Cash prizes on offer in FW’s 2021 Inventions Competition
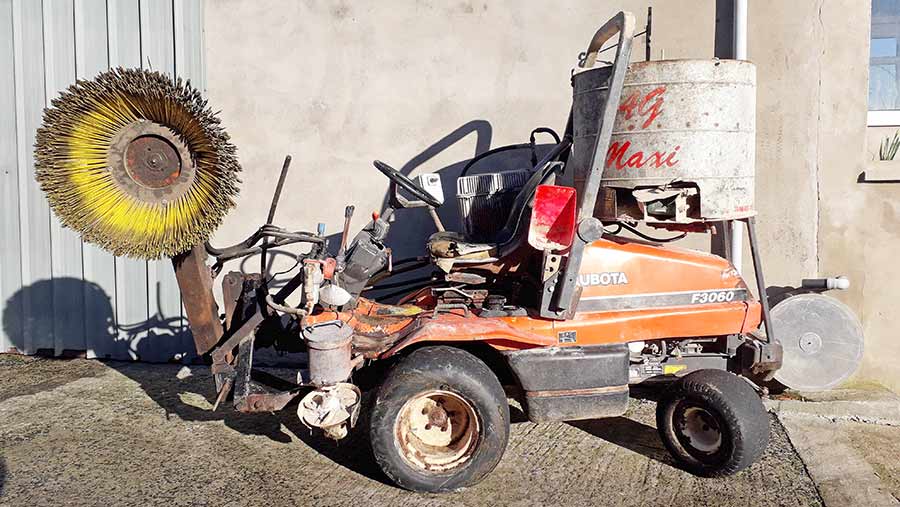
It’s time for another season of Farmers Weekly’s long-running Farm Inventions Competition.
With a back catalogue containing thousands of ingenious ideas, there’s nowhere better to read about workshop builds that have saved time, hassle or cold, hard cash.
And if you have designed a machine, gadget or knick-knack of your own, it’s time to get involved.
The competition’s format means that you can still win one of the top cash prizes even if you have built something small and relatively uncomplicated.
The total prize pot for this year is £2,550 – the winners of each category will bag £500, runners-up get £250 and third-place finishers take home £100, with the results decided by a panel made up of journalists and farmers.
See also: Read more workshop skills articles
Categories
The entries are split into three categories: simple, intermediate and complex.
Simple Items that took a day or so to knock together and are fairly basic in the way they work, but still save time or money.
Intermediate Anything more complicated, perhaps with a simple form of hydraulic or electrical system.
Complex Inventions that have taken weeks, months or even years to design and build. They usually involve an engine or fairly complicated combination of electrics and hydraulics.
Who is eligible to enter?
Farmers, contractors, farm managers and workers are welcome.
What if I’ve entered my design in other local inventions competitions in the past?
You are still welcome to enter.
What are the prizes?
The winner of each of the three categories gets £500, runners-up will bag £250 and the third-placers get £100.
Will you feature the winners?
All nine prize-winning inventions will be featured, along with the best of the rest, in Farmers Weekly magazine and online. Many of the machines that you see on the stands at shows such as Lamma start life in the farm workshop, so it’s a great opportunity to get your ideas in the shop window.
How do I enter?
Just send some details about how the machine works and what you use it for to oliver.mark@markallengroup.com
You will also need to attach a couple of decent-quality pictures and a contact phone number so we can get in touch.
The closing date for entries is 29 January 2021.
Who won last year?
GJ Agri’s self-propelled stone picker – Complex category winner
The Stonebine, built by Jack Bailey and his colleagues at Dorset-based contractor and engineer GJ Agri, was our 2020 Farm Inventions Competition champion.
