Custom-built cultivators offers money-saving alternative
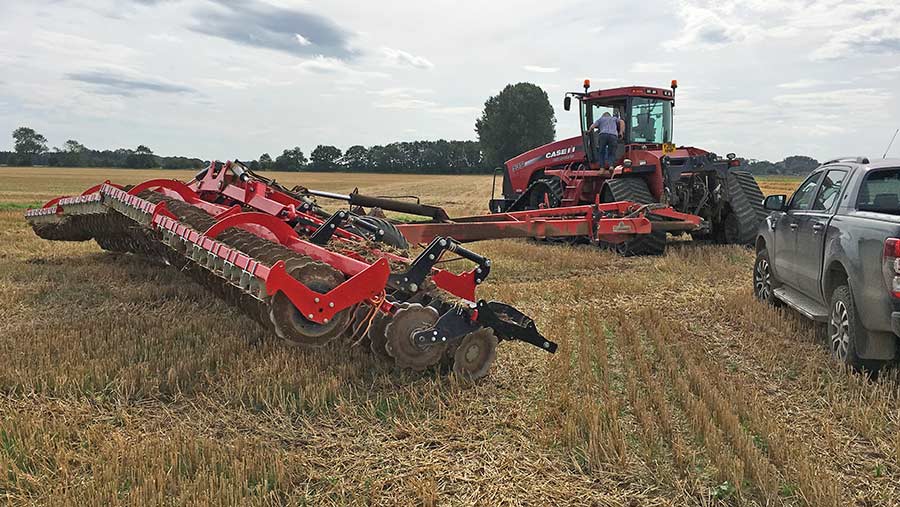
The cultivator market is awash with options to suit most tastes and budgets, but despite the plethora of choice there’s often a compromise when making the final decision.
The angle of the discs might be right on one machine, the leg configuration better on another, and the trash clearance just right on a third. Or the perfect machine exists and it’s that bit too expensive.
However, for those that don’t mind stepping away from the big brands, there are a number of small engineering outfits that can build customised cultivators without breaking the bank.
See also: How to pick the best cultivator wearing metal
Lincolnshire-based James Richardson and Jim Tarry from Suffolk are two such fabricators. They both manufacture machines to their own designs, but also offer a bespoke build service that can make customers’ ideas a reality – if they have a good chance of working properly that is.
Mr Tarry specialises in modifying existing machinery, too, meaning redundant machines can be given a new lease of life for a fraction of the cost of a new build.
James Richardson – JR Machinery, Millthorpe, Sleaford, Lincolnshire
How the business works
After studying agricultural engineering at Harper Adams and cutting his teeth on both the design and manufacturing teams at Sumo, James Richardson set about producing his own cultivation equipment.
The first machine was his versatile Apollo that could work as a single-pass cultivator or a direct oilseed rape drill. But since then, he’s built all manner of equipment from mole ploughs and subsoilers to drills, Cambridge rolls and packer rollers.
His workshop – based on the family farm in Millthorpe, Sleaford – has been set up to build heavy kit, with a 5t gantry crane purchased from a disused factory. Implements are designed with the help of CAD software and a large proportion of his steel is laser cut by a local firm.
His aim is to produce high-quality cultivators that don’t cost the earth. “I try and strike just the right balance – no over- or under-engineering – and I make sure that the price is right,” says Mr Richardson.
To do this, he has come up with a number of adaptable design platforms that can be tweaked to suit the needs of different customers. This avoids large amounts of design time that can add significantly to the cost.
Paint is applied in-house and he is in the process of installing a new powder coat oven to improve the process.
Here are a few of his creations:
Apollo
The first cultivator to be built under the JR Machinery brand was the Apollo, disc unit designed for primary cultivation and oilseed rape establishment.
In cultivation mode, the tool has a set of Sumo subsoiler legs, sandwiched between two sets of rubber-mounted discs, and a packer roller at the rear. There are two options for this – a Tilso Diamond packer roller or one of Mr Richardson’s own packers that is made from durable non-stick plastic.
The split-disc configuration was picked to prevent soil being mixed throughout the profile and keep blackgrass seeds on the surface.
For oilseed rape establishment, the front set of discs are swapped for slitting legs – to prevent the subsoiler legs bringing up any lumps – and the rear set can be replaced with Moore disc coulters running 150mm (6in) either side of the legs. These are linked hydraulically to maintain even seeding depth.
Seed is applied by an air seeder unit and there is the option of adding a liquid nitrogen fertiliser kit, too.
The Apollo is offered in 3m to 6m working widths and the 3.2m trailed version started at £22,950. He had made more than a dozen Apollos in various custom configurations before demand in his area switched to shallower cultivation. They can still be ordered, though.
