Driverless tractors are coming…
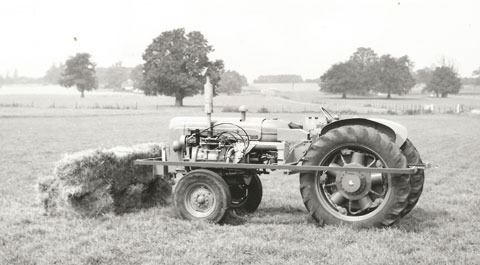
Driverless tractors could become one of the most significant developments in the history of power farming. Mike Williams wonders when and if the robot tractor revolution will begin
Robots already play an important role on farms. Examples include automatic milking parlours and on some arable farms robots handle potato packs.
Technology is already available to build driverless tractors that would perform at least some tasks efficiently, but there is little evidence so far that they threaten tractor drivers’ job security.
Obvious benefits of using driverless tractors would be a big reduction in man-hours at busy times, especially on arable farms, and the cost of the equipment might be less than expected.
Manufacturers point out that a cheaper, no-frills cab would be adequate for a tractor spending most of its time with no driver, allowing cost savings that would pay for at least some of the automatic control equipment.
Using the robot approach may also bring performance benefits. Control systems using high tech electronics, GPS and computers can be more precise than even experienced drivers, and there are claims that output and fuel economy can be improved by the extra efficiency.
In spite of their potential benefits, there has been little enthusiasm when robot tractors appeared in the past. According to one theory many farmers would be reluctant to trust essential field work to a completely unmanned tractor, preferring someone in the cab to make decisions and deal with problems.
This is the view of Stephen Leese at John Deere’s European Technology Innovation Centre.
He thinks there may be a psychological barrier discouraging farmers from choosing a totally driverless tractor, but they can still benefit from the advanced technology while having the reassurance of a driver in the cab, he says.
Mr Leese’s view is supported by recent developments providing automation with a driver in control. Some companies are applying this approach to grain carting from the combine, a job demanding a high level of accuracy and occurring at a busy time.
US company Kinze Manufacturing has developed a product that allows the combine operator to take control of a tractor and chaser bin and guide it to collect grain on the move.
With the Kinze system the tractor towing the chaser bin has no driver, but is under the combine driver’s constant control.
When the grain tank is due to unload, the combine driver uses a keypad with a radio link to start the tractor and bring it to the combine to position the chaser bin for unloading the grain tank.
With the grain tank empty, the combine driver sends the chaser bin back to the headland where it can wait for another load or discharge its load into a bulk trailer.
Kinze announced a prototype version in 2011 and updated equipment is being tested this year on three local farms.
Case IH won a Silver Medal when they announced their remotely controlled grain carting system in 2011 at the SIMA show in Paris. Called V2V or Vehicle-to-Vehicle, it operates as an extension to their Advanced Farming Systems (AFS) technology. For most of the time the V2V grain cart tractor is controlled conventionally by its own driver, but within 100m of the combine the remote control system can take over, precisely synchronising the position and speed of both vehicles.
The combine driver controls the grain tank unloading, and when this is complete V2V releases control and the tractor driver takes over again.
Grain carting is one of the tasks that can be handled by John Deere’s Machine Sync, which relies on communication between tractors or between a tractor and a self-propelled machine. This is another system where the grain carting tractor keeps its own driver, who hands over control to the combine driver while unloading the grain tank.
Machine Sync is also being developed to enable one driver to operate two tractors in what is known as a ‘master’ and ‘slave’ arrangement. The master tractor is driven conventionally by someone in the cab who also uses a remote control system operate the second or slave tractor.
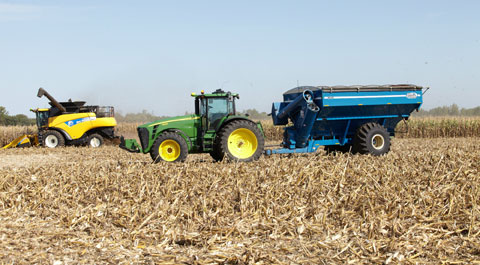
Two tractors and one driver also feature in the Fendt Guideconnect system, with the driver leading the way in the master tractor followed by the slave tractor.
Both are linked by a control system that combines GPS with high tech electronics and radio signals.
The distance between the two tractors is maintained at a setting chosen by the driver, and the second tractor also maintains an offset to match the implement width.
The control system is programmed to make the slave tractor imitate everything the master tractor does including speed changes, braking, headland turns and travelling to and from the field on farm tracks.
Field tests with prototype versions of Guideconnect started in 2012 and continued this year.
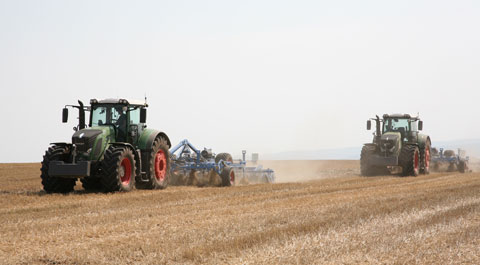
For those who prefer driverless mechanisation the Spirit project in America aims to allow one operator to control up to 16 tractors or self-propelled machines working up to 25 miles away.
Behind the development is the Autonomous Tractor Corporation which has developed a versatile 202hp tracklaying power unit that can be built as a tractor or provide a base for a self-propelled implement or grain cart.
