Give your Pottinger forage harvester some TLC
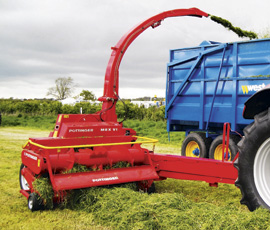
The basic design of trailed forage harvesters has remained virtually unchanged for a decade or more, says Clive Richards. The crop enters the machine via a pick-up and a set of feed rollers and then a multi-bladed flywheel chopper unit blows it into a trailer.
“The flywheel system has remained much the same and is a well-proven and reliable way to chop grass and blow it into a trailer,” he says. “There have, however, been improvements in the type of material used and, with higher horsepower tractors, components have been strengthened accordingly to provide greater outputs.”
One detail has remained the same though, and that is the need to correctly maintain the machine.
So, with help of Mr Richards let’s discover what needs to be done.
1: Starting from the front, the pto drive shaft should be checked for any twists or bends that will restrict its ability to slide freely. If it doesn’t, the shaft bearing will be at risk. Any bends will also cause the shaft to vibrate. Grease the universal joints and check the pto guard for damage.
2: This belt and pulley system takes the drive from the pto shaft to the flywheel. A choice of pulley sizes allows different speeds to be selected in respect of the available horsepower. Check the condition of the belt and replace if necessary.
3: The belt tensioning pulley needs to be greased, but not over greased – spillage on to the belt is not good news.
4: The oil reservoir for the automatic chain lubrication system needs to be topped up with chain-saw oil – it has the ability to cling to chains and is usually bio-friendly. A shot of oil is delivered every time the pick-up is raised.
5: Check all oiler pipes are connected to their brushes and the brushes themselves are making contact with the chains.
6: Grease blocks are convenient, but only if the grease arrives at the bearings – it’s worth a look to make sure it does.
7: The flywheel is fitted with 10 blades each edged with tungsten carbide. This blade is just about at the end of its working life and will need replacing – they each cost about £80.
8: The flywheel also has five paddles to blow the cut grass up the chute. Wear reduces output. They can be repaired by running a weld across the edge and then using a grinder to shape to a square finish.
9: Drive for the feed rollers and pick-up is a chain drive taken from the front of the flywheel. In normal drive position this belt drives down to the gearbox that creates the drive to the feed rollers. Should a blockage occur, the top pulley is lowered so that the belt drive is slackened and the black tyre creates a friction drive to the lower pulley to reverse the drive. Check the condition of the belt and the tyre.
10: A circular sharpening disc should be angled so that it sharpens blades evenly along their length – not just at their ends. Check the condition of the sharpening stone.
11: Feed rollers are remarkably resilient and only suffer the occasional bend. Wear and damage is more likely to occur on the second set of rollers.
12: Chute wear just happens – whole crop wheat can be particularly aggressive. Check for wear and replace before the surface becomes uneven and the flow of grass is impeded.
13: On machines with metal detectors, this is the system that brings everything to a sudden halt. The black canister is a solenoid which, when commanded by the sensor, trips the pawl and ratchet. It is a fail-safe system in that the solenoid needs to be powered for the feed rollers to turn – no power, no drive. A thorough inspection of this system should be made – one of the problems can be water getting into the solenoid.
14: With the pto drive disconnected, check the metal detector system. A spanner placed between the feed rollers should trip the solenoid. At the same time the two drive pulleys drop together to stop and reverse the drive.
15: This is the pick-up auger drive chain. Watch out for failure of the chain tensioning wheel – it tends to become wrapped in grass, which can destroy the bearing. Note the chain oiler brush.
16: Chute positioning is important. Make sure the in-cab electro-hydraulic controls allow the required movement and there are no oil leaks from ram seals, hose connections or splits in the hoses.
grasslandkit