Fleet of five diggers bulks out contractor’s winter workload
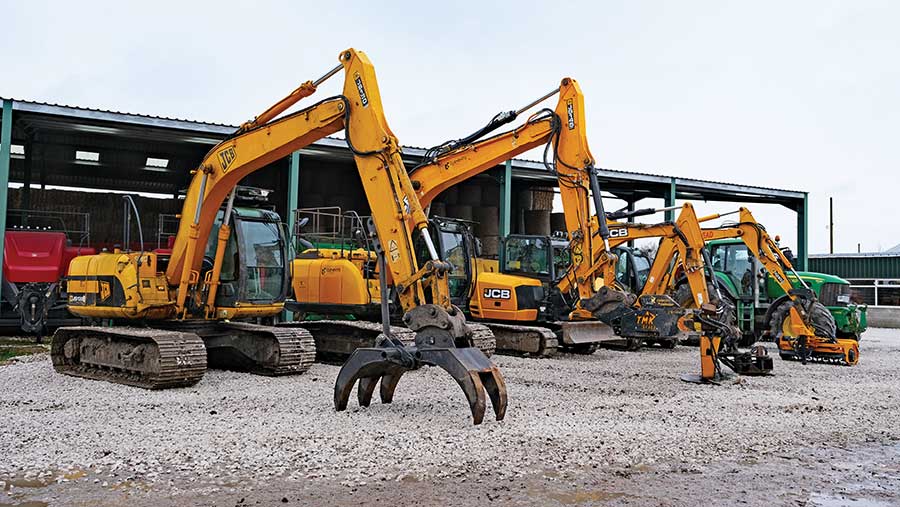
Lean winter months have been made profitable for York-based D&J Stead Contracting since investing in a fleet of tracked excavators paired with an array of timber- and hedge-taming attachments.
Tools allied to their five machines – ranging from 2.7t to 15t – include a circular saw, a couple of tree shears, a grab and a home-made 1.2m flail hedgecutter.
Together, these keep father-and-son team Duncan and Nick Stead plus full-time staff member Jordan Pooleman gainfully employed during the off-season.
See also: Farm diggers: Tips for buying a used 360 excavator
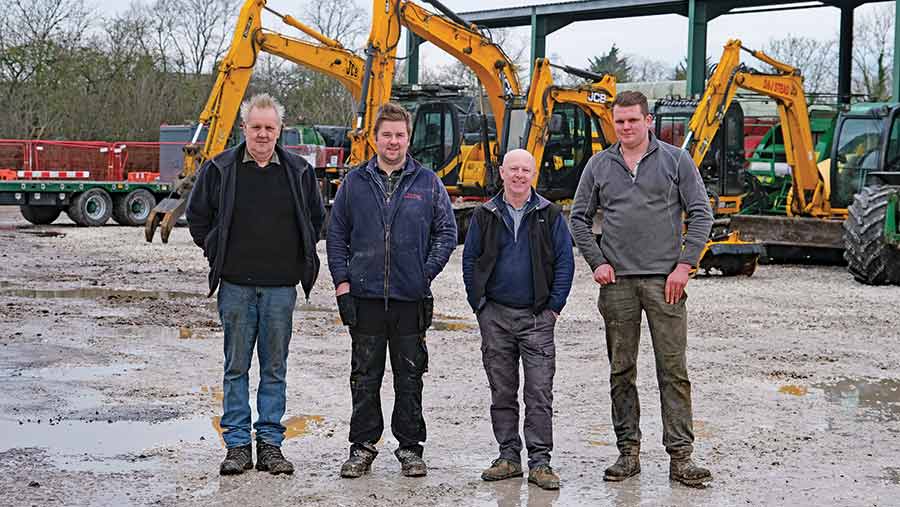
From left: Duncan Stead, Nick Stead, Ady Clark and Jordan Pooleman © James Andrews
Tasks for the tooled-up 360s include clearing windfall timber that’s deemed too dangerous to tackle with a chainsaw, dismantling trees in awkward locations and coppicing or trimming hedges.
A large chunk of the diggers’ workload is timber related, but they also carry out drainage work, build farm tracks, create bases for farm buildings and carry out general groundworks.
The Steads’ first foray into excavator timber work came after they adapted a three-blade Protech saw that was originally fitted to a Bomford 8181 hedgecutter.
“We made a bracket to put it on one of our 8t JCBs and it transformed it, giving us far more articulation for cutting branches at different angles,” says Duncan.
