Workshop Legend: We visit master tractor fixer Martin Percy
Based on a farm close to Blandford Forum, Dorset Tractors’ Martin Percy has built a reputation for repairing and restoring machinery of all shapes, sizes and shades for customers across the South West.
Set up with son Sam in 2021, the firm’s title is a nod to the long defunct Ford, New Holland and Claas dealership of the same name that served the region’s farmers throughout the 1970s and early 1980s.
Dorset Tractors has since grown off the back of Martin’s vast experience, gained looking after a wide variety of manufacturers’ products over the last 45 years.
See also:Â On test: We rate the latest battery-powered grease guns
Where did you learn your trade?
I grew up on the farm where my dad was a tractor driver, and I always had an interest in the mechanical side of things.
When I was 14, I got a job with our local International dealer, helping out in the stores, but jumped the fence when I was offered an apprenticeship with Dorset Tractors working on Fords.
It was quite an opportunity, as there were 25 of us working out of one workshop, mainly looking after Ford 5600s, 6600s and 7600s as well as County 4wds. I really learned a lot from the older fitters.
It was the heyday of farm machinery sales – the amount of kit moving was quite phenomenal. At any one time we would have at least 20 tractors in the yard waiting to be PDI’d.
Rather unusually, the business also sold and serviced both Sperry New Holland and Claas combines, so I got experience of two of the leading brands.
I fell into specialising in combines – both yellow and green – as a lot of the other fitters seemed to get itchy and sneezy at the prospect of working around harvesters, balers and hay equipment.
At the time, we were selling more Claas combines as the Dominators had established a name for themselves, despite the fact that New Holland’s 8080s were actually more reliable.
What were your most common jobs?
The 1980s were of course the era of the notorious porous blocks of the Ford 1000 and 10-series. With so many short motors to change, it got a bit competitive between the fitters to see how quickly you could get the job done.
Clutches were also a regular task, and many of today’s guys wouldn’t believe it but we actually split tractors out on-farm rather than dragging them back to the workshop.
How much did you earn?
My basic pay worked out to about £19 a week, but because Dorset Tractors was selling so much new gear we also got bonuses for getting stuff PDI’d out of hours.
At ÂŁ7 a baler and ÂŁ30 a combine it was money worth having and it meant we got them out to customers as quickly as possible to make room in the yard for the next batch.
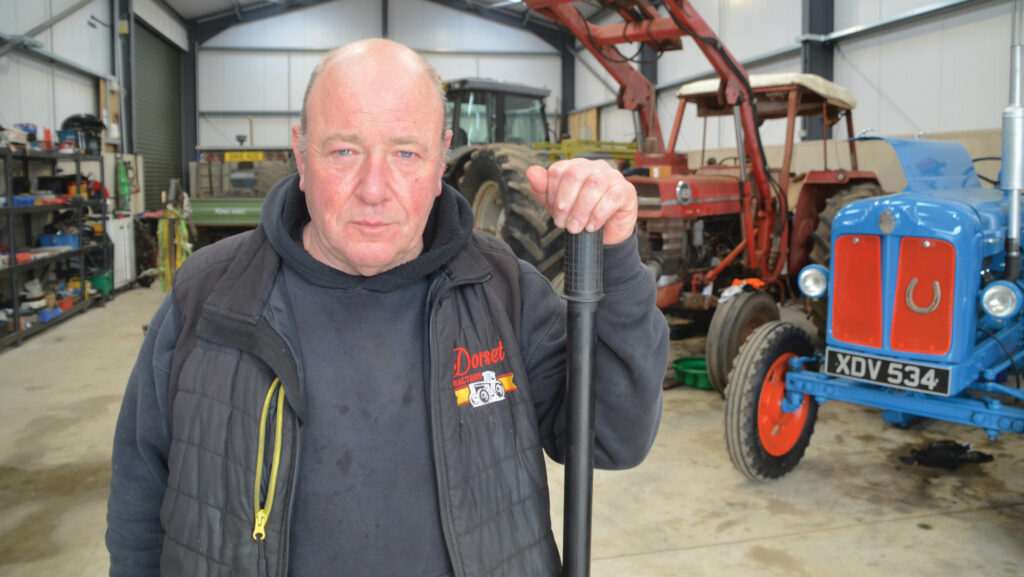
Martin Percy © Nick Fone
How did you get experience of other brands?
When Dorset Tractors went bust in 1982, Claas shifted to Bredy Agricentre at Dorchester and I followed. They had the franchises for Deutz, Marshall, Leyland, International – and, later, Case – as well as JCB.
I got the opportunity to work on some of the first Loadalls and was sent away on training courses for the latest Case products – 885s and 856s. They were totally different to the Fords I’d been used to.
The hydraulics were so much more complex but once you got to grips with how they worked, they were actually OK.
The infamous Hydrashift gearbox fitted to Case’s 94-series tractors in the mid-80s got a bad name for itself, but we quickly learned that all it really needed was regular oil and filter changes.
