How Essex farmer adapted one cultivator to do four jobs
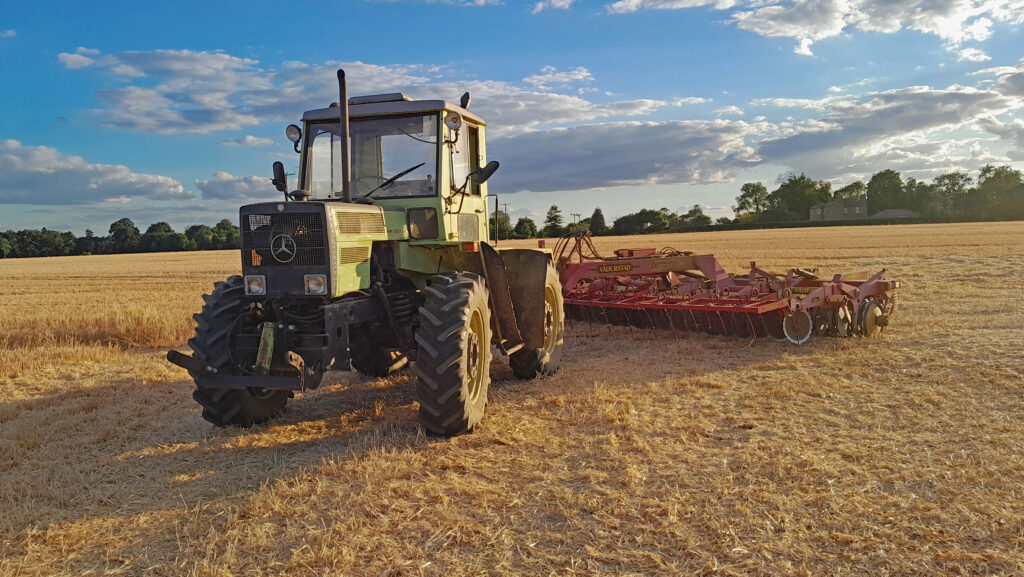
Armed with an ageing Vaderstad Carrier and yard full of scavenged parts, Andrew Metson has created a multi-use tillage tool that can also double up as a seeder.
Originally purchased with gangs of discs and a front straw harrow, the year 2000 machine was used for generating a bit of tilth ahead of the farm’s modified Weaving Sabre Tine drill.
See also: Farmers share kit ideas for sowing SFI seed mixes cheaply
It did a reasonable job of disturbing the heavy clay soils across his 60ha arable area near Ongar.
But when he realised how easy it was to remove and replace the cultivating elements, ideas came flooding in for how he could make it better.
“I’m a nosy bugger, so whenever I’m in someone’s yard I’m hunting around for old toot that I can make into something decent,” says Andrew.
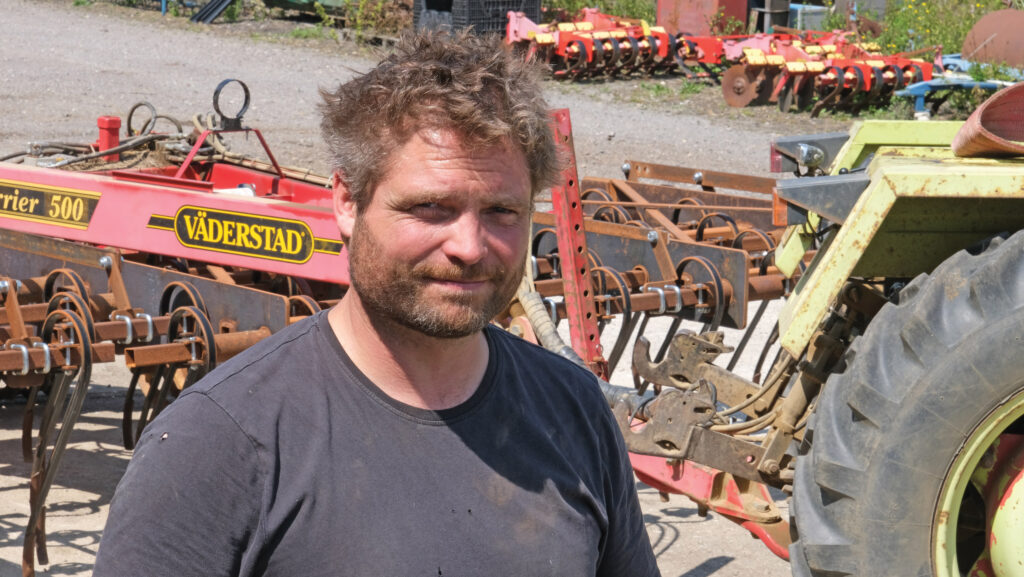
Andrew Metson © James Andrews
The first mod came after unearthing an abandoned front end off another Carrier at a local dealership.
