Grimme slims down Matrix mechanical precision seeder
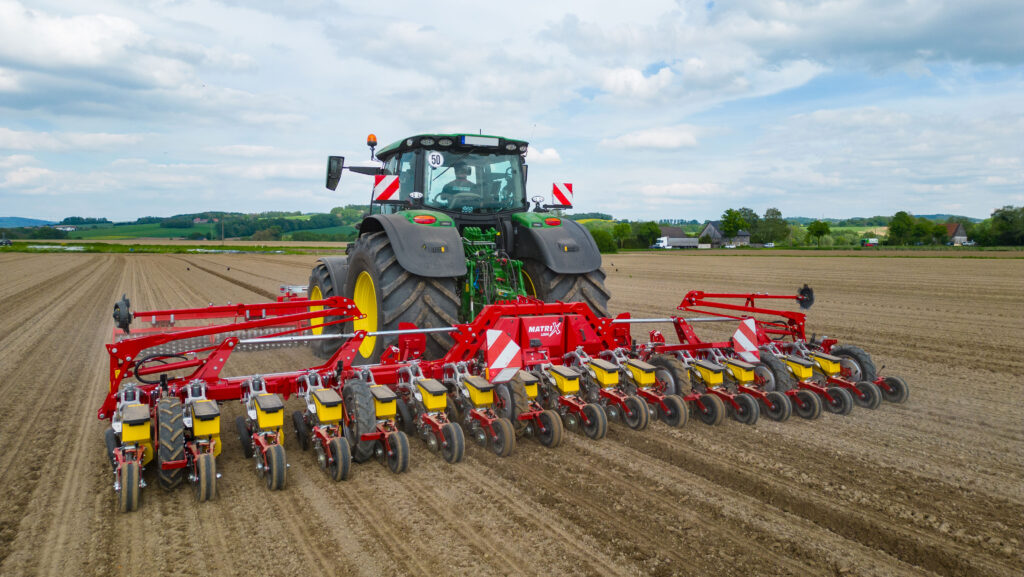
The latest 12- and 18-row Grimme Matrix beet drills have been given a makeover, resulting in a more compact layout, better weight distribution and easier operation.
The parallelogram that controls seeding depth is now made from hardened cast aluminium, with the lighter and more rigid design said to offer better ground contouring and force dissipation.
See more: One-pass Alien System combi pairs air drill with plough
A return to mechanical weeding on many farms demands accurate, central seed placement to avoid crop damage, and Grimme claims the revised linkage achieves this better than previous iterations.
There are also revamped hoppers with lids that close tightly via spring-loaded snappers.
And new optical sensors in each seeding coulter detect and count beet, oilseed rape and chicory seed, and alert operators to possible blockages.
Modular design
A benefit of the modular design is that it can be converted from conventional to mulch seeding.
Row spacing can be adjusted from 50cm to 45cm, with the two settings advantageous in situations where cultivation methods may change.
Wearing metal on the Matrix’s coulter system can be changed quickly via two screws – one loosened, the other removed – to reduce downtime.
Similarly, the leading cutting discs have extended tool-free adjustment to get more use out of each set, and the wheels can be folded up and locked into place during maintenance.
Optional clod clearers, which can be configured to run at six different heights, are no longer mounted on the main frame. Instead, they are in front of each seeding unit and set individually for each row.
Coulter pressure can be adjusted in five 30kg stages up to 120kg and seeding depth tweaked in 5mm increments from 0-5cm.Â
Press wheels, furrow closers and castor wheels are also altered with a simple lever system.
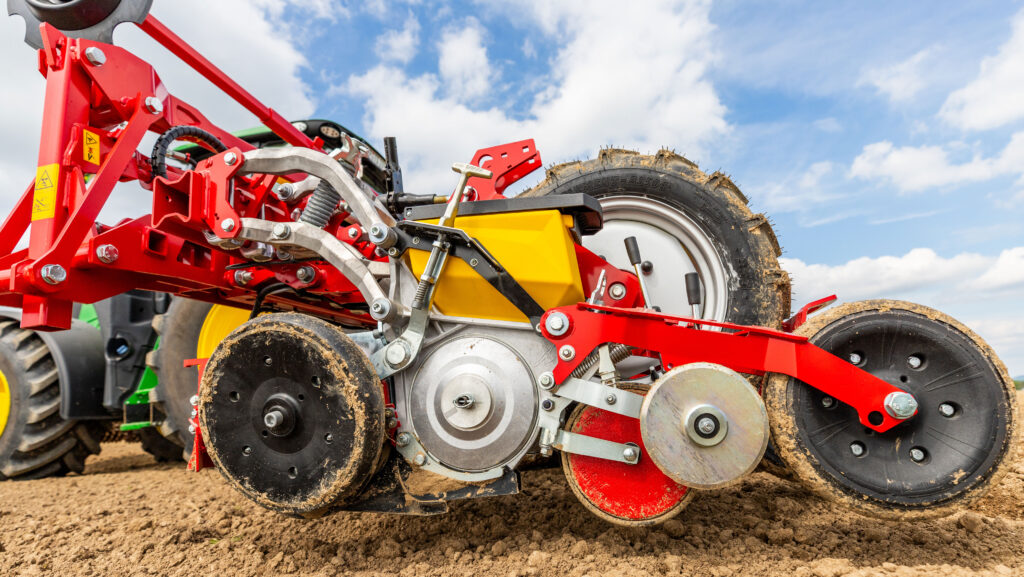
© Grimme
Increased intelligence
For precise, slip-free seed metering at different forward speeds, the Matrix has a radar sensor positioned under the main frame of the drill as an alternative to using the tractor’s speed signal.
Individual seeds are placed in a triangular formation for optimised plant distribution, and there’s now the ability to create turnpike rows.
These see the seed rate upped around the field edge where plants are more prone to pest attack, helping to account for potential losses and achieve an even crop across the field.
Operators can also create “harvest windows” during beet drilling, which leave markers that allow the harvester driver to match to drill rows when lifting, increasing efficiency and comfort in the cab.