20-year-old John Deere telehandler gets perfect £20k refurb
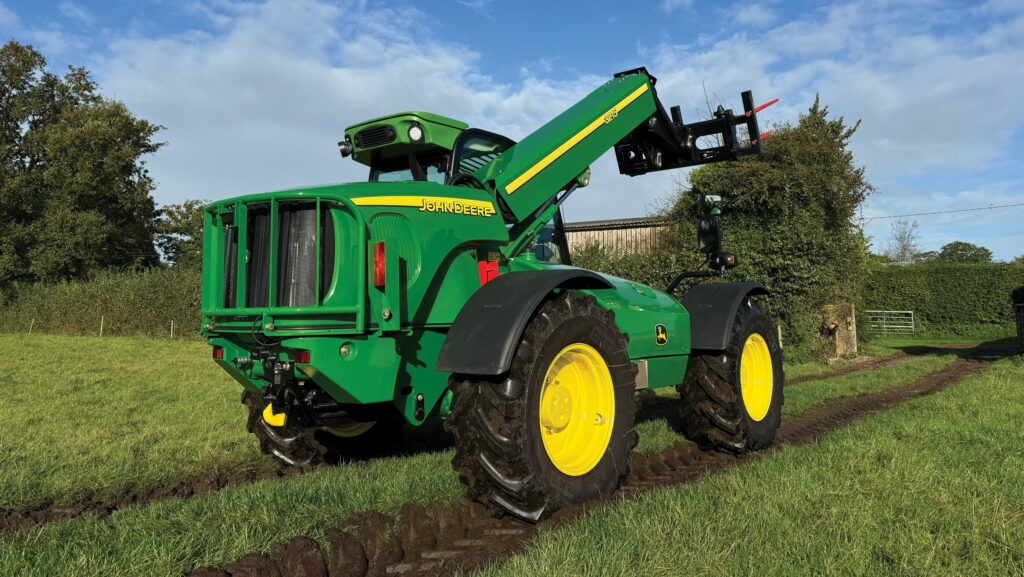
It’s boom time for noughties farm machinery, with demand surging for mechanically sound workhorses devoid of the electronic and emissions-related aggravations of their successors.
While John Deere, Case IH and New Holland tractors that emanated from those halcyon days continue to command almost-new prices, so, increasingly, are any telehandlers that can be found in decent nick.
Provided they haven’t suffered dog’s abuse, they’ll have the power, lift capacity and reach to match a modern machine. And, given most go without the creature comforts of a tractor, their cabs should be almost as good, too.
See also: 22-year-old Fendt Favorit 515C gets £15k revamp
John Deere handlers remain some of the most sought-after from this era, retaining a cult following despite being unceremoniously culled after a brief six-year production run that ended when the company switched its focus to guidance technology.
Among their admirers is Devon-based engineer Marcus Tucker.
After successfully tracking down a 54-plate 3215 two-and-a-half years ago, he embarked on a major renovation project to return it to showroom condition.
“I first drove a Deere handler when I was milking on a local dairy farm, and I’ve always liked them – the cabs are nice, the powertrain is reliable and, most appealingly, there’s no AdBlue system to worry about, which makes them easy to work on,” he says.
“I wanted the 3215 because it was the smallest and most basic model.
“The fancier 20-series had boom suspension, an electronic joystick, and a weighing system, but they are all potentially troublesome extras I was happy to go without.”
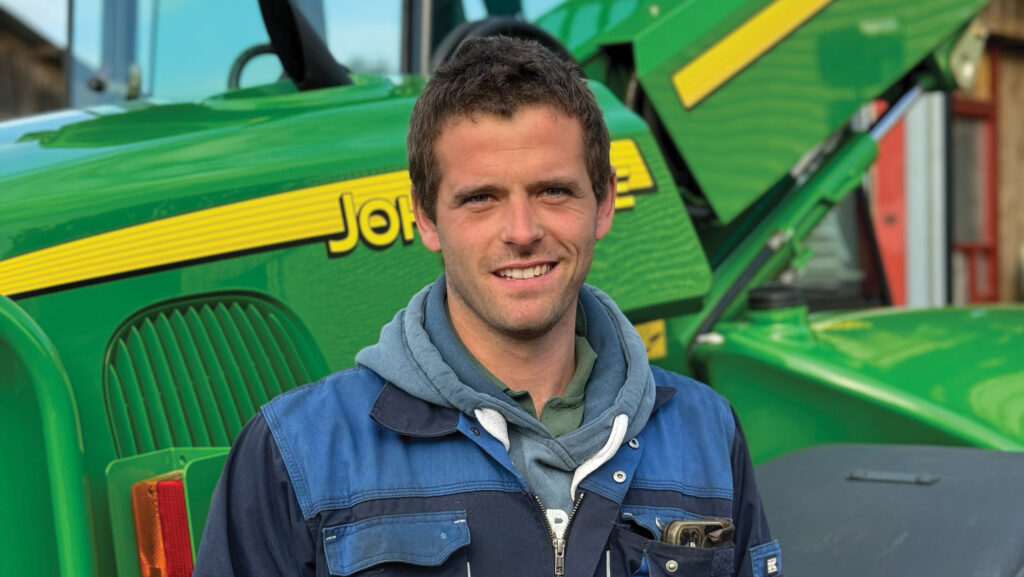
Marcus Tucker © MAG/Oliver Mark
The renovation
At £25,000, the 2004-built 3215 certainly wasn’t cheap. But with only 4,000 hours on the clock and a powertrain in good working order, it meant Marcus could focus on aesthetics rather than mechanicals.
