Workshop legends: We visit 84-year-old welding king Edgar Harding
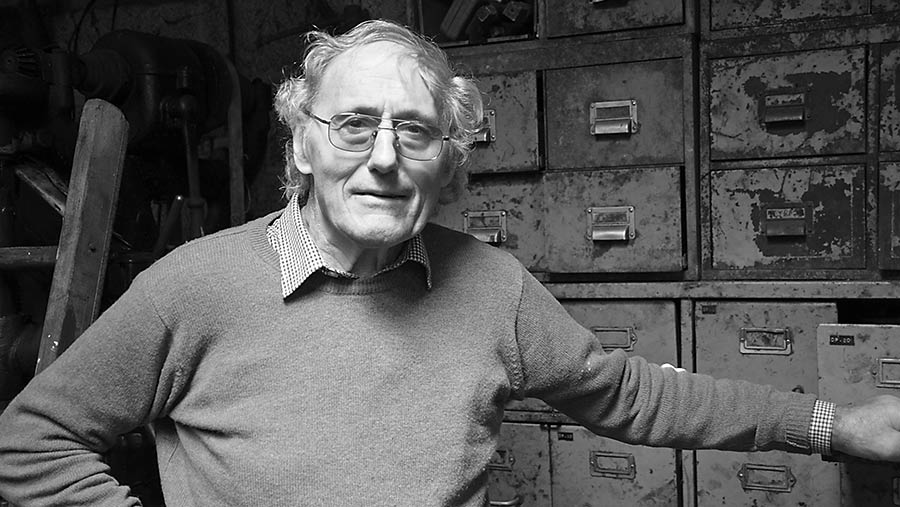
Across the country there are welders, mechanics, fitters and fabricators beavering away in sheds and vans to keep the nation’s farm machinery fleet in running order. In our series profiling these mechanical greats, we talk to Somerset superstar Edgar Harding.
Born in 1935, Edgar Harding has spent the past 70 years building and fixing all sorts of weird and wonderful machinery in his corner of south Somerset.
Although this is his home patch, his reputation for crafting the most intricate parts from scratch has drawn customers from across the south-west of England.
His deft hand with the welder and experience with the lathe has meant that customers have viewed him as the go-to man when it comes to recreating essential parts that are either no longer available or when the original isn’t cost-effective to repair.
Now well into his eighties, Mr Harding is still plying his trade, albeit at a slightly steadier pace.
See also: Workshop legends: We visit Norfolk’s master mechanic John Towell
Where did you learn your trade?
I’ve never had any real training – I’ve learnt everything from knowledgeable friends and books.
It’s my customers that have taught me really – whatever they’ve asked me to do, I’ve gone away and worked out how to do it.
On a small dairy farm you have to be pretty self-sufficient. We grew our numbers from 12 to 40 milkers to try and keep up but it was difficult, especially after my father died when I was 28.
My true interest lay with engineering. That was the route that I chose to go down and the cattle became a side-line – my hobby became my job.
How did you start out?
My father had bought a BOC oxy-acetylene welder and I messed about getting myself up to speed with that. The most repair-hungry machine on the farm was always the reciprocating finger-bar mower – I pretty quickly perfected the art of glueing it back together.
Other local farmers soon heard that I could do it and started bringing theirs to me to fix.
But I didn’t have all the tools I needed or the money to go out and buy them, so I started keeping bees and trading honey and beeswax to generate a bit of cash.
My first outright purchase was a £35 Rivett plain bed lathe, which enabled me to start turning pins and bushes – it was a big expenditure but it meant the machinery repair business could become a serious affair.
Not being a real livestock man, it gave me the opportunity to switch from dairy to beef and put more time aside for engineering work.
What were the key tools you needed?
The lathe was a big step forward, but it was arc welders that really changed the game. Initially, I had a 200amp BOC but it couldn’t run at the higher voltages required for the special rods that I use for more unusual jobs like welding cast, so I upgraded from that to a 250amp Oxford.
It’s a really good machine and enabled me to really finesse the job. It’s still going strong today.
What were your most common jobs?
One of the most frequent things I got asked to do was weld up broken plough mouldboards. They were expensive to replace so people asked me to fix them instead. That’s how I learnt about the importance of rod choice.
Going to low hydrogen rods meant that carbon didn’t mix with the steel so it didn’t go brittle at the weld. Nickel rods do a similar thing when welding cast.
Got any good welding tips?
With MIG it’s all about having a clean start – the grinder is your friend. I was one of the first in our area to get a MIG and it was the only way to weld up thin panels on mowers and other machines. But they don’t last as long as an arc welder.
Although simple beasts, arc welders require a bit of love and attention. I’ve still got the Oxford welder I bought in 1964 but it’s lasted because from time to time I’ve opened it up and drained the water out that naturally collects as a result of condensation.
I’ve had to rebuild a countless number of customers’ transformers over the years that have suffered water damage.
When it comes to rod choice, it’s always low hydrogen rather than ordinary mild steel because the welds are stronger. However, it can be harder to strike an arc with them.
If you’re working with high-tensile steel, use chromium rods and heat up the job to a good temperature beforehand. It needs to be beaten when still hot to temper it. Only ever use soft nickel rods for cast.
What did you find most interesting?
I liked the fact that I wasn’t pigeon-holed into sticking with one line of work – every day was different. One day I’d be making a milking machine line-cleaner and the next I’d be building bale sledges.
In fact, it was these that I quickly made a name with. One customer asked me to put together a bundler-collector so I scratched my head a bit and came up with a plan.
