How strip-cultivating power tillers can offer cost savings
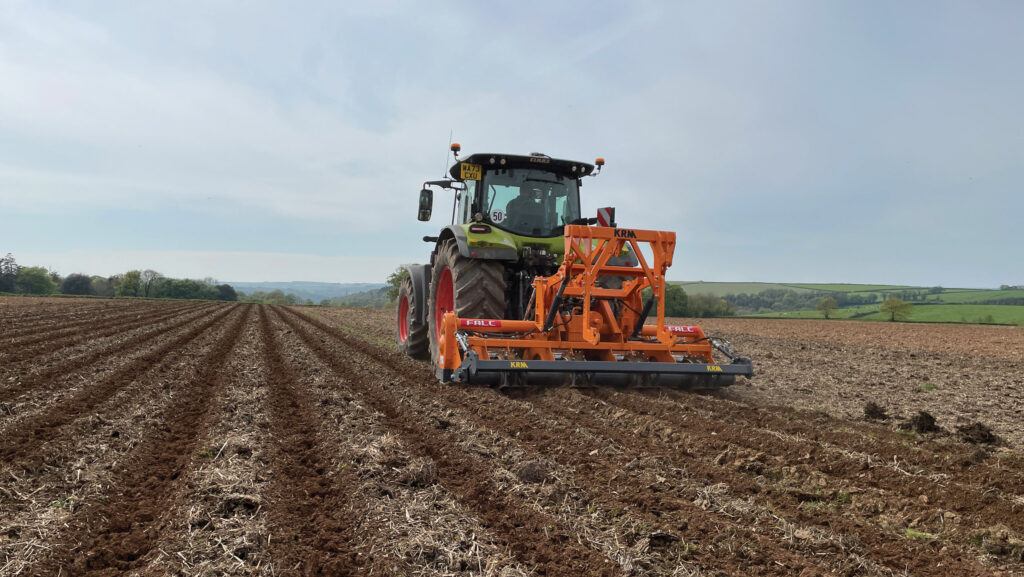
Does it really make sense to cultivate where only weeds are going to grow? Or create a soil structure vulnerable to a period of heavy rain just as the field is being harvested?
A number of growers and contractors are answering those questions by adopting strip-till cultivation using power tillers purpose-built for the job.
See also: Direct drills revisited: 6m Sly/Horizon Boss
Typically, these implements have a rotor with groups of blades spaced apart to till the soil in strips, often with baffles to stop it from being thrown on to the adjoining uncultivated ground, and with leading subsoiling legs to loosen the cultivated rows at depth.
A segmented packer roller in some form completes the ground-engaging elements, with a three-point linkage assembly on the back enabling a drill or planter to be operated piggyback-style.
“There are many benefits from using a powered strip-till cultivator,” argues Mike Britton at KRM, importer of the Falc Strip-Till.
“For one thing, it can be used as a one-pass system, and seed-bed preparation costs are reduced through savings in power and consequent fuel use, and in wearing metal replacement.
“In a sense, it combines the benefits of a no-till approach by leaving a large proportion of the field uncultivated, and conventional cultivation that creates the ideal conditions for seed germination and good root development.”
Mike also makes the point that with up to 70% of the soil surface remaining untouched, cover crops or a grass sward can be left in place and, particularly in the case of forage maize, this leaves a firm surface for harvesting machinery, tractors and trailers in a wet autumn.
That particular advantage is what prompted Edwards Farm Machinery to manufacture a strip-till power tiller, initially to meet the particular needs of vegetable growers.
“Farmers who normally let land for vegetable production became reluctant to do so because of concerns over the structural damage that could be caused to their soils in a wet season,” Rob Edwards explains.
“Our ST design combines non-powered cultivation elements with individual powered tiller units to produce the fine seed-bed that vegetable crops need – but only where the crops are going to grow.
“Come harvest, the untouched ground is more supportive, so harvesting rigs and tractors and trailers are much less likely to get stuck, and the soil itself is at less risk of being damaged.”
Strip cultivation, Rob adds, “has huge fuel-saving potential because it takes a lot less power than using a full-width power tiller, and it releases a lot less carbon into the atmosphere.”
What’s on the market?
