5 home-built pieces of slurry kit which improved efficiency
Armed with a degree in mechanical engineering from Ulster University, Niall Murphy returned to the family farm and contracting business and set about making handy custom pieces of kit.
His creations have helped streamline operations on the 90ha farm with 80-cow dairy herd in County Armagh, Northern Ireland, as well as improving the efficiency of their silage, muck and slurry pumping operations.
Thanks to his university qualification and a year spent working for JCB in product design and engineering, he’s well acquainted with CAD software.
As a result, most of his projects are drawn and tested on the computer before he ventures into the workshop.
Usually, the first fabrication work he carries out is to start assembling and welding pre-cut steel profiles that he gets sent to the farm directly from a laser cutting firm.
Below, we look at five of the projects he’s completed over the past few years.
See also:Â Inventions Competition 2021: Feeding and bedding tools
Slurry Giraffe pipe gantry
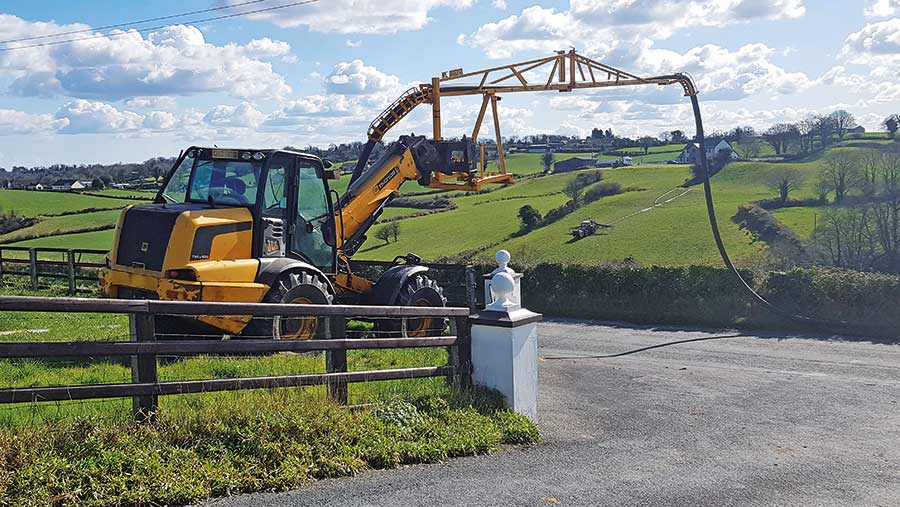
© James Andrews
Faced with the problem of having to span farm tracks and lanes with umbilical slurry pipes, Mr Murphy decided to build a telehandler-mounted gantry to keep them well clear of the tarmac.
His so-called Slurry Giraffe consists of a lightweight folding steel frame that can span 7.5m when opened out. It also lifts high enough for a fully loaded straw lorry to pass safely underneath.
For crossing smaller lanes, the gantry can be used in its folded transport position, avoiding it taking up unnecessary space.
Careful design work was put in to make sure the gantry was light enough to be lifted by a typical farm telehandler, yet strong enough to support the weight of loaded 6in slurry pipe.
To make sure the pipe stays in place when blowing out with a compressor, Mr Murphy fitted a series of securing bars.
He also incorporated removable curved guides to give the pipe a smooth arc as it enters and exits the gantry, as well as pushing it clear of the telehandler wheel.
Both guides can be mounted above the pallet tines during transport, and he’s added a traffic cone and sign holder ready to set up on the roadside.
Unreel slurry reeler
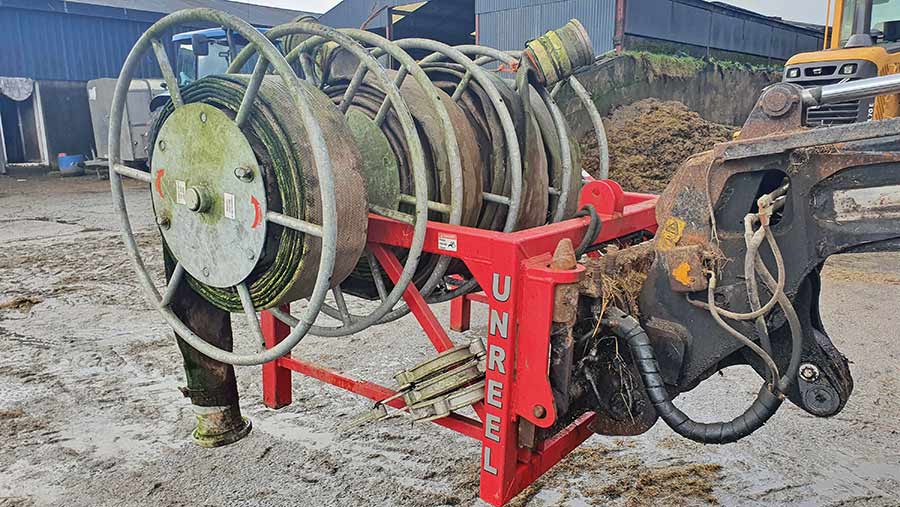
© James Andrews
To speed up the task of gathering small runs of slurry mixer pipe, Mr Murphy built a hydraulic multi-section reeler to fit on the front of his telehandler.