How have you seen farm machinery change over the past four decades?
Obviously things have moved on a long way from those early Ford 1000-series tractors, with more power, more complex gearboxes and overly complicated electronics.
But it was when I went to work for Deutz and Zetor dealer MJ Fry in 2008 that I really saw the difference in how things were developing.
Mike Fry sold huge numbers of those Czech-built Forterras and Proximas. They were generally reliable and easy to fix, unlike the Same Deutz-Fahr equivalents.
They had the build quality and driver comfort but were too complex.
With canbus electronics you needed a totally different way of thinking and a totally different toolbox. It was no longer just a roll of spanners – you had to have a multimeter, oscilloscope and a diagnostics computer.
Which were the most unreliable machines?
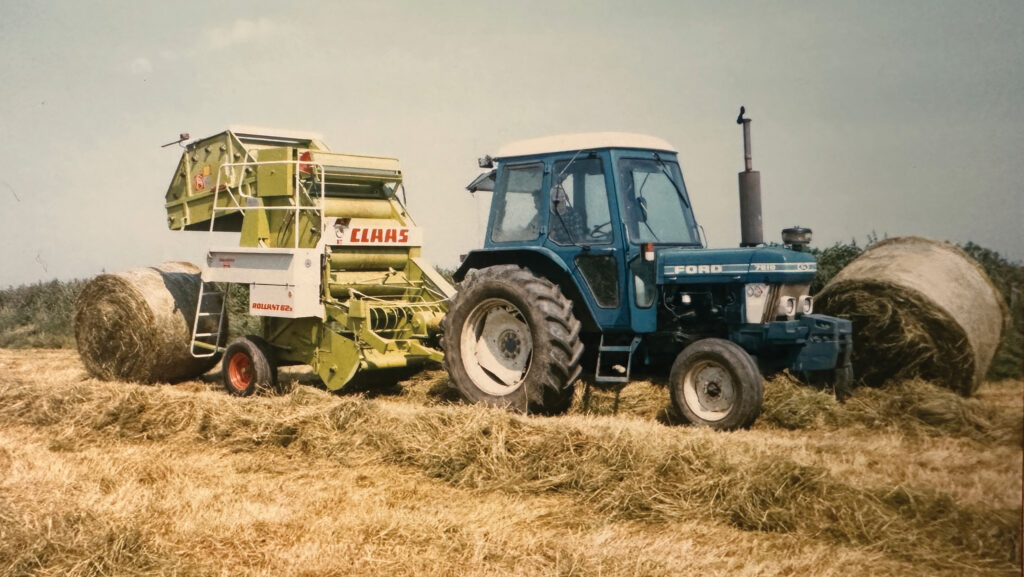
© Martin Percy
In the mid 1980s we took delivery of the first Claas round baler with the Rollatex auto-netting system at Bredy. It was the most frustrating machine I have ever worked on.
The control box was really primitive and just when you thought you had it set up right it would throw a hissy fit. It was truly terrible.
I also drove a New Holland FX375 forager for a season. When it was going it was a beast but keeping it going was hard work.
Eventually the best thing happened to it – it blew itself to bits, literally.
I thought the world was coming to an end – the machine was leaping up and down and there was metal flying everywhere. It wasn’t a sad goodbye.
When it came to handlers, JCB’s early 525-58s had some major wiring loom issues, leaky rams and booms that would crack.
Along with the smoky Perkins motors they kept us pretty busy but, despite all that, farmers loved them.
And having said that Zetors were pretty bombproof, there was one exception – the Proxima Power.
With its power shuttle the wet clutch packs simply weren’t big enough.
After a few hundred hours work they’d get jerky, wouldn’t calibrate and would eventually throw you out of the cab before burning the friction discs out.
And which were the best you dealt with?
In the mid 1990s I joined Hawood Agriculture that was selling Same Deutz-Fahr and Renault tractors alongside Caterpillar tracklayers and handlers.
With the John Deere engine and Gima backend shared with Masseys, those Renaults were the most undervalued tractors of the time.
We struggled to sell them so ended up running a small hire fleet – they were reliable and easy to work on.
It was a similar story with Caterpillar handlers.
They were bombproof machines but didn’t have a following at the time, partly because Cat’s parts prices were so ridiculous.
It got to the point where it was cheaper to strip a new machine of all its bits rather than buy individual components.
What was the most interesting project you worked on?
At MJ Fry we looked after a very elderly Deutz Intrac 150 systems tractor with a forward-mounted cab and rear load deck.
We were supposed to mount a trial plot forage harvester on it for a seed company but, before we even got to that, the gearbox fell to bits.
It was littered with solenoids and early electronics, and it was a bit of a learning curve trying to figure out how to get it back working.
Why set up on your own?
I was getting to an age where I was starting to struggle heaving big lumps of iron about and my son Sam had come out of the Royal Electrical and Mechanical Engineers in the army, so we thought it was a good opportunity to work together.
