Why Cambs arable farm invested in its own tractor-mounted trencher
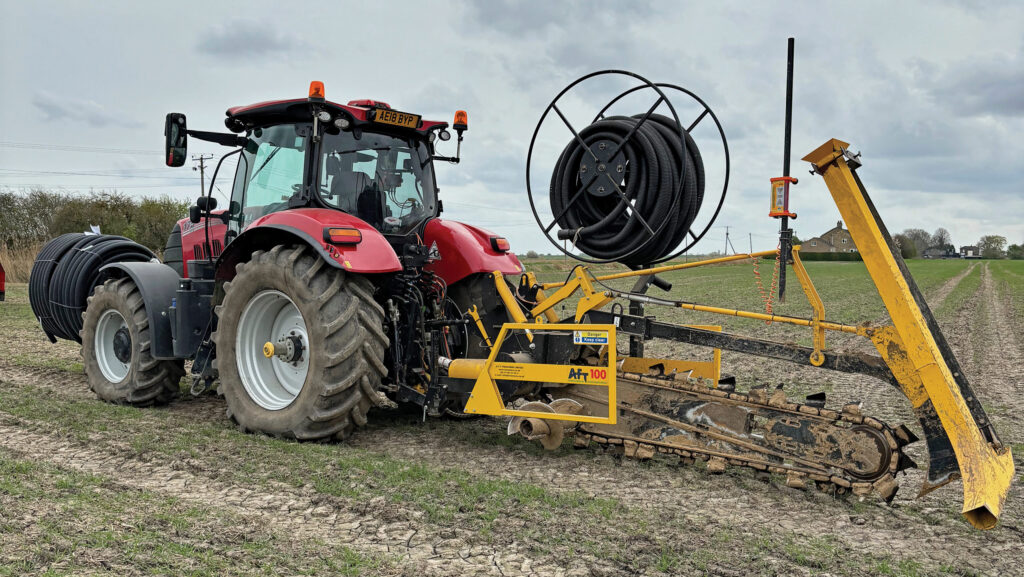
When a portion of their land began identifying more as lake than field during winter months, Stephen and Richard Mead were forced to invest in some drainage.
Quotes were sourced from local contractors, which ranged from about £2,500 to £3,000/ha in 2021, and they began exploring the option of completing the work themselves.
Acquiring the gear to do it properly would be steep to start with, but with the amount of ground they needed to cover they soon established that this would be a cheaper approach in the long run.
See also: How, why and when to mole drain
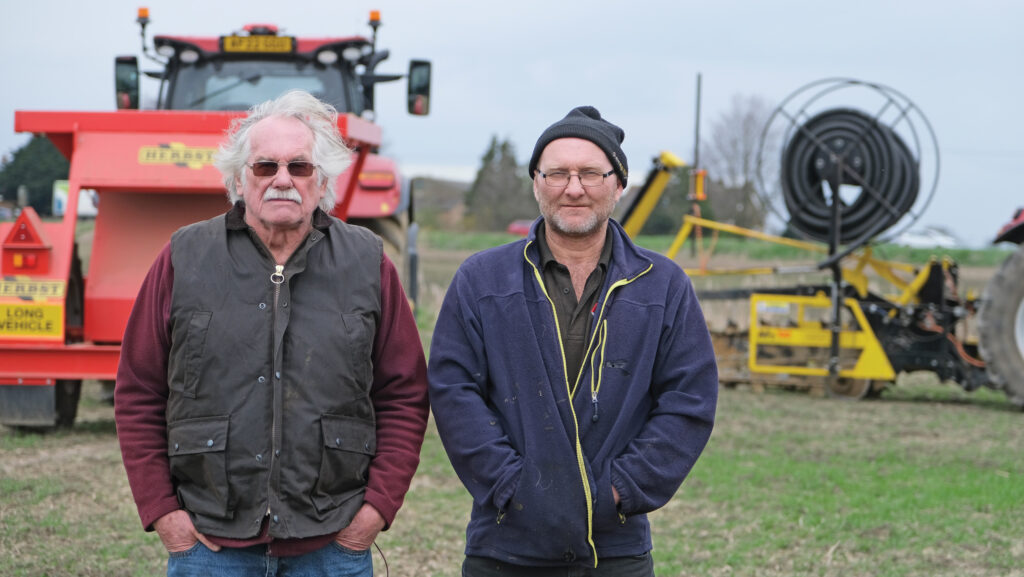
Stephen (left) and-Richard Mead © James Andrews
Most of the Meads’ land is a mix of silt loam ridges and clay hollows, with the former relatively free draining and the latter largely not.