Celli
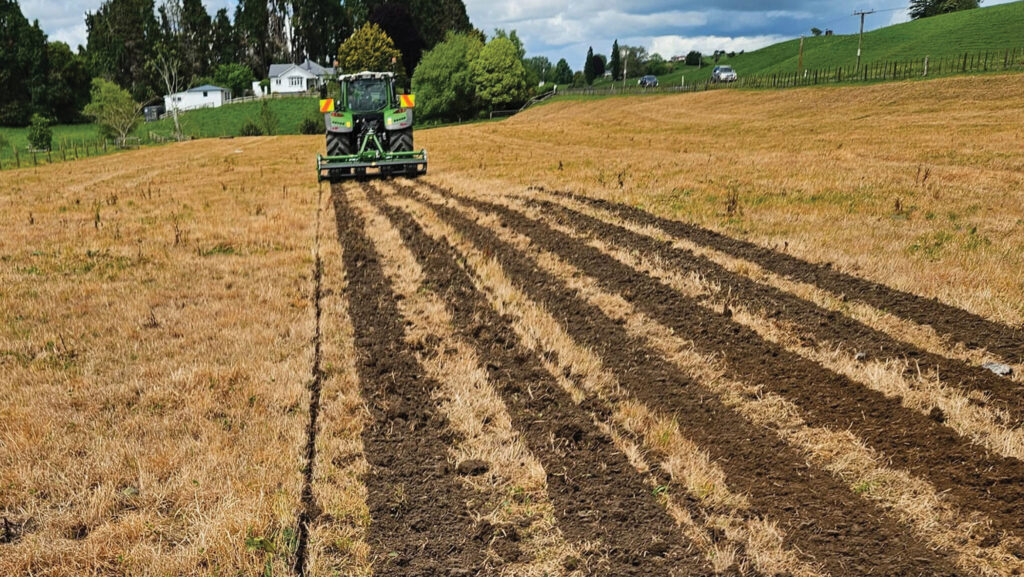
Celli’s Strip Till is based on the firm’s Tiger 250 rotary tiller © Celli
Italian power harrow and tiller manufacturer Celli has developed a strip-cultivating version of its Tiger 250 bladed tiller, adding Strip Till to its identity to emphasise that it cultivates selectively.
A four-row model has been introduced in New Zealand, where no-till and other alternative practices to traditional ploughing are very much in vogue.
Celli’s UK distributor, Nigel Quinn Agricultural Machinery Sales, reckons the implement has a list price of about £25,000 complete with the regular Tiger 250’s three-speed, 1,000rpm input gearbox, an oil cooler, double-welded flanges, and so on, plus wheel track eradicators and hydraulic adjustment for the segmented packer roller.
Versions with different strip spacings complete the Tiger 250 Strip Till details currently available.
Concept Agri – Lamma Hall 18, stand 176
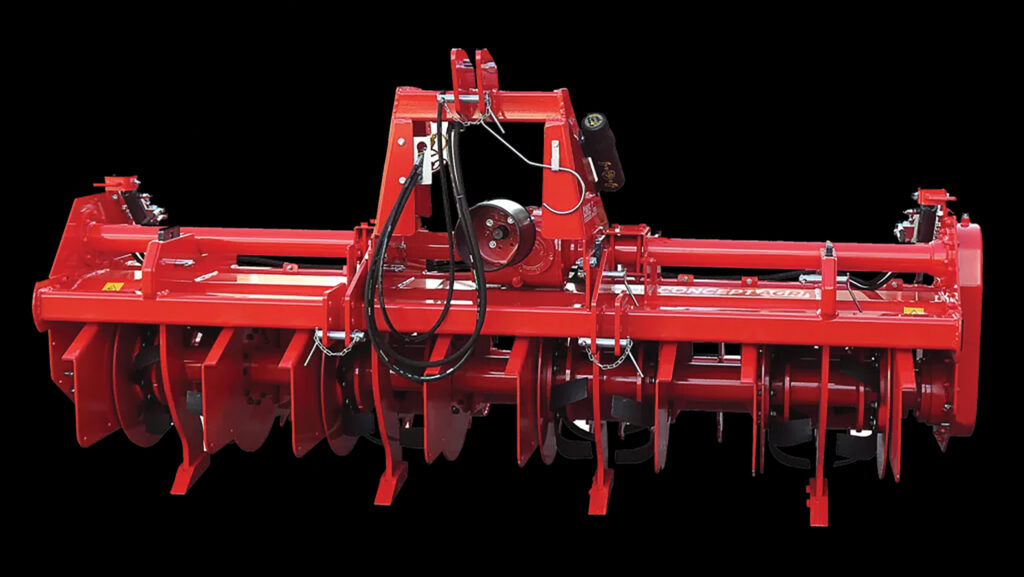
The 3m, four-row Concept Agri SFTrip tiller © Concept Agri
The SFTrip from Concept Agri is produced in four- and six-row versions, both 3m wide, resulting in cultivated strips 385mm wide and 750mm or 500mm apart, respectively.
