m-wide unit.
These bigger pick-ups have a weak point, snapping the central shaft just inboard of the cam-bearings.
Check with a New Holland dealer to find out whether the machine in question has had the mod to replace the shaft with a beefier version (anything built within the last two years is likely to have been fitted with the more robust unit).
Also check for cracks where the pick-up cam bolts to the side plate, as this is often an area where fatigue can set in.
Stub augers
The lower set of augers that sweep material in from the outer edges of the pick-up can shear off. This can result in some ugly damage to the packer tines – look out for botched repairs.
Typically, this is only an issue with four-stringers because the augers are required to sweep material into a much narrower channel than wider-chambered balers.
Packer
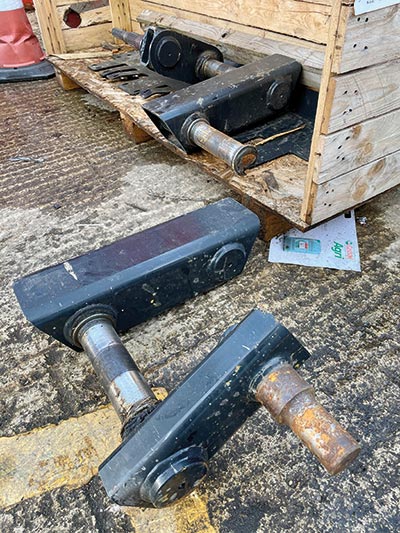
© MAG/Nick Fone
The packer crankshaft comes under heavy strain and can shear after two or three seasons’ work (around 30,000 bales).
It’s a couple of days work to fix, so is likely to make for a fairly hefty insurance claim. Annoyingly, without x-raying every component it’s pretty much impossible to know when it’s likely to occur.
Rotor Cutter models introduced three years ago have the benefit of a straight rotor shaft and therefore don’t suffer this issue. They’re also reckoned to run 20-25% faster than standard versions.
Pre-chamber
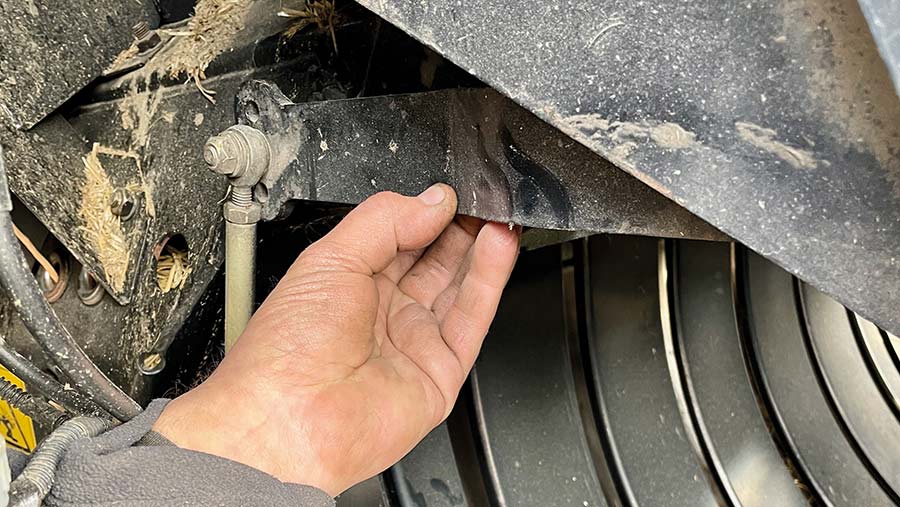
© Nick Fone
There are a number of elements within the pre-chamber to check over. First up, be aware that the friction material on the stuffer brake will tend to need replacing every 20,000 bales or so.
Grab hold of the stuffer trip cam linkage and check for play. It should be pretty tight, so if there’s any slack then it’s likely that the small shaft that the linkage pivots on has snapped.
It’s an easy fix if caught early, but if it drops out of its carrier it will cause the stuffer mechanism to seize.
At the top end of the pre-compression chamber there’s a row of claw-like retractable tines – holding fingers – that maintain pressure on the pre-packed wad until they’re prompted to trip out to allow material up into the main chamber.
The return springs can break but are simple to replace.
If the cross-shaft that these are mounted on has snapped, the baler will still run but it’ll struggle to produce decent bale shapes.
