Lincs grower’s bespoke harvester lifts 70k pumpkins a day
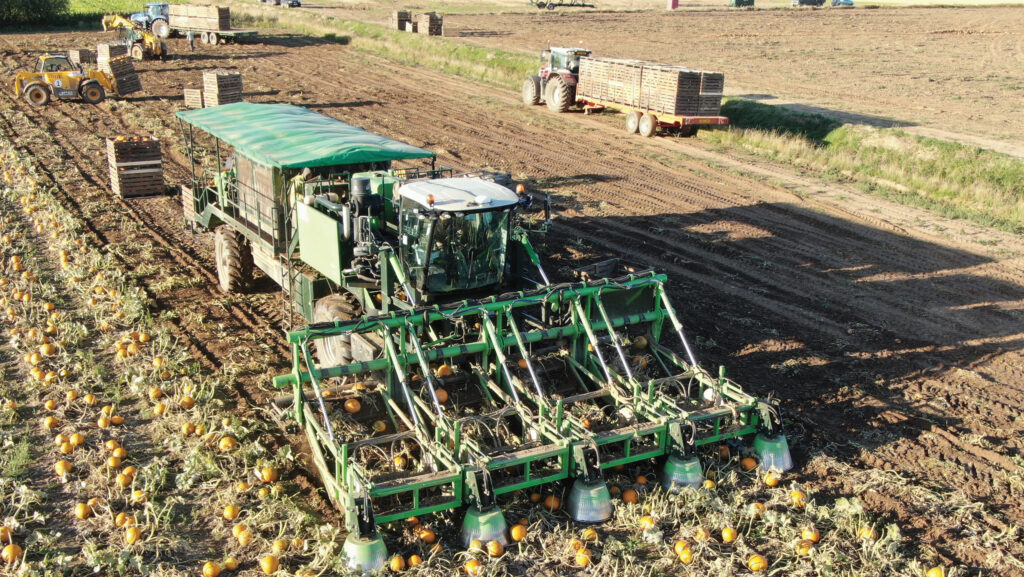
Each autumn, millions of pumpkins are plucked from their fields, carved into ghoulish lanterns and displayed with tealights flickering at their core.
The process of getting these orange gourds from soil surface to shop floors is a logistical tour de force, made all the more challenging by autumn’s oft soggy weather.
But by building a one-off, self-propelled harvesting rig complete with integrated washer and box loader, Lincolnshire grower David Bowman has dramatically streamlined operations.
See also: High-end bespoke builds put Grizzly Trailers on the map
The hulking machine can collect more than 70,000 pumpkins a day, getting the bulk of his 300ha crop harvested in just a couple of months.
By this time some 3.5m fruits will have been lifted – with a little help from some hand-picking crews – cleaned, sorted and distributed to retailers across the UK, Europe and as far away as Dubai.
Custom design
Designs for the harvester were penned by farm manager Mickey Daly and the late engineer Colin Reed, before Thetford-based Niagri took on the task of constructing it.
Work began in 2019 and the machine was ready for action halfway through the 2020 season.
However, it took a further three seasons to iron out teething problems and get it functioning perfectly.
The primary aim of the new outfit was to automate as much of the process as possible, cutting David’s considerable wage bill in the process.
Roughly 24 people were needed to run the previous harvester, most of which were tasked with manually loading the crop onto elevators at the front.
A series of mechanical cleaning webs and washers then took over, getting the pumpkins pristine enough for packing without human assistance.
However, a couple of manual graders had to step in for weeding out damaged and diseased fruits, while another team hand loaded boxes (bins) at the rear.
The start and end of this process were the obvious places to save on labour.
So, top of the wish list was a header for lifting the crop and a less labour-intensive system for filling the bins. Together, these developments would drop the crew number to just four.
Building a custom chassis would have completely blown the budget, so the hunt was on for an existing machine that could be adapted to suit.
A rolling potato harvester chassis built by Belgian manufacturer AVR proved the best fit, although major surgery was required to make it work.
First of the tasks was to reverse the direction of travel – a process that was simpler than it sounds thanks to the entirely hydrostatic transmission.