“I’d been looking for years, and this one seemed pretty solid,” he says.
“My original plan was just to tidy it up, but I’m a sucker for detail and it morphed into a far bigger renovation.”
He spent another £20,000 on metal and parts for the refurbishment – a total that would have risen to more than £60,000 should he have factored in his 1,500 hours of labour.
“Nothing is cheap – particularly when you’re using genuine parts. The only exceptions were the OEM-sourced spares and the bolts, headstock pins, sheet panel covers and mudguard brackets that I made myself.”
Though it was a pricey job, he’s already had two offers north of £60,000 – demonstrating the demand for decent, second-hand machinery.
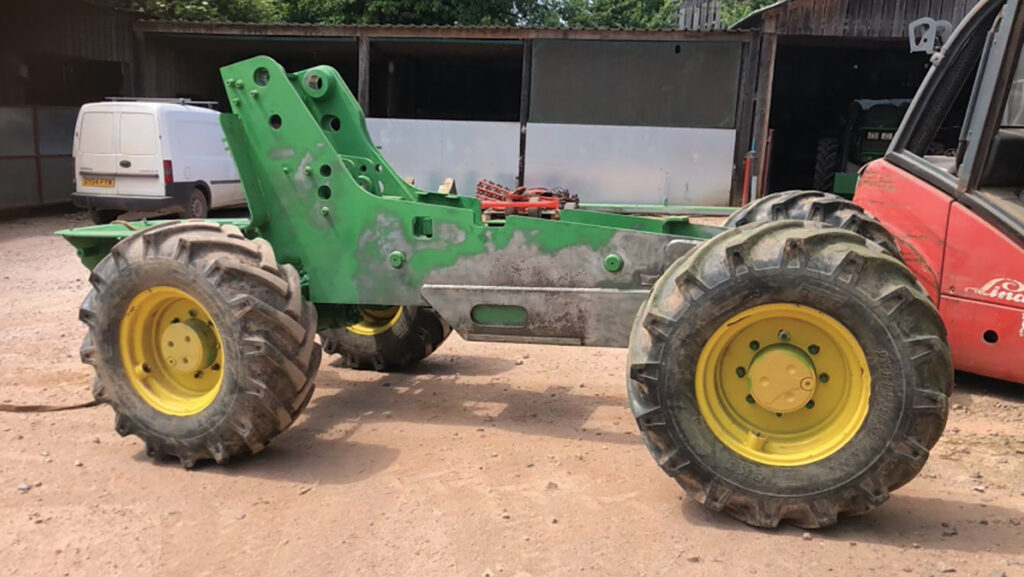
© Marcus Tucker
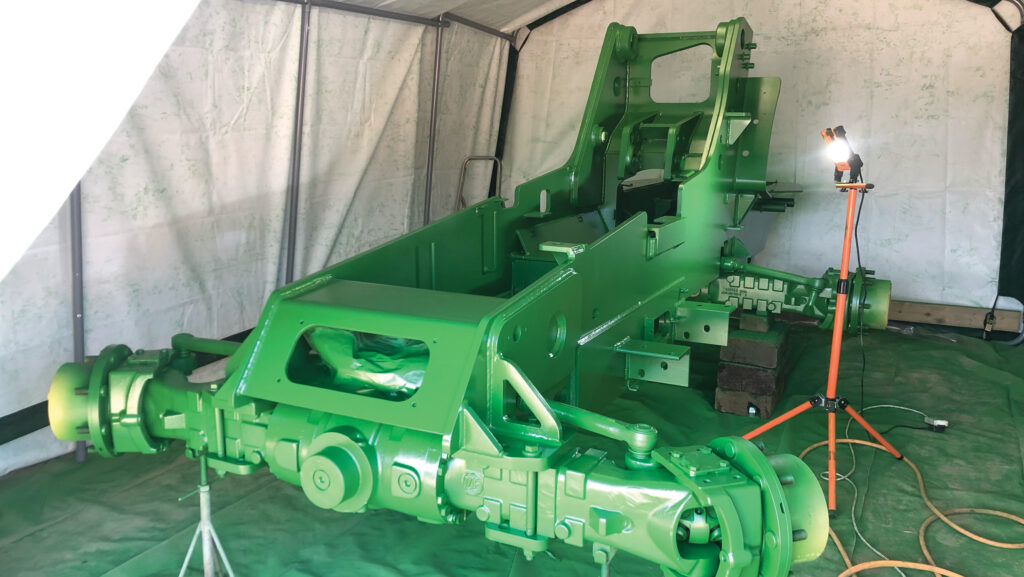
© Marcus Tucker
Chassis strip-down
Almost a year after the 3215 arrived, work starts by whipping off the boom, wheels, axles and engine.