Frustratingly, for quite a simple component it’s not the easiest to change. Replacement will take two fitters three to four hours.Â
Plunger
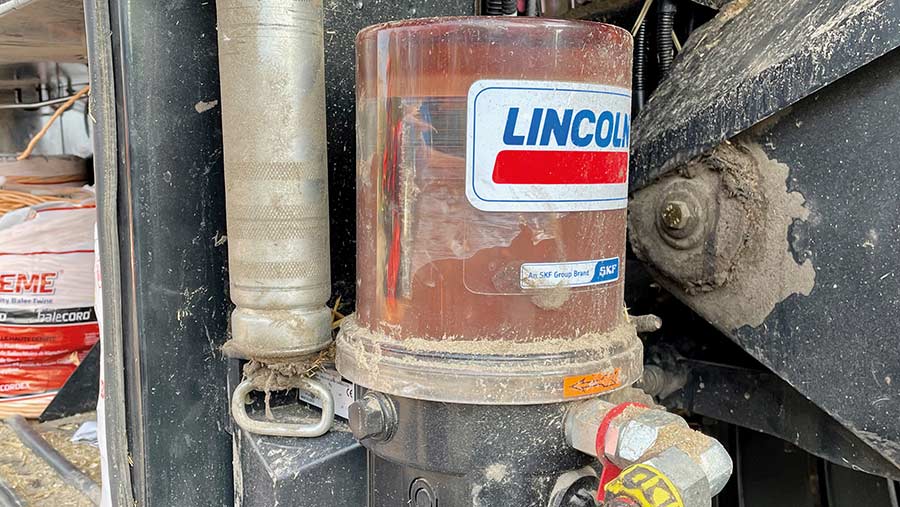
© Nick Fone
The four main plunger roller bearings rarely give any issues so long as their supply of grease from the auto-lube system isn’t interrupted.
Check that all the pipes are connected and haven’t been snagged – escaped grease should make any leaks obvious but if there’s any doubt, get the baler control box up and running and prompt it to run a test cycle.
It’s the same story for stuffer bushes and other components that rely on a regular supply of lube.
The fixed plunger knives can get knocked off by foreign objects so check they’re all still intact and, likewise, the cast points on the groovers that clear a path for the needles and strings.
If they’re broken then you can expect plenty of miss-ties.
Similarly, positioned on the side walls right at the front end of the bale chamber, the hay-dog wedges that hold the bale back away from the needles will cause knotter issues if their springs have snapped.Â
Up at the front of the bale chamber (right behind the gearbox) there’s a load-cell that monitors bale density.
It has a threaded adjuster bolt that is used to calibrate the system and this can shear, making it impossible to get the bale density set right.Â
Needles
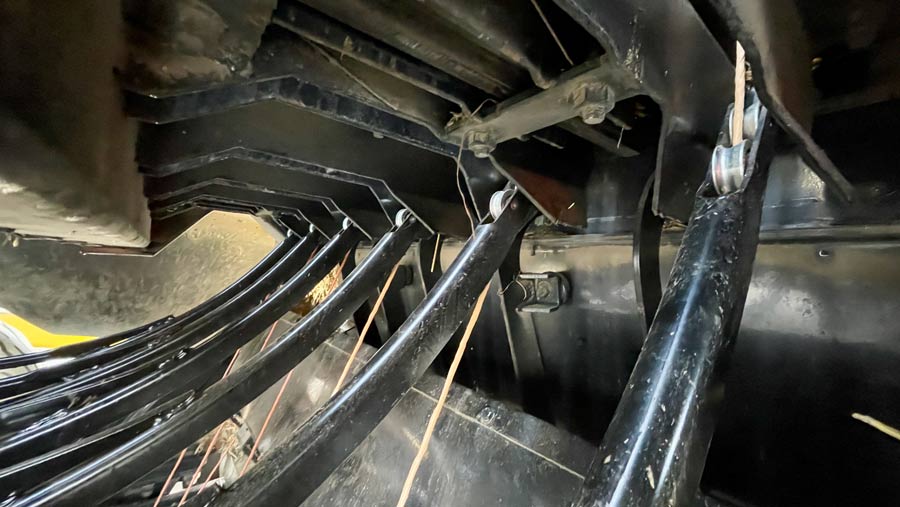
© MAG/Nick Fone
Other than looking for needles that have been snapped and botched back together with electric glue, the only thing to check is that the twine rollers run freely.