Disc cultivator
The disc cultivator is now one of the staple machines for the JR Machinery workshop and the chassis has been designed so that it’s easy to configure in different ways.
In its standard guise, it’s fitted with two rows of Simba DTX-style discs which are mounted on heavy duty arms set at an aggressive angle. This means they can work as shallow as 3in and still move all soil across the width of the machine.
One of Mr Richardson’s own ribbed packer rollers is fitted at the rear, which apparently does a similar job to a DD ring for a lower outlay.
Because the chassis is adaptable, it’s relatively straightforward to add tines, levelling paddles or seeder units as the customer sees fit.
A standard-spec 4.5m folding disc cultivator costs about £18,000.
12m shallow disc cultivator
A colossal 12m shallow disc cultivator was built to help get on top of the home farm’s burgeoning blackgrass problem.
It was Mr Richardson’s first prototype and after a couple of seasons’ testing and tweaking he’s perfected the design. He’s come up with several ways to adapt it to different applications and make it more cost effective.
In its current form, the cultivator has two gangs of discs with leading tines that are suspended from the main frame at their mid-point. This allows them to pivot over lumps and bumps and means they can be pulled at speeds of up to 16kph without bouncing.
When hooked to a Case-IH Quadtrac 535 and working at 3-4cm deep they can cover between 120 and 160ha in a day, making it quick to get a blackgrass chit on large blocks of land behind the combine. Levelling paddles can also be fitted in place of the tines for more aggressive soil bashing.
The disc gangs are permanently attached on this machine, but future versions will have a quick-release pivot so that buyers can drop the discs off and pick up a set of drags or tines. The design also has space for a seed hopper, which means it can double up as a cover crop drill.
The fact that it’s 9m long and has the wheels at the rear means it’s only really suitable for articulated tractors. However, it can be fitted with a rear steering axle, which significantly improves its manoeuvrability.
It costs about £70,000, which according to Mr Richardson is about £30,000 less than many comparable machines.
Grassland subsoiler
Another regular build is a grassland/low-disturbance subsoiler available in three-leg 2.5m or five-leg 3m formats.
This uses Sumo-style points on custom built legs, which are mounted on a V-shaped frame to make them more cost effective. Versions with five legs or more can have a second beam and staggered legs.
To prevent the leg ripping the sward open, each has a 520mm swivelling front disc mounted ahead of it. The idea of using large-diameter discs like this is that they bite deeper into the ground and do a better job of preventing the turf tearing.
The bearings are also tough enough to support the entire weight of the machine if it hits stone and has to ride up over it.
Rear packer rollers are built by Mr Richardson and they have lugs welded in place to help close the slot and leave a tidy finish.
These subsoilers are sold under the JR Richardson brand, as well as by Wilton Goligher in N Ireland and Dan Griffiths of Huffle Designs, which is based in Gloucestershire.
Three-leg versions cost £7,000.
Trailed subsoiler
The 4.5m, nine-leg trailed subsoiler pictured is one of several heavy-duty units built by Mr Richardson for large articulated tractors and crawlers.
This version uses JJ Metcalfe’s versatile NG leg system and is capable of working to depths of 15in if required. Originally, the subsoiler was built with a linkage drawbar, but when the farm switched to running a Case Quadtrac, it was converted to a conventional drawbar.
To prevent premature wear, a custom ring was built out of 50mm steel with a flat face for the pin to engage with. A parallel linkage on the drawbar also makes sure the pin stays level at all times. “If you used a standard arrangement on an implement like this, you’d probably wear it out in a day,” says Mr Richardson.
A guide price for building a similar machine to the one above is £30,000.
Packer rollers
Having perfected his packer roller manufacturing technique, Mr Richardson offers to build retrofit units for existing machines.
His ribbed packer is constructed from a central tube with preformed rings welded around the outside. This apparently makes them durable and cost-effective to build.
They cost £1,000 per metre, including scrapers.
Jim Tarry – JTS Machinery, Kirtling, Newmarket, Suffolk
How the business works
Having spent 40 years working with and modifying farm cultivation equipment, Suffolk-based engineer Jim Tarry knows a thing or two about moving soil.
During his agricultural career he’s worked on a number of farms operating, modifying and fixing equipment. However, for the past two years he’s been running his own business building cultivators, altering existing machines and carrying out bespoke fabrication jobs.
His fascination with cultivation has come from years of operating machinery and tweaking it to make it run better. “I’ve never been one to set the machine up once and then never get off the seat,” says Mr Tarry.
“I’m always looking at the way the soil and trash flows through it and coming up with ways to make it better in the workshop – often the smallest of alterations can transform the way a machine works.”
