Inventions Comp 2025: Low-cost sprayers, spreaders and cultivators
Contractors and farmers reveal their cunning plans and projects to save on the budget with some clever sprayer, spreader and cultivator inventions.
We take a look at some of the best entries to our Inventions Competition 2025.
See also: How Essex farmer adapted one cultivator to do four jobs
Will Monkman’s Avadex applicator
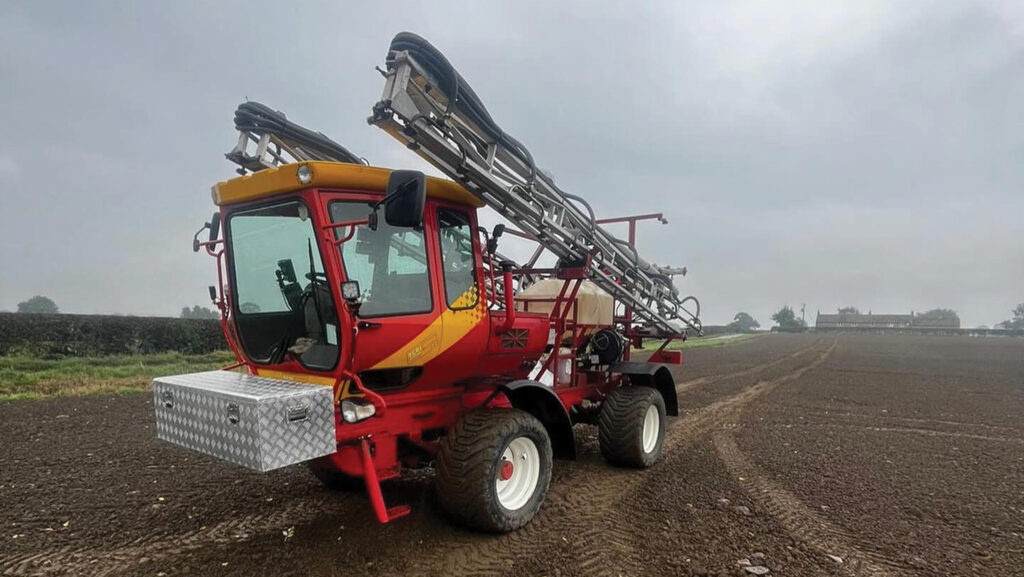
© Will Monkman
After seeing an increase in demand for Avadex application services, contractor Will Monkman of Malton, North Yorkshire, decided it was time to gear up.
He quickly chalked off the idea of buying a new 24m Techneat machine for the back of the tractor after receiving a quote of £52,000.
Instead, he tracked down a second-hand applicator of the same size for £8,000 and spent another £23,000 on a 2008-plate Agribuggy self-propelled sprayer to mount it on.
This lightweight setup allows him to spread Avadex and, potentially, small-seeded cover crop mixes and slug pellets, using existing tramlines.
The first job was to strip off the spray pack, which he replaced with a new frame to accommodate the 300kg hopper.
He then fabricated a set of spreader plate brackets, which he spaced at 50cm.
Mounting these was the biggest challenge, as it had to be done without them fouling the cab or framework when the boom is folded for transport.
Once this conundrum was solved, he plumbed them into the distribution heads – a process that required 22m of new pipe at a cost of £10/m. A local engineer then helped set it up and wire it in.
