Keenan mixer wagon renovator offers repair tips
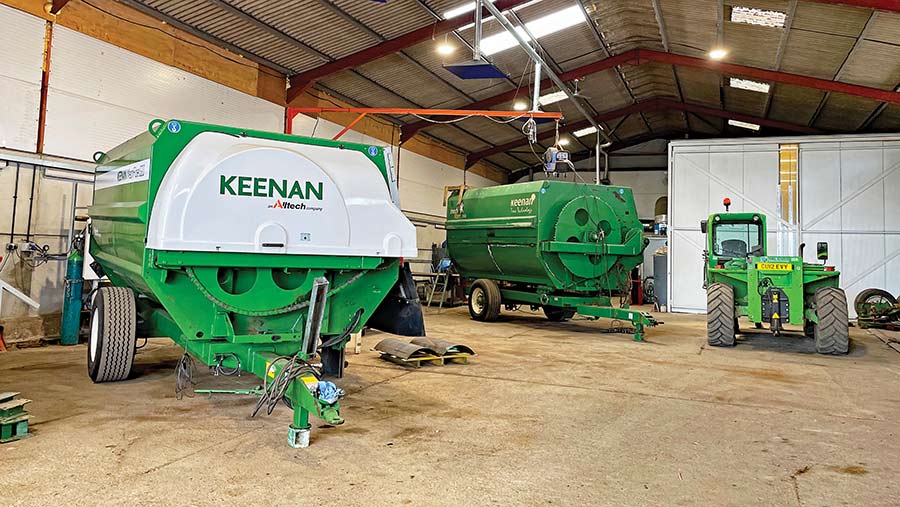
The daily chore of chomping through tonnes of abrasive feedstuffs mean a mixer wagon’s innards only have a limited lifespan.
Added to that, the tight environments in which they work and the fact that buckets are tipped above them every day means the risk of impact damage is substantial.
But even the hardest worked, and slightly wonky, machines can be brought back from the brink with the right know-how.
Gloucestershire-based WJW Engineering has been one of Keenan’s approved refurbishing firms for the past three years, renovating two or three worn wagons a month.
See also: Tips for buying a second-hand tub feeder wagon
Each is subjected to a 60-point inspection upon arrival, with some requiring just a light touch and others getting a complete mechanical overhaul, sandblast and respray.
Regardless of the condition in which they arrive, all leave the workshop functioning like new and looking almost at smart as when they rolled off the production line.
They are then sold on by Keenan as Approved Used wagons, which are priced about 30-40% less than a new equivalent.
Any of the models built in the past 10 years are suitable for conversion, but one of the most common, and sought after, is the MechFiber320.
This runs on a single axle and has a 14cu m capacity, capable of feeding 55-85 cows a load.
In addition to the refurbishment work, WJW Engineering is a Keenan-accredited service agent.
Owner William Walmsley and his five-strong team of engineers offer mobile servicing and repairs covering a 50-mile radius from their base near Cirencester.
However, they travel longer distances for major jobs, such as fitting new liners.
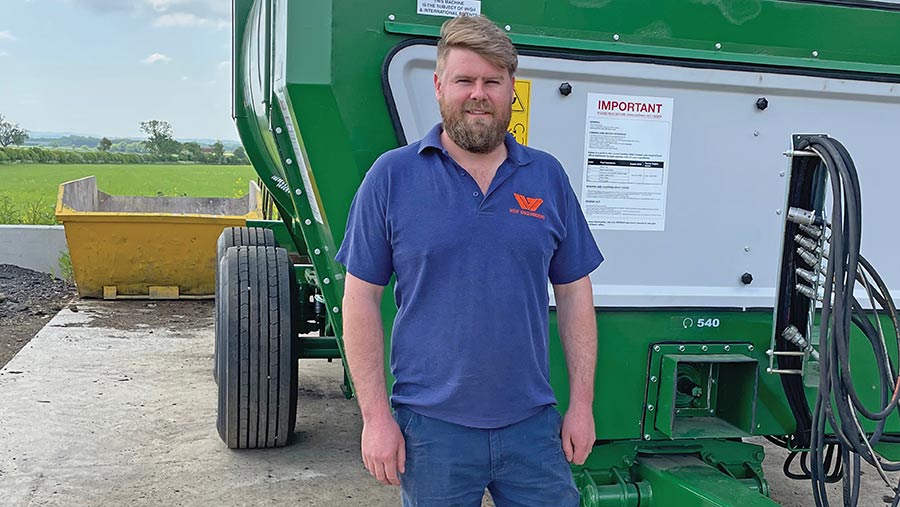
WJW Engineering owner William Walmsley © James Andrews
The team also carries out other on-site machinery welding repairs and bespoke steel fabrication, fits hard-wearing Ferobide tiles to wearing metal, and has a sandblasting and painting service for large equipment.
