Why shallow, high-speed Ecomat plough works for mixed farm
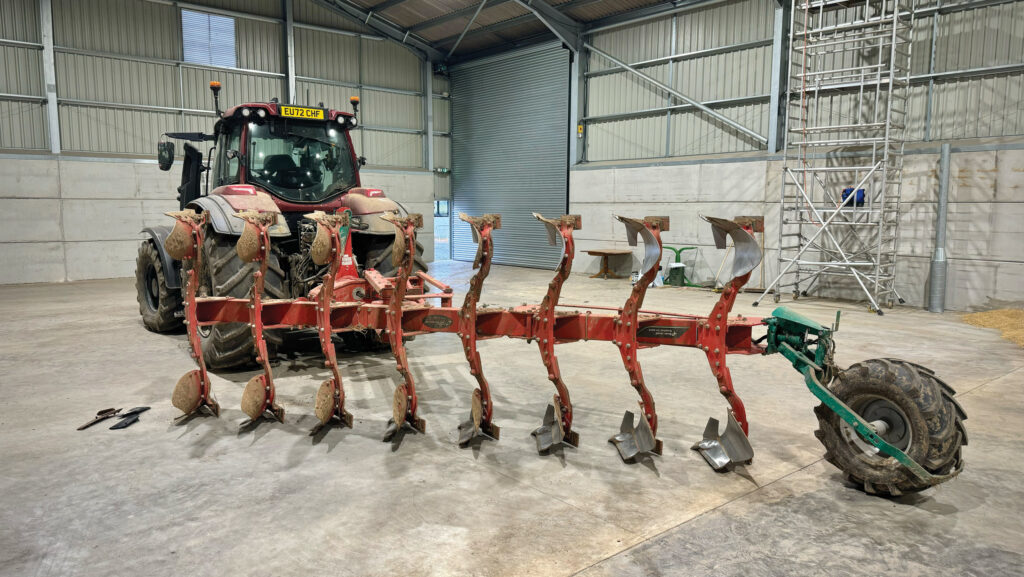
A skimmerless speed plough is now the cultivator of choice for Worthing-based Sompting Estate’s Titch Hill Farm, which has been on a quest to improve the efficiency, consistency and environmental friendliness of its crop establishment regime.
That’s no mean feat given farm manager Mark Heritage is battling soils drowning in tyre-slicing flint and sitting atop both nutrient-light chalk and savagely heavy clay – all in a single, small field.
See also: Versatile Guttler cultivator-cum-drill works for Suffolk farm
But, he says, these challenging conditions are where the shallow-working Kverneland Ecomat comes into its own.
Typically set to operate no deeper than 15cm, it can avoid the worst of the clay and chalk lurking below.
And, at speeds that can top 12kph in the right conditions, this plough-cum-cultivator (a plultivator, surely?) can comfortably keep ahead of the power harrow combi drill when weather windows are tight.
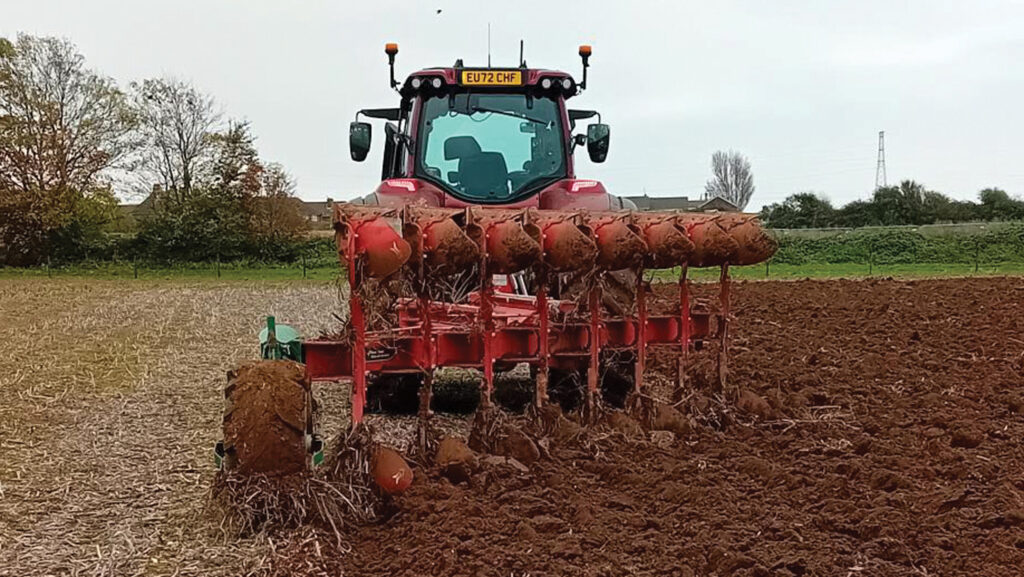
© MAG/Oliver Mark
Cultivation changes
Mark joined the business two-and-a-half years ago, when Sompting Estate grabbed the chance to take its 320ha farming concern back in hand.