Adam Hills’ UTV-mounted sprayer
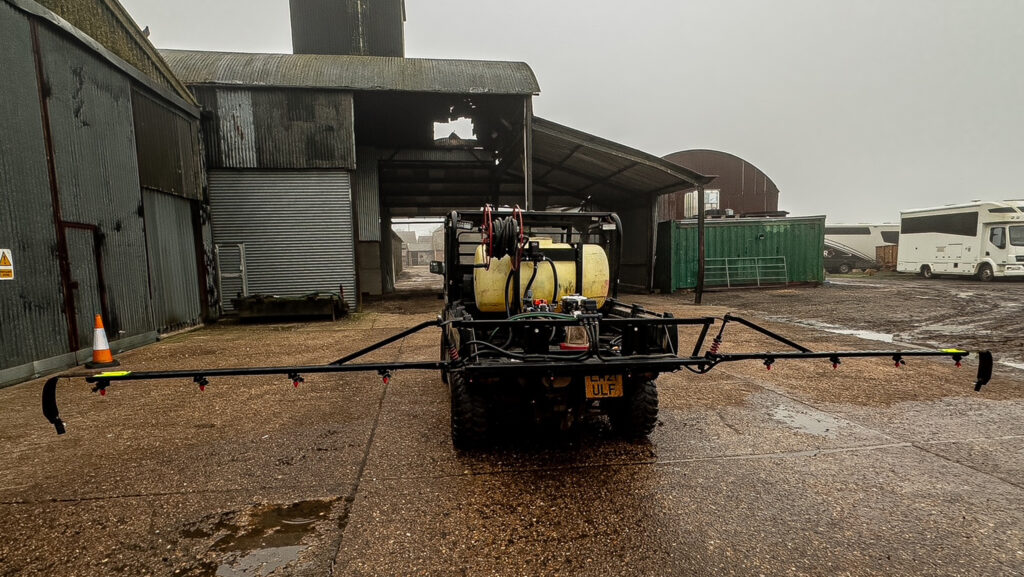
© Adam Hills
Spraying horse paddocks and game cover with the farm’s self-propelled machine was proving a bit of a fag for Hertfordshire-based Adam Hills, so he set about assembling a smaller and more manoeuvrable alternative.
The plan was to mount it on his Kawasaki Mule UTV, which meant assembling all the bits on a custom frame small enough to slot snuggly into the 500kg-rated load bed.
Phase one was to track down a donor machine – an old trailed Hardi – which was stripped of its 6m boom and 300-litre tank.
They were to be reused, but the original petrol engine and single-cylinder spray pump were deemed too tired and inefficient.
So, in went a twin-diaphragm pump and motor, complete with a pressure regulator and tank agitation, and fresh pipework across the board.
The new setup came with two outlets – the boom plumbed into the first and a hand lance in the second.
The latter is used for spot spraying creeping brambles and cleaning the grainstore pre-harvest.
The main expenses were £600 for the pump and £200 for assorted metal, part-funded by a fire sale of unused stuff kicking about in the workshop.
Andrew Wilson’s mobile potato wash rig
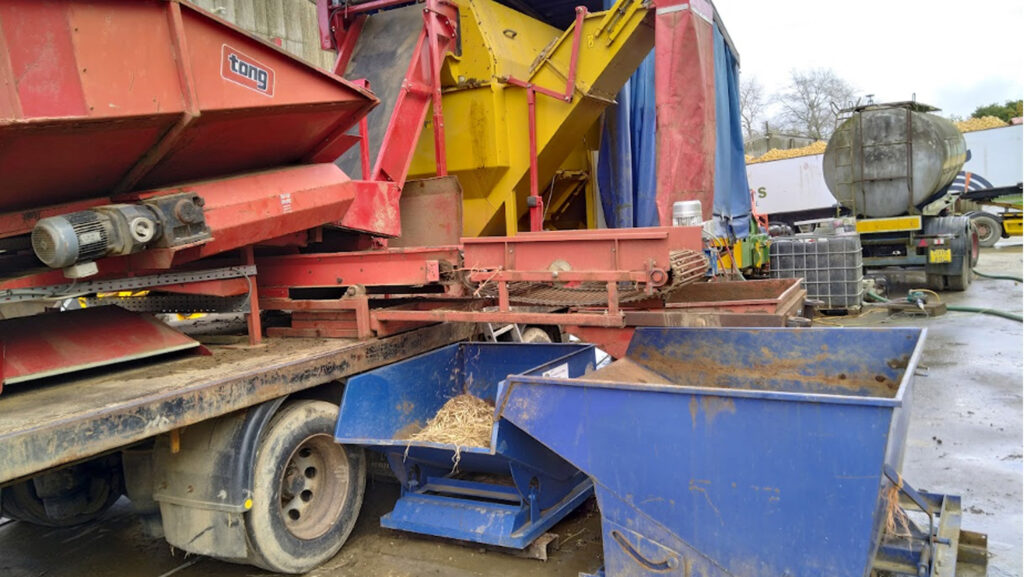
© Andrew Wilson
Slingsby spud grower Andrew Wilson was in dire need of a more efficient washing system and, unable to find what he wanted, he set about building one.