Here, we look at the work that goes into bringing a used wagon up to Approved Used spec and some of the on-farm repairs the company completes.
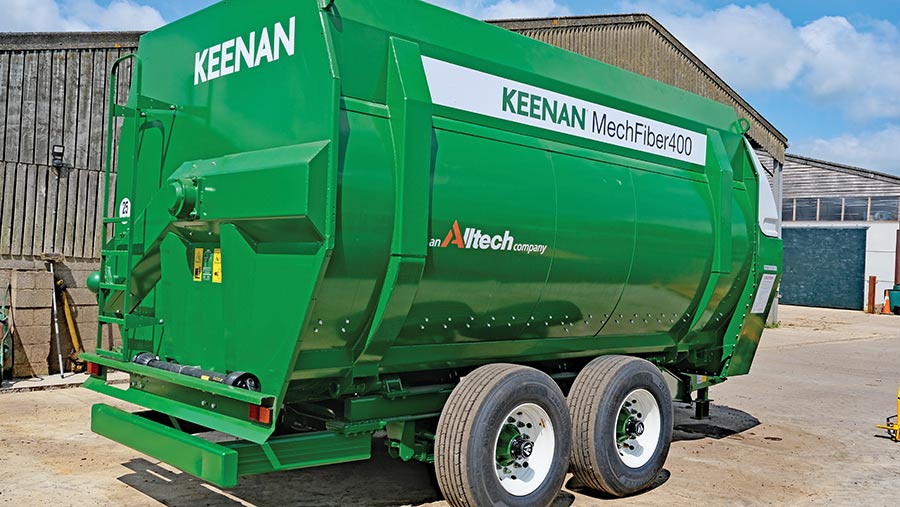
An Approved Used MechFiber400 © James Andrews
Belly liner
The action of paddles mixing abrasive feedstuffs inside the tub will eventually wear the liners through.
For Approved Used models, the firm always welds in a new set of 6mm plates, which reset them back to factory specification.
These are pre-curved to the shape of the tub, but a good bit of skill is required to get them sitting in the correct position.
When liners are fitted in WJW’s workshop the team uses a welder suspended from a gantry crane.
But for on-farm work they have diesel-fuelled welders in their service vans, meaning they are fully self-sufficient.
The heat of welding in the liners tends to burn through the paint on the outside of the machine, which is touched-up afterwards to keep the rust at bay.
This clearly isn’t a problem for Approved Used machines as they are treated to a full shot-blast and respray.
The first time liners are replaced, new plates are welded on top of the originals.
However, when it comes to fitting a second or third set, previous metal often needs to be removed to make sure there’s enough paddle clearance.
Typically, liner replacement takes about a day and the cost for those having the job carried out on farm ranges from about £4,500 to £7,000 depending on the model and condition.
