Borders farmer takes drainage in-house with DIY tile plough
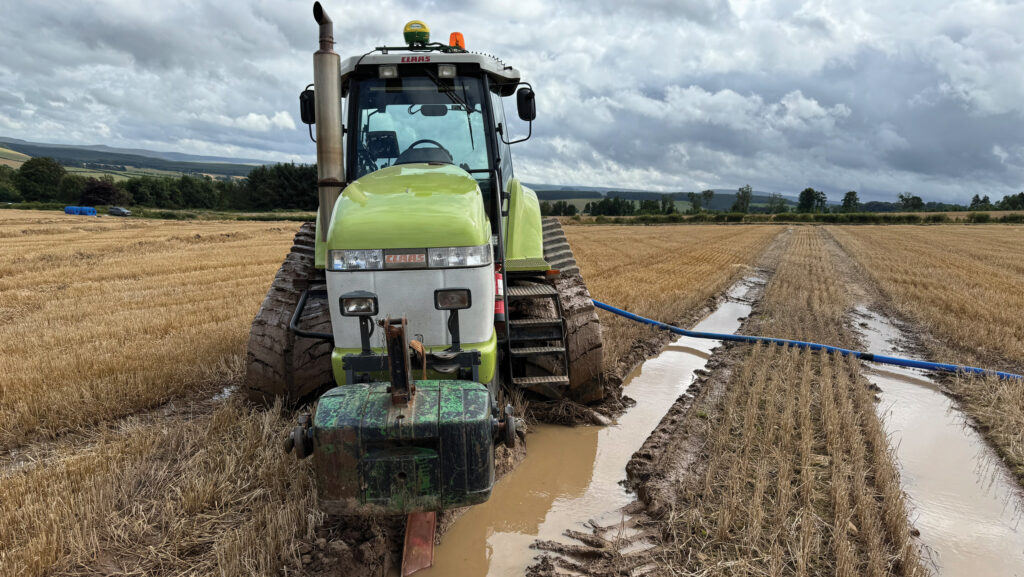
Chain trenchers, drain jetters and mole ploughs are quickly becoming the must-have accessories for arable farms contending with unrelenting rainfall events.
But several UK growers intent on keeping their drainage work in-house have opted for a relatively new means of whisking away the drink from sodden fields.
Patrick Fraser is one of three farmers in southern Scotland to invest in a tile plough from Indiana outfit Soil-Max.
See also: Why Cambs arable farm invested in its own tractor-mounted trencher
Having stumped up nearly £35,000 for the hardware and accompanying technology, he is now geared up for a DIY job on his 350ha of predominantly sandy loam arable land near Jedburgh in the Scottish Borders.
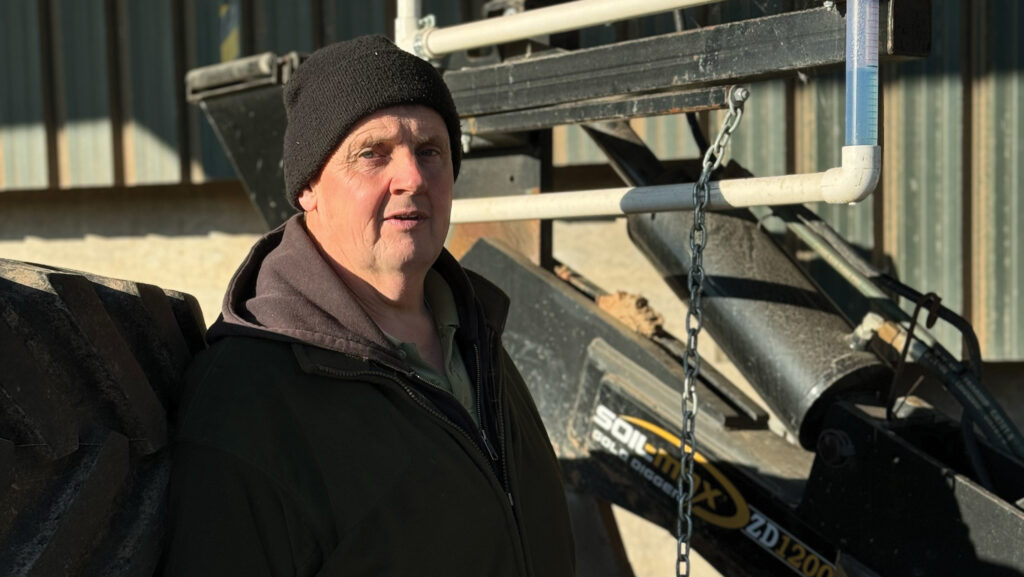
Patrick Fraser © MAG/Oliver Mark
“We have a hotchpotch of old clay tiles and stone drains, few of which are mapped,” says Patrick.