Doing this created more space for cleaning and washing equipment, while also turning it into a more manoeuvrable rear-wheel-steer machine.
At the same time, the Claas cab was spun through 180deg and repositioned at the new front end, giving it the silhouette of an elongated combine.
Ingenious header
More of a challenge was creating a header that could scoop the crop cleanly off the soil without causing damage.
Years of research and development went into this process, with 15 different test units trialled behind a tractor, before the setup was perfected.
The final version has four sections – each covering a row of crop – with floating “cones” at either side that gently guide the pumpkins towards a webbed elevator.
A rotating reel made from loops of pipe then takes over, preventing the fruits from rolling away as the elevator scoops them up.
This process is made all the more challenging by variable pumpkin sizes, which can range from 16cm to more than 35cm in diameter.
Stems are also bundled in with the crop, but a haulm roller at the top of the elevator grabs most of these and deposits them back on the field, minimising the quantity of debris to sort later.
More webbed elevators transport the pumpkins, shaking out soil as they go.
However, a couple of manual graders are still required to weed out any damaged or diseased fruits.
Next comes a washing unit, where a series of rotating brushes and water jets buff them to supermarket levels of cleanliness.
Cleverly, this is fed by a self-cleaning water tank, complete with rotating screen for filtering out soil.
This means, in normal conditions, the machine can work an entire day without having to be topped up.
And when it is refilled, it’s done so with water harvested from the roofs of buildings in the yard.
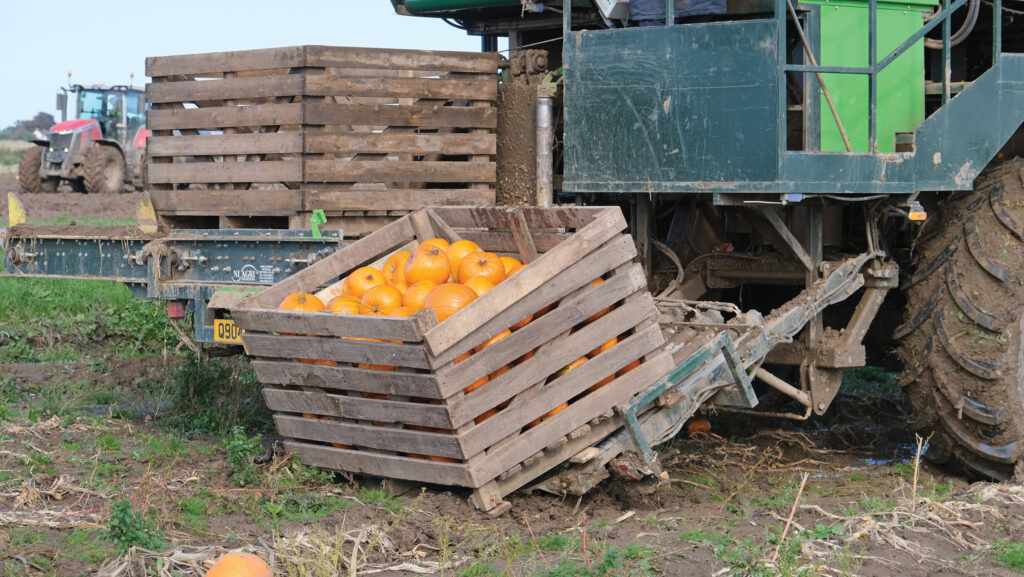
© James Andrews
Filling boxes
Finally, the hydraulic filling unit comes into play, tilting the bins at an angle so the pumpkins roll in gently, before lowering them to the ground.
A JCB Loadall then scoops them up and plonks them onto a trailer bound for the packhouse.
Meanwhile, another telehandler loads empties at the other side of the unit, allowing simultaneous filling and unloading.
Each bin holds roughly 100 pumpkins and the rig can process 700 of these a day.
Equally impressive are the logistics of ferrying eight trailers to and from the yard so that the harvester has an uninterrupted supply.
Such is the tightness of their turnaround that one employee is dedicated purely to ratchet strapping loads.
There’s even a team charged with repairing the wooden bins, all of which are made in-house during the off season.