What remains is a naked chassis, which is painstakingly attacked with a needle gun and given a thorough rub down to remove any loose paint and rusty metal.
This prep work takes some 150 hours and is quickly followed by a lick of Deere-green primer to ensure any subsequent chips in the topcoat don’t show through.
The cab is also stripped back to the bare frame and sent away for professional shot blasting and powder coating. It’s a relative bargain, at £150.
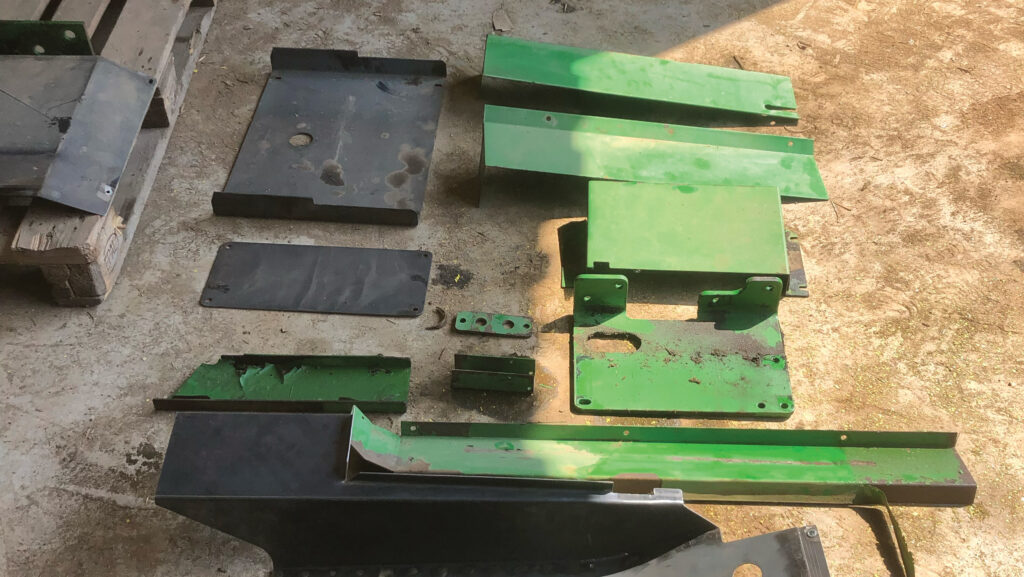
© Marcus Tucker
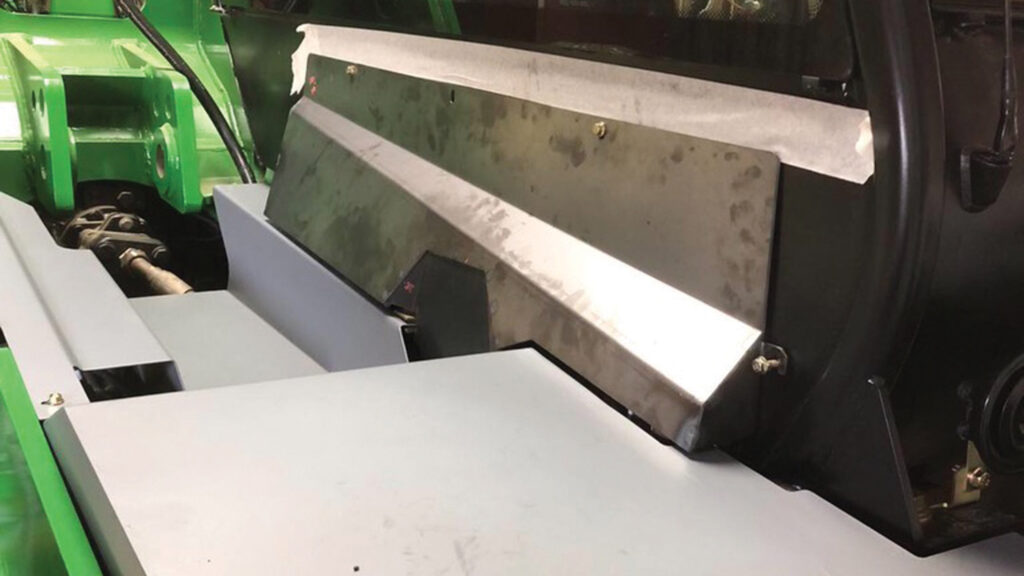
© Marcus Tucker
Replacing guards and covers
The sheet metal panels that cover the trough, boom side and chassis front are still intact, but warped and pitted.