Four undrained fields were the worst culprits for water standing in the hollows. However, many of the clay drains installed on their 223ha arable farm near Guyhirn, Cambridgeshire in the 1960s were beginning to lose their effectiveness.
“We had about 72ha that needed draining as soon as possible, which would have cost around £180,000 to £215,000 if we’d got contractors in,” says Stephen.
That gave them a considerable budget to play with when looking for suitable equipment to carry out a DIY job.
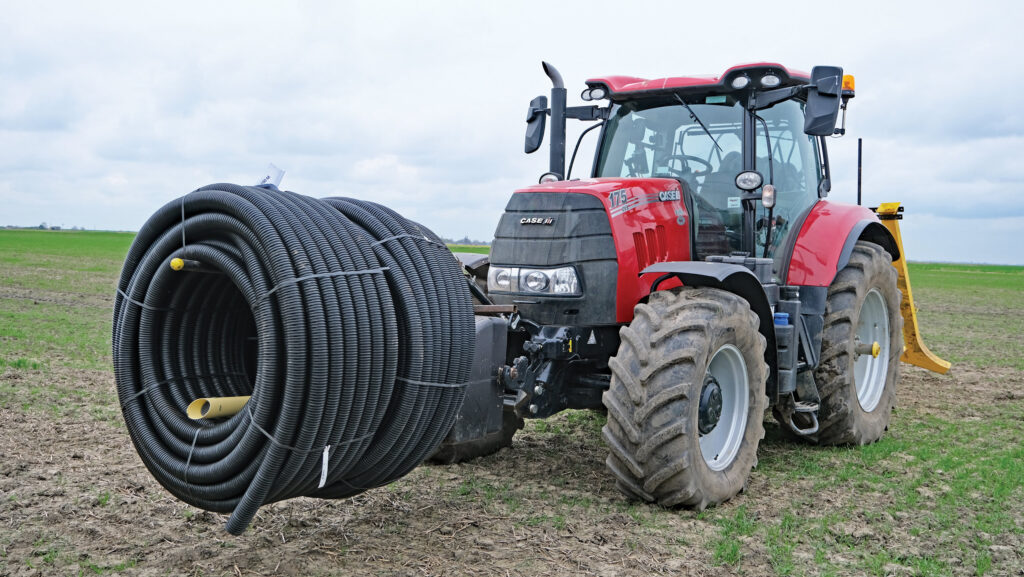
© James Andrews
Tractor-driven trencher
AFT100 trencher
- Digging depth 1.8m (1m, 1.2m, 1.4m and 1.6m models also available)
- Digging width 125 to 300mm
- Depth control Laser guided
- Price paid £35,300 in 2021
Second-hand drainage machines were a bit of a minefield, so they turned their attentions to new tractor-driven models, eventually shelling out £35,300 on an AFT100 trencher.
This came with the longest 1.8m digging arm, enabling it to get to the depth of their lowest drain outfalls.
Other features include a hydraulic pipe reeler and an automatic laser guidance system, which continuously alters the working depth to achieve the correct fall on the pipe.
Another extra was a combined gravel hopper and pipe laying chute, which they initially thought would be the most efficient method of getting both these items in the ground.
They also invested £9,500 in a Herbst gravel trailer and built their own front linkage-mounted blade for pushing soil back into the trench once the pipe is laid.
This was fashioned out of an old Farmforce front press, with the blades formed from a curved diesel tank reinforced with lengths of RSJ.
Before putting any pipe into their undrained fields, Stephen and Richard drafted in Lincolnshire Drainage Services to survey the fields and design the most efficient way of moving the water.
The farm sits on so-called Bedford Adventurer land that was reclaimed at the turn of the 18th century using a series of hand-dug channels.
Some of the land sits below sea level, rising to a maximum of 7m above, and without these most of it would sit under water for a large portion of the year.
Today, the nearby Cross Guns pumping station keeps the water level down by helping the water on its way to the River Nene.
The pumps are required for getting it out of the immediate local area, but there’s sufficient fall for it to travel most of the way via gravity.
