Automated square bale handling systems can cut time and costs
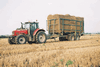
Cereal growers don’t generally like to see bales on their fields, since cultivations can’t start until they are hauled off.
It’s at this point many farmers vow never to sell any straw ever again and start making threatening phone calls to the contractor or straw merchant who, only a couple of months before, had promised to have fields cleared within a matter of hours.
But there are now a number of automated big square bale handling systems available that collect and stack straw bales with a minimum of time and fuss. Apart from being able to work quickly, they also cause less ground compaction than a traditional loader and trailer collection system.
One of the more innovative machines on the market is the Walton Eclipse which first made an appearance way back in 1981. Since then, its designer John Walton reports he has sold about 60 machines – 40 of them in the UK.
The Walton Eclipse, which is now built under licence by CHK in Merseyside, differs from other bale collectors in being able to create a secure stack with crisscrossing layers of bales.
The importance of this is that stacks can be placed without first having to provide a series of supports – whether it’s a pyramid of bales or a fixed structure such as a wall.
“This means stacks can be deposited safely on the field edges for later collection without having to waste time transporting each stack back to the farm buildings,” explains Mr Walton.
The Eclipse has also been designed to handle all sizes of big square bales – from 700 x 1200 x 2400 Claas Quadrants through to 1200 x 1300 x 2400 Hesstons. The important dimension is bale length, which needs to be within +/-15cm of 2400mm.
In operation, the stacker picks up bales on the move and follows the line of the baler with the bales first met by an extending bar that absorbs the initial impact and starts to push the bale along the ground.
A grab unit then descends on to the bale to spike and hoist it on board and deposit it on a turntable. After a second bale has arrived, the turntable rotates to orientate the bales so that they are either across or inline with the machine.
The turntable then raises the bales through 90° to place them in the stacking area. Successive pairs of bales are stacked in horizontal and vertical positions to provide the overlap and the stack is formed by pushing already-loaded bales to the rear of the machine.
The size of bale dictates how many can be stacked – 10 Hesston bales, 16 Quadrant bales, 21 Krone or Deere, and so on. All functions are automatically sequenced but can be manually controlled if required.
Unloading is a matter of tipping the stack vertically and then driving forwards – an operation which takes only a couple of minutes at the most, says Mr Walton.
Case Study: Brian Peacock, Thirsk, Yorkshire
Farmer and contractor, Brian Peacock, based at Leake Hall, Knayton, Thirsk, has owned and operated a Walton stacker for the past four seasons.
“An important part of my business is straw,” he says. “I buy it in the swath for baling and, using my own transport, sell it on during the winter to livestock farmers.”
Mr Peackock runs three square balers – a Mini-Hesston (900 x 800), an MF187 (1100 x 900) and a Hesston (1300 x 1200) – and uses the Walton to handle the bales produced by all three which annually total more than 10,000 bales.
“The machine needs a good operator who knows what he’s doing. There can be an awful lot going on when a bale comes on board and you need to be able to monitor it to makes sure all is well.
“Output varies depending on bale size and carting distance but we can keep up with the output from two balers and clear 50 or more bales an hour,” he says.
To speed operations, bales are usually stacked on the field headlands or nearby and then, using the same stacker, reloaded and carted to a more permanent site when time allows. This is where the overlapping stacking system helps to ensure stacks remain upright when unloaded.
“Once the last pair of bales are on board it is a matter of driving away and unloading,” he says. “Shod on tandem axle flotation tyres – 560.60 22.5 – ground compaction is minimal which is another good point to mention when negotiating a deal with a farmer to buy his straw.
“At about ÂŁ40,000 the Walton stacker not a cheap machine,” points out Mr Peacock. “But when speed of bale clearance is so important it’s difficult to imagine doing the job with a loader and trailer.”
* Click here to see a video of the Walton stacker working.