Under the previous tenants, with which he worked, the mix of grass leys and arable land was rotationally ploughed.
But two-thirds of the time tillage was completed with a relatively crude Kongskilde Delta ripper/crumbler combination, with decidedly mixed results.
“The best yields always came after we ploughed – crop emergence was more uniform and we suffered from less weed and disease pressure – but the owners were very keen to go down a more regenerative route,” says Mark.
“We want to improve soil condition and reduce chemical inputs in a way that works for our land. Until now, we’ve struggled to find the right balance.”
The quantity of flint means direct drilling has never been an option – tines aren’t strong enough and discs won’t reliably stay in the ground – and some degree of soil inversion is essential to bury the stones every year.
“But what really got my cogs whirring was when we came to plough up some permanent grassland that was protected by Natural England’s Environmental Impact Assessment (EIA) regulations,” he says.
With the business staring at a potential £10,000 bill for archaeological assessments of fields worked deeper than 100mm, Mark began researching the alternatives.
“We couldn’t carry on full depth ploughing but, equally, we could afford to drop the plough without impacting crop performance,” he adds.
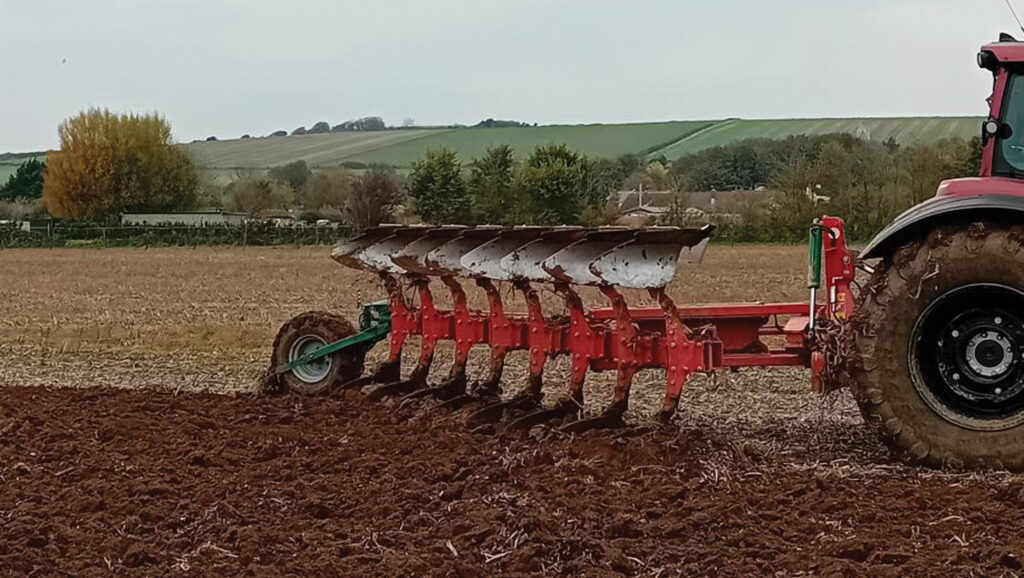
© MAG/Oliver Mark
That’s where the Ecomat came in. Rather than forgoing mouldboards altogether, it gives him the option of skimming the top 60mm like a set of discs to mix in trash, or invert most of the soil when pushed closer to its 180mm maximum depth.
According to KV’s boffins, the plultivator’s shorter bodies, which are shaped more like a skimmer than a conventional mouldboard, will turn over 75% of surface material – making for an end result somewhere between the 100% inversion of a plough and 45% for the average cultivator.
Demo seals the deal
A demo 10-furrow model was delivered by local dealer C&O Tractors in April, and Mark was impressed.
“It suited out system perfectly. It worked shallow enough to avoid the heavy clay subsoil and solid chalk, was easier to pull up the hills than a conventional plough, and left the deeper structure undisturbed, so the fields are easier to travel on for the rest of the year.”