From this he salvaged the levelling boards and a few rams, before building a frame to mount them in front of the disc units.
These make it more aggressive when doing a second pass where there are clods to bash up or when working on ploughed ground.
He also improved the effectiveness of the paddles by fitting alternate straight and cranked blades, as well and inserting a bar to lock them all together.
On the back of this success, he continued his budget procurement process, adding a full set of tough spring tines with rear levelling boards that bolt in place of the discs.
He doesn’t use these very often, but they’re handy for busting up baked ground or stiff furrows.
Straw rake
Most ambitious of his modifications was a project to convert the Carrier into a heavy-duty straw rake.
The hope was that this would hasten decomposition by evening out crop residues and breaking up lumps, as well as encouraging a blackgrass chit without burying brome.
Raiding Vaderstad’s back catalogue of bolt-on bits wasn’t an option this time, so he had to go it alone.
Picking the tines was the first dilemma, as he wanted something far tougher than those used by mainstream brands.
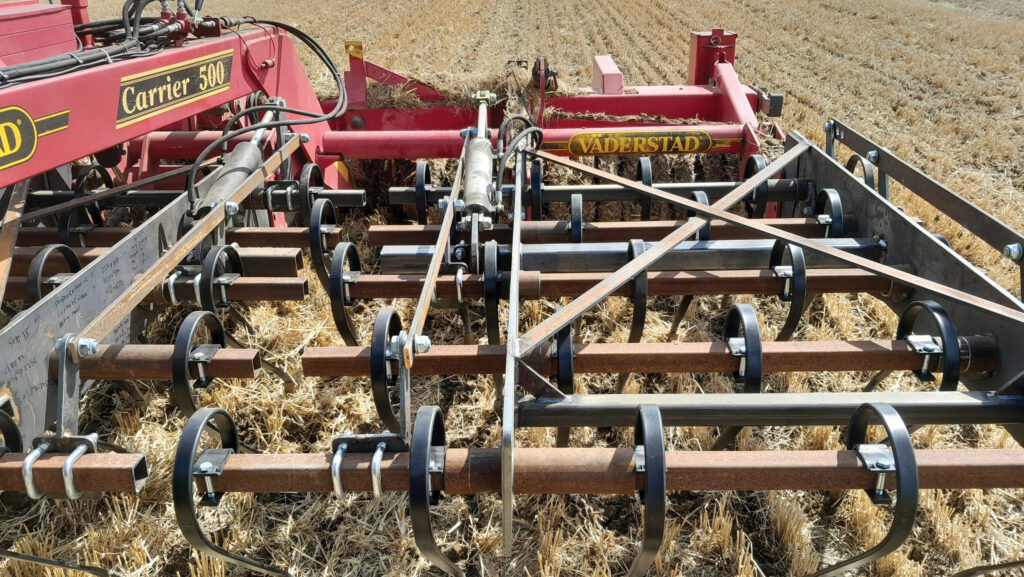
The Carrier as a stubble rake © James Andrews
His search eventually led him to France and the long spring tines that Techmagri uses on its Cultimulch machine.
With replaceable points, he hoped these would last longer than conventional straw harrow tines and move a bit more soil.
They were tricky to get hold of, though. “At one point it was looking like I’d need to order about 500 to get a delivery, but I eventually found someone who could help me import a few,” he says.