If the baler has done a lot of silage work then its bearings may fail, trapping strings and snapping them.Â
Knotters
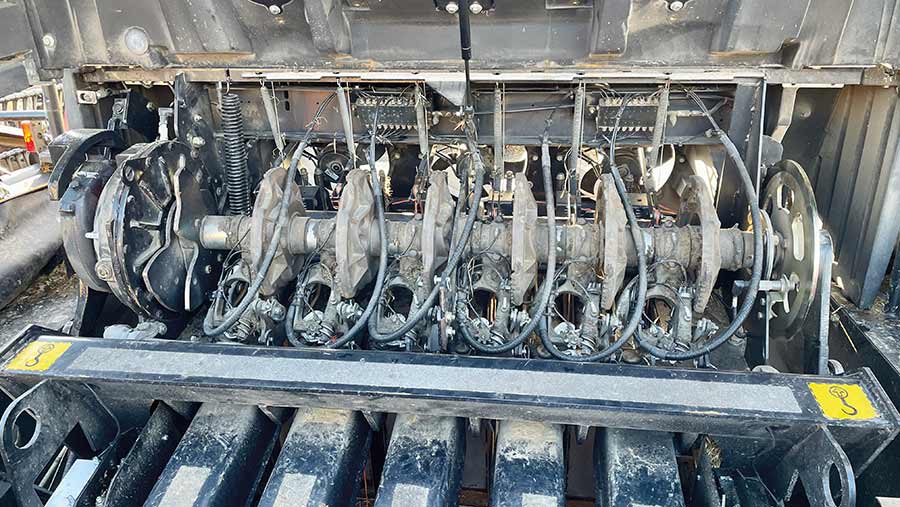
© Nick Fone
New Holland big balers double knot each string. The knotters are industry standard Rasspe units that are pretty reliable.
First up, check that each of the bill-hook tongues is in place.
Then have a look at the tucker finger plates – if the lug on the top left corner snaps off then the finger can over-centre and break the end of the knife arm off.
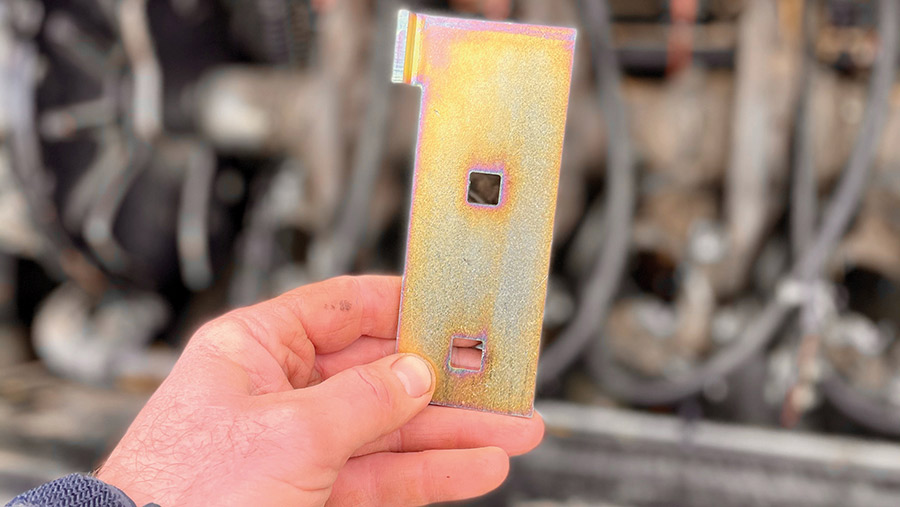
© Nick Fone
If any tucker finger springs are missing then it’s likely that the knotter won’t tie. Equally, look out for broken spring clips on the twine retainer, which will have the same effect.
Spec-savers
Aside from the obvious choices of bale size, there are a raft of options that will have an impact on the second-hand value of big square balers:
- Running gear – a tandem-axle baler will generally command a £3,500-£4,500 premium over a single beam machine. Add passive rear steering and 560mm wide rubber into the mix and you can expect to pay a further £1,000-£2,000.
- Bale weigher – load cells on the tailgate are a sought-after extra, adding at least £2,000 to the price tag.