Rigid tines with chisel points are standard, although dealer Robert H Crawford fits tungsten carbide-shielded Metcalfe NG System points as an alternative, offering low draft and long-wearing characteristics.
Either way, the legs are carried on a toolbar across the front of the implement, with working depth to 500mm adjustable individually by a pin-and-hole arrangement, and they are tucked in close to the rotor so that “boiling” soil is immediately broken down to create a fine tilth.
This measure also keeps the length of the machine as short as possible.
Fixed divider plates discourage soil from being thrown on to the uncultivated ground by both the tines and the L-shaped blades, while discs attached to the rotor and positioned either side of the groups of blades cut a well-defined edge to each strip of worked soil.
To the rear is a segmented packer to consolidate the resulting seed-bed strips, with hydraulic adjustment providing variable working depth down to 230mm.
Concept Agri recommends having 150-200hp available from the host tractor, with drive channelled to a gear train lubricated by an oil bath located down the left side of the tiller, looking from the rear.
Mechanical and hydraulic piggyback linkages for carrying a planter or drill are the principal options that enable a one-pass till and drill solution.
List price: SFTrip 300/4 four-row 4m – £26,330; 300/6 six-row 3m – £27,275
Edwards – Lamma Hall 19, stand 660
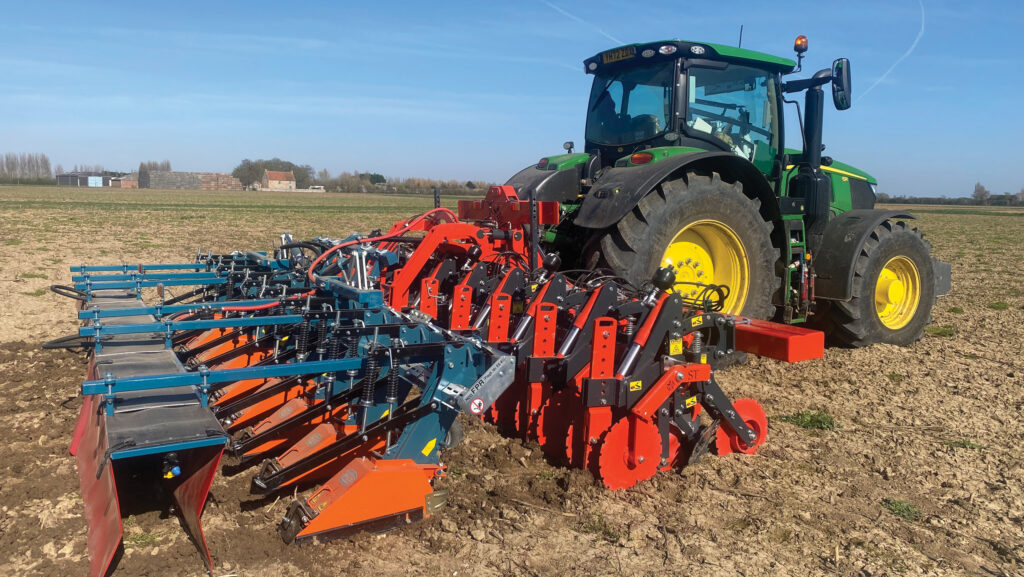
Edwards ST working 10 strips 220mm wide at 610mm centres © Edwards Farm Machinery
The one-pass strip cultivating system from Edwards Farm Machinery is formed from two implements – a non-powered assembly to create the strips initially, with individual row tillers mounted on the back to produce the fine tilth required for vegetable and related crops.