Key criteria were that it was mobile, could be loaded by a bucket, and would filter out sludge to help reduce the cleaning burden.
His first task was to source donor components, which included a 45ft step frame curtain sider purchased on eBay, a Tong washer that came out of a packhouse in Ireland, and a second-hand grader from Dave Brackenbury.
As he was tight for time, Andrew outsourced the assembly task to Mark Semper at Jomac Engineering.
He set to it, mounting the washer in the centre of the trailer and stripping down the grader to make use of the hopper, coils and conveyors.
The finished machine is loaded by a telehandler bucket at the rear and passes the spuds through a rotating screen suspended above a tank of water.
Sediment then drops down to an auger, which transfers it to a chain and slat elevator that loads it into a skip.
This means the water only needs to be changed for every 200t they process and the sediment tank needs scraping out every 1,000t or so.
Just three people are required to run it, only one forklift is needed and there’s virtually no mess.
In contrast, the old static system required eight people, three tractors, two forklifts and a lot of swearing.
Total build cost was about £40,000 and it’s been in regular use since it was completed in 2017.
Philip Matthews Agricultural Contractors’ drill filler
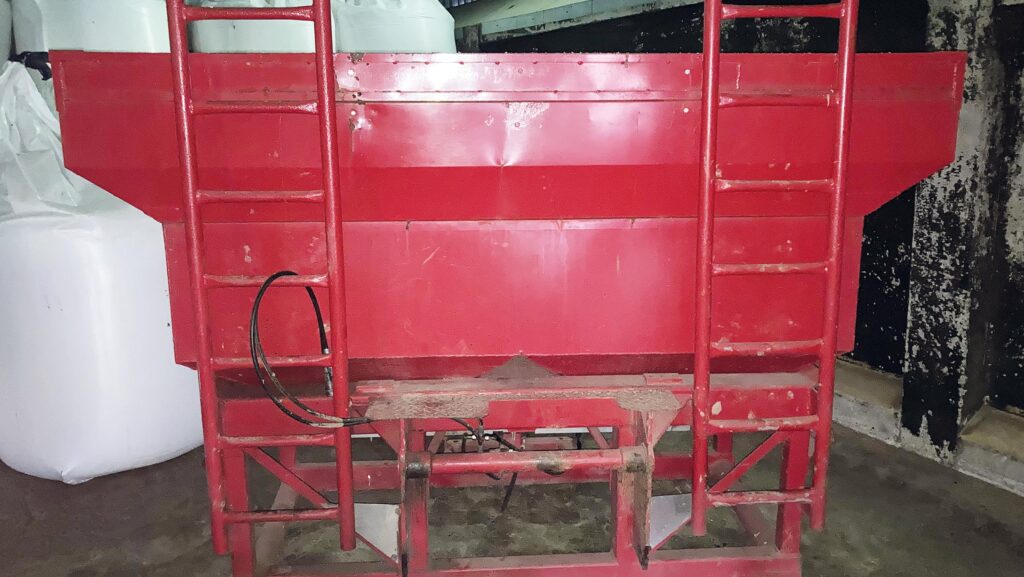
© Larry Eaton
Keen to streamline the process of refilling their Vaderstad Rapid drill and Kuhn Axis fertiliser spreader, the team at Chesham-based Philip Matthews Agricultural Contractors built a speedy filling device.