After efforts to sandblast and repaint the originals fail to meet Marcus’s strict quality control, Marcus decides to start afresh.
Using the old ones as templates, he cuts, folds and, later, paints 2mm sheet to make his own. This is marginally thicker than the previous 1.6mm gauge to add extra rigidity.
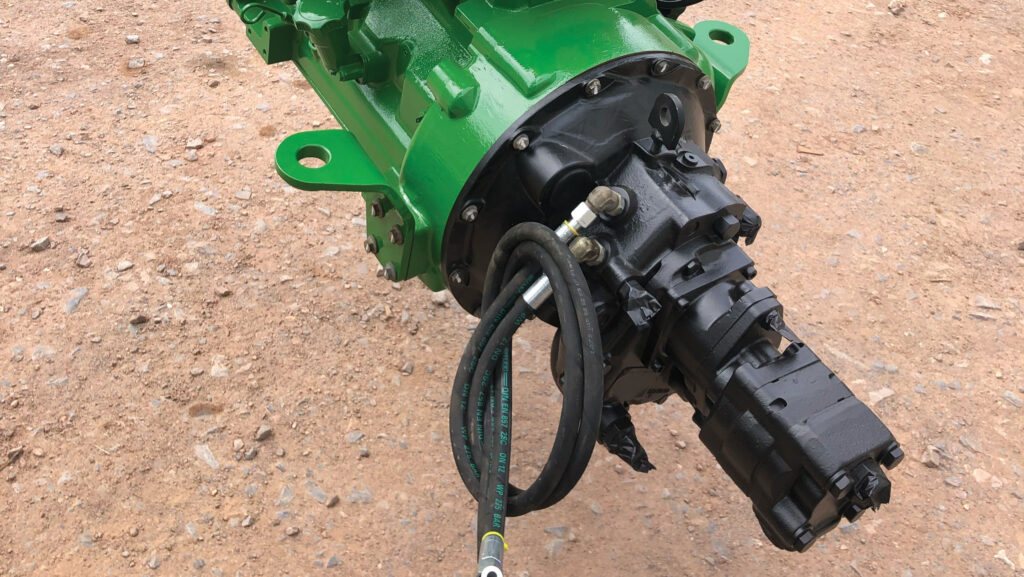
© Marcus Tucker
Engine respray
Both the 100hp John Deere engine – also found in a 6420 tractor – and ZF manual four-speed transmission are mechanically sound, so no remedial work is required.
But, with the block hoicked out, he decides to replace the transmission pump, as this is the sole weak spot in an otherwise bombproof drivetrain.
The tedious and knuckle-skinning task of rubbing down the engine begins. It is then resprayed, along with the auxiliary components, transmission pump and torque convertor housing. The job is done in-house using a pop-up Clarke paint booth (£180).
He also decides to fit an air-conditioning system, sourced from second-hand specialist Nick Young Tractor Parts (£1,000). A further £750 goes on a new condenser unit.
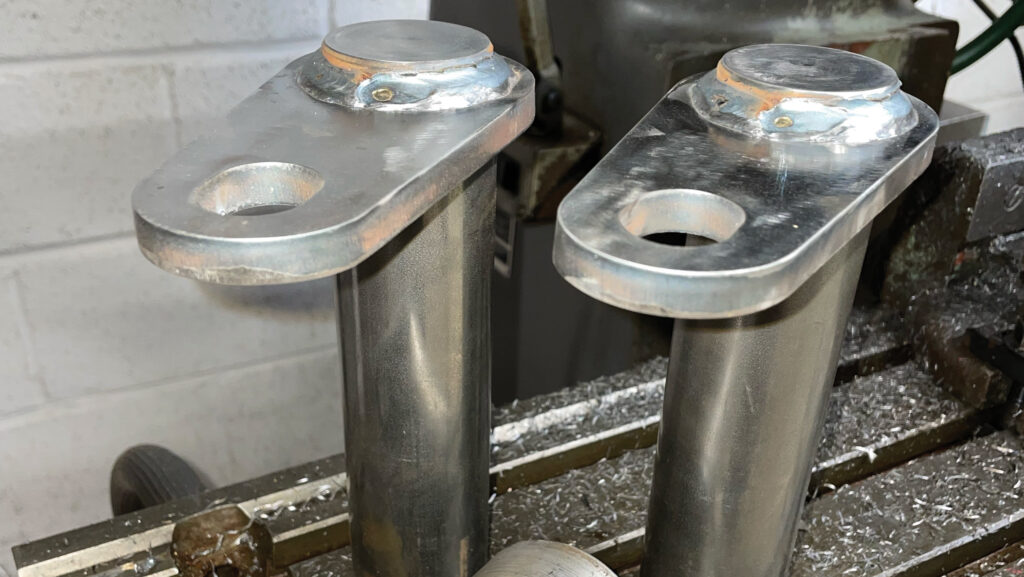
© Marcus Tucker