Next, he designed the carriers, which feature steel side plates cut out by local firm NCD Engineering and pivoting cross bars so that tine angle can be adjusted hydraulically.
To make sure no trash passes through unlevelled, these were fitted with a generous 65 tines, staggered over five rows to reduce the risk of blockages.
It works best at speeds of about 15kph, but it has to be timed carefully to get the best results, he says.
“People used to think that straw raking was a job you could do to keep busy on a wet day, but you just end up dragging it into lumps and making a mess. Instead, you want to go out when it’s so hot the straw is cracking.”
Having read some advice from Philip Wright of Wright Resolutions, he runs the tines as near vertical as possible, giving maximum disturbance at minimum depth.
Just like the original Carrier tool gangs, the straw tines are secured with just a couple of pins.
Complex plumbing
Plumbing the rams to raise and lower the gangs and alter tine angle was one of the most complex tasks.
This is because Vaderstad uses a volumetric system to ensure each ram in the circuit moves at the right time.
“You’ve got to get them arranged in order, otherwise it’ll do some very strange things – I had oil dripping everywhere when I first tried to set it up.”
To avoid such problems when switching the configuration of the machine in the future, these are now carefully colour coded.
Just two spools are required to operate the harrow, with one permanently plumbed to the raise/lower rams and another that operates the folding mechanism or tine angle adjustment, depending on the position of a diverter valve.
The hydraulics also allow the second and fourth rows of tines to be lifted out of work in damp or trashy conditions.
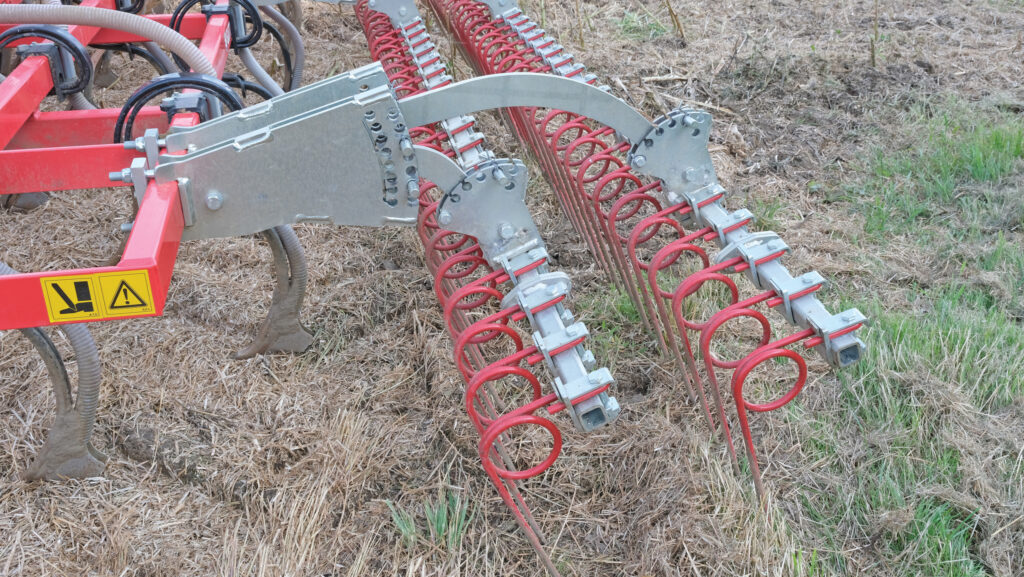
© James Andrews
Cover crop drill
The Carrier isn’t purely limited to cultivation tasks, as Andrew has created a kit to convert it into a cover crop drill.
This was built around its original disc configuration, with the seeding element put together almost entirely using bits carved off old Accord drills.
“I’ve got loads of parts I’ve collected over the years, most of which sit around as yard ornaments, but they do come in handy every now and again,” he says.