As a result, the farms on which he’s worked have benefitted from having disappointing machines transformed into invaluable tools for a very modest outlay.
Mr Tarry now operates out of a workshop in Kirtling, Newmarket, and trades as JTS Machinery. He’s put his knowledge into creating his own low-draft primary cultivator and plans are afoot for a secondary seed-bed former to complement it.
He carries out all fabrication work himself and only outsources laser steel cutting and the two-pack paint finish that’s applied to his machines.
Here are a few of his creations:
Maverick Mid-Till 400
The Maverick Mid-Till is a low draft primary cultivator that works 125mm-250mm (5-8in) deep and leaves the soil open rather than pressed down by a packer roller.
At the front it has two rows of staggered McConnel Shakaerator-style tines, which were picked for their low power requirement and effective soil lifting without bringing up subsoil. These are spaced at 74cm and have a 100mm point.
Together these move about 90% of the ground before a set of Simba Cultipress tines work up any topsoil that has snuck past the legs. The angle of these is adjustable to get the maximum amount of soil mix.
The final element is a hefty set of 660mm Gregoire Besson-type ridged discs that slice through clods, mix and chop without causing compaction. These are more aggressive than many rubber-mounted angled discs and, because they carry the weight of the machine, won’t ride over stubborn clods.
Unlike many other cultivators of this type, there’s no packer to consolidate the ground afterwards. Mr Tarry chose to do this so that the soil remains open for air and rain to work through or to dry out when it’s wet. It also means it’ll do a tidy job when the ground is wetter than ideal.
The pictured machine is the 4m mounted version, which has 11 McConnel legs, 10 Cultipress tines and a heavy-duty frame that brings the total weight to 3.42t.
Mr Tarry recommends pulling it with a tractor between 250hp and 350hp. However, his demo machine is a John Deere 7920 (putting out about 200hp) and it can pull it at 8kph in most conditions.
The 4m version folds to 2.4m for transport, comes with a set of road lights, and has a list price of £29,650. A 3m ridged version is also available at a cost of £15,000 and trailed versions can be built to order. These also have the option of pulling a roller for conditions where moisture needs to be conserved.
For one local farmer, Mr Tarry has built a simplified version of the Mid-Till using an old McConnel Shakaerator at the front.
He-Va Disc Roller cover crop drill
Replacing the front levelling paddles with a straw rake and adding an Opico Variocast seeder has given a redundant He-Va Disc Roller a new lease of life as a cover crop drill.
One of the first jobs was coming up with a compact design for the straw harrow which didn’t hamper the machine’s turning circle. Mr Tarry managed to achieve this without making any major modifications to the original chassis, so the levelling paddles can be put back in the future.
The twin row of 12mm tines have hydraulic angle adjustment for altering their aggressivity and there’s a gauge so that the driver can see the setting from the cab.
Fitting the seeder unit on the top of the machine was relatively straightforward, but a bit of fettling was required to get the seed distribution right. Mr Tarry opted to place the seed behind the rubber flap that stops soil from the discs flicking onto the packer roller.
This meant making custom seed distribution plates and adding steel reinforcing bars to stop the rubber flaps swinging back and interrupting the spread pattern.
Finishing touches included adding a set of steps with guard rail to make it safe to fill the seeder, and changing the angle of the scrapers so that they sit deeper in the roller and keep it properly clean.
Modified Vaderstad Carrier
A rather tired Vaderstad Carrier 650 was significantly altered so that it could produce a fine seed-bed on heavy land that had been worked up by a primary cultivator.
The original disc units were removed and swapped for a set of tines and levelling paddles from an earlier model. “I can’t see the point of discs on a machine like this, so I went in search of a set of tines and levelling paddles from an older machine and managed to do a straight swap.”
Once the tines and paddles were installed, Mr Tarry welded a length of flat steel across each bank of levelling paddles. This locked them solid, making them more aggressive, and as the steel spans the gap between each board, it breaks any clods that attempt to pass through.
His final modification was to add a solid levelling bar on the front. This helps give a smooth, flat seed-bed and helps shatter some of the biggest clods.
Levelling board kits
Mr Tarry is a big fan of the levelling board as it’s a simple, cost-effective cultivation tool that often gets overlooked.
As a result he’s come up with a bolt-on hydraulic levelling board kit for a Vaderstad Rexius Twin or Simba Cultipress. It can also be modified to suit a much wider range of machinery.
He’s worked hard to get the pitch of the board right so that it delivers the ideal amount of soil movement and shattering and has angled the steel on the outer edge to prevent clods being pushed out onto previously worked ground.
Removable plates on the inner edge allow it cover the full width of the machine, without clobbering the drawbar during folding. A 6m kit costs £4,500.