Driver’s view: McHale Fusion 3+ round baler
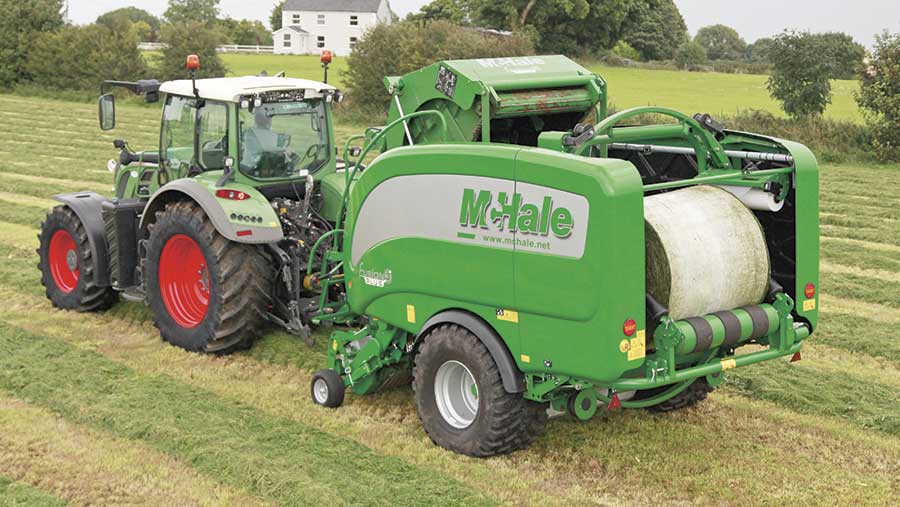
Making consistently good baled silage is always something of a challenge. Whether round or square, film-wrapped bales are prone to damage, especially on their angular edges, and getting an airtight package is achievable only with plenty of wrap – really a minimum of six layers is the only way to guarantee good quality grub come winter.
But that comes at a cost. Not only is there the expense of buying the film but there’s also the issue of getting rid of it when it’s done with. Could doing away with netwrap on round bales and replacing it with film help to solve some of these issues?
See also: Prototype self-propelled round baler raises output
Devon contractor Troy Stuart has spent decades wrestling with how best to make decent baled silage, both for his customers and for his own use on the family’s beef finishing unit.
Business facts – Stuart Partners near Exeter, Devon
Contracting Silage – grass, maize and wholecrop, all arable operations, muck and slurry, square and round baling and wrapping
Farmed area 850ha
Cropping Winter wheat 320ha, OSR 160ha, grain maize 30ha, forage maize 110ha, rye 90ha, contract combining 240ha
Livestock 2,600 beef finishers
Soils Predominantly clay loams varying through to sand
Machinery
Tractors – John Deere 8370R, 6215R, 2 x 6155Rs, Fendt 939, 936, 828, 3 x 724s, 2 x 720s
Loaders – 2 x Claas 7055s
Forager – Claas Jaguar 970 with 12 row Orbis maize header
Combine – Claas Lexion 770 TT with 10.5m header
Balers – 2 x Claas Quadrant 5300s, Krone 1290 HDP II, McHale Fusion 3+
Staff 12 full-time, plus three more at peak times
“Back in the 1980s we had a round baler but found it slow and tedious and by the ’90s had moved across to big square Claas Quadrants. But at the time the options for wrapping them were limited,” he explains.
“We bought a Rekord big bale wrapper which proved to be an excellent machine – over 24 years we had three of them. We wanted to wrap at the stack to avoid damage but I could see that by wrapping bales singly we weren’t running as efficiently as we could be, so we started to experiment with wrapping the Quadrants in pairs. It worked a treat and meant we were using significantly less film for every kilo of silage.”
Baler-wrapper combos
It was during that time that round baler-wrapper combinations started to appear, with varying degrees of success.
Wanting to ensure they could offer their customers every possible option, the Stuarts were keen to explore this new technology and had various different machines on demo, including a Welger/Goweil combination, John Deere’s own all-in-one unit and a McHale Fusion. It was this last machine that caught their eye.
Having stood back and watched how other contractors got on with the first Fusions in the area, by 2009 Mr Stuart had decided it was sensible to go down that route, as a good number of his customers still wanted round bales.
“We liked the way the McHale transferred the bale out of the chamber on to the wrapper – it was faster and much more suited to working on steep ground than any of the other combinations we’d seen working,” he says.
“So 11 years ago we ordered our first Fusion. It immediately proved to be a success, particularly on Devon’s hilly terrain. Uphill or downhill it worked well and one of the biggest pluses was that we could carry a bale on the table and only release it once it was on flatter ground.
“The other big bonus of being able to carry one on the wrapper was that bales could be dropped in lines, massively improving the efficiency of the clear-up operation.”
Following the success of that first machine, three years and 15,000 bales later, it was changed for a second-generation Fusion with an improved bale transfer system. That in turn did another three seasons before being swapped for a Fusion 3.
Film-on-film
It served the business well but was replaced earlier than expected because a new version had arrived on the scene with a clever trick up its sleeve. While the Fusion 3+ will operate much like any other baler-wrapper combo, first applying netwrap in the chamber and then film on the wrapper table, it can also substitute the net for film in the chamber – so that each bale is encased entirely in airtight plastic.
There are a number of advantages to this “film-on-film” approach, according to McHale. Plastic applied around the circumference of the bale while in the chamber can be stretched under greater pressure to expel more air than netwrap would, in theory resulting in better conditions for fermentation.