Terry Anderson, Spirit’s chief designer, thinks the self-propelled machine version will become more important that the tractor.
GPS and RTK were considered unsuitable for the Spirit guidance system, partly due to reliability problems and also because the radio system chosen for field operation has a lower cost.
For travel between fields using farm tracks the Spirit power units can be programmed to follow a vehicle such as a pick-up truck, and they can be towed for travelling on public roads.
Mr Anderson explains that Spirit was developed because conventional tractors have become more complex and recruiting suitable drivers is increasingly difficult in many countries.
When the Spirit tractor units are available commercially – perhaps in two years – farmers will be able to manage machines instead of people, he explained.
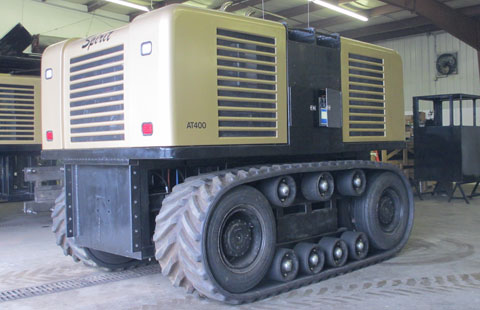
Driverless technology for tractors and for cars are both at about the same level of development, and the commercial prospects for both are held back by legal limitations and uncertainties.
A Department for Transport spokesman agreed that the legal position for using a driverless vehicle on public roads is far from clear but, he explained, the DfT is currently working with an Oxford University research group to draw up an official policy. This is still in progress, but the aim would be to give clear guidelines for future users, he said.
The Association of British Insurers, which represents the insurance industry, says their current view is that an approved driverless vehicle – either car or tractor – could not be used on a public road unless it is carrying someone competent to take over the controls in an emergency.
This was also the opinion at Thatcham, an insurance research and advice organisation, but their view about using a driverless tractor on farm land or private roads was less clearcut.
It appears that for field work the tractor need not carry a driver if there are no obvious hazards, but exactly what might be considered a hazard and who would make the decision is far from clear.
Driverless tractors are not a new idea. A simple mechanical guidance system achieved very limited success in the US about 100 years ago and there have been plenty of attempts since then, so far with little prospect of a big commercial breakthrough.
Guide Wheel System. American designed self-steering kits using a frame attached to the tractor’s front wheel hubs were available from about 1912.
They worked only for ploughing, using a guide wheel attached to the frame to follow the previous furrow bottom and guide the steering.
A benefit claimed for the kits in the days before Health and Safety Inspectors existed was that the driver could dismount and walk beside the tractor, climbing aboard again to take control for the headland turn.
Guide Wire System. Driverless tractor development moved to Britain when engineers at Reading University used buried wires to guide a much-modified tractor in 1956.
Wires 20cm below the surface carried an electric current that was detected by sensors on the front of the tractor. The sensors were linked to the steering mechanism, guiding the tractor as it followed the wire.
The idea was adopted by the National Institute of Agricultural Engineering at Silsoe which took over the project, and commercial development followed in 1958.
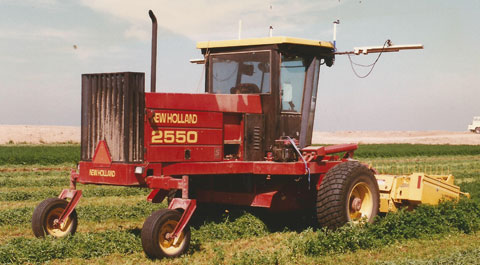
Three or four systems were installed on fruit farms to guide grass cutting tractors in orchards, but the idea was soon abandoned.
Radio Control. Radio signals were used to guide a Ferguson tractor in America in about 1957 when an operator with radio equipment stood in the field sending signals to the driverless tractor.
This showed the idea worked, but it was otherwise pointless as the operator would have controlled the tractor more conveniently and efficiently from the tractor seat.
The Ford company in Britain chose a different approach in about 1959 when they demonstrated two Fordson Major tractors working with one driver.
The driver operated the controls of his own tractor manually while using a radio to control the driverless tractor. This looked impressive, but it might cause confusion when both tractors reached the headland at the same time.
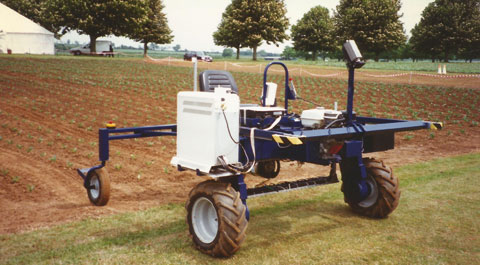
Image Analysis. Engineers at Silsoe developed a small driverless tractor guided by computer analysis of images from a CCTV camera on the front of the tractor.
The tractor was designed in 1996 for working in rowcrops such as vegetables and sugar beet, with steering controlled by the computer that analysed the camera pictures to identify the rows of crop plants and the weeds between the rows.
The tractor worked well and made accurate headland turns but, surprisingly perhaps, there was little commercial interest, although the guidance system was successfully adapted for use on inter-row hoes.
GPS. Signals from the GPS space satellite network were combined with image analysis to provide the control system for a driverless self-propelled crop swather demonstrated by New Holland in the US in 1996. The control system could take over completely in the field, including headland turns, and appeared to work well but the idea has not progressed to the production stage.
Video: Fendt driverless tractor