The leading equipment kicks-off with a vertical serrated disc cutting along the centre of the strip, two angled row-cleaning discs with prominent fingers to sweep crop residue and other debris aside, and a wavy-edge disc that begins the cultivation process.
Next are two more serrated discs that cut the edges of the strip and discourage soil heaved upwards by the hydraulic break-back protected soil-loosening tine positioned between them from spilling over on to the uncultivated ground.
Finally, there are the individual powered tiller units carried on three-point linkage at the back of the “static” strip preparation tools.
Available in 2.5-6.5m widths and capable of working to a depth of 80mm, these are produced by Italian manufacturer Comeb and have chain drive from a full-width enclosed shaft, with the ability to follow surface contours under adjustable spring pressure.
Options include a shielded pre-emergence spraying setup for each strip, and there are various working widths and row spacings for the bespoke outfit to suit forage maize, vegetable crops such as cauliflower, and tree planting.
List price: £31,000-£90,000.
KRM – Lamma Hall 18, stand 470
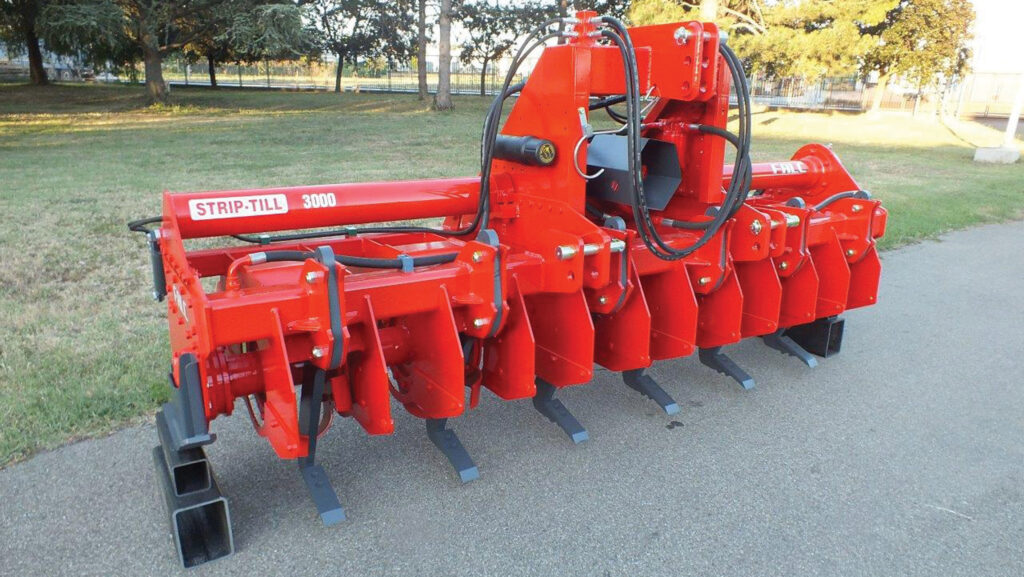
A 6-row Falc Strip-Till showing front tines and inter-row baffles © KRM
The Falc Strip-Till distributed by KRM has hitherto been available in 3.3m four-row and 3.3m six-row sizes with cultivated strips spaced 750mm and 500mm apart, respectively.
But a 6.3m version, available in eight-row 750mm and 12-row 500mm configurations with centre-split folding, will be unveiled at the Lamma show to meet demand for maize-planting contractors already running a drill of this size.
Unlike the four- and six-row machines, which can have a hydraulic implement linkage to work the tiller and planter as a single-pass outfit, the weight and centre-split folding constraints of the 6.6m variant means the new implement would be worked separately ahead of a planter.
All Strip-Till models come with an oil cooler for the gearbox, which transfers drive to an oil-bath lubricated gear train on the left side of the implement, looked at from the rear, which is protected by a generously-proportioned ski-like skid plate repeated on the opposite side.
Power requirement is put at 130-220hp for the 3.3m versions, and 250-400hp for the 6.3m, to handle the ripper tines positioned close to the tiller blades, and the four or six blades attached to each flange.
In addition to minimising the length and overall bulk of the implement, the close-coupled arrangement of tines and tiller blades provides immediate cultivation of soil “boiling” up from the subsoiling tine.