In addition, by using film around the barrel of the bale, its biggest surface is already covered before it hits the wrapper table, providing operators with the option of reducing the number of layers applied at the back-end of the machine.
The final plus point is that there is only one waste product – without netwrap in the mix there’s no longer a need to sort plastic before it goes for recycling.
“We’ve always stuck by the principle of applying six layers of film – if you go to four the silage clearly doesn’t make as well and mould gets in. It’s also more prone to damage,” Mr Stuart says.
“By using film in the chamber rather than netwrap we can reduce the number of layers applied on the table to four and we still end up with seven around the outside of the bale. The only weakness is that critical 3-5cm around the shoulder, where the chamber film doesn’t quite make it all the way to the edge.”
User experience
Stuart Partners’ contracting foreman Ed Eavis has plenty of experience operating the Fusion, but it’s not a one-man machine.
“The baler itself is very easy to operate and the new control box is a big improvement, providing a camera view of the netwrap/film rollers and knife and allowing drivers to tweak settings,” he explains.
“That’s critical because when you’re using film the process is nowhere near as smooth as with netwrap. You need an operator who’s really switched on as settings need to be constantly altered as the crop varies hour-on-hour.
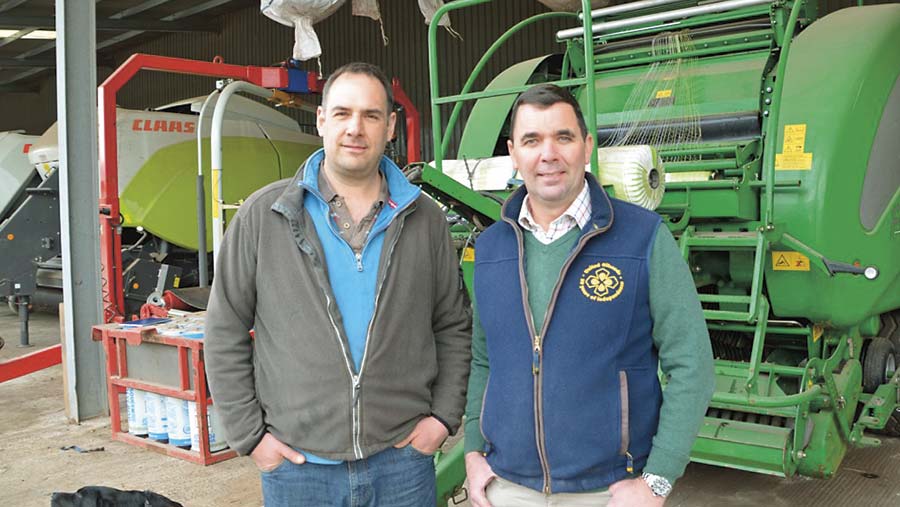
Ed Eavis and Troy Stuart © Nick Fone
“Temperature and changes in the type of grass mean the film can wrap around the rollers or even the rotor. But there’s never any real rhyme or reason, which is frustrating. The key thing is to stop going forwards the second the box bleeps and also to adjust the delay between the bale being formed and the film being applied.”
He admits: “In truth all our guys would choose to use netwrap because you’re not on and off the tractor all the time and you can just keep going.”
Output
Average rates when using net wrap and then applying six layers of film on the table stand at about 30 bales an hour, including time for moving fields and changing rolls of wrap and film (spot rates might climb to 45 bales an hour). However, McHale reckons the machine is capable of pushing out up to 60 bales an hour in perfect conditions.
Using the film-on-film approach, those rates drop back to an average of 25 bales an hour, simply because of stoppages. This clearly has an implication for the cost-effectiveness of the operation.
“By using film around the bale and four layers on the wrapper rather than netwrap in the chamber and six on the table, the plastic cost is 10-15p a bale less,” Mr Stuart says.
“But because our output is so reduced, the actual job is costing more. The two factors pretty much balance each other out and we end up charging the same rate for applying netwrap or film.
“Kilo-for-kilo, when you take haulage and handling costs into account, big square bales are still the cheapest option but it’s not always possible on smaller farms.”
Square bales
As for the square bale silage job, three years ago the aging Rekord wrapper was changed for a Goweil machine. A self-contained static unit, it has its own three-cylinder Kubota diesel engine and remote controls, enabling it to be towed to site by the same telehandler that is used to load it through the day.
Hydraulic axles mean it is lowered on to the deck for work, and once loaded it does everything else automatically including tipping the wrapped packages onto a rubber mat so that the table is clear for the next bale. Employing a rubber-belt bed rather than rollers, it is capable of handling pretty much any size bale from single 120x70cm to 120x90cm, round bales or even pairs of 120x70cm.
“At home we end up using a mix of round and square bales depending on the size of the fields we’re cutting,” Mr Stuart says.
“We definitely see a better quality of silage and less mould in the round bales where only film is used. Next step is to get a bale slice for the loader that will hold back the plastic and possibly even string to make the feed-out process a whole lot quicker and cleaner.”
Four decades of Stuart Partners’ baled silage
1980s Welger round baler and bagged bales
1990s Claas 1200 Quadrants (120x70cm in pairs) and Rekord wrapper
2000s McHale Fusion baler-wrappers alongside Quadrant/Rekord combination
2015 Claas 5300 Quadrants (120x90cm singly) and Goweil wrapper
2015 McHale Fusion 3+ using film-on-film instead of net wrap