The hardest bit was getting the back door to reliably slam shut after the bales had been released. I gave it a bit of thought and came up with a cantilever arrangement for the tailgate.
A neighbour of that first customer saw the sledge and asked me to build him one – word soon spread and I ended up making more than 30.
What were the more unusual things you got involved with?
Strangely enough, I accidentally got a bit of a name for myself making church keys. I was asked initially to fabricate a replacement for a local church safe so I pulled apart the old medieval-style lock and worked out how it operated.
I then made up keys to fit – it took a few goes but after a while I’d got the hang of it and the process quickly become a speedier affair.
I didn’t think of it as being particularly special at the time, but I once built a quick-hitch link-box for a customer that won awards and got featured in the NFU journal.
What was your bread and butter?
As time moved on, finger-bar mowers were replaced with drum models and the Fahr KM22 was all the rage. Gears often got damaged and needed replacing, but off-the-shelf they were pretty pricey. Most of the time it was just a couple of teeth that needed building back up.
I then started buying old mowers that had been consigned to the scrap heap, pulling them apart, fixing them up and selling them on.
By specialising in the KM22 and keeping heaps of spares on the shelf I accidentally became the place where farmers would come if they needed anything for a Fahr mower.
People I’d never heard of would turn up in the yard having come from as far afield as Cornwall or the New Forest.
Alongside this I got a name for myself with Lucas bits, fixing up starter motors, dynamos and alternators.
Drum mowers then fell out of fashion and the business moved towards spare parts, particularly bearings and pto bits – things that were universal to all farm machines. And that’s how it stands now really, although I’ve slowed down a bit.
I still enjoy the challenge of being given a broken part that a replacement can’t be found for and repairing it or making one from scratch. I like saving the customer money and the hassle of finding a new part.
What was your biggest achievement?
As a completely untrained 20-year old with no proper knowledge of how things worked, I pulled apart the gearbox on our Fordson E27N and managed to shoe-horn in an extra gear so that it would run slow enough for harrowing but fast enough for roadwork and mowing.
To do it, I cut out the handbrake to make room for the extra gear and then had to add a brake lever to operate the disc brakes – this acted as a new handbrake.
I surprised myself that it worked but it gave me a belief that I was capable of doing these jobs if I sat down and put enough thought into them. Every time I’m confronted by a difficult challenge I think back to the lessons I learned from that project.
How do you deal with issues that seem impossible?
I’m rarely beaten by a job but there’s a commercial reality to everything – you have to earn a living so you can’t keep banging your head against a wall. I’ve stuck to the rule that you must have at least four attempts at anything before admitting defeat. You can’t expect things to always work first time round.
What’s your favourite tool?
The lathe. It’s always been central to my work. Most people can make a job of welding but there aren’t many who are prepared to make stuff from scratch. The lathe started my career really.
You have to really think through how to approach things and get them perfect but the end results are satisfying.
I was once told by a local machinery dealer that I was spoiling things by doing all my repairs. If I stopped fixing things then they’d be able to sell a whole heap more new machines – I took that as a massive compliment and carried on with extra enthusiasm.
What other sidelines did you have?
Our cows had always grazed among apple trees and my father had been making cider since 1940. Naturally I took this on and learnt the dark art.
Having been doing it for decades, I didn’t put a lot of thought into it but built a name for producing a particularly dry cider.
To my surprise, one day I received a phone call saying I’d won an award from Camra for my cider, having been nominated by an anonymous individual.
Word got out and a number of other awards followed, but I’d never done a thing to promote it. People clearly liked it but I never drank too much of it – I didn’t want to let it cloud my judgement…
What are the biggest changes you’ve seen?
Here in our corner of Somerset the biggest change has been a shift from small 10- or 12-cow dairies scattered throughout the parishes to huge units with up to 1,000 cows. But the basic core principles remain the same – in this region we’re all about growing good-quality grass for milk.
When you think something like a 46hp Ford 3000 was the main tractor for most farms 50 years ago and now we’re talking about machines well over 200hp, it makes the mind boggle.
What would you say has been the biggest machinery development in that time?
That’s a tricky one but for me it was probably the reversible plough. It massively improved the efficiency of the job and meant you didn’t end up with troughs all the way across the fields – everything matched up.
More recently it has to be things like GPS-controlled fertiliser spreaders with forward-speed related rate control.
What vehicles have you had over that time?
I started out with an Austin A40 pick-up, in fact I had two. I kitted them out with brackets to carry my bale sledges and used them to deliver them out all over the place.
They were then followed by two Austin Maxis, which had drawbars for a trailer. I was a fastidious reader of Exchange and Mart and always after a bargain.
I found my big lathe in the paper and had to go and fetch it from north of London with a Maxi and trailer. I would regularly travel the country on the trail for good deals, especially when I realised there was a business to be had out of buying broken-down machinery.
A Volvo 360 followed the Maxis. It was a different class and didn’t break down once in the 10 years I had it. It was the best vehicle I’ve ever owned, far better than the Land Rover Discovery that followed it – it was terribly unreliable.
What advice would you give to someone starting out in agricultural engineering?
Be prepared to do any work that’s thrown at you and worry about figuring out how to do it afterwards.
Sometimes you have to be prepared that certain jobs won’t pay but you have to do some things to gain respect and build yourself a reputation.
Also, don’t make things more complicated than they need to be. When you set out on a job, always focus on keeping things simple.
Get in touch
Our Workshop Legends series relies on readers getting in touch with nominations. So if you know a mechanical genius, welding master, or a brilliant farm handyman then send an email to oliver.mark@proagrica.com