Plus, it’s a great way of building up organic matter, he says.
“Rather than burying it deep, we’re putting the leys’ nitrogen-rich clover straight into the following crop’s rooting zone, and we’re only disturbing worms in the top 15cm, which is better for long-term soil health.”
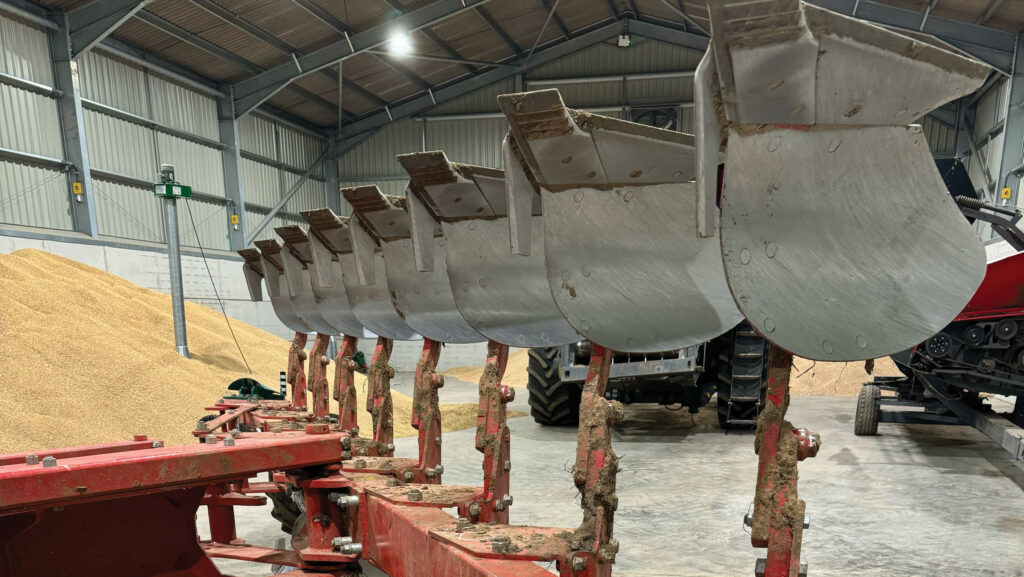
© MAG/Oliver Mark
Almost as soon as the demo left the farm, in went an order for an eight-furrow version – the smaller of the two on-land models.
Total cost was £38,000 including hard-wearing XHD metal, making it similar in price to that of the six-body LO plough on which is it based.
Fast work
One of the Ecomat’s attractions is its working speed. To achieve effective shattering and mixing of soil and surface trash, Mark occasionally pushes it to 12kph.
“The ground was bone dry when the plough turned up in August and I was working shallow, so I had to go fast to crumble it,” he says.
And with the eight furrows set at 16in spacings, making for a total pass width of 3.25m, he can cover up to 3ha/hour – far exceeding that of the 3m Amazone combi he follows with.
This output affords him the time and options to catch the ground at its best, either drilling straight afterwards if soil conditions allow or weather forecast necessitates, or blatting through several fields in a few days before leaving the soil to dry out.
Furrow width can be tweaked from 12-20in, but it’s a manual affair that also involves changing the shares to match.
“16in seems about right – it’s not so wide that it slows the tractor [a Valtra T255] on the hills, I can still cover the ground quickly, and soil throw remains even on the slopes.”
With this setup, the relatively light draft – particularly compared with the farm’s conventional five-furrow KV – means the tractor sups a modest 21 litres/hour.
Wheel slip is drastically reduced too, despite this being an on-land-only model with no option to drop into the furrow for extra traction.
This ‘limitation’ has been an advantage, because the tractor can run on chunky 710mm rear tyres, and they are kept out of the furrow where they would otherwise be carved up by the flint.
“We’re not cutting the tractor tyres up anywhere near as much. We used to get through a set every three years on the main ploughing tractor,” he adds.
Speccing it
Mark opted for the eight-furrow model purely because it would be easier to handle, and turn over, on the estate’s steep ground than a 10.
It is based on KV’s six-furrow LO plough, with the same 300hp-rated headstock, on-land linkage and beam.
However, with two extra bodies and no skimmers, point-to-point spacing is reduced to 65cm and the shear-bolts are also downsized, but they’ve come under relatively little stress thus far.
“I’ve only replaced four – all on the front furrows – and they’ve only snapped when I’ve dropped into ruts around pylons and momentarily sent the boards far deeper than intended,” says Mark.