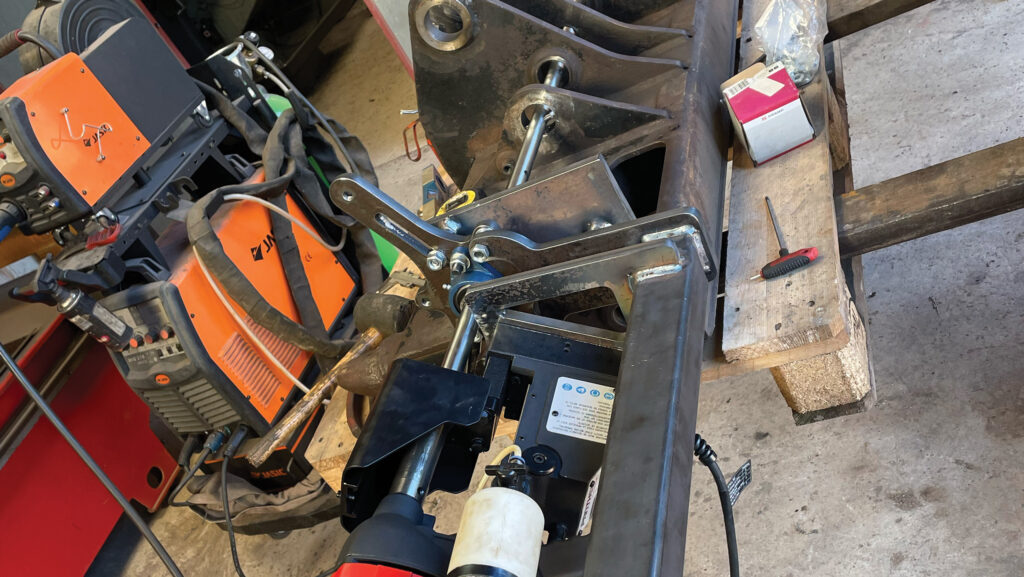
© Marcus Tucker
Bits, bobs and bolts
As well as air-con, Marcus adds a twin mirror with wide-angle section (£200, new from Nick Young), an upgraded lighting package with an extra two units on the front of the cab (£690), and a pair of rear cameras (£325) – one for reversing and another for the pick-up hitch.
The hitch itself – a Dromone – is in decent fettle, except for a bent guide tab that is quickly straightened up.
All the handler’s bolts, plus the lengths of solid hydraulic pipes, are sent for re-plating – a process that involves dipping them in acid before electroplating them with a protective layer of zinc – ready for reassembly. In all, this costs (£1,100).
He also line bores the headstock pins to make sure they’re bang on.
The price for a line borer, at £25,000, is too rich, so he makes his own. A mag drill acts as the power source and he machines a boring bar to fit a small 12mm indexable lathe tool, which works a treat.
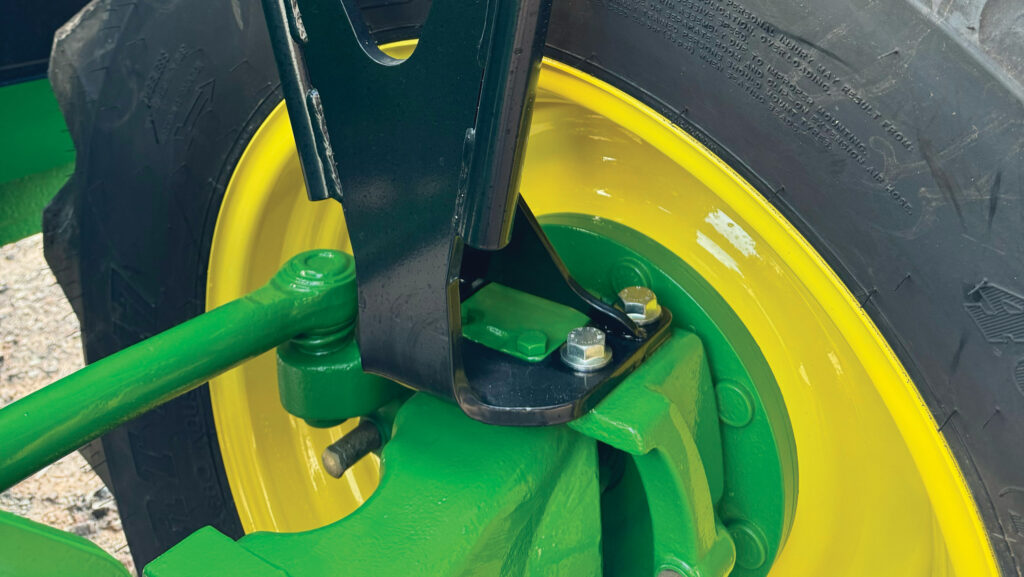
© MAG/Oliver Mark
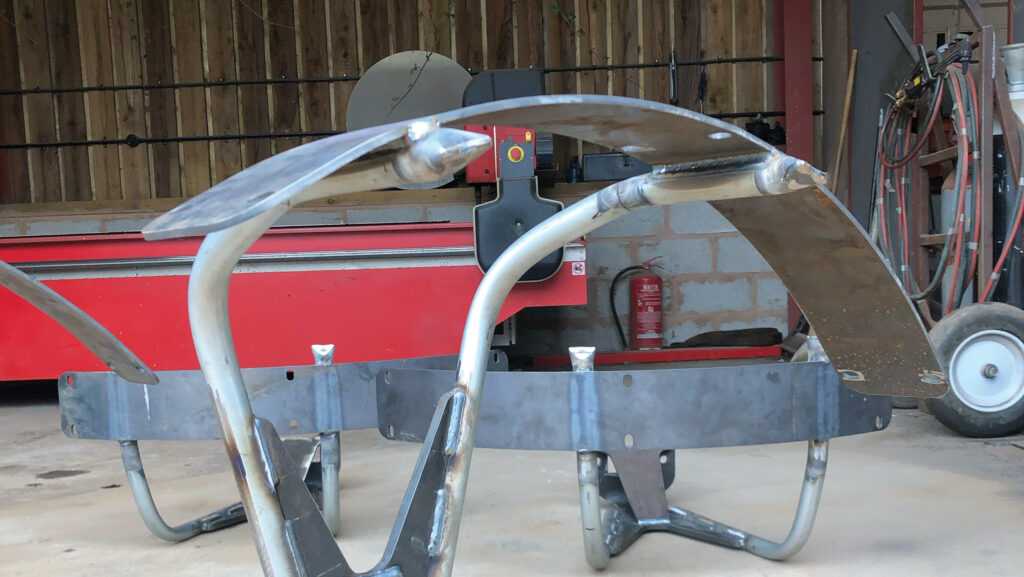
© Marcus Tucker
Wheel change
After deciding that the machine’s original 20in rims looked odd, Marcus tracks down a pair of 24-inchers from Nick Young.