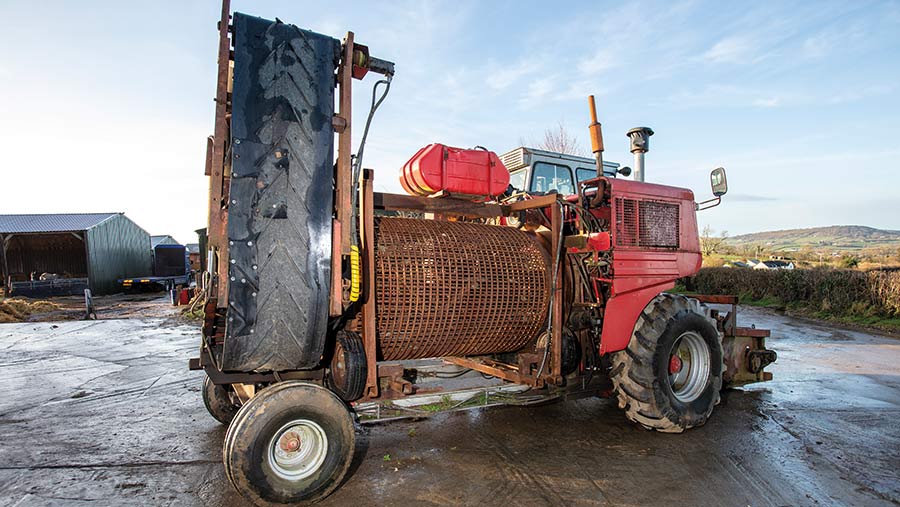
GJ Agri’s self-propelled stone picker © Fototek
The quirky converted combine was designed to harvest an unusual crop – flint from fields north of Lyme Regis.
Having scoured the market for a suitable stone-picker, they could only find machines that used spring-loaded tines to flick rocks into a big hopper.
However, these were no good for the farm’s building-grade flint stone – worth £65/t in good condition – as they tend to deliver a dirty sample. The sprung tines also have a habit of cracking the flint, obliterating its sell-on value and leaving razor-sharp shards across the field.
So, after five years of planning, the team at GJ Agri got to work building their own hopper-less version.
The priority was a self-propelled machine with a side cab that would leave ample space for the elevator to run under the engine, so when a 1970s Massey Ferguson 500-series combine came up for sale, they snapped it up.
The donor machine, on a little under 4,000 hours, was stripped almost bare – the only major components that remained unmoved were the engine, front axle and hydrostatic drive.
Major surgery included fitting chassis rails that extended the combine to form enough space for the screening system.
The picking and processing elements include a second-hand Reekie 300 SA digging rotor and web, and an Extec 5000 elevator. One of the biggest expenses was a trommel screen, which was home-built because there was nothing reasonably priced on the second-hand market.
Power to a new triple-stack hydraulic pump arrangement comes via the combine’s old threshing drum drive belts. This runs oil to separate hydraulic motors on the auxiliary services, including the trommel and front and rear elevators.
The flow to each can be altered using an external control valve, and functions can be turned on and off via in-cab switches.
In work, the engine runs at full chat – roughly 2,100rpm – and forward speed is determined by the quantity of stone.
Lifting rowed-up flint from a 7m band limits progress to roughly 1kph, but it can get up to 3kph when picking straight from the ground across its 2m working width.
To give an idea of output, it lifted roughly 1,250t of flint from a 4ha field in one day, some of which was already raked into a line.
The version pictured at the top of this article had come straight out of the workshop, but the team has since fitted guards to all the components and shot-blasted and painted it.
Roger Page’s sward-slitter dribble bar – Intermediate category winner
Intermediate category top spot was taken by Roger Page’s sward-slitter dribble bar.
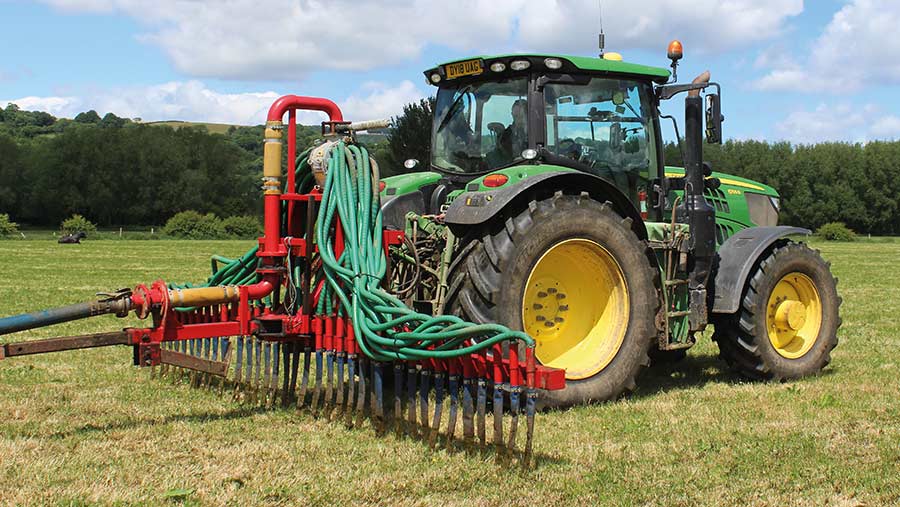
Roger Page’s sward-slitter dribble bar © James Andrews
Following a number of customer requests to combine sward slitting and slurry application into a single operation, Powys contractor Mr Page came up with a custom dribble bar design.
