Yorkshire farmer assembles a pair of tine drills for £10k
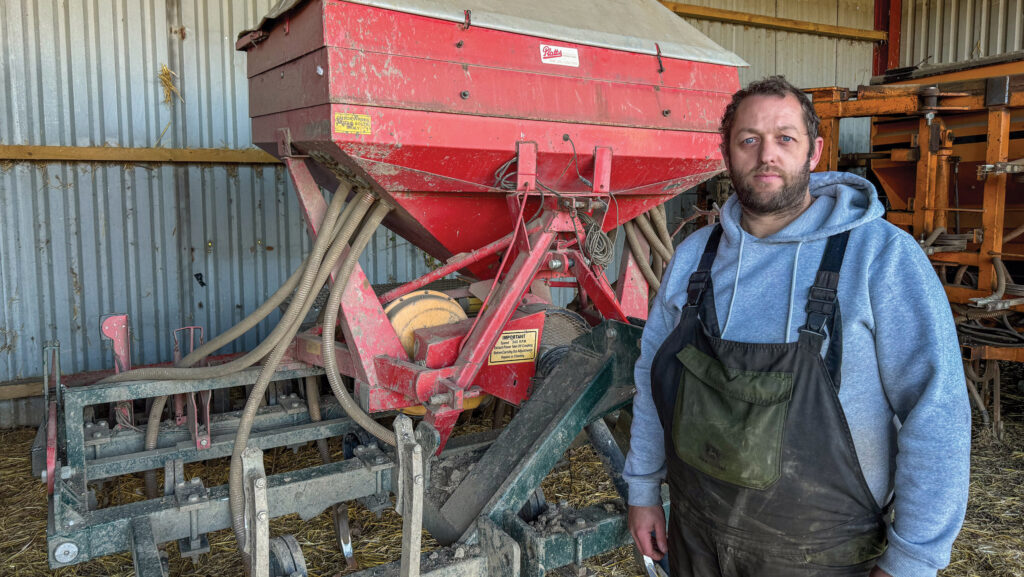
Recent autumn drilling campaigns have been a real slog for crop producers, with periods of extreme weather limiting work windows and leading to poor establishment.
And that’s all the more galling when you’ve spent big on a drill and the associated inputs – labour, diesel and wearing metal – to get seed safely in the ground.
See more:
These pressures are forcing many farmers to reassess their establishment systems in an effort to find something that is reliable, relatively low risk, and cost effective in a range of soil types and conditions.
Among them is Karl White, who runs a mixed beef and arable unit on the edge of Barnsley, South Yorkshire, alongside his father Stephen and son Jake.
Farm facts: JC White & Son, Dodworth, Barnsley, Yorkshire
- Farm size 225ha, predominantly heavy clay
- Cropping Wheat, barley and beans, plus 40ha of grass for equine haylage
- Livestock 120 barley-fed store cattle for a local farm shop
- Staff Karl, father Stephen and son Jake, plus one other during peak periods
Heavy land
Wheat, barley and beans are grown on heavy clay land, and in sticky years, the plough and power harrow combi drill system favoured by his father for decades remains the most reliable method of establishment.
However, it’s time consuming and expensive, as the ground has to be worked down after ploughing, then drilled – a process that involves at least three people.
A tine drill seemed the obvious solution but, rather than shelling out up to £40,000 on a brand-new machine, he decided to have a go at putting his own together.
He already had a suitable donor – a 3m pig tine cultivator purchased from an online auction for £500.
This was originally earmarked for use post-combining to lightly scratch stubbles and encourage a chit of weeds for spraying off.
With some inspiration from his agronomist, Andrew Kealey, he set about transforming it into a drill by mounting a trusty Accord hopper and the associated pipes, seed boots and land wheel-driven metering system.
Not one for technical drawings, Karl simply made a mental plan before attacking the metalwork.
The trickiest part, he says, was working out how to fit the drilling kit on the cultivator’s frame.
For starters, the headstock needed beefing up to handle the extra weight, and he had to ensure there was enough space to avoid the pto shaft, which drives the fan, clashing with the frame when lifting and lowering.
There was also a bit of jiggling required to maintain access to the bottom of the metering unit for emptying the tank.