This is based on an old 2t fertiliser spreader hopper, with Manitou telehandler brackets welded on the back and a pair of large hydraulically operated sliding shutters to release the contents.
While the drill or spinner are working, another operator loads the filler with product ready to drive over and top them up when needed.
The seed or fertiliser is deposited in a matter of seconds, saving the faff of having to get out of the cab and untie or cut open bags.
This means the machines have to stop work for very little time, which makes a huge difference to output over the season.
While they were in fabricating mode, they modified a flatbed trailer to carry the rig, which they tow behind their telehandler.
This has custom brackets to support the filler, as well as security bars to lock it in place.
Alex Bullock’s 6m subsoiler
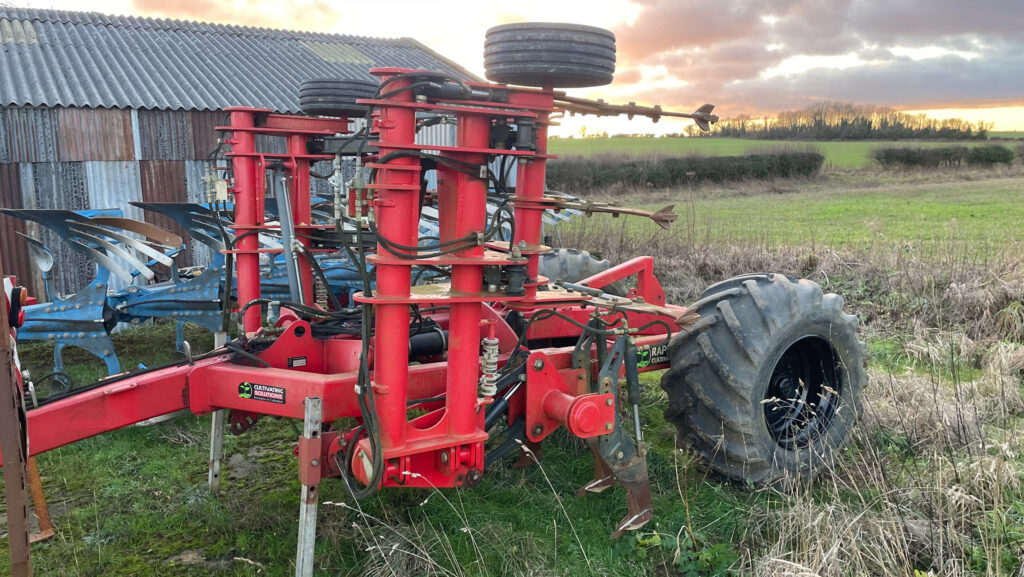
© Alex Bullock
After selling his Vaderstad Rapid drill, Gloucestershire-based Alex Bullock was left with a redundant 6m Cultivating Solutions toolbar.
The best offer he had for it was just £1,200, so he devised a plan to convert it into a trailed subsoiler.
Having sourced a second-hand trailer axle, he grafted this to the back of the bar where the drill would have originally been, before bolting on a set of rims running 600/55 R26.5 tyres.
These were originally from an MB Trac and had been languishing in the back of the shed for years.
However, because they were eight- rather than 10-stud, he removed the centres with a plasma cutter and welded in replacements using a jig to ensure they were central and ran true.
Initially, he’d planned to pull the subsoiler using the original towing eye, but to get it working deep enough, the points were almost dragging along the ground during transport.
To remedy this, he switched to a Scharmuller link-arm mounted hitch, which allows far higher lifting, better depth control when working and tighter turning on headlands.
This was by far the most expensive part of the build, but transformed it into a much more user-friendly machine.
