Claas Rollant 630 RC Uniwrap offers faster bale transfer
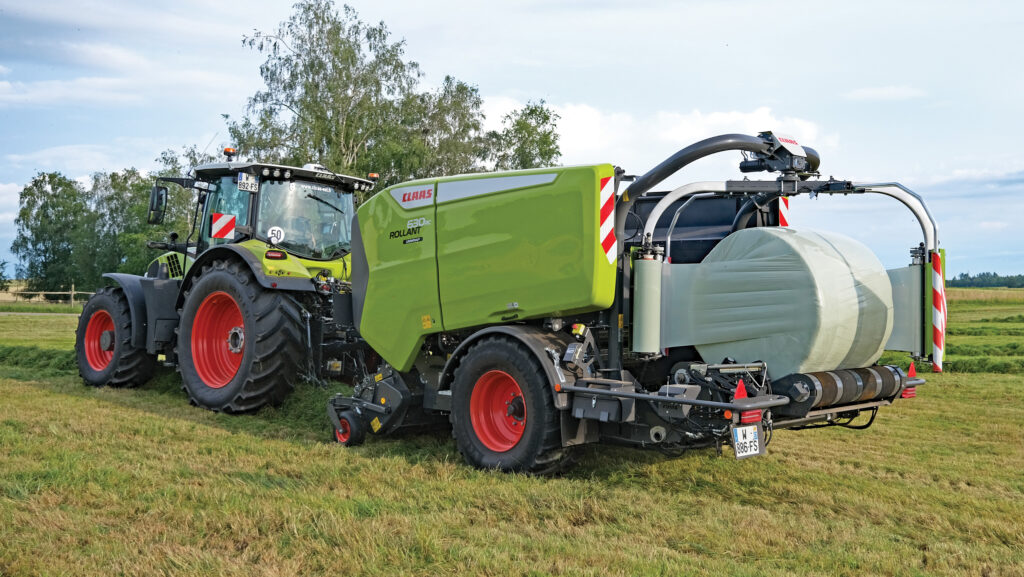
Claas has unveiled its third-generation round baler wrapper, which has received a smattering of updates to increase output, improve durability and make it easier to work on.
Unlike the two-model 400-series that went before, just one machine is in the offing – the Rollant 630 RC Uniwrap.
However, with the option to specify this with or without the manufacturer’s bale core density-hiking MPS Plus system, buyers still have the same amount of choice.
See also:Â Ultimate guide to buying a round baler 2024
Revamped pick-up
Most obvious of the 630’s updates is the move to plastic rather than steel bands on the 2.1m pick-up.
One benefit, says Claas, is that these return to position if nudged, unlike steel which can bend and cause tines to rub. But they’re also far quicker to remove if a tine needs to be replaced.
Some buyers might be dubious about the choice of plastic in this high-stress area, but the company assures us that it’s more than tough enough for the job.
Pick-ups are now offered with five tine bars as standard – there were four on the old model – and there’s the option of a single or double crop roller that folds down to give easier access.
The cam track has also been redesigned with a smoother profile that reduces power requirement by some 20%.
Several steps have been taken to lengthen the lifespan of moving parts, including dropping the number of drive chains from four to three far chunkier versions, and upgrading the oiling system with a larger tank and adjustable flows to each chain.
Choice beefing-up of certain driveshafts, steel profiles and tailgate mountings also puts it on a stronger footing for withstanding heavy use in tough conditions.
Faster bale transfer
As for output, engineers have been beavering away to shave precious seconds off the time it takes to transfer the bale from chamber to wrapper.
By altering the back door of the baler, they’ve been able to streamline the path of the transfer arm, cutting the duration of the bale’s journey from about 8sec to nearer 6sec.
Operators have got an easier time of it too, with an auto-locking system that speeds up wrap loading and a small external controller that allows the chamber to be opened and the wrapper to be spun without having to hot-foot it back to the cab.
Extension of the auto-greasing system also means the wrapper is included in the network of pipes – this had to be manually lubricated on old models.
The wrapping process is slicker, with six layers of film at a 52% overlap applied in 23sec, and a new hydraulic film brake offers a greater degree of pre-stretch, which can be adjusted from 67% to 82%.
Features carried over from the old model include the double-tined cutting rotor, which pushes the crop through 25 knives.
These can be put in and out of work from the cab and there’s the ability to run a half set.
The optional MPS Plus density system also works as it did before, with a bank of three pivoting rollers that tip into the bale chamber.
These reduce the size of the chamber as the crop starts to roll, helping to create a denser bale.
Bale diameters can be adjusted from 1.25m to 1.35m, and there’s the option of both net or film binding.