FW Inventions Comp opens for entries with £2.5k prize pot
It’s time for another season of Farmers Weekly’s long-running Farm Inventions Competition.
With a back catalogue containing thousands of ingenious ideas, there’s nowhere better to read about workshop builds that have saved time, hassle, or cold, hard cash.
And if you have designed a machine or gadget of your own, it’s time to get involved.
The competition’s format means that you can still win one of the top prizes even if your creation or modification is small and relatively uncomplicated.
The total pot for this year is £2,550, with the results decided by a panel of journalists and farmers.
See also: UK made kit converts any tractor to RTK autosteer for £3k
Categories
The entries are split into three categories: simple, intermediate and complex.
- Simple Items that took a day or so to knock together and are fairly basic in the way they work, but still save time or money
- Intermediate Anything more sophisticated, perhaps with a simple form of hydraulic or electrical system
- Complex Inventions that have taken months or years to design and build. They usually involve an engine or fairly complicated combination of electrics and hydraulics.
Who is eligible to enter?
Farmers, contractors, farm managers and farmworkers can submit their inventions.
What if I’ve entered my design in other local inventions competitions in the past?
You are still welcome to enter.
What are the prizes?
The winner of each of the three categories gets £500, runners-up will bag £250 and the third-placers get £100.
Will you feature the winners?
All nine prize-winning inventions will be featured, along with the best of the rest, in Farmers Weekly magazine and online.
Many of the machines that you see on the stands at shows such as Lamma start life in the farm workshop, so it’s a great opportunity to get your ideas in the shop window.
How do I enter?
Just send some details about how the machine works and what you use it for to oliver.mark@markallengroup.com.
You will also need to include a couple of decent-quality pictures and a phone number so we can get in touch.
The closing date for entries is 24 January 2025.
Who won last year?
Complex category – AJ Heywood & Sons’ slurry separator
The complex category winner was a self-powered slurry separator built over two years by Alan Gilkes for Cornish contractor AJ Heywood & Sons.
The machine was designed to split the liquid and fibrous elements of dairy waste, no matter whether cows are bedded on sand, straw or sawdust.
In doing so, farmers no longer have to apply thick slurry through a dribble bar, significantly reducing the risk of it sitting on top of the grass sward and contaminating subsequent silage crops.
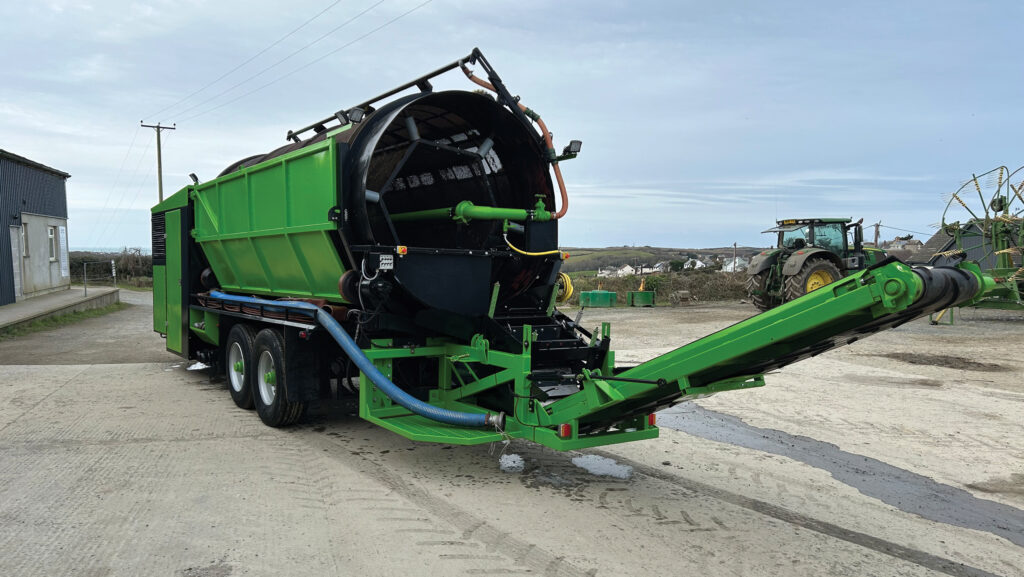
© Alan Gilkes
See also: Thompson Brothers’ bespoke umbilical slurry pumping trailer
The starting point was a redundant soil screener, sourced for just £4,500.