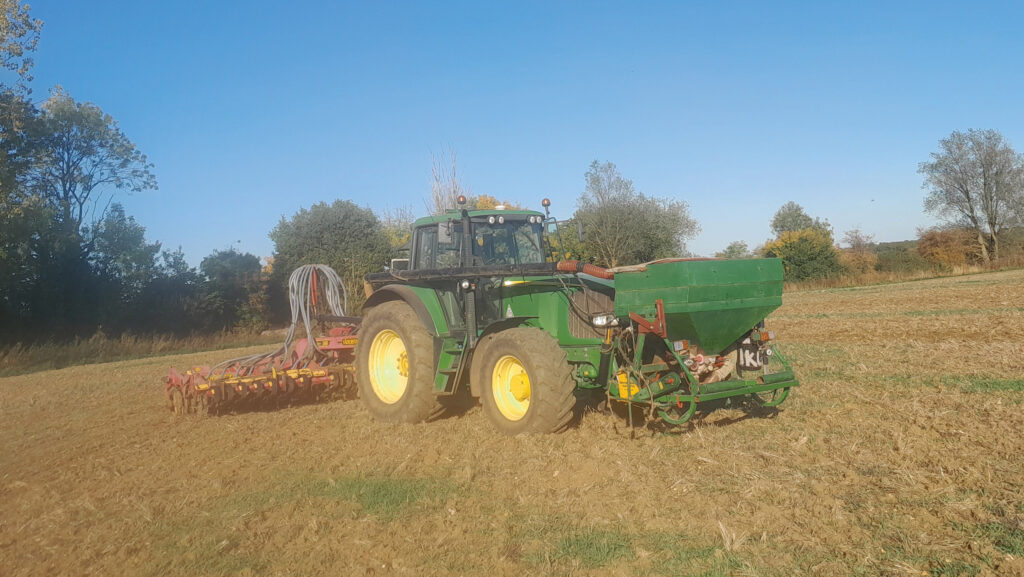
The Carrier in drilling guise… © James Andrews
One old hopper provided a distribution head, from which 19 pipes were routed to each of the rear discs.
Conventional drill pipe was used for most of the run, with short lengths of 25mm blue water pipe acting as the coulters.
These place the seed close to the ground, just behind the rear disc, ready for the packer to press them in.
As for the supply of seed, this comes from an Accord DF1 front hopper that his dad, Chris, picked up for just £250 as it had been used for applying fertiliser.
It was a bit worse for wear, but he tidied it up, gave it a lick of paint and fitted a metering unit from another of his old hoppers.
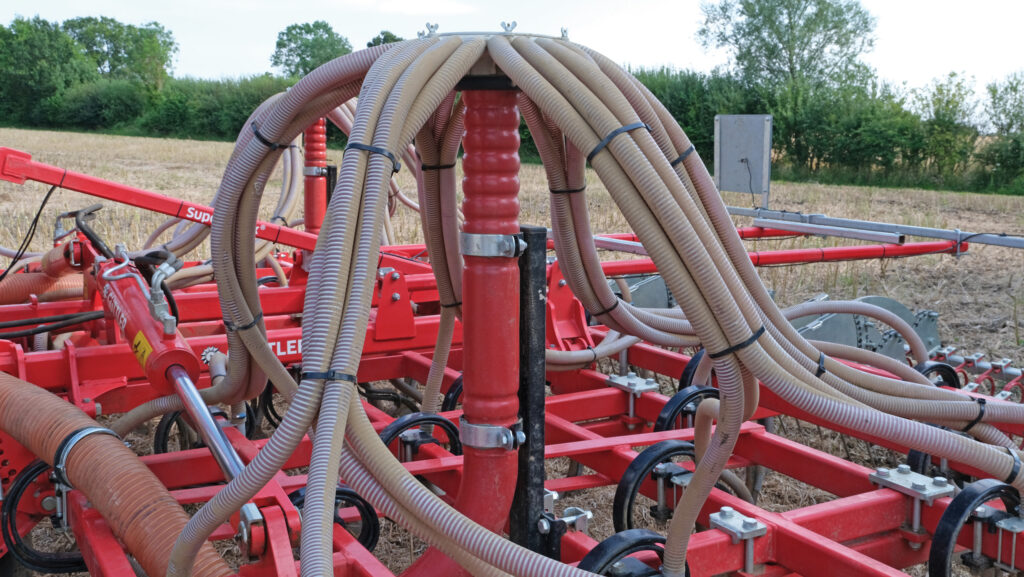
© James Andrews
Regular soil pipe was used to transfer seed up the side of the tractor, with just a few metres of large-diameter flexible hose required to negotiate the bends.