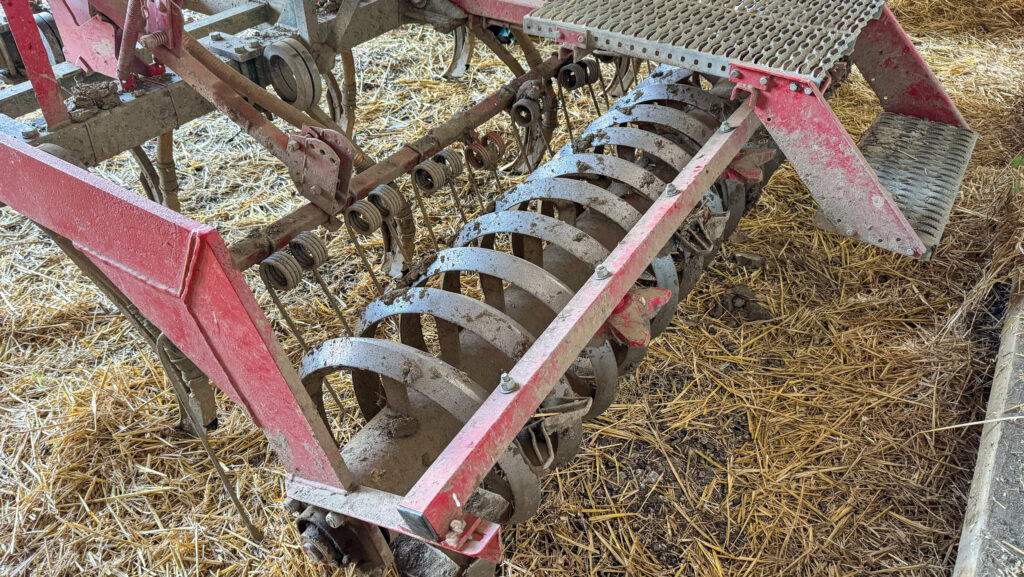
© Adam Clarke
Lightweight roller
The drill has 13 tines on 230mm rows, with these finished by a light coil packer rather than a heavy roller that would be liable to overconsolidate the soil, leading to capping.
This still firms the ground up enough for decent seed-to-soil contact and minimal slug risk, but the star-type cleaners fitted aren’t always up to the job of keeping the roller free of debris.
“Conditions have been atrocious over the past couple of seasons and that sometimes causes the centre of the coil roller to bung up, so that’s one thing I’ll definitely change – I don’t want to be getting out to clean it.
“Someone suggested a Guttler-type roller, but I think that might be a bit heavy,” says Karl.
One modification already completed is the addition of wheel track eradicators, with four leading tines taken from a recently acquired 6m Simba Freeflow and mounted behind the wheels on the front of the frame to maintain a uniform sowing depth.
Comparable yield
The drill covered about 180ha in 2023, sowing most of the barley and wheat, and some beans, directly into stubble in combination with a front-mounted Kongskilde Terra Disc.
Happily, a side-by-side comparison in a field of wheat showed no significant yield difference compared with the usual plough and power harrow combination system.
Autumn 2024 was a slightly different story, with the old regime called into action to deal with the ruts left from a wet harvest, and heavy rain from early September.
“We had to turn land over in places to get it to drain, so we went through with the power harrow combination drills we have.
“But where the tine drill was used, it worked well – I was doing 16-20ha a day, and I could do a couple of days on a single tank of fuel, so it saved significant costs.”
More capacity
As successful as that setup was, Karl decided he needed to go bigger in order to cram as much drilling as possible into increasingly short weather windows.
He tracked down a Simba Freeflow for sale locally for just £2,000 but, at 6m, his John Deere 6210R wasn’t going to be powerful enough to pull it – especially on his steepest fields.
So he set about chopping it to a more manageable width, something that proved more complex than expected.
His original plan to lop a metre off each folding wing was scuppered when he realised that it would involve a lot of work and expense, as the folding rams on the front and rear platforms would need replacing with shorter alternatives.
So, instead, he went to the narrowest width possible without interfering with the ram pivots – 4.8m – by cutting 500mm out of each folding frame.
But he did have to reposition the rams that pressurise the rear tyre packer and control seeding depth, moving them to the outside of each wing.