After chopping the chassis to put in a stepped frame and rejigging the axle configuration, Alan set to work on the separation system.
This is driven by the screener’s original six-cylinder, 130hp Iveco engine that, fortunately, was in good working order.
It runs four hydraulic pumps, three of which were already on the donor machine.
The fourth was salvaged from an old JCB TM telehandler. These run the major powered units – the main pump that discharges the dirty water, the drum, a roller press and the auxiliary rams.
In work, slurry from a lagoon, reception pit or tower is pumped into the centre of the separator.
The twin-mesh drum turns slowly, corkscrewing the material in a similar fashion to a cement mixer.
A hydraulic ram at the front allows the operator to alter its pitch, and, therefore, how quickly the fibrous element is moved through the cylinder.
As it rotates, the nitrogen-rich liquid drops into a sump bath below.
This is then pumped back to a store, sometimes via a settlement trailer that allows any sand to fall out of suspension so that it can be removed.
Some of the liquid fraction can also be recirculated to a pair of brush-type wash bars – one internal, the second external – that keep the mesh clean.
The solids are churned out the back of the drum, where they drop into a double roller press that squeezes out the last of the juice.
The resulting material, which has a dry matter of 25-30%, is then jettisoned from a 4m elevator at the back.
At about 100cu m/hour, output isn’t quite high enough to keep an umbilical system fed, but it could potentially be rigged up to work with a nurse tank and tanker.
Intermediate category – Jonny Leech’s monitor mounting brackets
Jonny Leech’s quick-release brackets for in-cab displays won last year’s intermediate category.
After having several monitors pinched, he came up with a design that would make them as easy to remove from the tractor as a GPS receiver – thus allowing farmers to stash them somewhere safe overnight.
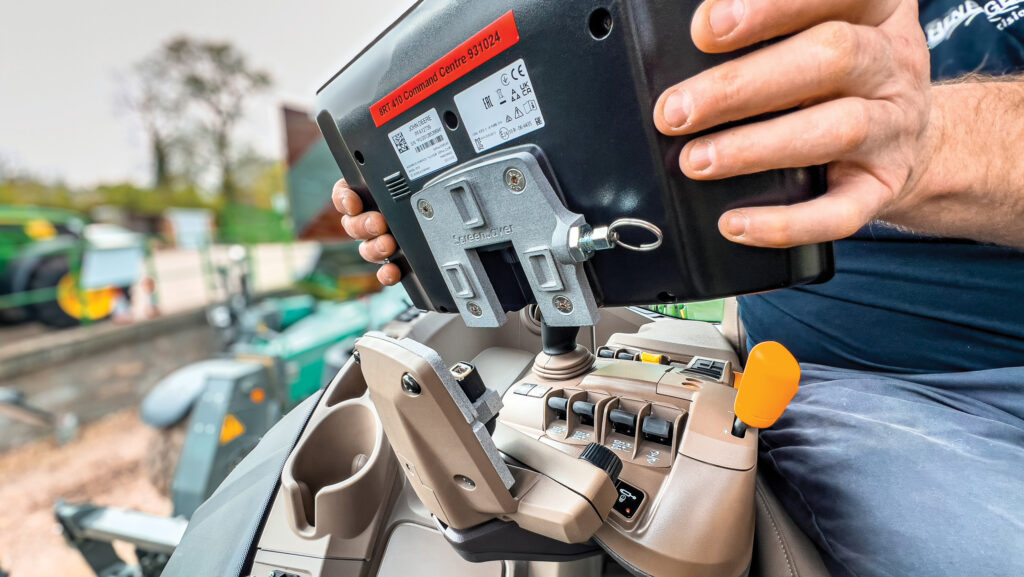
© Jonny Leech
See also: How to get cheaper or more accurate RTK guidance
One half of the ScreenSaver bracket is attached to the original mounting arm, the other half to the back of the display; the two slot together and the ethernet power and data cable is connected at the same time.