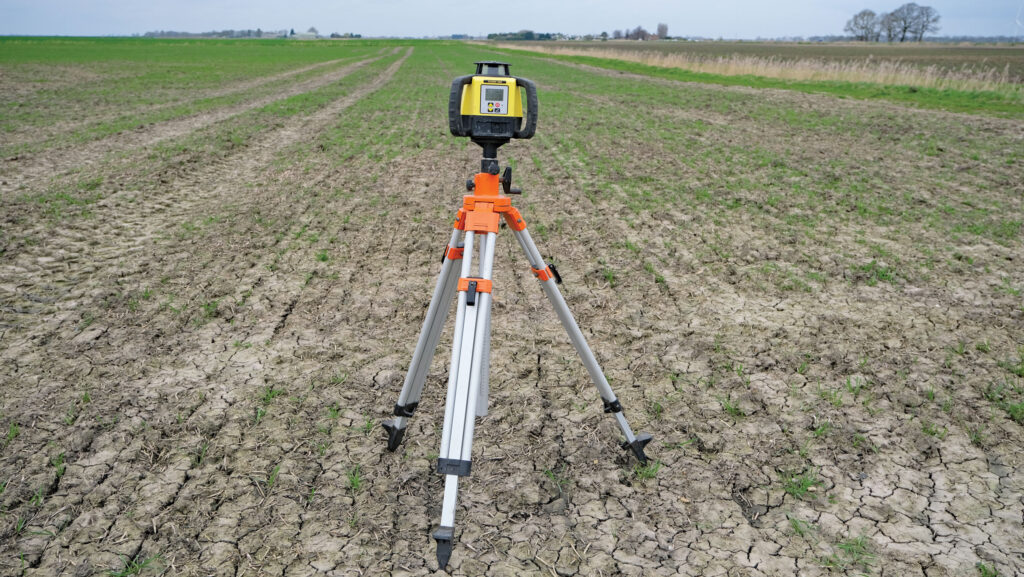
© James Andrews
Using the machine
Once there was a drainage blueprint to follow, the father and son team could get to work.
For each pipe run, they set the machine up on the edge of the ditch or drain and dig down to the desired depth of the outfall.
The laser is mounted on a separate tripod and, once it has been levelled, they input the desired fall – typically between 0.15 and 0.25m over 100m.
They then slide the receiver on the machine up or down a pole until it picks up the laser beam.
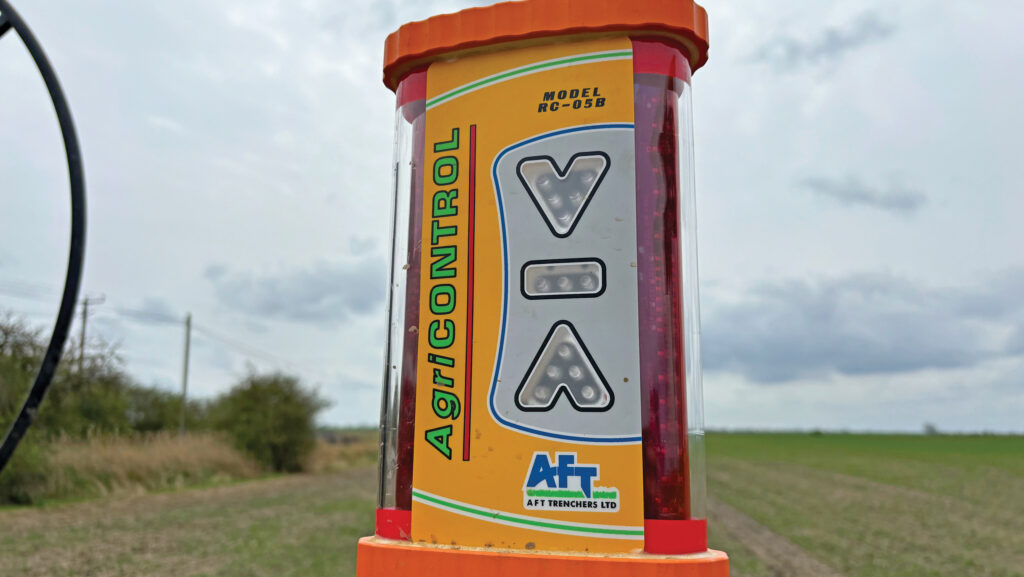
The laser receiver © James Andrews
Next, Richard presses a button on the in-cab control box to activate automatic mode and it will dutifully follow the path of the laser without any further input from him.
His only challenge then is to drive in a perfectly straight line. “We’ve got autosteer on the tractor, but we’re running on a Trimble Rangepoint correction signal which won’t engage at the 0.25kph we’re travelling at,” he says.
To get around this, Richard does a dry run at the start of each field to put in wheel marks that he can follow.