- Moisture meter – coming in at over £2,000 new, expect moisture sensors to hike the price by at least £1,000.Â
- Electronic bale length – although it’s a nice-to-have feature, the extra complexity of having in-cab adjustability of bale length means it won’t add anything to the ticket price of a used machine.
What to pay?
There’s no hard and fast rule for what you should pay for used big balers, but it will clearly depend on their age, bale count, spec and general condition.
Here are a few examples of machines currently up for sale or recently sold to give a guide, along with commentary from independent Lincolnshire-based dealer George Starling.
New Holland BB9090 (equivalent to MF 2190)
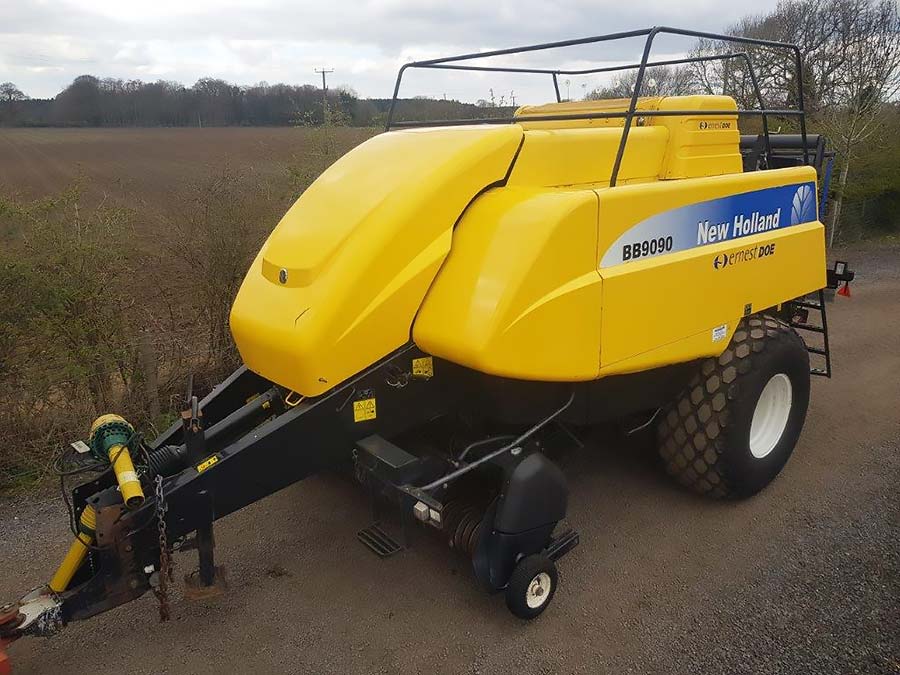
© MAG/Nick Fone
- Year: 2009
- Bale count: 47,676
- Bale size: 120x127cm, six-string
- Extra spec: Roller tailgate
- Guide price: £23,000-£27,000
Comments: Fairly low bale count for the year of manufacture.
The BB9090 offered a massive improvement in output and bale weight over the BB980 and MF 190, so examples such as this are often bought by straw contractors as a spare machine to ease the pressure at harvest – meaning they might be producing 4,000 rather than 10,000 bales/season.
Like most of this age, it has been welded under the knotters.
New Holland BB960
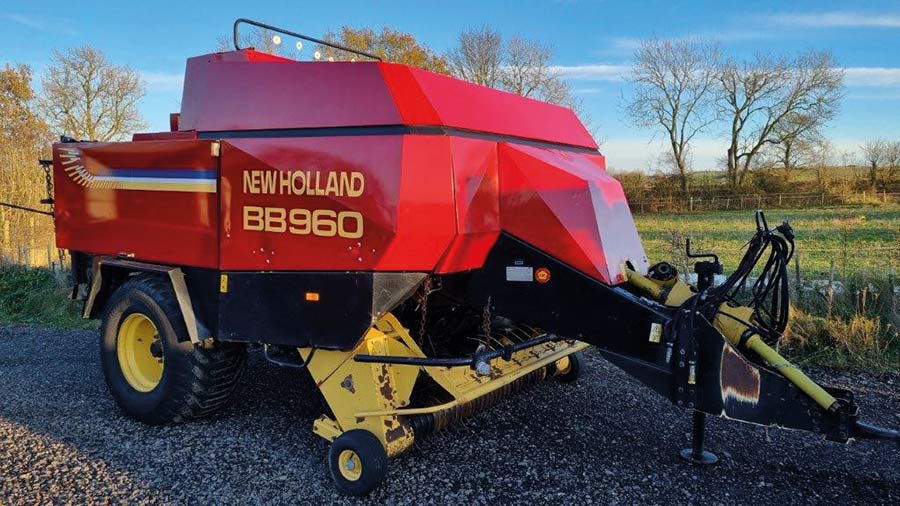
© Nick Fone
- Year: 2000
- Bale count: 68,551
- Bale size: 120x90cm, five-string
- Extra spec: Air brakes, bale ejector and roller tailgate
- Guide price: £14,500-£16,500
Comments: Particularly low bale count considering the year of manufacture and it appears in decent enough condition, so will probably be quite capable of knocking out a couple of thousand bales a year.
