Exotic and unusual harvesters: cotton pickers
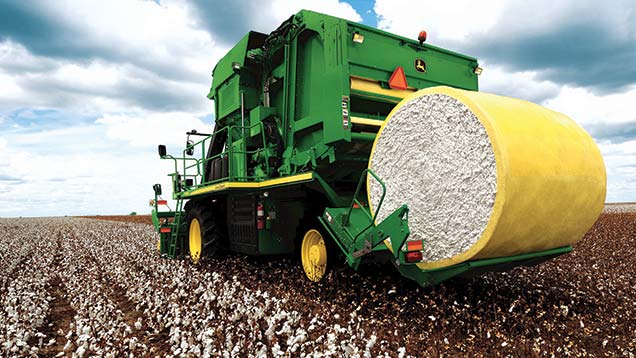
In the latest in our series on unusual and exotic harvesting equipment, Nick Wigdahl looks at how cotton is harvested and baled in one operation.
Cotton requires plenty of rainfall or irrigation (60-120cm/year) and heavy soils, but it is moderately drought and salt resistant and is well suited to semi-arid lands.
White is the most common colour of the cotton bolls, but green, red and brown variants are also available. Genetically modified cotton is widely grown to resist the larvae of various species of moths.
See also: Exotic and unusual harvesters – sugar cane
China is the world’s biggest cotton producer with 7m tonnes harvested a year, followed by India with 6.6m tonnes, the US with 2.8m tonnes, Pakistan with 2m tonnes and Brazil 1.6m tonnes. Average yield in the US is about 0.9t/ha.Â
Cotton is measured in bales, each weighing 220kg and containing enough fibre to make about 1,200 T-shirts.
However, prices to farmers fluctuate wildly. They reached an all-time high of 211c/lb in March 2011 but have fallen steadily since then to today’s price of 65c/lb. That’s the equivalent of about £1/kg or £1,000/t
History
Before mechanisation came along, cotton picking required huge amounts of hand labour. This was the key driver behind the slave trade before the American Civil War and the share-cropping system afterwards.Â
The two world wars prompted a huge labour shortage in the US. The rural black population declined by 21% between 1940 and 1950 as workers flocked to the armed forces or defence industry in the north.
A patent for a mechanical cotton picker was filed as far back as 1850 and there followed another 1,800 patents proposing techniques as varied as vacuums, static electricity and mechanical fingers. Â
Finally, in 1942, International Harvester’s H-10-H single-row machine solved the problem of the spindle capturing only a small percentage of the fibres. Even those early machines of the 1940s were estimated to replace 40 labourers.
Developments in plant breeding have played an equally important role in increasing harvest productivity. Plants that have bolls higher off the ground and which ripen uniformly allowed the harvester to pass through the field only once a season, rather than the multiple passes that were required before.
Defoliation of plants by herbicides just before harvest also permitted higher travel speeds and cleaner samples. Â
Strip or pick?
Cotton is harvested with either a picker or a stripper. Stripper-type harvesters, as the name suggests, strip the entire plant of both open and unopened bolls along with many leaves and stems.
The unwanted material is then removed by equipment at the gin or processing plant. Strippers mainly work in very dry areas where yields are lower, such as west Texas or Khazakstan.
Pickers, or spindle-type harvesters, remove just the cotton from open bolls and leave the bur on the plant. The idea came from ancient spinning wheels. The spindles, which rotate on their axes at high speed, are attached to a drum that also turns, causing the spindles to enter the plant.
Before doing so they are moistened. The cotton fibre is wrapped around the moistened spindles and then taken off by a special device called a doffer. Cotton is either delivered to a basket (the combine harvester equivalent of the grain tank) or is baled on board, which permits continuous harvesting.
Today’s machines
The difference in the two basic mechanisms is reflected in the price. The base price for John Deere’s CS690 cotton stripper is US$636,200 (£397,000), while the CP690 picker is $857,000 (£535,625).
This puts cotton harvesters right up there with the biggest combine harvesters and four-row self-propelled potato harvesters in terms of price tags.Â
The CP690’s spec is impressive – a 560hp powerplant, double wheels on the front, auto steering, a 1,135-litre fuel tank, 1,100-litre water tank (for moistening the spindles), four-wheel drive and a full LED light package. Â
There are 3,360 spindles on the six rows, arranged in a screw pattern, which helps extract the cotton. Radio-frequency identification (RFID) tags are automatically attached to each bale so that the farmer knows where in the field each bale came from.
Continuous baling has hugely increased output as machines don’t have to stop to empty their baskets or wait for trailers. John Deere’s latest machine can harvest at about 4.5mph.
Strippers work faster and can handle windier conditions but deliver a much dirtier sample compared to pickers. The four-row 9970 has an output of up to 35ha/day, while its six-row replacement, the CP690 stripper, will be considerably higher.
The cotton harvesting manufacturing industry is unusually concentrated, with only John Deere and Case-IH producing machines in the western world.