Farmer saves cash by 3D printing parts for home-built drill
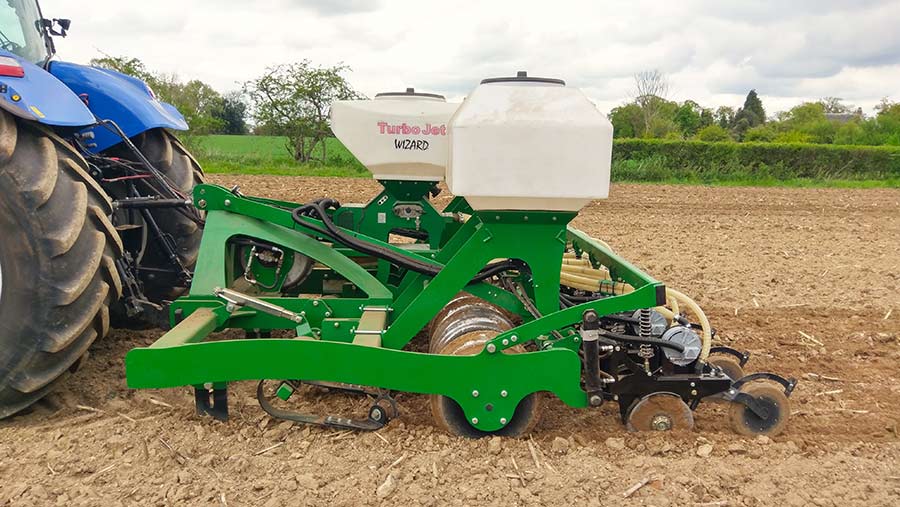
Farm workshops are a brilliant starting point for heavy-metal machinery projects but, for inventions requiring delicate components, there’s inevitably a point at which home-builders have to resort to buying bits off the internet.
But that’s not so for Jonny Leech, a Norfolk farmer and self-employed designer who decided the shrewder move was to buy his own 3D printer that would allow him to churn out plastic parts of any size or shape on the cheap.
His motivation for investing a princely £175 in the clever printing kit was to develop a precise maize seed metering system that would improve the farm’s patchy forage maize yields.
See also: 10 single-pass cultivator options for heavy land
The printed plastic parts were the first part of a jigsaw that also involved making his own subsoiler-style chassis combined with a quality stash of components found around the farm, including old coulters, DD packer rings and a Stocks Turbo Jet applicator.
Last year, prior to embarking on the project, he tried sowing the farm’s forage maize crop using a regular Great Plains Centurion configured to 50cm-row spacings to determine the impact of drilling without seed singulation and precise in-row spacing.
Sadly, a severe lack of rain savaged yields anyway, but it grew enough to conclude that plants in close proximity to one another were weaker than those with more space.
And the process of blocking rows on the drill’s distribution head played havoc with the air stream, leaving clumps of plants to compete with one another.
Decision made; singulation of the seed was key to consistent crop performance – he just had to design a drill fit for the job.
Singulation system
Most maize metering systems use a vacuum to suck seeds into recesses dotted around a speed-regulated rotating disc.
Operators can then adjust the in-row spacing by altering the speed at which it whizzes round.
The drill-making big guns have this system down to a fine art, with Vaderstad claiming to be able to singulate maize seeds at barmy speeds of up to 20kph on its high-capacity Tempo.
However, off-the-shelf versions are unpalatably expensive when bought in low quantities.
Typical prices can hit £500/row, which would have blown Mr Leech’s budget before he had started on the machine’s metalwork.
Instead, he used his experience from a two-year spell as a design and test engineer at Great Plains (prior to the closure of its Lincolnshire factory) to draw up the system using 3D software package Solidworks.
The plans were then transferred to the printer, which created them as three-dimensional models by squirting heated plastic through a tiny nozzle to form a stack of 0.2mm-thick layers (see box, 3D printing explained).
Testing phase
The most challenging part of designing the disc-based singulator was finding a way to control the vacuum so that each seed is released down the tube at a precise point, says Mr Leech.
In the end, he settled on a scheme that works conversely to most other singulators by sealing the non-vacuumed quarter of the disc to a neutral pressure.
However, he has since found a plastic compound that his printer is able to form into a flexible seal, so future versions will have more traditional three-quarter air-proofing.
A pressure gauge on the vacuum manifold helped set the hydraulic fan to provide the perfect pressure for pulling seeds on to the disc without having doubles and misses, and little plastic singulator teeth help to knock off any unwanted hangers-on.
As Mr Leech worked through the dozens of revisions and tweaks, he decided to rig up a test bed to check performance. To do so, he salvaged a window wiper motor to rotate the disc and a redundant hoover to form the vacuum.