It’s less money than an MF 187 of the same year and bale count, but will struggle to complete in output and bale weight.
New Holland BB1290
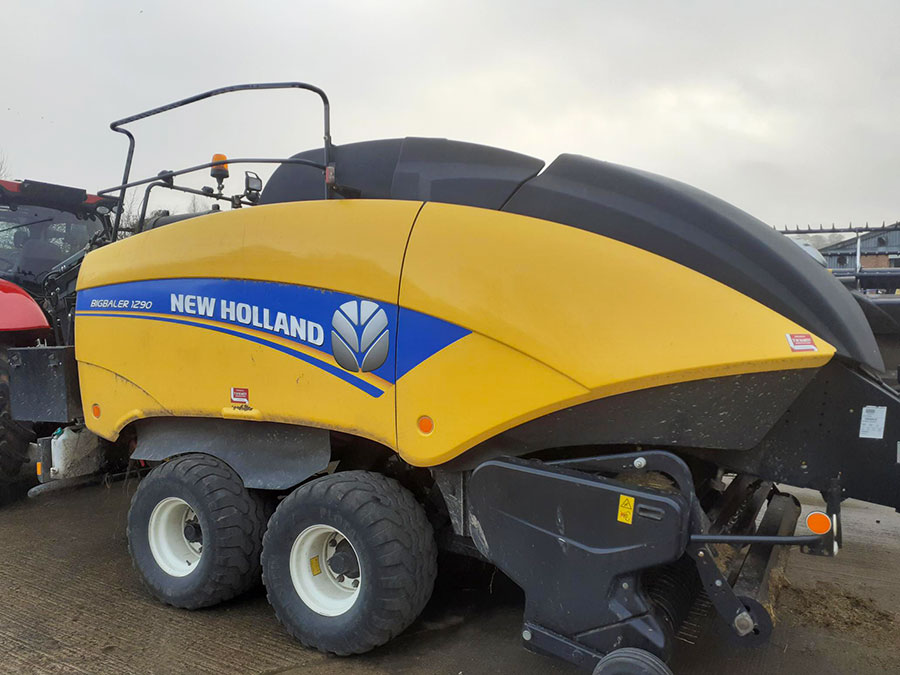
© MAG/Nick Fone
- Year: 2016
- Bale count: 30,000
- Bale size: 120x90cm, six-string
- Extra spec: Automatic greasing, two-piece roller chute, partial and full bale eject, bale weigher, moisture sensor
- Guide price: £53,000-£57,000
Comment: Good, solid baler, but it won’t match a high-density machine for bale weight in dry straw – something that is reflected in the price. Later ‘Plus’ models will produce far denser bales.Â
New Holland BB890
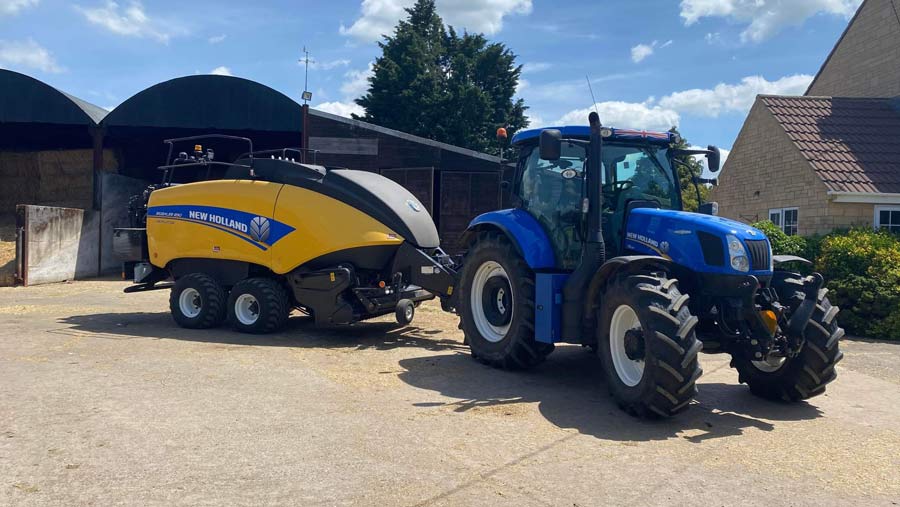
© Nick Fone
- Year: 2019
- Bale count: 27,000
- Bale size: 80x90cm, four-string
- Extra spec: Packer Cutter, automatic greasing, two-piece roller chute, partial and full bale eject
- Guide price: £61,000-£65,000
Comment: Bale count marginally below the average. New Holland 80x90cm balers are often the machine of choice for grass specialists as they consistently produce good-shaped bales with even density.