The big expense came in speccing Kverneland’s tungsten XHD points. At about £6,000, these certainly weren’t cheap, but it’s an investment Mark reckons will pay dividends over the next few years.
“The reversible points on our conventional KV five-furrow plough rarely last more than 15ha, but the XHDs have done 100ha so far and are still like new,” he says.
“Based on that, they should be good for at least three years, which will save me wasting the best part of half a day changing metal on 16 furrows multiple times a season.”
He also opted for metal rather than plastic boards, purely to minimise the flint damage.
“The only issue we’ve had – and it’s not a problem exclusive to KV – is getting the paint off the boards to shine them up.
“Everything wanted to stick rather than flow, at least until I took it into our stoniest field.”
Mark turned down the other two prominent Ecomat options. One was plastic leg protectors which, so far, haven’t been missed.
But he does plan to fit trashboard extensions above the landside knifes whenever he next replaces the metal, as these will stop the soil boiling over into the neighbouring furrow.
The rest of the spec is much like any high-spec conventional plough.
The standout feature, says Mark, is KV’s novel Trailer Transport System, with the pivoting headstock allowing the Ecomat to follow the tractor like a trailer when swung into its butterfly position.
There’s also a hydraulic depth wheel with a position memory that prevents the backend ever dropping in too deep.
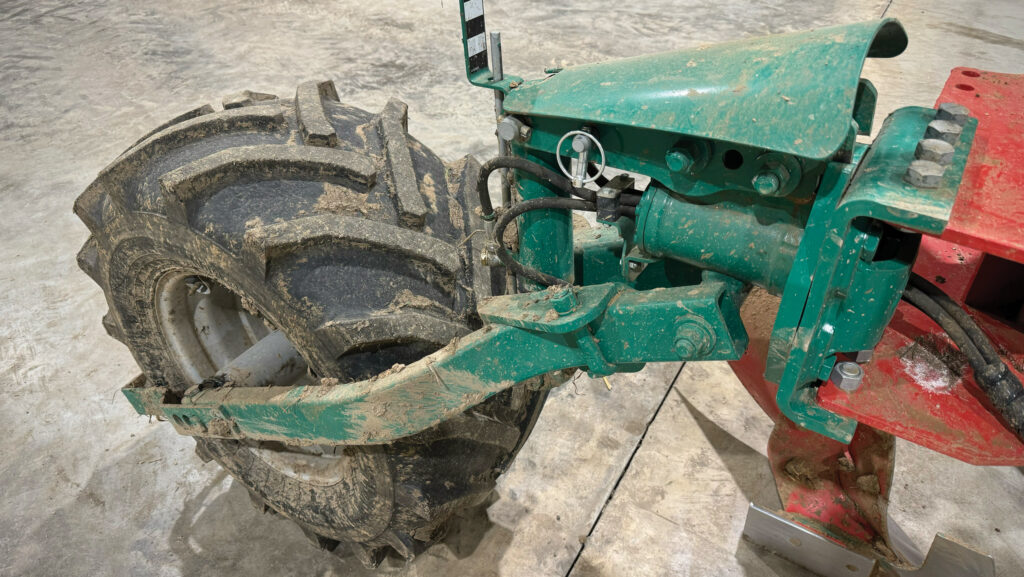
© MAG/Oliver Mark
“I like that I can change the depth instantly on the move, there’s no threaded turnbuckle to battle with, and on the last headland run I can push the wheel right down so there’s practically no trough around the boundary,” says Mark.
This leaves a level surface ahead of his Amazone combi drill with front press, making for a reliable system that should work in most conditions.
“We’ve effectively gone back to working the ground like a horse-drawn plough,” he says.
“Our approach is a work in progress and I’ll be monitoring worm counts and crop performance but, so far, the Ecomat has been my best investment on the farm – and I’d certainly say if it wasn’t.”
Farm facts
- Size 325ha
- Cropping 100ha species-rich chalk grassland; 120ha split between winter wheat, winter barley, spring barley, winter beans; 18ha herbal leys; 10ha vineyard
- Soil types Wildly varied, including flint, chalk and heavy clay
Sompting Estate’s Kverneland Ecomat
- Furrows Eight
- Interbody clearance 65cm
- Working width 3-5m
- Underbeam clearance 80cm
- Weight 2,150kg
- Lift requirement 6,400kg
- On-farm price £38,000 (inc XLT tungsten metal)