“Most of them are still working to some degree, but they are gradually deteriorating and we’ve had an increasing number of blow-outs caused by stones, roots and blockages.”
Though the tiles can be fixed relatively easily, either by rodding or replacing them, the stone drains are also gradually silting up and proving more of a problem.
As a result, Patrick has been battling perennial field ponds that have harmed yields and interfered with cultivation and drilling.
Last year’s oilseed rape crop took more than a metre of water through the growing season – well over the farm’s 500-600mm average – and, with conditions still testing, only half next summer’s rapeseed made it into the ground.
“It’s increasingly hard to manage the water we’re getting and there’s no magic wand to fix it – it’s all about marginal gains,” he says.
“And drainage is the one thing we can control.”
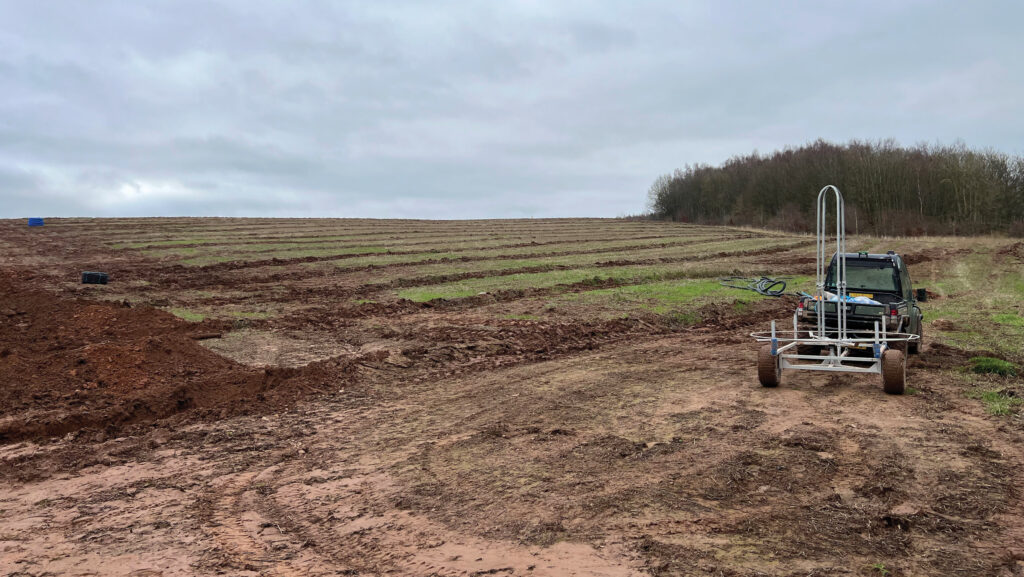
© Patrick Fraser
Sizing up the options
Patrick first attempted to improve the ancient tile and trench systems in 1996, enlisting a contractor to redrain some 15ha following a ruck of burst pipes.
Another two fields were dealt with 15 years ago.
However, he’s been priced out of repeating those exercises, primarily because of the exorbitant cost of gravel to back-fill over the pipe.
“We aren’t blessed with the geology that would give us a natural stone source on the farm, so we’d have to buy gravel in,” he says.
“Even by spacing the lateral runs at 20m, we’d need 125t/ha of stone.
“At current prices, that’s nearly £2,500/ha, which is incredibly hard to justify.”
And, reluctant to shell out the same again for a drainage contractor, he decided to take the task on himself – and abandon gravel back-fill entirely.
The obvious move would have been either to buy or hire a chain trencher, but he was put off by its potentially slow work rate, particularly when contending with the heavy rocks that lie below the surface.
Instead, he opted for Soil-Max’s tile plough.
“The options were either to accept that the whole thing was too expensive and do nothing, or find a means of making it work,” he says.
“The Soil-Max was reasonably priced, and I hoped that by that by doubling the number of lateral runs [setting them at 10m spacings], it would still be effective without back-filling, particularly as we’ve no shortage of fall here.”