Alex says it works well, providing conditions are not too wet, and it covers the ground significantly faster than his 3m McConnel Shakaerator.Â
Stuart Gallop’s Avadex applicator
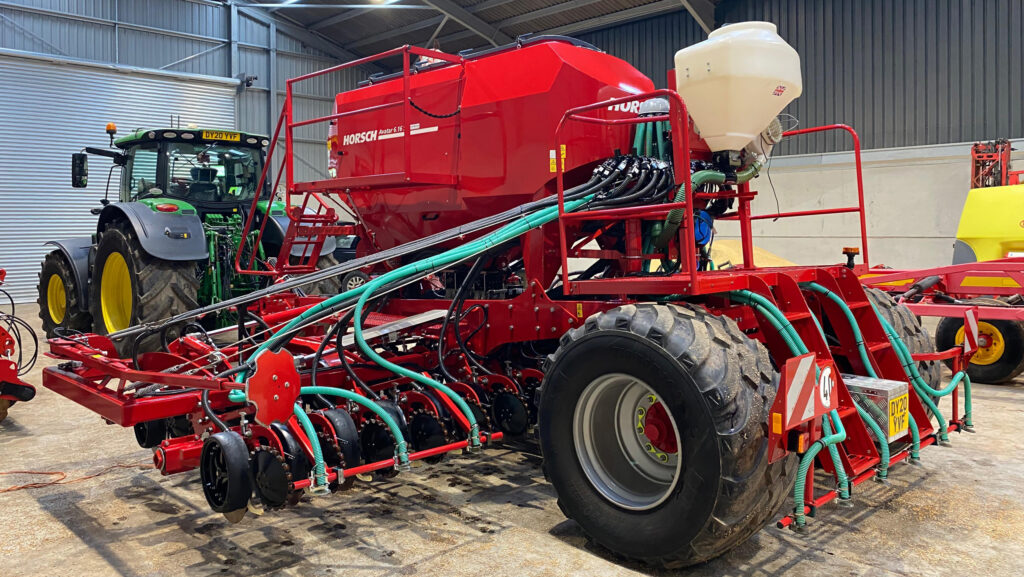
Stuart Gallop
You would be hard pressed to tell that the rear applicator attachment on the pictured 6m Avatar isn’t an original Horsch fitment.
In fact, it’s all the work of Stuart Gallop, based in Berkeley, Gloucestershire, who went to great lengths to ensure it matched the drill – including finding identical step treads and handrails, and finishing the lot with a Horsch-red powder coat.
At the front of the gangway is a tank, fan and metering unit upcycled from a set of rolls.
To maximise accuracy, the latter is wired into a pressure switch in the coulter bank so that the spreader plates are only fed when the drill is in the ground.
These are mounted on a bar aft of the soil working components to scatter Avadex or small seeds in the same pass.
Adam Truesdale’s self-powered implement carrier
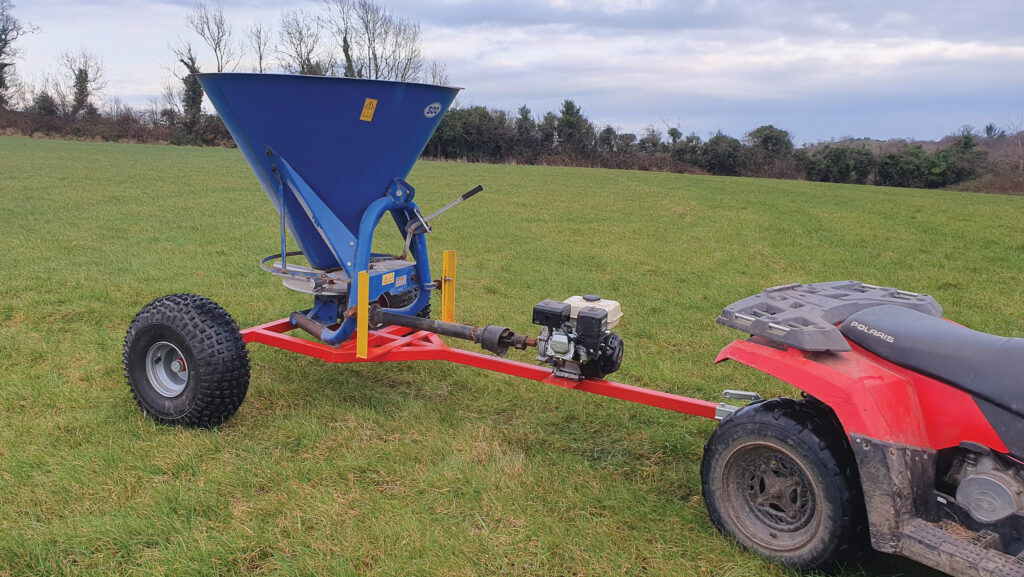
© Adam Truesdale
Mounting a four-stroke engine to the drawbar of a lightweight trailer allows County Down smallholder Adam Truesdale to run a Fleming fertiliser spinner or Jarmet sprayer behind his Polaris ATV.