These are a relative snip at £150. But after getting bored searching for another couple, he bites the bullet and forks out for new ones from local Deere dealer Smallridge Brothers (£750).
The used wheels are shotblasted, primed with a zinc powder-coat, and given a two-pack primer and topcoat.
The new ones also get a colour-matching respray, and all four are fitted with BKT 460/70 R24s (£1,680).
This wheel upgrade necessitates new mudguard skins (£240 Dunlops supplied by Kramp) and fender brackets.
Stunned by an £850/bracket quote for a genuine set, he does what any self-respecting engineer would do and fabricates his own.
And Marcus is back in his workshop again soon after, because a set of suitably sized ball joint boots are no longer available.
Deere’s solution? A complete new set of track rods (£4,128). Marcus’s? Skim 2mm off the shoulder of the track rod and fit a set of boots he has on the shelf.
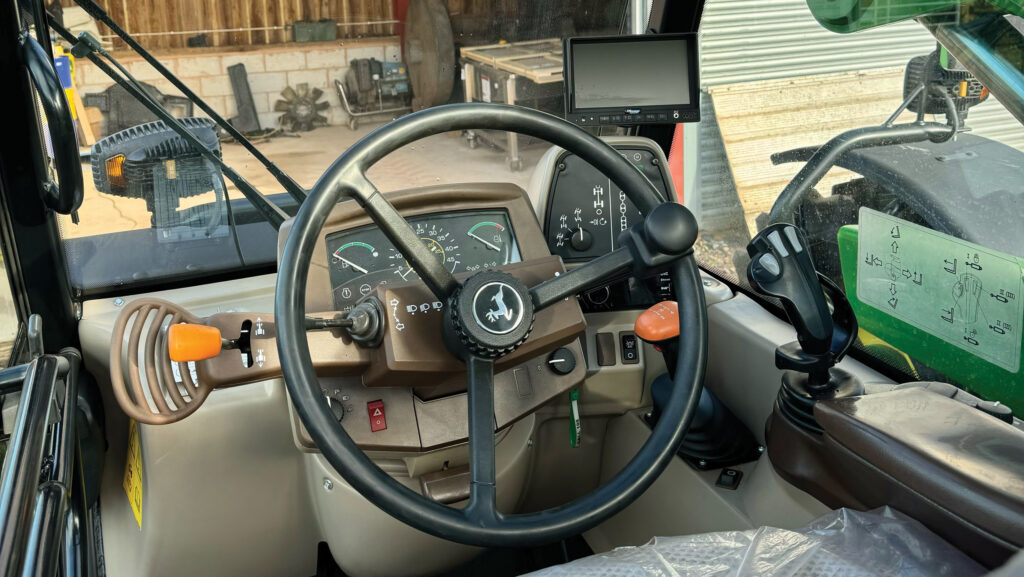
© MAG/Oliver Mark
Cab
The headlining is black with mould and the plastics rank, but both are remedied with a steam clean from a local valeting business (£30).