This has three main segments, which can accommodate lengths up to 40m – although most of his are 25m.
He also fitted a fourth section on the left with a removable side. This can be used for gathering up barbed wire or for winding borrowed pipe before it is returned.
An added benefit of fitting the reeler to a telehandler is that it can be raised, allowing slurry to run out quicker during rolling.
The outfit is powered by a hydraulic motor plumbed into the handler and it has a chain drive to the reel with a 4:1 speed reduction.
All the fabrication work was done in-house, apart from getting an engineering firm to bend the pipework and sending the reel to be galvanised. In total, the project cost about £970.
Close-coupled 1,000m reeler
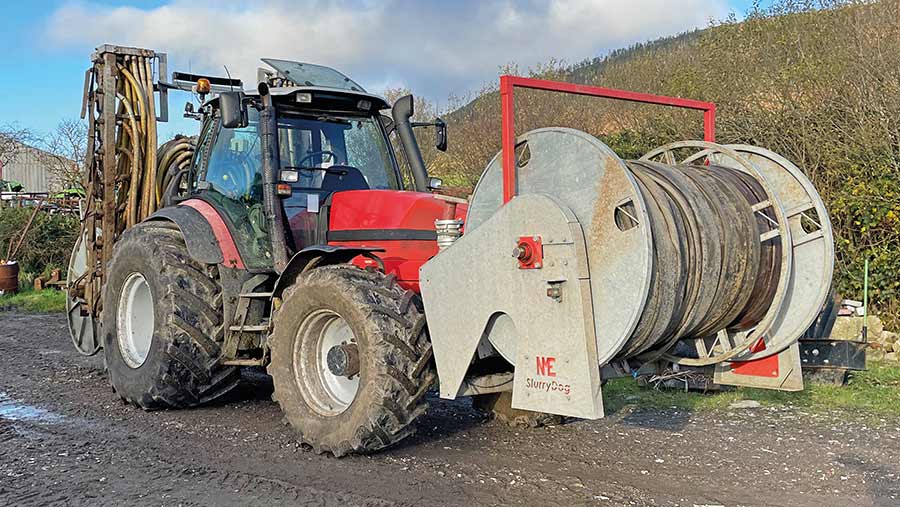
© James Andrews
After the success of his first reeler, Mr Murphy set about building a high-capacity version – dubbed the Slurry Dog – that would hold 600m of pipe on the main bobbin and a further 200m on the side.
To make it easier to lift on the front linkage of his Same Iron 150.7, and to reduce the distance it sticks forward, he spent hours designing a close-coupled sub-frame on the computer.
Although it took him a long time to get the geometry right, he says it was worth the effort as it is so much easier to manage.
All steel for the project was laser cut at a cost of £300 and he spent a further £600 having the frame galvanised to keep the rust at bay.
While his original reeler had an external chain drive to reduce the gearing, he managed to hide this one inside the main frame for a cleaner look.
Finishing touches include holders for spare pipe couplers and a mounting point for a homemade pipe clamp that’s operated using an impact driver.
This typically gets used when the pump has been turned off and they want to add in another length of pipe without slurry pouring out.