“Once the first pipe is in, I reverse down the next run at a high enough speed for the GPS to work, giving me the next set of wheel marks to follow.”
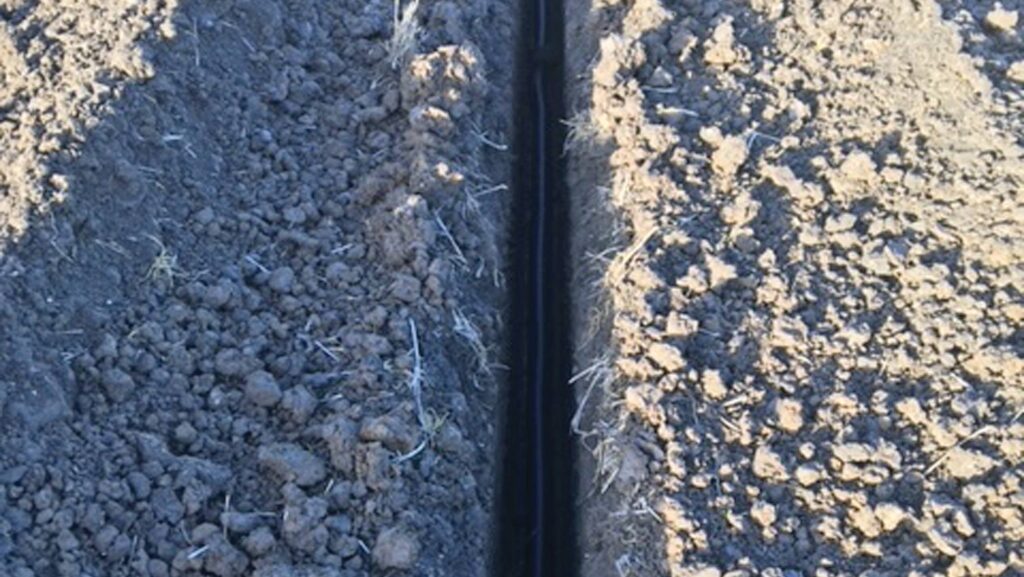
© James Andrews
Their pipe of choice is 80mm perforated, which the machine dispenses in 100m rolls, and Richard has made a holder for the tractor’s front linkage that can carry an extra two spools.
To begin with, they laid this using the combined pipe chute and gravel hopper, with Stephen driving alongside to feed the stone in from the trailer via its extending belt conveyor.
However, they had to keep stopping the drainage job to fill the trailer up with stone, leaving Richard twiddling his thumbs in the field.
Trenches dug on their ground aren’t at a high risk of collapsing, so they changed tack and spent an extra £1,400 on a dedicated pipe chute.
It allows them to lay just pipe with the trencher and put the gravel in afterwards directly from the cart.
This approach is far quicker as Richard can keep trenching without any interruptions. Stephen has also found a way to calibrate the cart so that he always puts an even layer of stone over the pipe.
“I set the speed of the tractor at 2.5kph and by adjusting the flow of the spool valve feeding the elevator to 25% it gives an even 16in covering,” he says.
They only use gravel on the clay areas of fields though, as the silts are sufficiently free draining that they don’t require it. “That really helps reduce the cost per metre,” he adds.
This system has worked well, so the original chute and gravel hopper arrangement is up for sale.
Once the gravel is in, Stephen hops on a separate tractor with the front blade attached and pushes the soil back into the hole.
As the trencher digs, it has short augers at either side of the chain that place soil in neat bands beside the cutting.
For this reason, they built the dozer in a V shape with two angled blades that push both sides in at once.
“By the time I’ve run up the trench and back, the soil is sitting in a neat mound, which eventually settles to give a fairly even surface,” he says.