A piece of box section, reinforced with some 12mm steel plate, was welded to the outside of the frame to accommodate their mounts.
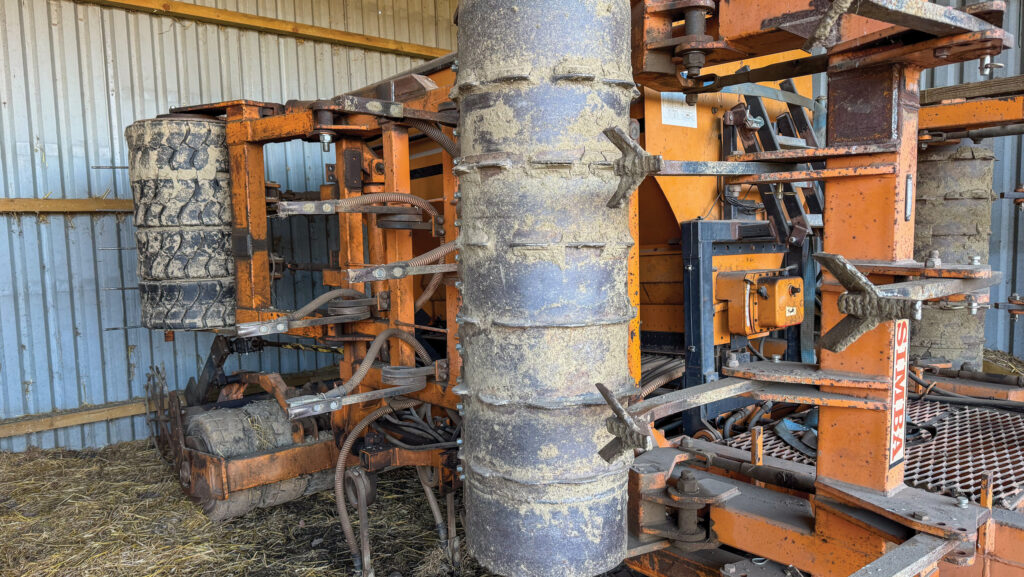
© Adam Clarke
Reconfigured packer
Perhaps the trickiest part, though, was chopping down both the steel rollers that sit behind the machine’s leading tines, and the tyre packers at the back.
The front roller had to be cut in a way that ensured the welded roller fins aligned with the home-made winged leading tines, the latter designed to work about 150mm deep and lift any surface compaction out of the seeding zone.
The scraper system also needed a slight rejig to ensure it didn’t clash with the roller fins.
When it came to the packer, the back actor of Karl’s JCB 3CX was used to strip the stubborn old tyres off the shaft, ready for it to be cut it down.
Replacement rubber came from Newark-based Tanvic Tyres, with various width of forklift tyres used to match the length of the truncated shaft.
The final major alteration was to the hopper. As Karl decided to set the drill up on wider rows than it was originally designed for – 21 tine coulters at 200mm spacings – a good number of the hopper outlets were redundant and blocked off.
Left as it was, there was a danger that some coulters wouldn’t be fed if seed ran down unevenly, so Karl split the tank with some mild steel sheet and shifted all the pipework to the foremost outlets.
As slugs are an issue on his heavy ground, the idea is to use the slightly smaller rear half of the hopper to apply pellets during drilling, with a Y splitter combining them with the seed just before the boot.
Challenging project
The Freeflow project took about three months to complete and cost a total of £5,500 – the most expensive items being the new forklift tyres on the short rear packer sections.
Wet weather meant it wasn’t involved in the autumn drilling campaign, but it has been used to sow some cover crops.
“It should allow us to get on a lot quicker – we could probably cover 40ha a day on some farms.
“We’re a bit restricted by our field sizes here – some are only 2ha – but it’ll easily do our biggest 20ha field in a day plus a bit more, so I’m quite happy with how it’s turned out,” Karl concludes.
Get involved
Farmers Weekly’s annual Farm Inventions Competition is open for entries, and you could be in with a chance of winning one of nine cash prizes totalling £2,550.
Whether it’s a simple time-saver or a monster project, just send a few pictures and some basic information about how it works to oliver.mark@markallengroup.com. Closing date is 24 January 2025.