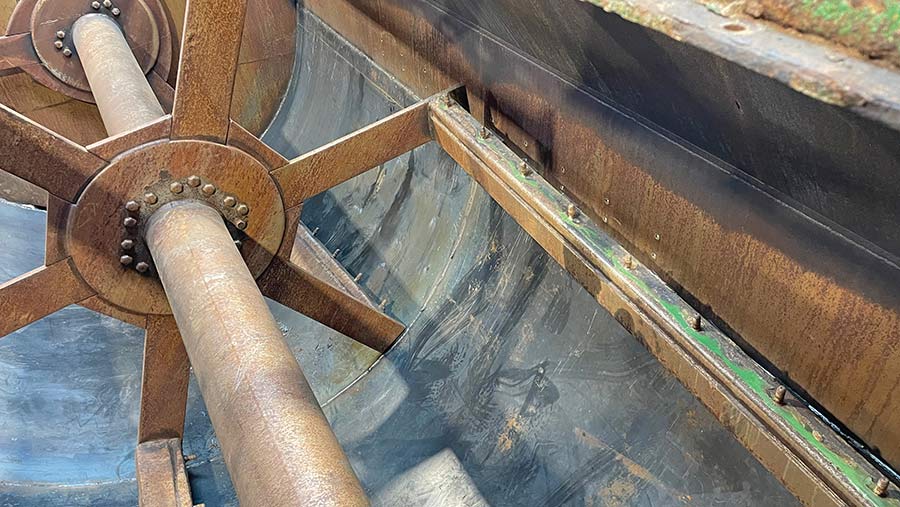
New liners © James Andrews
Auger trough flights and liners
Unloading auger troughs and flights will wear out over time, so many machines going through the workshop will have these replaced.
One method is to pull the auger out of the machine, but WJW can do both jobs with it in-situ.
This is largely down to the fact that the flights come in sections, which can be fed round the tube before being welded in place.
As the auger only turns slowly, there’s no need to have it balanced.
Plating the trough is a similar process to the belly liner, using steel sections that are pre-bent to the correct curvature.
The cost of having new auger flights fitted on farm is about £1,500 to £1,750, and it’s the same again for the liners.
New VFC door seals and retainers are often put on at the same time.
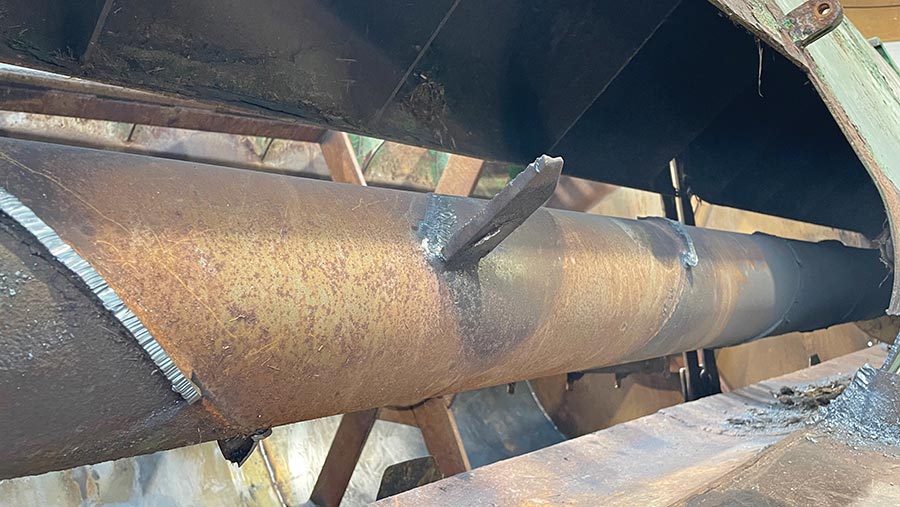
Auger flights being replaced © James Andrews
Knives and rubber paddles
Rubber scrapers on the paddles and the knives mounted in the base of the tub are both crucial for getting a well chopped and incorporated mix.
The paddles also play an important role in efficient unloading of the machine – both are replaced as a matter of course on refurbished models.
Owners of existing machines should factor in changing the rubbers every couple of years, but knife wear is harder to quantify as it varies considerably depending on the workload.
Paddle rubbers cost roughly £350 to £450 a set, and knives are priced from £25.
Refurbished machines are also fitted with a new top knife, which cleans the paddles and helps the mix incorporate more effectively.