The only problem was that the thin blades needed professional sharpening and they tended to flex in thicker material. “We never broke one, but it always makes you wince when you see a spinning blade bending in front of your eyes.”
Single saw blade
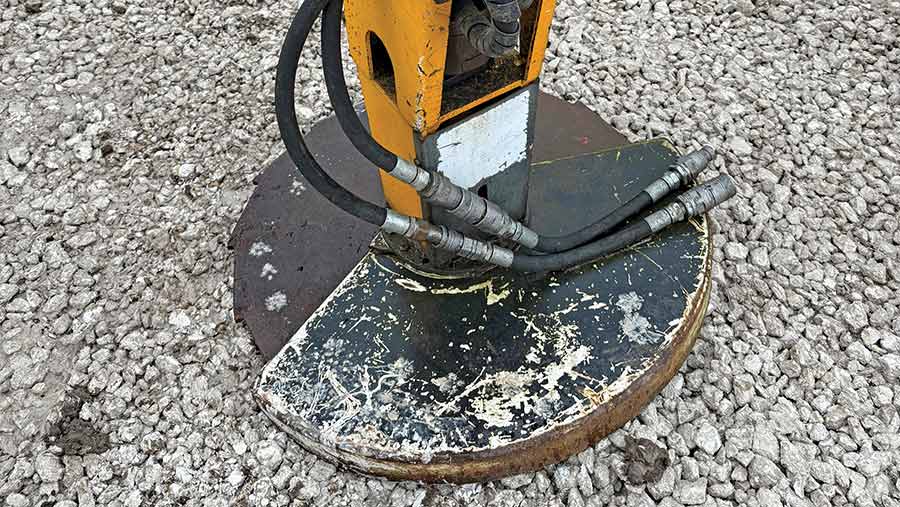
Saw blade © James Andrews
That’s when they upgraded to a heavier-duty single-blade Arbocut 2000 from Joe Turner Equipment.
Nick fabricated a bracket so that this would fit on their 8t JCB 8080 and 85Z excavators, and has since made an adapter so it will work with their heavier-duty 15t JS145 and JS130 Groundworker machines running on 65mm pins.
“It’s much tougher, so we can use it for cutting larger timber and don’t have to worry about blade flex – it can also be sharpened with an angle grinder, so maintenance is really straightforward,” says Nick.
Hedgerow coppicing is the primary role for the blade, where it makes short work of removing woody growth. On most jobs, customers will ask them to simply reduce the height of the hedge, but the best results come when they’re felled at ground level, says Duncan.
“Both options result in a decent hedge, but those where we’ve chopped back all the growth come back the thickest. Plus, it makes it easier to plant up the gaps,” he says.
The only downsides of the blade are that the lack of an integrated grab makes it awkward to clear-cut material, leaving copious amounts of debris to tidy up. They also have to make careful cuts to ensure limbs don’t fall the wrong way, hitting their machine or other obstacles.
Tree shears
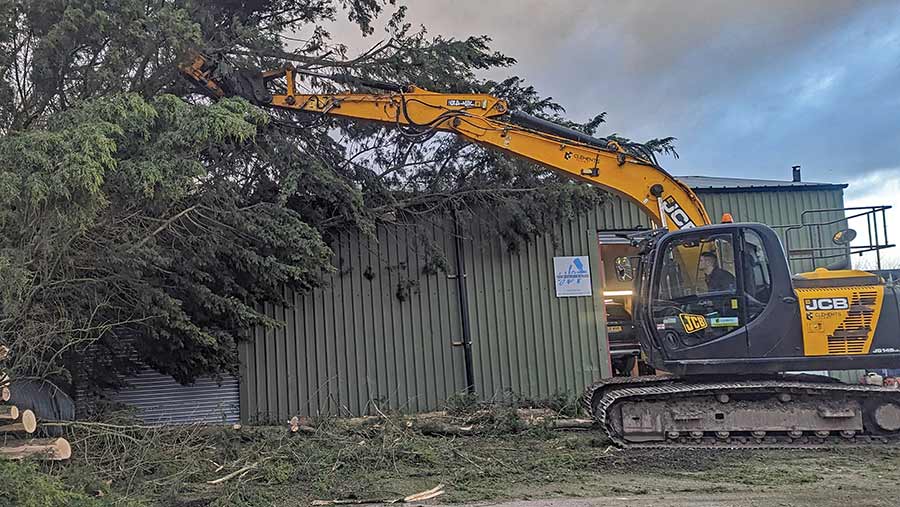
TMK 300 tree shear © James Andrews
This is where their two tree shears come in. The first of these is a Hard Life TSH model from Bucket Warehouse, which they fit to their 8t machines and use for material up to about 150mm in diameter.