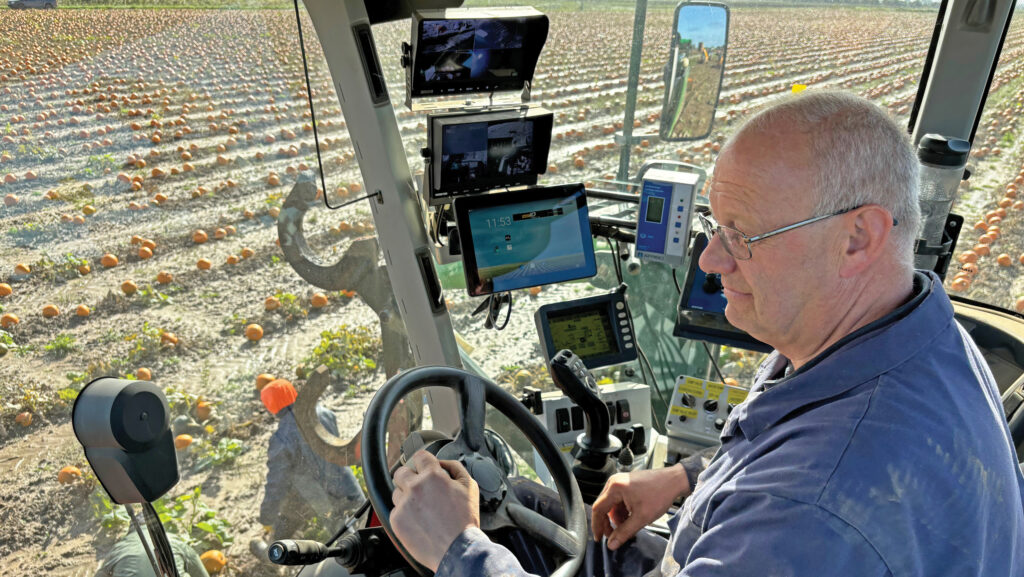
Driver Jez Smith © James Andrews
Driving it
Almost all the functions are driven hydraulically, with banks of electronic spool blocks controlled via a screen in the cab.
Once the speeds of the various sections have been set – each is programmed to run faster than the previous one to avoid blockages – driver Jez Smith can concentrate on piloting the rig and tweaking header adjustments via a separate purpose-built control box.
Forward speed is a sedate 2kph, but with yields averaging about 2,000 fruits/ha, filled boxes come off thick and fast.
Generally, the harvester rolls into action in mid-September and its work has to be completed before Halloween, after which demand completely dries up.
If conditions turn particularly wet – as is the case this autumn – the machine has been designed so it will still work with hand picking gangs.
In this setup, the header is dropped off, allowing the team to place pumpkins directly onto the webbed elevators.
This requires a temporary increase in staff numbers, but still saves time over the old system and allows work to continue.
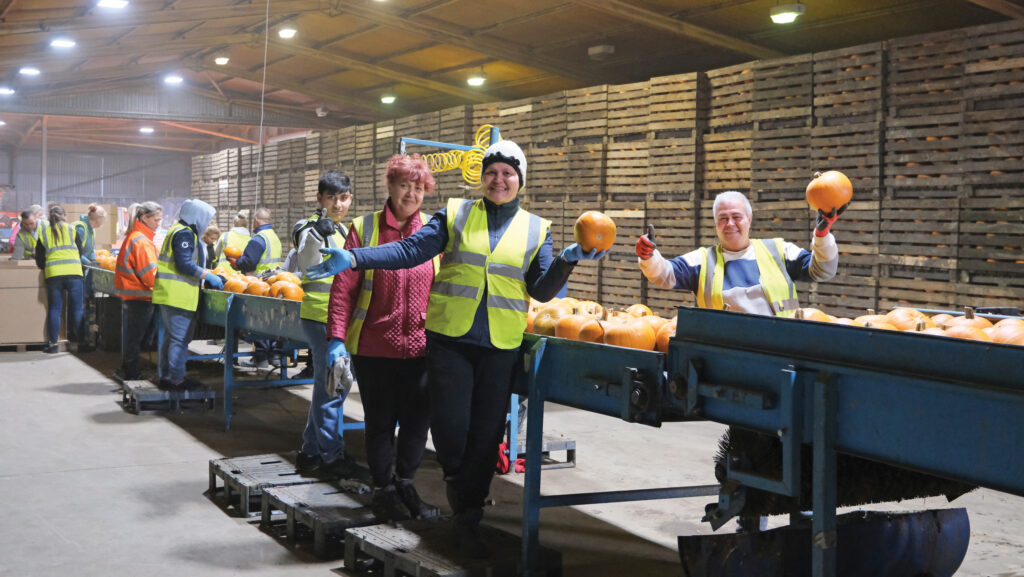
© James Andrews
Packing and shipping
Harvesting is just the first part of the process, with the crop requiring further grading in the packhouse.