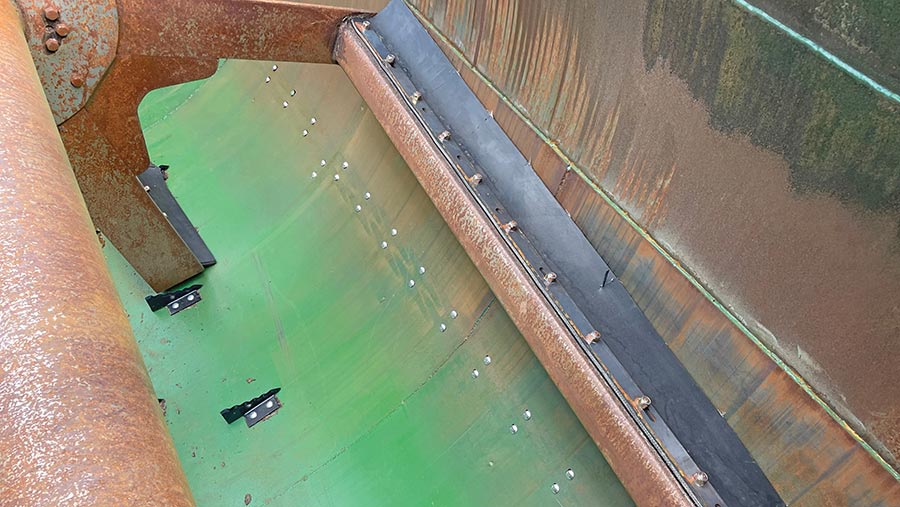
Knives and rubber paddles © James Andrews
Snapped or bent paddles
If any bulky items get dropped into the tub, they can bend or snap the paddles off the machine or maybe even bend the central shaft.
In some cases, this would render it a complete write-off, and examples like this wouldn’t go through the Approved Used refurbishment process.
However, WJW specialises in correcting problems caused by mishaps like this.
Only recently, it rebuilt and reattached a paddle arm on farm after it had been sheared off when an unsecured bucket was accidentally tipped in while it was running.
Sandblasting and repainting
All refurbished machines are sandblasted to bare metal before receiving a full respray in factory-correct colours.
To the casual observer, they look like new, but if you look closely there can be some evidence of pitting in the metal and the machines have “Approved” decals on the side.
The same service is offered to customers with existing machines of any make or model.
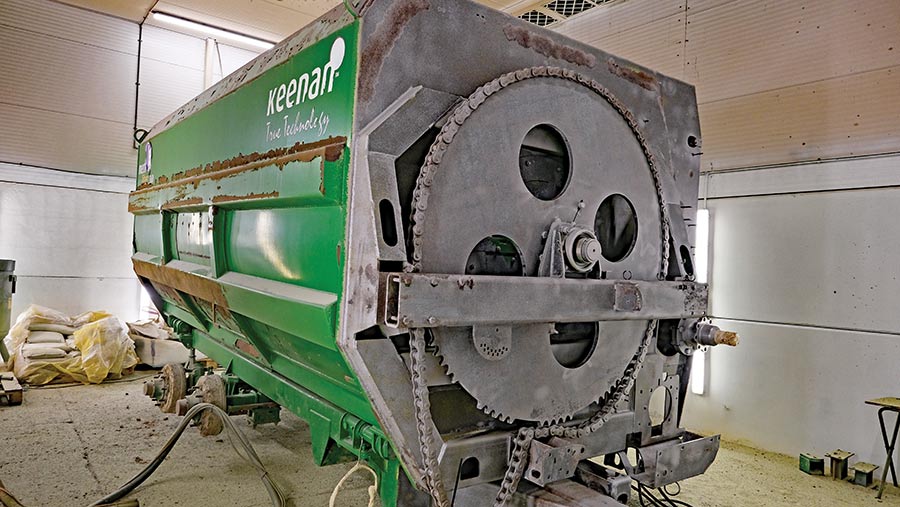
Sandblaster © James Andrews
Control system upgrades
Many machines go out with a reconditioned Stad04 control unit, which carries out basic weighing, mixing and unloading functions.
But, because all units are interchangeable, it’s possible to upgrade to a more sophisticated setup, such as the InTouch.
This syncs data with the Keenan InTouch dashboard so that users can keep accurate records of what is being fed each day, as well as helping them deliver a consistent ration.
It can also be controlled from an app.
Owners of older models running on outdated controllers can also ask WJW Engineering to supply and fit a unit that’s more up to date.
Weigh cells and electrics are generally reliable unless a rat has been nibbling at the wiring.
If there are any signs of trouble in this department, the firm will fit another wiring loom.