Andrew has used the outfit to successfully establish legume-based cover crops and has had his best results when it’s set to only work the ground lightly.
As a result, he is considering raising the height of the blue water pipe coulters so that they sprinkle seed from height, rather than place it near the soil surface in rows.
Other general modifications include adding a toolbox bracket, making two storage boxes for housing spare wearing metal and replacing the original electric depth stop with a hydraulic one.
This uses an adjustable plate to cut off oil flow to the rams when the front tool is at the desired depth.
He also made his own heavy-duty spanner for altering turnbuckles on the cultivating elements and adjusting the pitch of the whole machine.
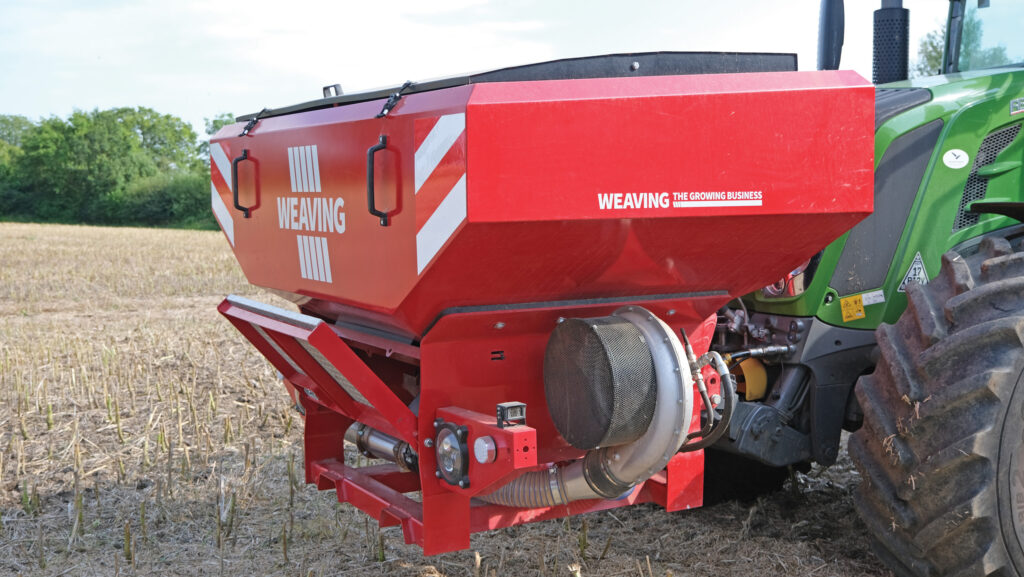
© James Andrews
Dual use hopper
Not one to have single-use kit lying around, Andrew also uses the Accord front hopper to feed the farm’s 5m Weaving Sabre Tine toolbar drill.
This was a failed prototype – the outsides of the wings would lift out of the ground during work – so they picked it up for just £7,000 a decade ago.
They came up with a budget fix that involved fabricating brackets to lock the whole frame solid in one 5m span.
Seeding depth might be a problem for those on undulating ground, but because Andrew’s fields are all flat it works just fine.
Most of the farm has been in a reduced tillage regime for 10 years or more, meaning heavy clay soils are sometimes in a fit state for the Sabre Tine to direct drill behind the straw rake.
However, the Carrier’s other cultivating elements are still required from time to time.
“We put some borage in for the first time this spring and we used both the disc and heavy tine setups to knock the ground into a decent seed-bed.”
Horsch FG
Despite the Carrier’s success, Andrew has another cultivator conversion project in his sights.
This time he’s after a Horsch FG, which he reckons will have even more potential for custom cultivation and drilling tasks.
“The attraction is that it runs Bourgault points, which would give me so many options for playing around with the setup,” he says.
“The only problem is they’re still a bit too expensive, so I’m keeping an eye out for one that’s in decent condition for a sensible price.”