By comparison, early examples of the equivalent MF 2150 sometimes struggled to get enough grass in the top of the bale.
There aren’t many recent balers of this size on the second-hand market, but the single axle lets it down slightly.
New Holland D1010
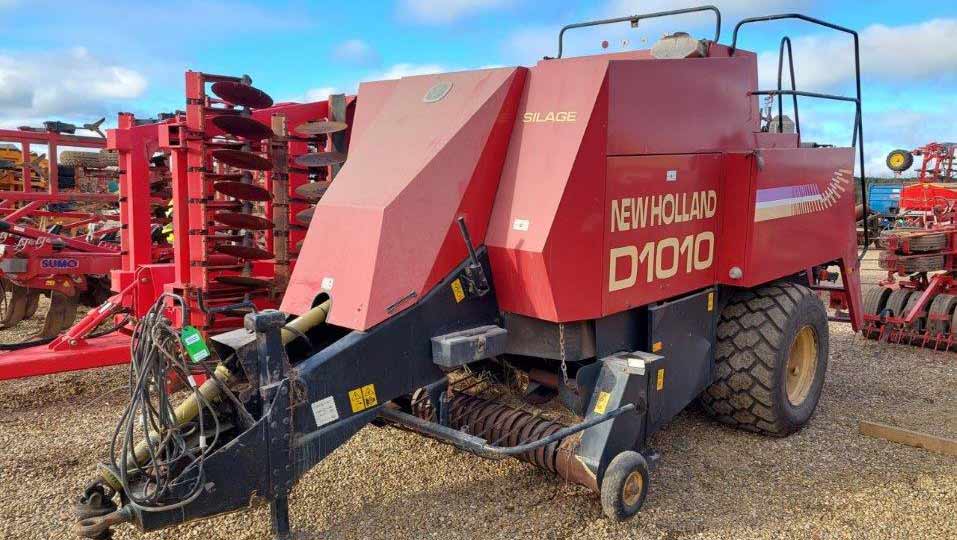
© Nick Fone
- Year: 1999
- Bale count: 15,768
- Bale size: 80x90cm, four-string
- Extra spec: Silage kit, roller tailgate, bale ejector
- Guide price: £9,000-£12,000
Comments: A very sharp example with no signs of excessive use, which goes some way to backing up the incredibly low bale count.
The popularity of six-string slab balers means it is getting harder to find tidy four-stringers, but the 80x90cm bale has a slight edge in the straw market if someone specifically wants the smaller size flakes to spread by hand.
The D1010 will hold its own against an MF 185.