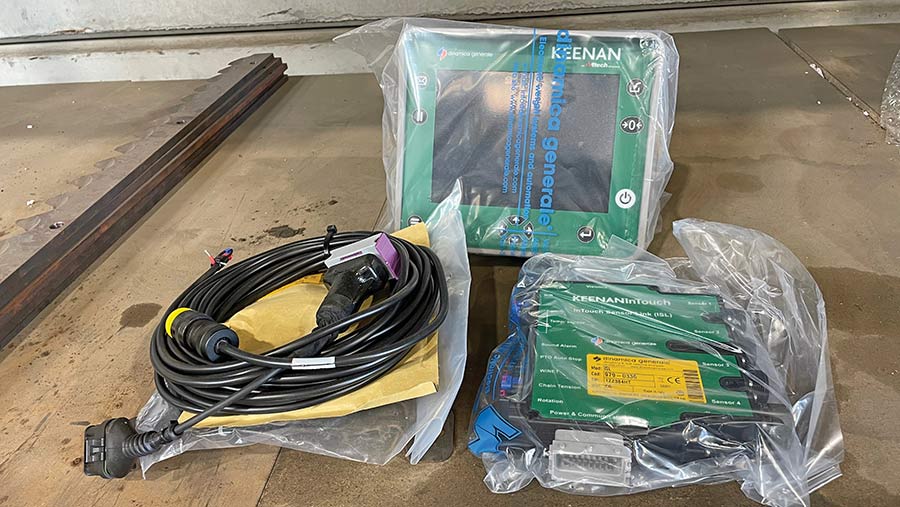
InTouch controller upgrade kit © James Andrews
Spline shaft bearings
As the driveline on the front of a Keenan wagon moves so slowly, it doesn’t wear too badly – particularly on machines with an auto-lube system, or the more sophisticated models that run in a sealed oil bath.
The bearings on the splined pto shaft that accepts drive from the tractor are a common wear point though, particularly if they haven’t been given a regular shot of grease.
They’re replaced as a matter of course on Approved Used examples, but, for owners, they just need to be regularly greased and checked for play periodically.
This is easy to do by rattling the shaft to see if there is excessive movement.
Bearings for the main rotor and unloading auger tend to last pretty well, so they are not replaced unless showing signs of wear.
However, the main drive chain is generally renewed.
Finishing touches
To round off an Approved Used refurbishment, WJW fits fresh tyres, a new pto and, if damaged, a replacement front panel to guard the driveline.
All hydraulic pipes are renewed, too, and they get a complete set of door seals to prevent the ration dribbling out during mixing.
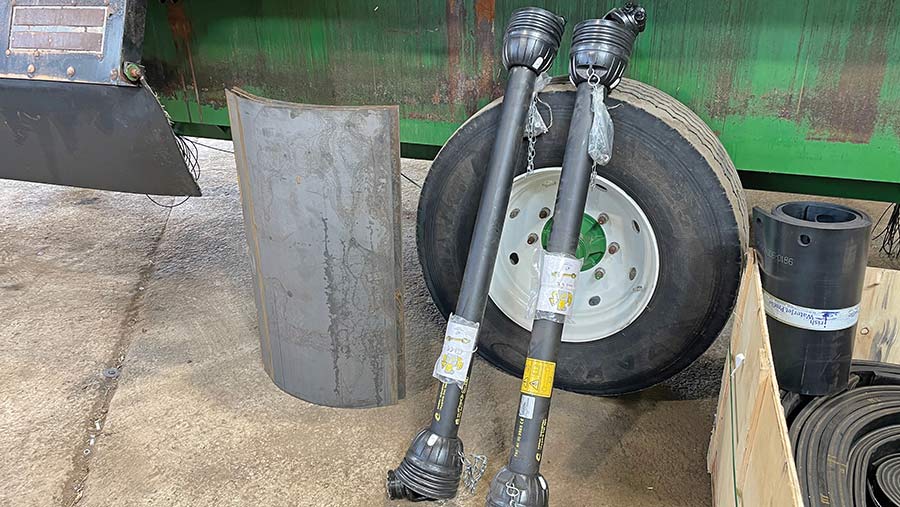
New parts © James Andrews