Massey Ferguson unveils new twin-chamber conventional baler
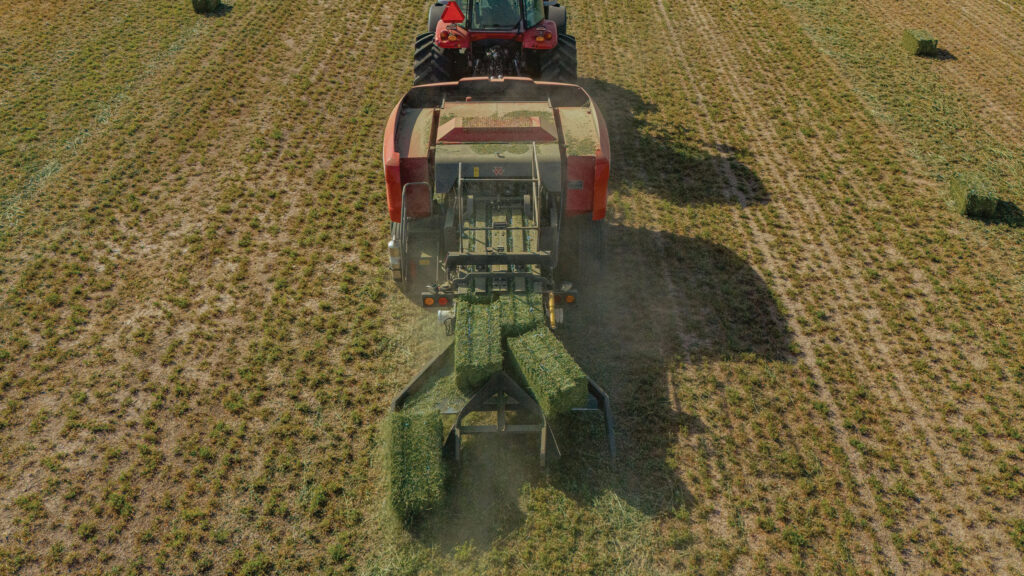
There has been a flurry of new developments in the small baler world in recent months, the latest of which was Massey Ferguson’s launch of a new twin-chamber conventional baler at the National Farm Machinery Show in Louisville, Kentucky.
Loosely based on the company’s Hesston-built in-line small balers, the snappily-titled SB.1436DB produces two bales at one time, apparently doubling output when compared with a single chamber machine.
As material is lifted off the deck by the 2.6m wide pick-up, it passes into a single 90cm wide, 35cm high chamber. Here, it is separated by a splitting knife to create pairs of 46cm wide conventional bales.
See also: Farmer builds ingenious twin-chamber double square baler
These then pass into the compression segment where density is controlled hydraulically.
Left and right chambers have independent knotter trip arms – a design said to ensure uniform bale lengths irrespective of swath consistency or the machine’s position over the row.
Bale monitoring
This is all aided by Hesston’s clever Simplebale monitoring system that automates certain elements of the baling process to ensure uniform densities and dimensions.
From the cab, operators can keep an eye on key functions such as flake counts, flake thickness, bale weights and lengths. Massey says this can have a big impact when it comes to improving output.
“Just by averaging an extra two flakes per bale an operator can lose 71 bales per hour,” explains Dane Mosel, Massey Ferguson/Hesston marketing manager.
“With a target weight of 18kg and 12 flakes per bale, that equates to 1.43t of productivity lost each hour. Simplebale eliminates this issue by automating bale production, helping operators achieve better results.”
Running at 90 strokes per minute with a 1,000rpm pto, the MF SB.1436DB requires a minimum of 120hp up front.
The company recommends that tug tractors should be at least 5t over the weighbridge to avoid getting bossed about by the baler.
The twin-chamber Massey’s twine-lockers can apparently hold up to 20 balls of string – enough to pump out up to 8,000 bales before refilling.
To further limit downtime, it’s also fitted with auto-lube for the knotters.
But, sadly, MF says it has no current plans to bring the new machine across the pond.
Paksan
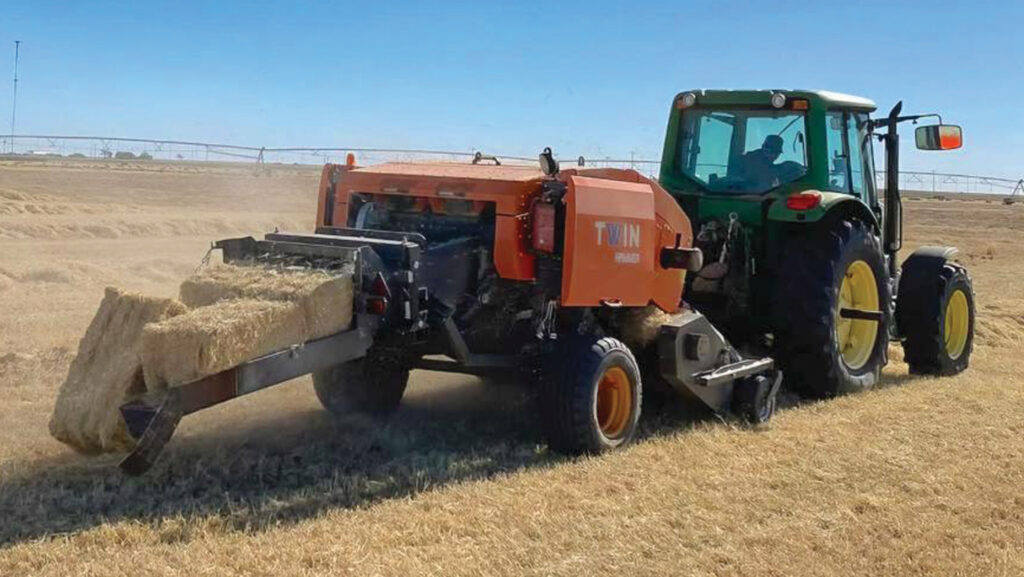
Paksan’s Hammer Twin produces either a brace of conventional-sized three-stringers or one extra-wide flat-pack six-stringer © Paksan
Last season, Turkish baler maker Paksan sent its own double-chambered small baler out for evaluation in the US.