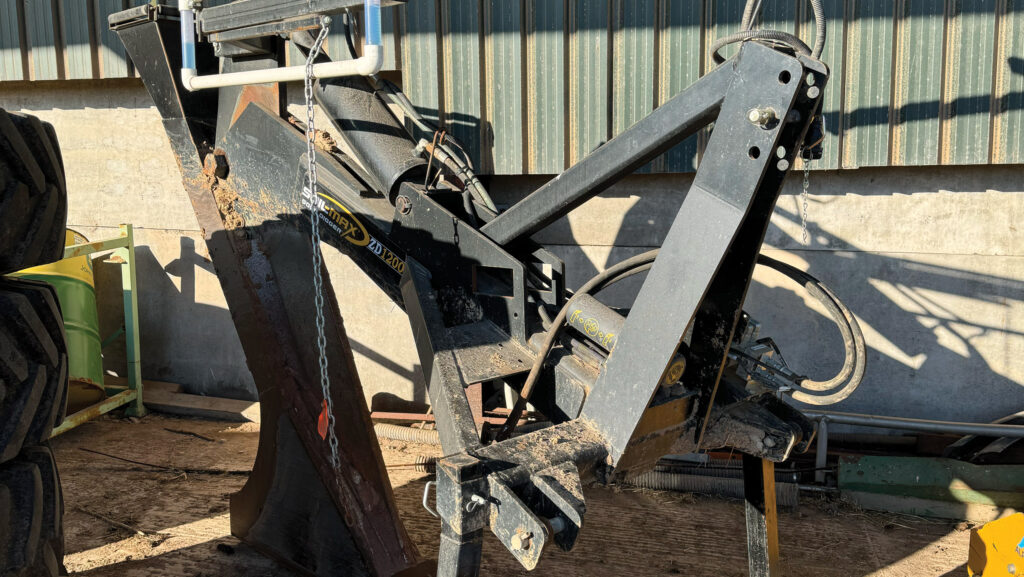
© MAG/Oliver Mark
Soil-Max Gold Digger ZD1200
He settled on the firm’s smallest model, the ZD1200, after seeing it in action at another Borders farm.
As the name suggests, the 1200 will work to a maximum depth of 1.2m – well beyond Patrick’s 75-85cm target range – and lay pipe with a maximum bore of 4in.
As it’s a so-called “pitch plough”, it uses a big hydraulic ram above the main beam to alter the angle – and thus depth – of the shank with millimetre precision, leaving the tractor’s three-point linkage in a set position.
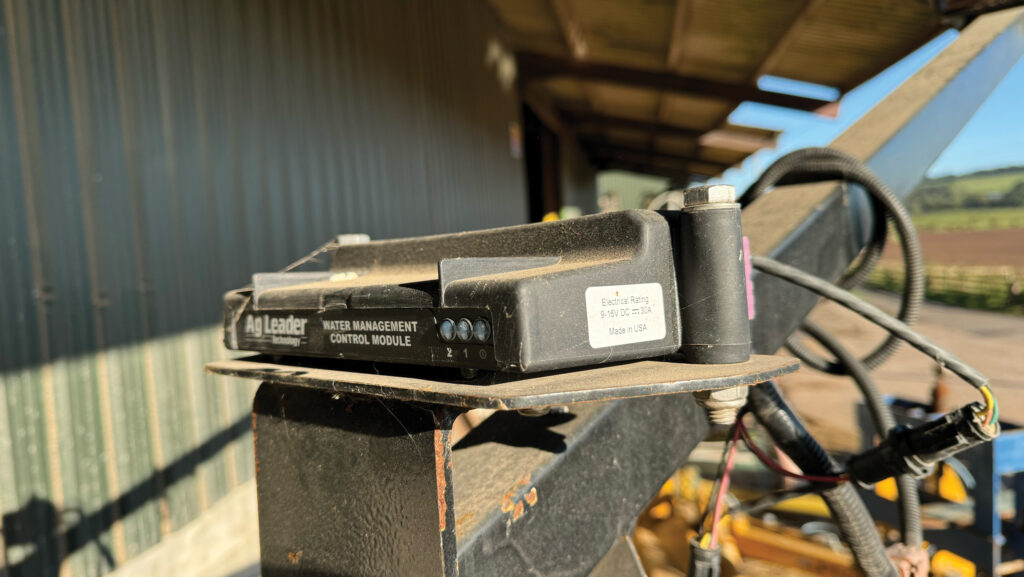
© MAG/Oliver Mark
Grade tweaks are automatic, thanks to a GPS receiver on the plough that monitors altitude changes and feeds this information to an Ag Leader controller linked to a proportional hydraulic valve.