This has a double-edged blade and twin grabs that make it easy to align the timber. For added versatility, the Steads have teamed this with a tilt head, which allows them to get onto angled branches without having to constantly shunt the excavator around.
“It’s not quite as handy as a rotator head, but it does the job and is far less expensive,” says Nick.
When there’s bigger material to handle, the 15t JS145 is deployed with a beefy TMK 300 shear fitted. This can cope with softwood up to 300mm in diameter and has a collector arm to increase capacity.
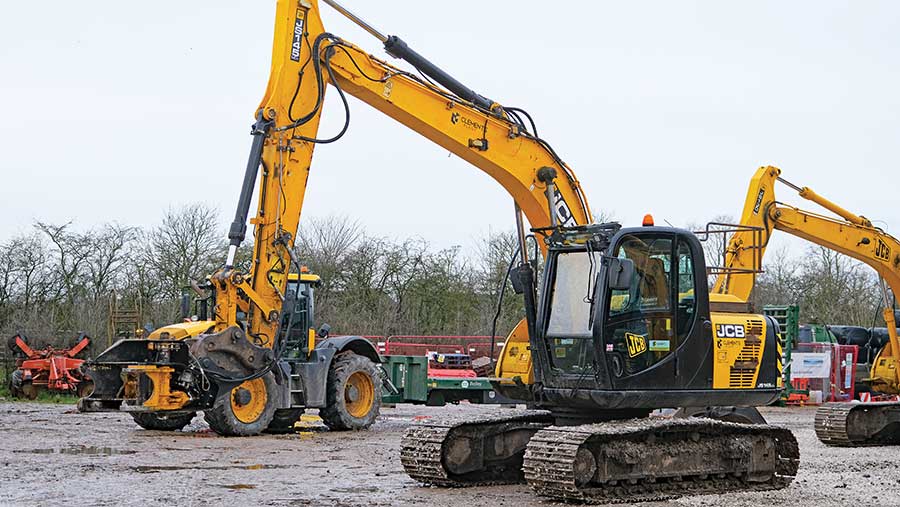
JS145 with TMK300 tree shear © James Andrews
“This is great as you can cut a piece of timber and hold it in place while you grab the next – it means we can maximise the capacity of each mouthful, rather than having to slew round to dump each branch individually,” says Duncan.
They also opted for a secondary knife fitted on the bottom of the grab, which helps cleanly cut smaller branches, preventing them wedging in the gap between the arm and main blade.
A couple of other add-ons were available, including a delimbing tool that allows it to strip off small branches when the shear is run up the trunk. They decided this wasn’t necessary, but their grab does have a top blade fitted that will allow them to add one in the future.
As the shears are so versatile, they’re gradually taking over the circular saw’s workload. “They’re safer, as you’ve got so much more control, and they’re faster as you don’t have to spend as long tidying up afterwards,” says Duncan.
Even so, for jobs where there is a particularly large quantity of debris to organise, they’ve got a grab that fits on their 15t machines. This makes short work of clearing up the site and they say it really comes into its own when the ground is too wet to access with a tractor loader or telehandler.
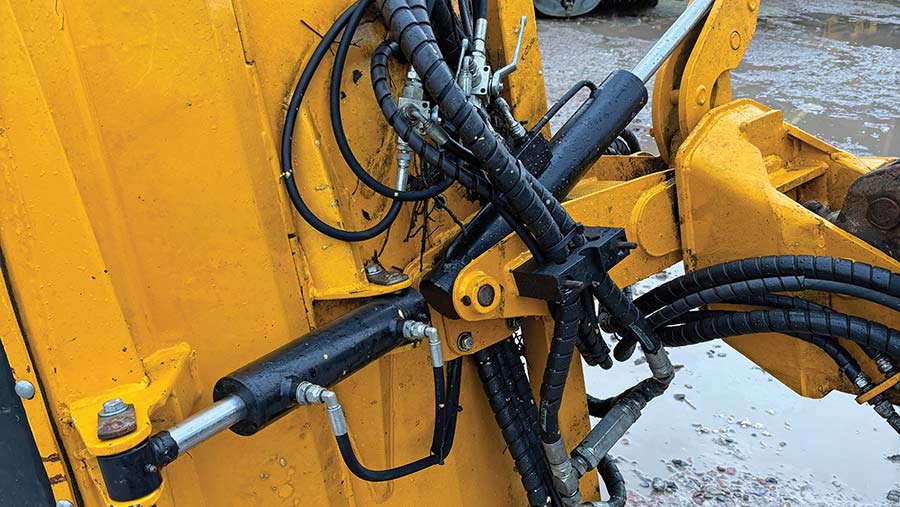
Hedgecutter head © James Andrews
Home-made hedgecutter attachment
Keen to have a hedgecutter that could work in tight spaces and make less mess on wet ground, Duncan and Nick adapted a flail head to fit on their 8t excavators.