His original attempt at combining the two processes involved mounting his Opico sward slitter on the front linkage and running with his 6m trailing shoe at the rear.
However, the sward slitter proved too hard for the tractor’s auto-steer system to overrule, so he went in search of another solution.
He initially looked for an off-the-shelf dribble bar, but none of these had the correct pipe spacing to line up with the slitter’s rotors.
Therefore, he set about making his own in the farm workshop. The starting point was to mount a three-point linkage on the slitter for the dribble bar to hang from.
The dribble bar frame was then constructed with a central section that carries a Vogelsang macerator and a telescopic towing arm for the umbilical pipe. This is designed to push the pipe out of the way during headland turns and has a drop-down foot for gathering it up at the end of the job.
The pipe outlets are mounted off box-section wings on both sides and these fold hydraulically with the frame of the slitter. According to Mr Page, this was the trickiest part of the build to get right, as there was so much pipework to deal with.
It was built in the winter of 2017 using all new metal, and it took about 70 hours to complete. Total build cost was about £7,000, including the £2,000 macerator.
No changes have been made to the design since then and about 60% of Mr Page’s umbilical work is now carried out with it. The rest is split between trailing shoe and splash plate.
Robert Schwier’s seed bag cradle – Simple category winner
Winner of the hotly contested simple category was Robert Schwier’s seed bag cradle.
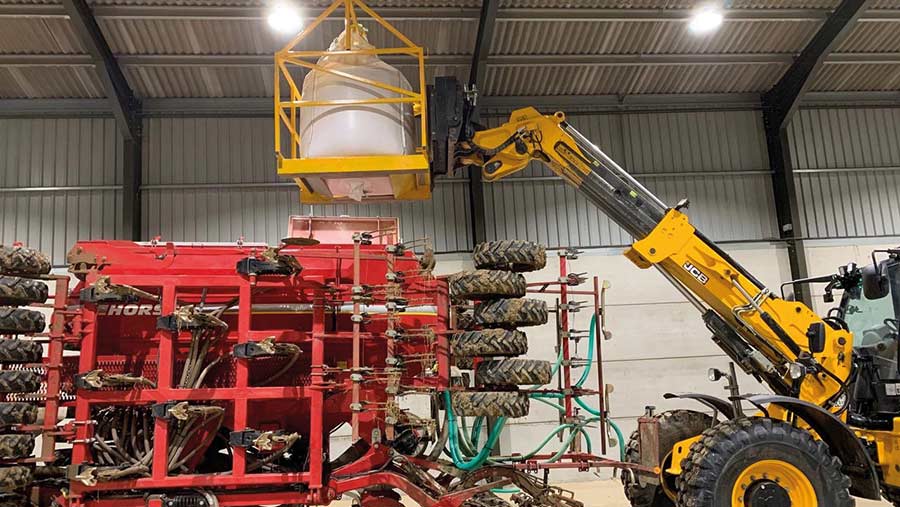
Robert Schwier’s seed bag cradle © Robert Schwier
After a 1t seed bag strap broke, narrowly missing the operator and damaging the drill’s Avadex unit, Essex farmer Mr Schwier decided to come up with a safer alternative to lifting live weights above workers’ heads.
Safety and ease of use were paramount, and his cradle design removes any reliance on the bag’s strap and instead rests the full weight on the heavy-duty box section of the cradle.
The bag is lifted into the box and a bar is put through the strap loops. This doesn’t take any of the weight, but stops it from falling through the bottom when it’s empty.
The cradle is lifted via pallet fork slots underneath, which helps to keep the centre of gravity much lower than before, while also extending the reach of the farm’s articulated loader.
It is easier to see when travelling on tracks and following vehicles, as the bag isn’t swinging around and blocking the driver’s view, says Mr Schwier. It took about a day to knock up and cost very little, as all the metal was already on the farm.
Our sponsor
To achieve your goals, you need the right tools for the job. If what you need doesn’t exist, simply invent it. We share this ethos and used it to create the Ineos Grenadier. An uncompromising 4×4, built on purpose and there to support those who need it most.