A trapezoidal point carves a flat trough below, with polycarbonate wings holding the channel open as the pipe is laid.
As the outlet for this lies directly below the shank pivot, movement is minimal and the risk of kinks and pinches all but eliminated.
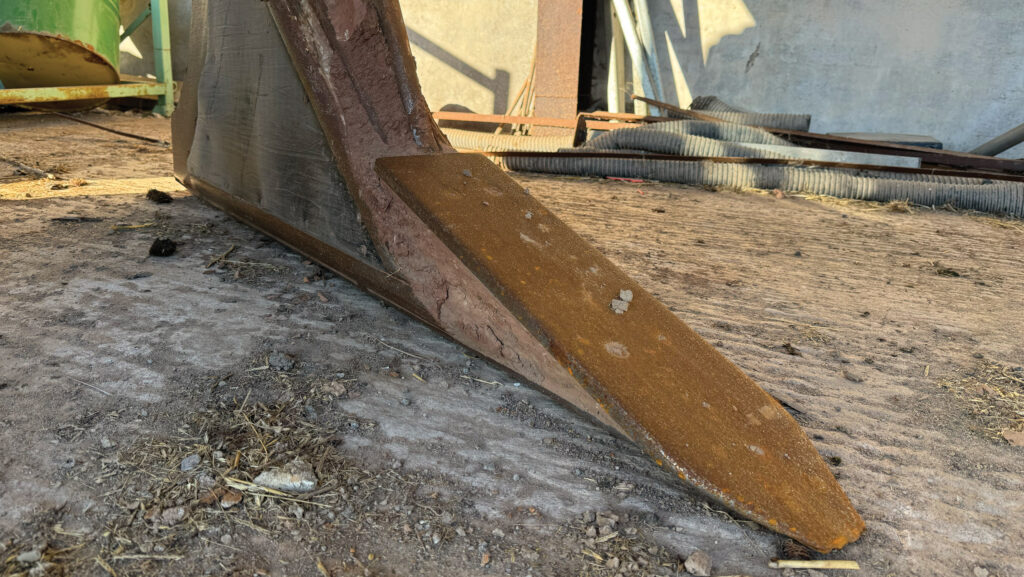
© MAG/Oliver Mark
The total £35,000 bill included an Ag Leader Integra in-cab screen and the aforementioned control module.
Fortunately, Patrick already owned the three receivers required for the plough, tractor and base station.
“A big chunk of the cost is in the electronics – that’s what gives you the confidence that you’re doing it right,” he says.
“And it’s still a relatively cheap means of doing the job.”
The 4in pipe comes in at 88p/m on 450m rolls so, at 1,000m/ha, it costs roughly £1,000/ha, including all the junctions.
Beyond that, there’s just wearing metal and diesel to factor in.
After welding Ferobide onto the tip, the last point managed 16ha – replacements are priced at about £380 – while the tractor burns roughly 40 litres/ha.
Setup
With three Starfire receivers to get singing in harmony, initial setup can be a convoluted affair.
“As we’re working to such fine tolerances, an accurate RTK signal is essential.
“We found a mobile network wasn’t reliable enough – it needs a radio signal from a base station,” says Patrick.
As well as guiding the tractor’s sideway movements, the receivers are constantly recording the altitude – data that is crunched by the Ag Leader “water management control module” on the plough.
This allows the system to lay the tile autonomously, constantly tweaking the pitch by a few millimetres to maintain the desired fall.
To do so, operators must first complete a “survey” pass along the intended A-B line with the plough in the air, starting at the highest point and ending where the lateral is to join the main drainage pipe.