The starting point for the build was a 1.2m flail from a scrapped Bomford 8181 trimmer, which had holes in the top of the hood and seriously worn flail lugs.
After stripping it down, they welded new metal onto the lugs and balanced it by spinning it and checking for vibration. A new hood skin was also grafted in place and they made a hydraulic front flap so that they can get more material into it.
The original head pivot point was retained so they can rotate it from side to side, and they added quick-hitch brackets above this. As the head needs three hydraulic services, the ram on the hood flap is fitted with manual diverter valves, which they’re planning to upgrade to an electric version that they can operate from the cab.
To begin with, they used the original 90hp motor, which worked well for a short time before promptly blowing up.
After doing some research, they replaced it with a larger 120hp version sourced from Joe Turner Equipment, which has a case bleed built in. This allows oil to drain back if too much pressure builds up.
In addition, they added a check valve between the pressure and return lines to protect the pump against backflow and back pressure. This did the trick, as the flail has now given years of trouble-free service.
“The flail is also handy to have with us when we’re using the tree shears and blade, as we can pop it on to tidy up any small material without needing to bring an additional tractor,” says Nick.
The final member of the timber work fleet is a JCB Fastrac 4220, which is teamed with either a 30ft Bailey or 20ft Herbst beavertail trailer for moving the kit around.
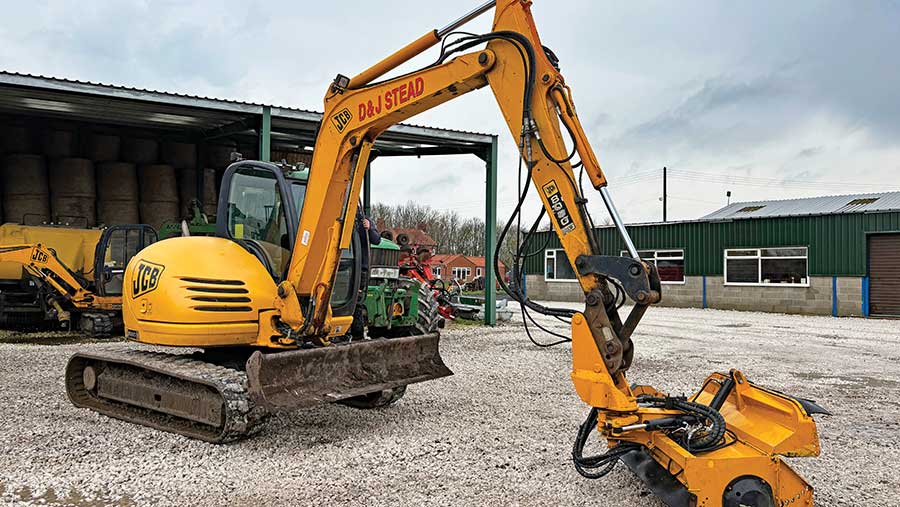
JCB 8080 with hedgecutter head © James Andrews
Additional hydraulic services
As several of the Steads’ excavator attachments require two hydraulic services, they bought their most recent machines with two lines already fitted and added additional ones to the older models.
They’ve done this by fitting electric diverter valves to the line feeding the jib swing ram, as this isn’t used very often.
All of the hydraulic work has been made easier by the fact that they recently bought a local hydraulics business, run by staff member Ady Clark, meaning they have instant access to pipes and fittings.
D&J Stead excavators and attachments
Excavators
- 2015 JCB JS145 (15t)
- 2004 JS130 Groundworker (15t)
- 2015 JCB 85Z (8t)
- 2009 JCB 8080ZTS (8t)
- 2004 JCB 8027 (2.7t)
Attachments
- Arbocut 2000 saw blade
- Bucket Warehouse Hard Life TSH tree shear
- TMK 300 tree shear with gathering arm
- Modified 1.2m Bomford flail head
- Heavy-duty grab