As it was the first one he’d built, he decided to keep costs down by buying a Chinese replica of a Honda engine.
This cost just £300 delivered, complete with a reduction gearbox to reduce the output speed to 540rpm.
He then had a pto stub shaft machined to fit on the end, making it easy to couple to the implement sat on the box-section chassis.
Some simple bracketry joins the spreader or sprayer’s Cat 2 pins to angle iron uprights.
According to Adam, the empty trailer is barely heavier than a wheelbarrow, runs well on wet ground, and saves travelling long distances with a tractor.
Joe Brodie’s straw rake
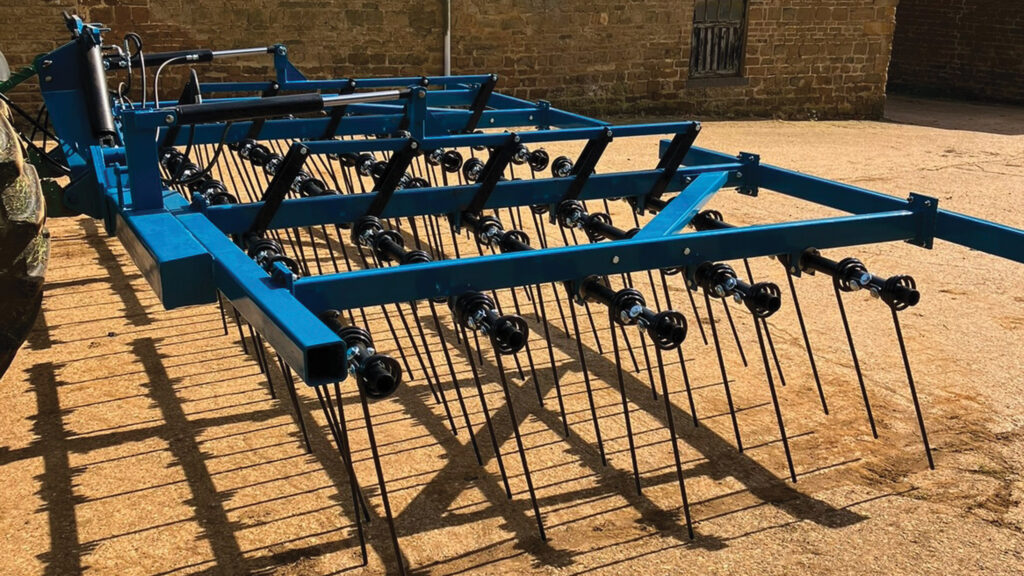
© Joe Brodie
Northamptonshire-based Joe Brodie fancied his chances of building a 6m straw rake for less money that it would cost to buy – and so it proved.
Total spend came to £4,500, of which £2,500 went on the ruck of 16mm tines from Spaldings.
The pitch of these can be altered via a pair of hydraulic rams, from almost vertical to horizontal, allowing them to be folded backwards for transport and, in work, tweaked to suit the volume of trash.
Rather than build a headstock from scratch, he pinched one from a scrap power harrow and welded on box-section beams that form part of the main frame.