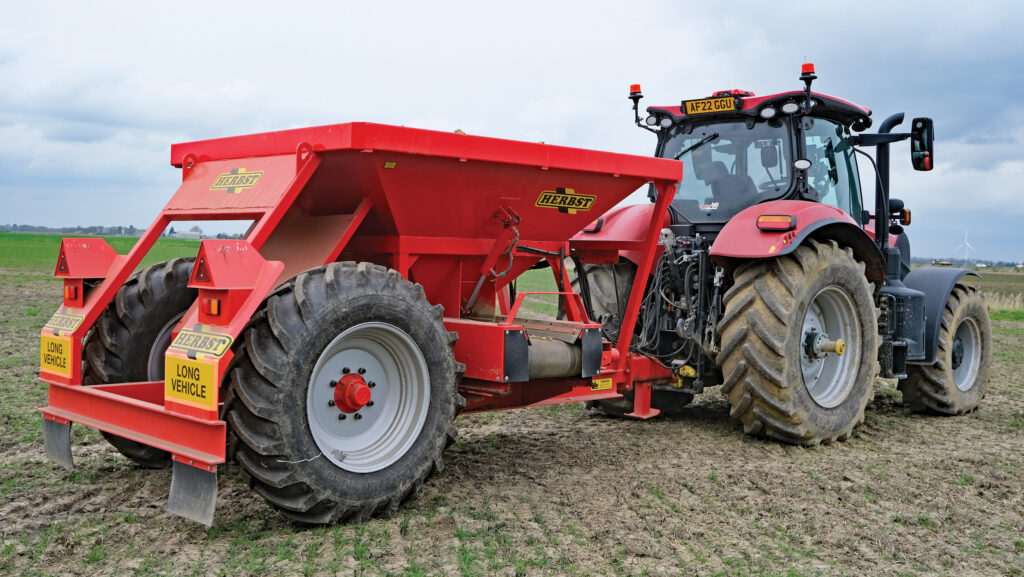
© James Andrews
Sound investment
Since Stephen and Richard bought the machine in 2021, they’ve piped all four of their undrained fields and put a few new runs in next to collapsed clay sections in other fields.
This adds up to 10,200m, which has so far cost them £2,945/ha – roughly the same as the original cost of a getting a contractor in.
“That figure includes the cost of all the machinery, so the price per hectare will get far cheaper as we do more with it,” says Stephen.
For clay drained fields, costs are further reduced by the fact they can work off the original 1960s plans, rather than paying for additional surveying.
They intend to gradually work their way around the farm putting new drains next to the old clay runs. Consumables for this work out at about £2/m.
Drainage is generally carried out between harvest and drilling and, with crops such as winter rye grown for a local anaerobic digester plant, and winter barley, they have a decent window before the next crop goes in.
All the land they’ve drained so far has improved dramatically, with no water standing on the surface, despite the deluges of the past few months.
The clay content of the soil does mean they need to work it to achieve decent crop establishment.
This means most ground gets ploughed and immediately worked with a 3.5m Kuhn power harrow to create a seed-bed.
To keep the surface open after working and allow water to drain through they have a Mecmac spring-tine cultivator mounted on a three-point linkage behind the harrow.
When they are ready to drill, the crop is put in with a 4m Vaderstad Rapid.
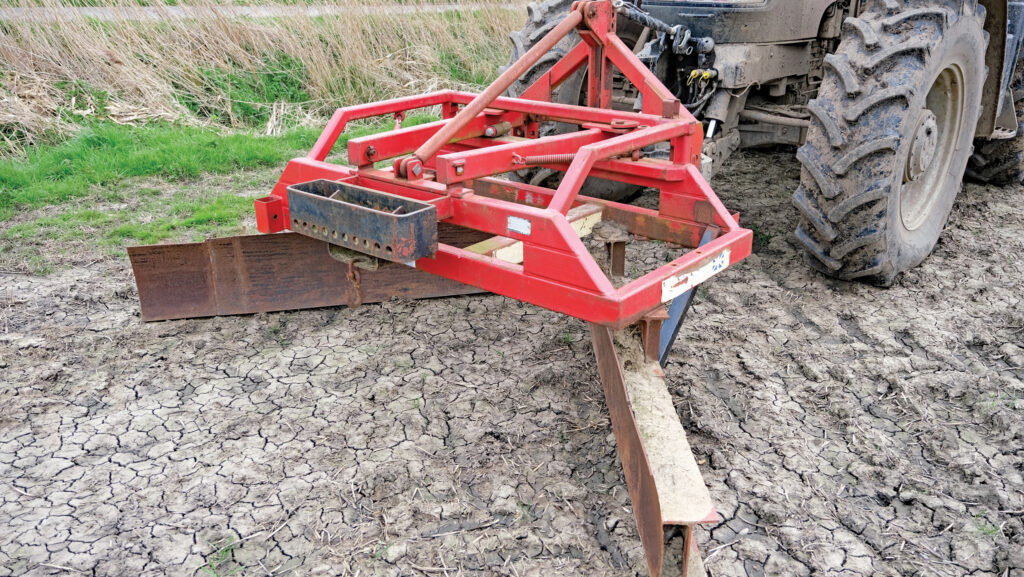
© James Andrews