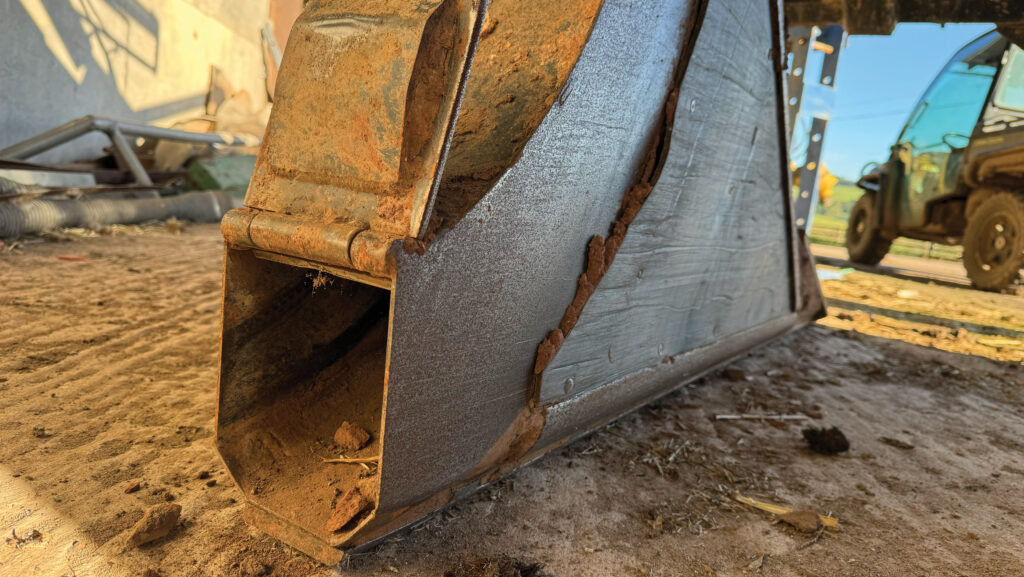
© MAG/Oliver Mark
During this, the GPS system records changes in height to determine whether there’s adequate fall within the operator’s pre-set depth range.
If there’s not, both depth and fall thresholds can be altered until the plan is deemed workable – at which point the installation can begin.
Three-person job
The task of laying the tile usually involves three people – one of whom pilots the Claas twin-track crawler.
A second is responsible for digging the 10ft trench where the lateral is to join the main drain, forming the start point for the tractor’s uphill run.
Once the bout has begun, the digger driver hops out, joins the two via a Y-branch, and fills the hole back in.
When possible, a third person is roped in to run the pipe trailer behind a Gator.
“We opted against speccing an on-board pipe carrier,” explains Patrick.
“I could see no great advantage in it, as it’s far easier for the Gator driver to shoot back, load another reel of pipe and sort the joins.”
How much power?
According to Soil-Max, a 5t tractor of circa 150hp can manage the job, though this depends on soil type, topography and surface conditions.
“Power isn’t a problem – it’s more about weight and traction,” says Patrick.
“Ground conditions are the biggest factor – the top needs to be dry, and we’ve done it successfully on frost.”
Laying the main drainage pipe presents the biggest challenge, as it tends to be set at 90cm – 15cm deeper than the laterals.
To overcome this test of traction, he completes a pre-rip down to 60cm, followed by a second at full depth.
If there’s still a shortage of grip, a strap is shackled to a towing eye on the main beam, allowing two tractors to pull the plough in unison.
The one downside of the pre-rip is the extra soil heave it causes. How this sizeable earth ridge is dealt with depends on the cropping plan.
“If we’re draining in autumn ahead of a spring-sown crop then I tend to leave the soil to settle naturally over winter,” says Patrick.
“But if it’s going straight into another crop, we’ll squish it back down with the tractor.”
Working speed is typically 0.8-1kph, which translates to 1,000m/hour or 4ha/day in easy-going conditions.
“It’s a fast way of laying pipe accurately, but it’s a long-term job,” concludes Patrick.
“If we can do 10ha/year then, by the time we’re done, we’ll have improved the whole farm for the next generation.
Soil-Max tile ploughs
European-spec ZD versions of the Soil-Max ploughs devised by Indiana farmer Denny Bell were launched in 2018.
There are two linkage-mounted models available, the smaller of which is the ZD1200 limited to a maximum depth of 1.2m and pipe bore of 4in.
Prices for these start at £25,000, excluding an in-cab control box, GPS receiver, gravel box and on-board reel carrier.
Alternatively, there’s the ZD1600 that’ll go to 1.6m.
This has a larger point, funnel and rear boot to handle 6in-diameter pipe, and costs upwards of £40,000.
There’s also a trailed pull-type version to lay up to 10in pipe to a depth of 2m.