The tines have shallow-angled chisel points, working depth is adjustable by a pin-and-hole arrangement on each leg, and there is a vertical steel tube in front of individual leg units ready to set up a fertiliser placement kit.
Soil is consolidated ready for planting by a 550mm-diameter segmented “toothed” packer with scrapers, and twin hydraulic cylinder adjustment sets the tiller rotor’s working depth between 150mm and 250mm.
The two 3.3m implements weigh in at 2.3t and 2.5t, respectively, before the optional rear linkage is added, while the 6.6m versions tip the scales at 4.2t and 4.76t.
List price: Strip-Till 3000/750/4 four-row 3.3m – £33,650; 3000/500/6 six-row 3.3m – £35,140; hydraulic planter/drill linkage – £3,580. Strip-Till/P 6000/750/8 eight-row, 6m – £68,210; 6000/500/12 12-row 6m – £71,200.
Weaving – Lamma Hall 20, stand 770
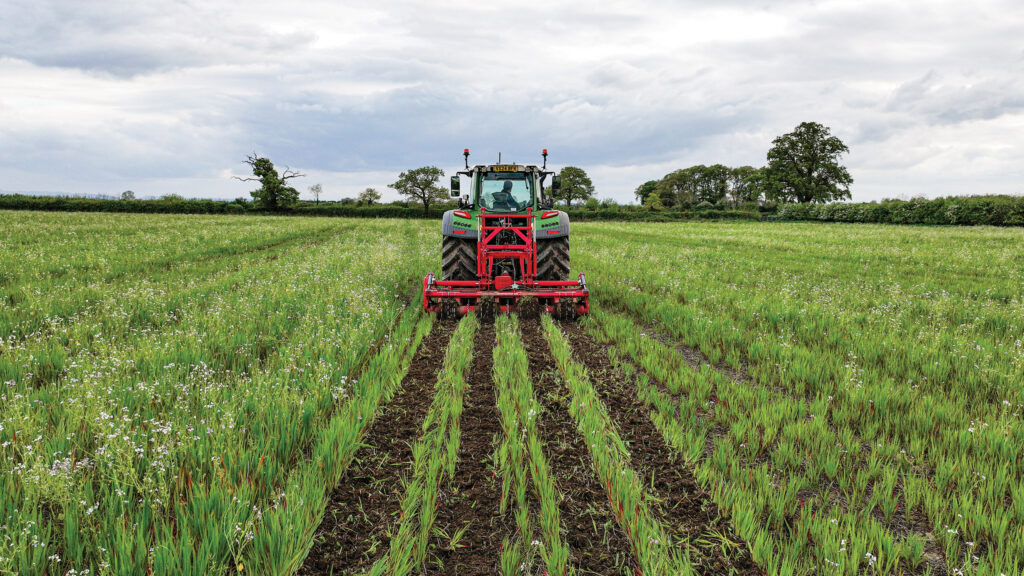
A four-row Weaving RotaStrip preparing a seed-bed © Weaving
The three sizes of RotaStrip tillers in Weaving Machinery’s range cover several configurations for cultivation and sowing or planting, using either two implements operated separately or brought together for a one-pass job.
Weaving reckons an 8-12kph working speed is suitable for such operations.
There are 3m four- and six-row versions, 4.5m six-row, and 6m eight-row models, all equipped with Weaving’s own Low-Disturbance winged subsoiling legs, which are protected by shear-bolts.
Fixed shields between each leg and group of cultivating blades aim to prevent loosened soil spilling out of the cultivated area on to the untouched ground, while rotor-mounted discs cut a clean edge to each of the tilled strips.
To finish, a segmented toothed packer roller consolidates the resulting seed-bed to retain moisture – especially where planting or sowing is carried out later as a separate pass – and provide a firm, consolidated finish for the planter or drill to work into.
Hydraulic adjustment of the 480mm-diameter packer roller provides infinitely variable cultivating depth control.
A 3m four-row RotaStrip weighs in at 2.3t, while the 4.5m six-row version comes in at 4.4t.
List price: RotaStrip 300/4 four-row 3m – £20,800; 300/6 six-row 3m – £24,800; 450/6 six-row 4.5m – £38,800; drill or planter hydraulic hitch – £2,650; 600/8 eight-row 6m – £42,800.