We both like fixing simpler machines and take satisfaction in keeping older kit going as well as doing full restorations, and we’ve developed something of a niche preserving classic and vintage tractors.
With the rebirth of the Dorset Tractors name I’ve been amazed how quickly we’ve gained a following. Sam tells me it’s all down to the power of social media…
What’s the key to success?
We like to do everything properly – no half-job bodges. I’ve always believed the key thing is to be open, up-front and honest but also business-like at the same time. After all, we can’t afford to be Charity Tractors.
One thing we do that is slightly unusual is offer a pay-as-you-go service.
We’ll start by doing a preliminary check over and sort any basic issues. Once we’ve got an idea of how much work is involved, we’ll then price the other tasks individually.
The only problem with that is that we do get projects stacking up in the workshop – but at least we don’t have money outstanding.
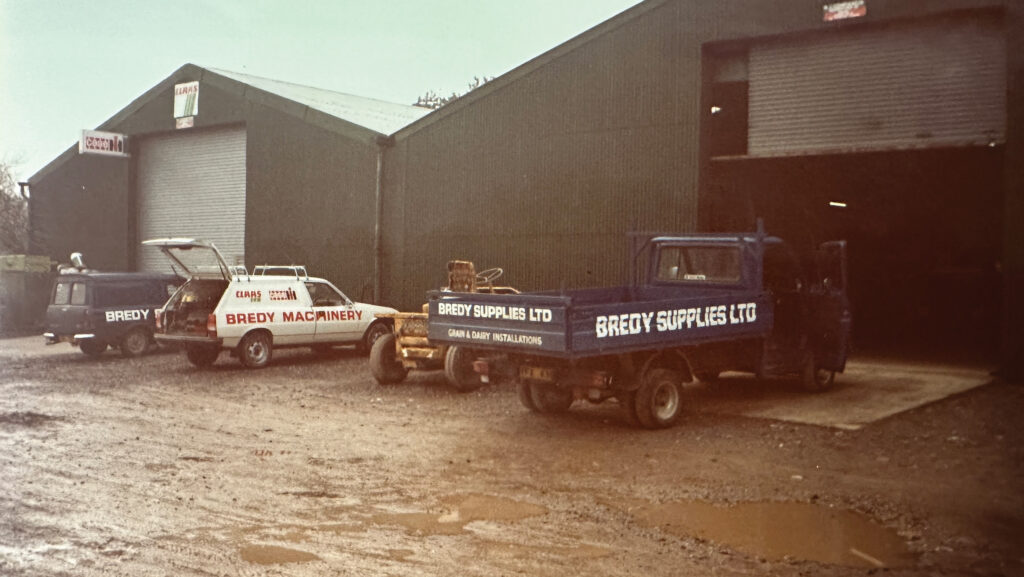
© Martin Percy
What have been your best and worst work vehicles?
Without question, the Mercedes Sprinters we’ve got now are the best vehicles I’ve run.
We’ve got three – a 14-plate, 15-plate and 16-plate – that have each done between 80,000-160,000 miles and have proved to be really good.
They’re nice to sit in and have proved far more reliable than the VW Crafters and Ford Transits I’ve had previously.
I once had an LDV 400 Convoy which nearly broke me. Just about everything imaginable went wrong with it, particularly the running gear.
It was the 400 with twin wheels on the back – the brakes were useless and the rear axle half-shaft seals just constantly dropped oil.
It was endless – tyres would scrub out, springs would snap and it was forever wanting suspension bushes.
I thought I was being clever by having a big van you could get an engine in the back of, but it was a massive mistake.
It was basically a Morris Marina with a shed on top. If the wind was blowing it would just rock about – you had to hang onto the steering wheel for dear life.Â
I had it three years and that was three years too many. I spent more time fixing it than I did fixing other people’s gear. It was truly awful.
Biggest achievement?
Starting our own business with all its challenges.
Laying a foundation for my son so he can carry on supporting the agricultural industry with integrity and honesty, which will hopefully gain loyalty and trust from our customers.
What’s been your worst mistake/mishap?
Too many to mention – probably using my hand as a hammer.
Favourite tools?
Up until recently I had a set of Britool spanners and sockets that I bought when I was 16.
They’re still going strong, but somehow they seem to have made their way into Sam’s van now.
I’ve also got a random black Kamasa 15/16in spanner that is totally indestructible.
What advice would you give to anyone wanting to start out in ag engineering?
Find a good college that teaches proper engineering like Reaseheath.
Go to as many rallies and shows as you can – there’s a lot of knowledge out there and you just need to talk to people. Finally, find a decent employer, which isn’t always as easy.
Have you got any good workshop tips?
Buy the best tools you can afford.
Having a clean, tidy workshop with a place for everything makes you more efficient.
Safety is a big factor – never block the doorways and always having an escape route in case anything goes wrong.