It polishes up well – except for the seat. A replacement Grammer unit is sourced (£850), and a new front windscreen goes in as the old one is suffering from slight delamination.
The 5in-long indicator stalk is rusty too, but the quote for a replacement comes in at a staggering £750. Reluctantly, a crude polish and paint will have to do.
Once back together, the temperature gauge on the dash starts dishing up iffy readings, so it’s packed off to David King Electronics to be sorted (£120).
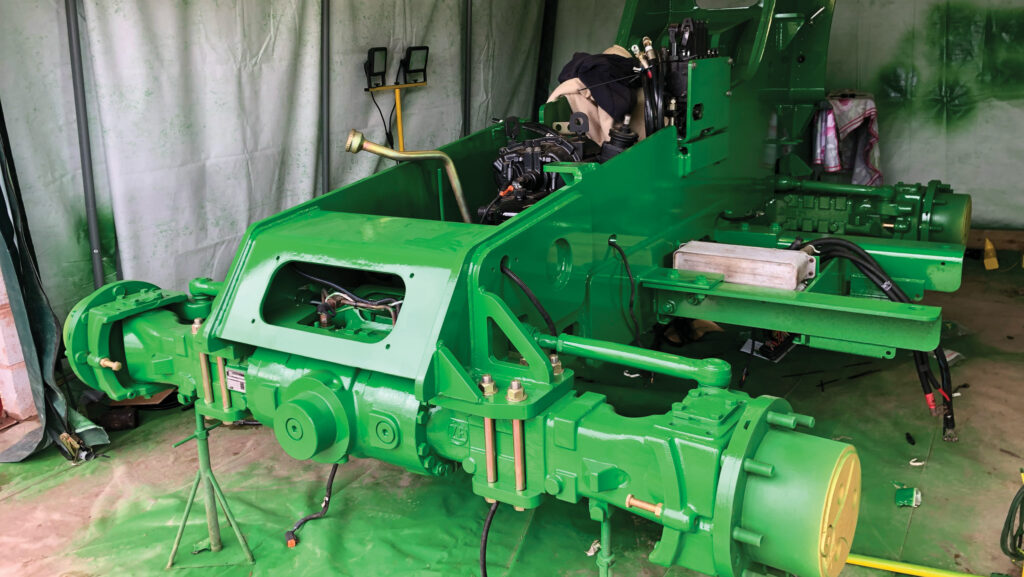
© Marcus Tucker
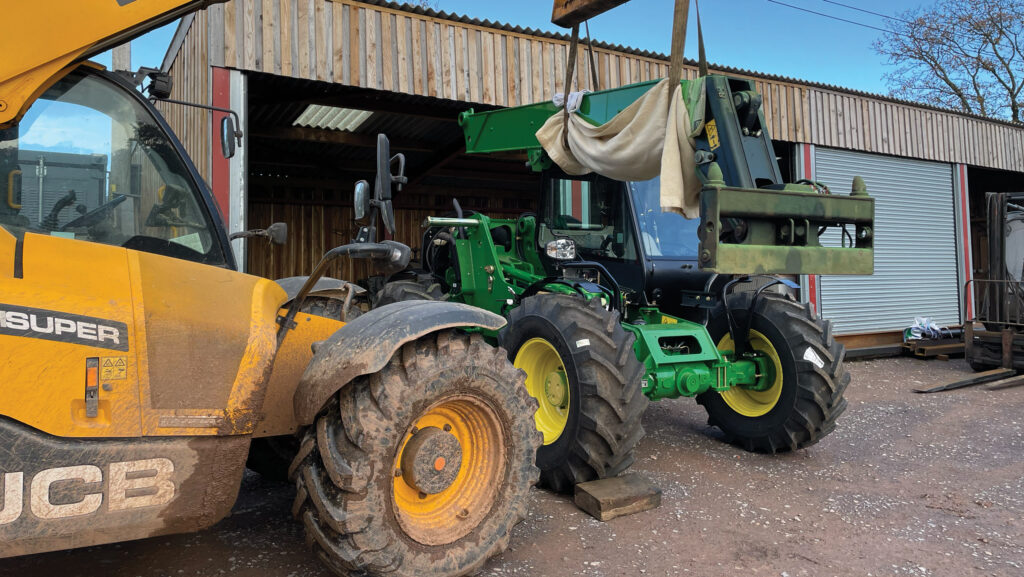
© Marcus Tucker
Putting it back together
Reassembly starts with a spray of the axles and the sections of the chassis to which they mount. Once these are bolted in place, the whole lot gets another coat.
The cab goes on next, followed by the delicate job of lowering the boom into place.
He goes shopping for new decals and aluminium data plates. Some are obsolete, so they are remade by Lotus Designs (£65).
The last task is to replace the missing rear engine guard that protects the grille and fibreglass bonnet.