Front mower cameras
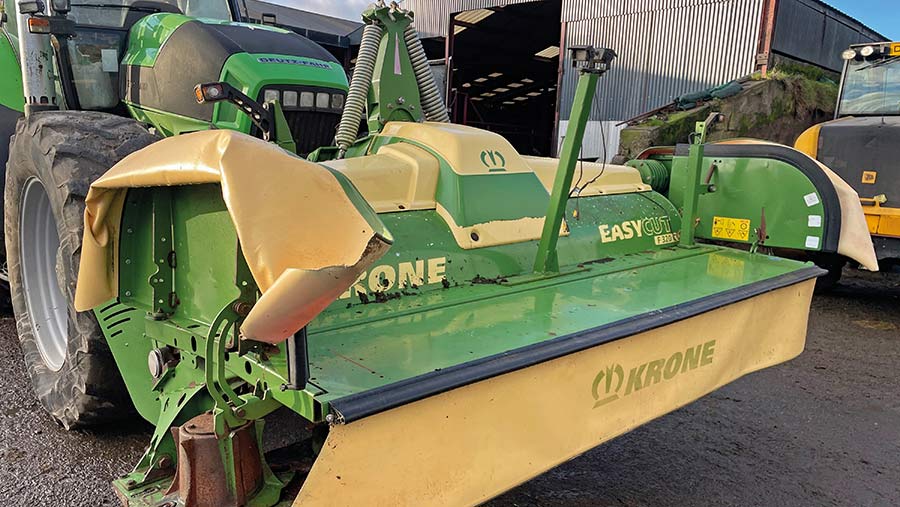
© James Andrews
Having had a few close calls when pulling onto the road with a front mower attached, Mr Murphy decided to fit a pair of night-vision cameras – one facing left and one facing right.
These are installed on a bar that sticks up well above the mower so that they give a clear view of the highway.
It seemed a waste to only use the cameras on the mower, so he also made a bracket to attach them to the front of his Deutz-Fahr X720.
Because this tractor has such a long bonnet, they significantly improve safety for any road work.
The cameras were bought online for £70 apiece and each is wired into its own display so the image is easy to see.
To help other motorists spot him, particularly at night, Mr Murphy has also added lights protruding above the mower guards.
Three-point linkage tractor jack
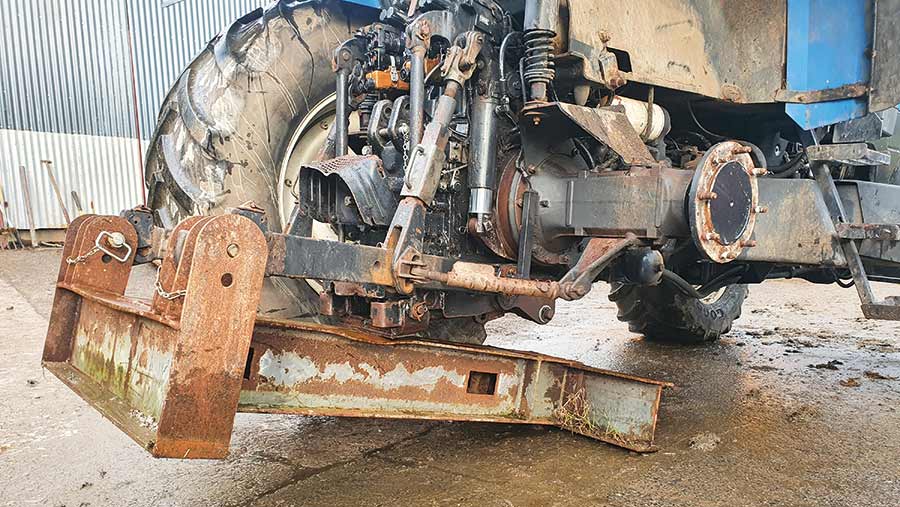
© James Andrews
To speed up tractor wheel changes and make the job safer, Mr Murphy built a simple jack that uses the three-point linkage to lift the rear wheels off the ground.
It works on the same principal as the Trakjak – built by fellow Irish contractor Padraig Fay – so as the link arms are lifted, the frame pivots on the pick-up hitch, causing the rear of the tractor to lift.
Mr Murphy’s version is a simpler take on the concept and was built out of metal he already had on the farm.
He says the tool has transformed wheel changes as he doesn’t have to mess about with bottle jacks and piles of wooden blocks.
Because both tyres are lifted clear of the ground, it’s also easy to turn the hubs so that the studs line up with the holes in the wheels.
To improve safety, he plans to add a set of adjustable legs that will support the weight of the tractor if the linkage fails.
He designed these in CAD, had the parts laser cut and they are sitting in the workshop ready for him to weld in place.