Dubbed the Hammer Twin, it produces pairs of three-string bales 36cm high and 46cm wide. It, too, has a splitting knife dividing the bale chamber, but this can be removed to create 92cm wide six-stringers.
It also differs from the Hesston-built machine in that it can have an optional helter-skelter arrangement fitted at the rear so that bales are dropped in a single row, rather than in two lines.
This key feature means it’s possible to tow a sledge or bale accumulator behind.
The Hammer Twin has a 1.8m wide pick-up and requires at least 90hp at the flywheel. It’s claimed to be capable of pumping out 500-600 bales/hour, with bale weights of up to 40-50kg in straw and 50-70kg in hay.
Paksan says it hopes to have one working in Britain this summer with importer Bale Baron UK.
Custom builds
But twin-chamber balers are nothing new. Back in 2019, Farmers Weekly featured a one-off, custom-built double-barrelled baler built by Virginia farmer Rusty Inskeep.
Consisting of two New Holland BC5070 conventional balers conjoined at the pick-up, it will apparently fire out double rows of bales at a rate equivalent to three standard machines.
It was a similar story for the Grady family in New Mexico, who developed their own side-by-side in-line machine – the Twin Pak – out of a necessity for greater output.
In 2022, they signed a deal with John Deere that saw the balers retailed through the green giant’s dealers. No sign of them this side of the Atlantic as yet, though.
JB Industrie accumulator
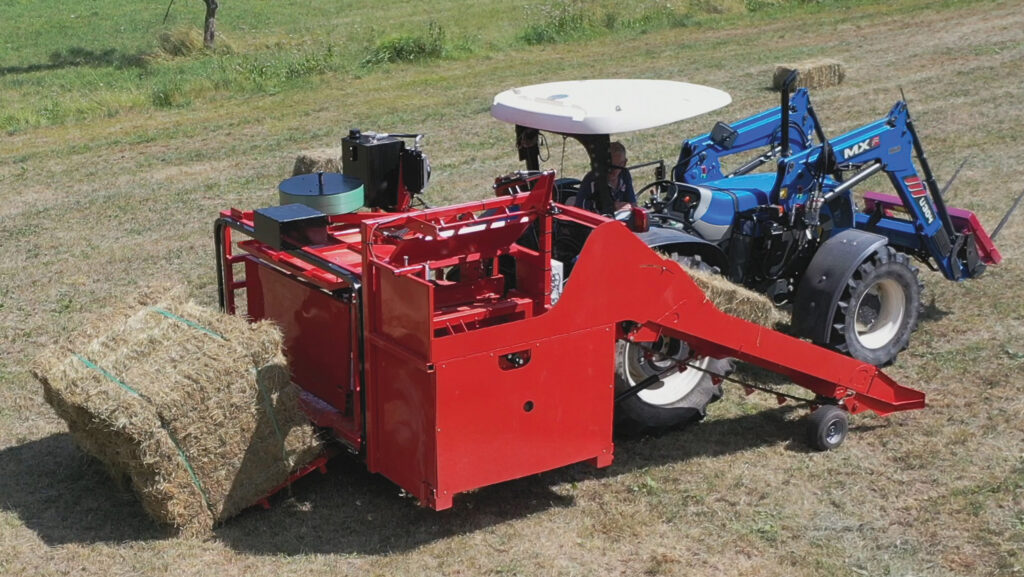
JB Industrie’s linkage-mounted PackBale accumulator bundles up 10 or 12 bales and straps them together © JB Industrie
While all these concepts might boost daily bale counts, the idiot bricks they pump out still have to be cleared off the field – nobody’s favourite task.
There are various bale accumulator and sledge options well established in the market, but a new contender from across the Channel is keen to get a foothold in the UK.
Based in south-east France, JB Industrie builds a simplified bale accumulator that is linkage mounted rather than trailed behind the baler.
Called the PackBale, it uses a chain and slat conveyor to pick up individual bales, stack them one on top of another, shunt them sideways, and then pack them into bundles of 10 or 12.
According to the company, the key to simplicity is to avoid rotating the bales by keeping them in line with the direction of travel.
Although vague on pricing, JB says the capital cost of the PackBale is a fraction of competitor machines from the likes of Bale Baron and Bale Bandit.
Recognising that having a separate implement requiring yet another in-field pass might not float everyone’s boat, the company tells us plans are in place to develop an integrated baler-accumulator that will combine two machines in one.
JB Industrie also makes a range of bale sledges that can produce flat-packs of eight to 18 bales.
Either trailed behind the baler or bolted to the chassis, they employ a tipping table to gather bales together irrespective of forward speed. That way, big, dense swaths don’t cause issues.