Nick Young saves the day with a beaten-up second-hand version; the most badly bent steel bars are replaced, the rest straightened up, and a coat of paint has it looking like new.
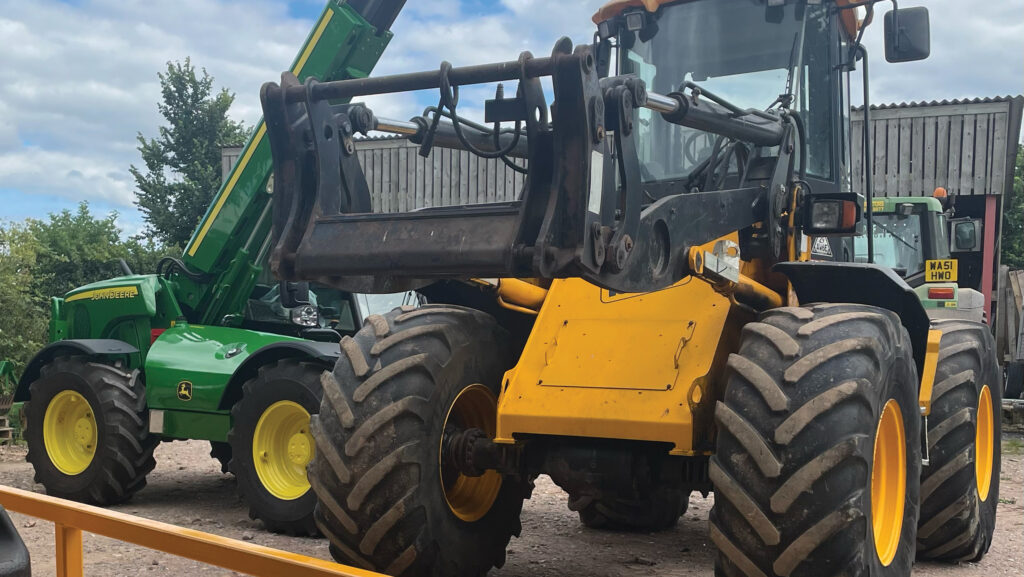
© Marcus Tucker
Upcoming project
Next to get the Tucker treatment is a fire-damaged JCB 416S loading shovel sourced from salvage specialist Adam Hewitt.
A potential bargain at £8,500, it has so far cost the same again to get it running ready for buckraking before Marcus addresses the aesthetics.
And this could be the first of many.
“There’s a massive market for old-school, pre-AdBlue machines that are mechanically sound,” he says.
“Admittedly, I went to town on the 3215 but, even factoring in my labour, the total cost for a customer might be £75,000, versus £120,000 for a new JCB.”
With that in mind, he reckons demand for revitalised telehandlers may even be stronger than that of tractors.
“Telehandlers are more forgiving than tractors – the cabs don’t change much over the years, there are fewer rust-prone spots, and the metal is generally heavier duty with fewer thin panels.”
However, ramping up the business will rely on sorting the current bottlenecks – sandblasting and painting – to reduce the turnaround time to about four months.
Marcus has already invested in an industrial-spec sandblaster that should cut the 150 hours of chassis prep time down to nearer three hours.
“Preparation is key. The surface must be smooth, so getting a good finish starts long before the final spray and involves hundreds of hours of work.
“It’s easy to get bored with this work, but it’s the difference between a good job and an average one.”
A proper spray booth is set to come next, with second-hand options available for about £10,000.
This will allow him to complete all surface preparation and painting in-house and, crucially, in all conditions.
MT Engineering
Marcus Tucker’s MT Engineering business will make or repair pretty much anything made of metal.
Examples of his work include bespoke fabrication projects that range from telehandler headstocks to staircases, as well as machining of pins, shafts and gears, and refurbs of tired equipment.
He also produces replacement belly plates for feeder wagons using an 11t roller set.
His latest acquisition is a Butler slotting machine, which allows him to cut internal keyways and splines, and external gear teeth.
John Deere 3215 (2004)
- Engine 4.5-litre, four-cylinder John Deere
- Power 100hp
- Transmission Manual four-speed torque convertor
- Lift capacity 2.8t
- Max height 5.62m
John Deere telehandlers
John Deere’s dalliance with the telehandler market was brief but successful.
Having secured a marketing agreement in 1995 to sell Matbro machines in green livery, it then acquired the brand from its financially stricken owner, Powerscreen International.
A six-year production run followed, starting with the first of its in-house-built 3000-series at the turn of the millennium.
Initially there were two models – the 3200 and 3400 – but later came the 3215, 3415, 3220 and 3420.
As well as adding its own engine and cab, Deere redesigned the frame, boom, transmission and hydraulic system, and fitted a plush interior that is still pretty respectable by modern standards.
The handlers were built at John Deere’s factory in Zweibrucken, Germany, until a global market assessment concluded that demand wasn’t strong enough.
Production ceased in 2006, and the plant reverted to manufacturing combines and forage harvesters.