And if lifting has taken place in particularly wet conditions, it’s sent through a secondary washing system, similar to that used on the harvester.
After this, teams sort the pumpkins by size, weed out any abnormal specimens, apply each supermarket’s specific pricing labels, and pack them in crates ready to be displayed on the shop floor.
A constant stream of HGVs – up to 45 a day – then whisk them off to their final destination.
David Bowman pumpkins
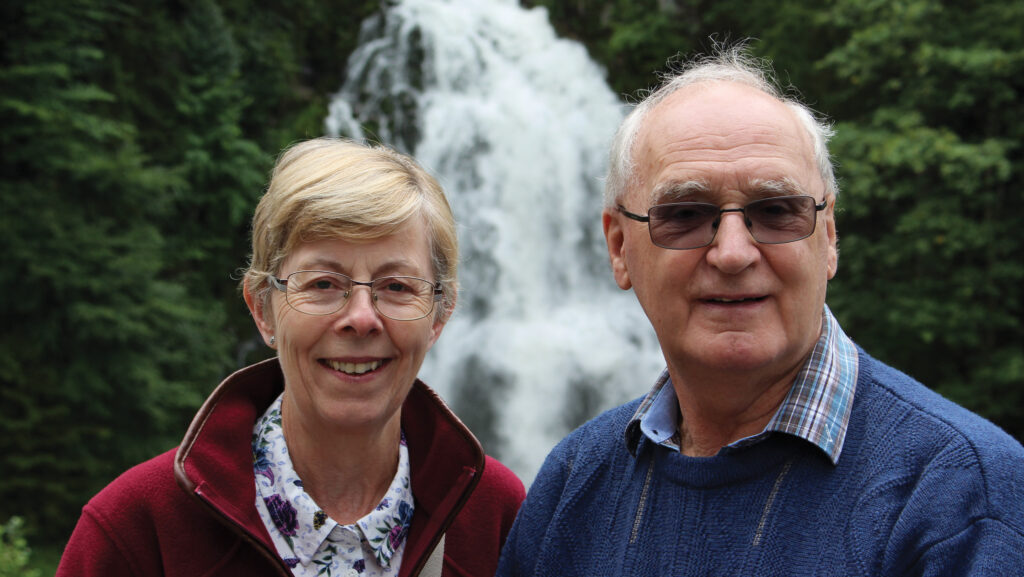
Janet and David Bowman © James Andrews
David Bowman has been producing pumpkins for more than 50 years, having started out scattering seeds alongside marrows destined for piccalilli.
There was little demand for them in the early days, but after a chance phone call with Tesco’s veg buyer, he managed to establish a market.
That first year he grew enough pumpkins to hand fill 1,200 second-hand apple boxes and David Bowman Pumpkins was born.
Such was the rise in demand thereafter that by 1990 he’d built his first trailed harvester which was capable of loading 150 boxes a day.
The first self-propelled machine came 16 years later and, with the help of his wife Janet, he’s grown the business to be one of the largest producers in the UK.
Tesco, Aldi, Lidl and Iceland are the biggest domestic outlets for the crop, but David also supplies scores of farm shops and pumpkin patches, as well as donating 10,000 a year to local primary school children and supporting the annual Spalding Pumpkin Festival.