Case 424RXL (exactly the same as a New Holland 1270)
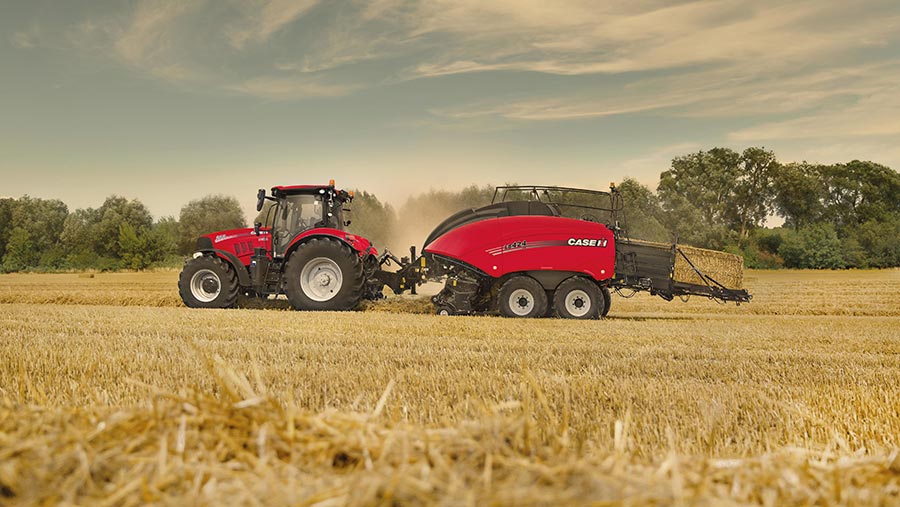
© Nick Fone
- Year: 2017
- Bale count: 20,600
- Bale size: 120x70cm, six-string
- Extra Spec: 15-knife rotor chopper, chain lube, moisture meter, electric bale length, weigher, rear camera
- Guide price: £48,000-£53,000
Comments: This example is fully loaded with everything bar air brakes.
It can’t consistently match the bale weights produced by an MF 2260 (circa 400kg) in wheat straw, but might cost £10,000-15,000 less for the same age and spec.
The 120x70cm size bale represents best value per cubic metre of material – almost comparable with high-density bales.
Wildcard – Fendt 1290NXD (equivalent to MF 2270XD)
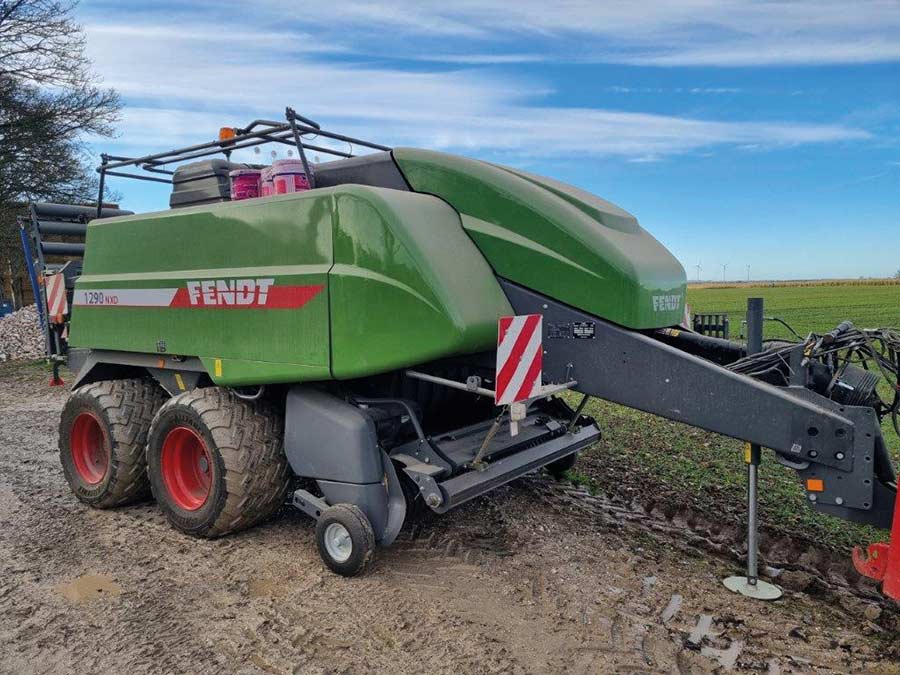
© Nick Fone
- Year: 2021
- Bale count: 13,106
- Bale size: 120x90cm, six-string
- Spec: Weigher, air brakes, 620/40 R22.5 tyres
- Guide price: £115,000-£130,000
Comments: Will clean up like new and this model still has most of its five-year, 50,000-bale warranty intact (one-year warranty is standard).
It will comfortably make a 500kg bale in wheat straw, but it needs a tractor of at least 250hp on the front.
There’s a strong export market for this specific model, so examples are hard to find.