To separate them, operators support the display terminal, pull a spring-loaded pin and lift it away.
A version for John Deere Gen 4 and new Gen 5 screens is being sold through sole distributor Ben Burgess for £105, and iterations for Case IH AFS Pro and New Holland Intelliview displays are also available.
Simple category – Rob Gash’s chaff deflector
Nottinghamshire farmer Rob Gash conjured up a neat add-on that has transformed the ability of his Case IH 9240 combine to spread chaff evenly when leaving straw in the swath.
The angled deflector, made from metal plate flanked by rubber flaps, is automatically swung in and out of position via an electric actuator wired into the same switch as the chopper hood.
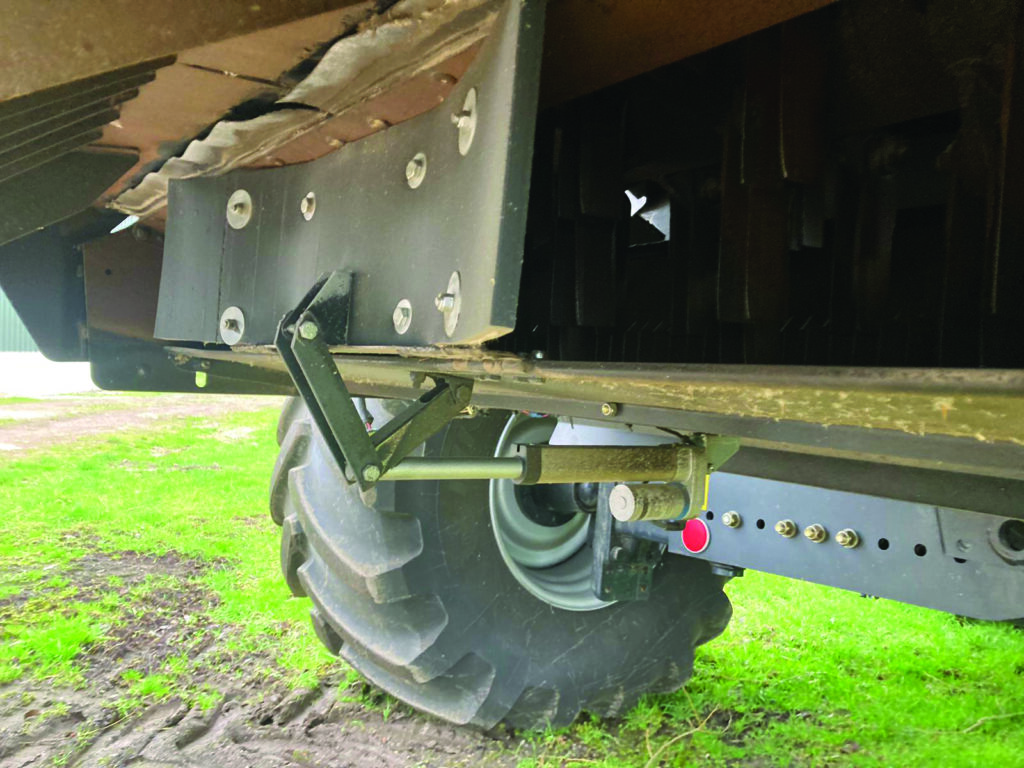
© Rob Gash
See also: How combine add-ons can help slash weed seed spread
In work, it directs the chaff to the outer veins of the spreader, ensuring it is fired across the full 12m width of the header.
This has eliminated subsequent problems of having excess chaff under the straw swaths when direct-drilling.
According to Rob, there are no such issues when running the factory-fitted Redekop chopper, which he says destroys the straw and reliably blasts all material full-width.