And 15 prototype designs later, he had a unit that performed to 99% singulation accuracy at 12kph, which was ample given it would be mounted to a slow-moving subsoiler.
It then took three months to print the parts for all six rows but, at £60 in total, cost a fraction of bought-in equivalents.
JL Design maize planter
- Width: 3m
- Subsoiler legs: Six
- Working depth: 14in
- Hoppers: 2x 400-litres
- Openers: double-disc
- Row spacing: 50cm
- Metering: disc-based singulation system
- Power required: 200hp
- Working speed: 8kph
- Build cost: £10,000 (coulters, Stocks applicator, packer rings and other components were of no cost)
Feeding the disc
The disc’s ability to pick up and singulate seed is compromised when there are too many or too few available, so managing the size of the seed pool that sits against the turning disc was crucial.
To keep a steady feed, Mr Leech mounted a proximity sensor in the singulator’s plastic housing, which speaks to a cruder metering system further up the chain.
By adjusting its sensitivity, he was able to regulate the amount of seed dropped down to the disc.
In real working conditions, it constantly flickers on and off as seeds arrive and depart, balancing the supply of seed with the demand of the singulator.
As the seed pool level drops below the sensor, it engages a triple-pocketed metering cup that drags seed from the main hopper over a lip and into the airstream produced by the fan, which carries it to the singulator’s holding bay.
Driving the singulator
To keep things cheap and simple, each singulator unit has a chain-and-sprocket drive from the rear press wheels.
The driven side (nearest the ground) uses a stainless-steel sprocket, but the one at the other end of the bicycle chain is 3D-printed and made of plastic, which means Mr Leech can manufacture a stock of gear options to alter the sowing rate.
Amazingly, the plastic sprockets managed 70ha without showing any signs of wear. And the perk of using plastic is that it will break if something jams, which may save damaging something more valuable further up the line.
Drill design
Mr Leech’s plan initially centred around building the metering system – the key element in achieving sowing consistency – but once its accuracy and reliability was proven, the focus switched to the chassis and drilling components.
As the farm lies on drought-prone land and maize is a notoriously lazy rooter, he decided to go for a strip-till system incorporating a subsoiler leg – a setup that would also lend itself to planting sugar beet and oilseed rape.
He settled on a fairly simple 3m mounted unit and commissioned a local fabricator to laser-cut and weld the chassis he had designed.
The general layout mirrors that of a regular subsoiler, with six legs staggered across two rows to loosen directly underneath the seed.
These carry Sumo’s low-disturbance, narrow-winged GLS grassland points for maximum shattering but limited soil heave to avoid pulling too many clods to the surface.
Working depth tends to be set at around 14in but can be adjusted by way of holes on the legs, which means the position of the packer and coulters on the main frame remains consistent.
Star-shaped wheels trail each leg to flick trash from the rows and minimise the risk of hairpinning, and the packer element is made from old DD rings welded into pairs.
These close the slot behind the leg and keep the ground as flat as possible ahead of the seeding element.
Coulter assemblies
A Great Plains Centurion was raided for its double-disc assemblies and main coulter bodies, but their rudimentary single-pivot arrangement had to be replaced with a parallel linkage.
This helps to keep the maize coulter running level and encourages seeds to fall vertically to the trench without hitting the tube’s walls, which would otherwise compromise the consistency of in-row spacing.
The linkage attaches directly to the chassis so, as long as the top link of the machine is adjusted correctly, the units should always run level.
Each row also has its own compression spring, which maintains downward pressure but offers a degree of contour following.
Mr Leech tried to 3D-print his own seed tubes to run down the back of the double-disc openers, but his fairly low-grade printer left plastics with a slightly grainy finish so, instead, he bought the same drop tubes and seed sensors as used on Great Plains’ planters.
Although his tests indicated that the cells in the seed disc filled reliably, he fitted an LED counting sensor half way down each tube to monitor exactly what was going into the ground.
At £130/sensor, it was one of the more extravagant expenses but, with precision the priority, they were essential for monitoring each row’s real-time seed population and displaying it on a Dickey John PM300 screen.
It also has an alarm facility to alert the operator if the target seed population – 115,000 seeds/ha in Mr Leech’s case – strays outside of a set boundary.
A second, home-made control box allows individual row shut-off using simple toggle switches and relays that talk to the singulator’s proximity sensors, which is important for tramlining.
Granular fertiliser
Jonny Leech’s drill also has the capacity to apply micro-granular fertiliser directly in the row with the seed, which he hopes will promote early rooting.
He has fitted a Stocks Turbo Jet to plates on the main chassis, which allows him to apply Primary-P starter fertiliser – made up predominantly of phosphorous – at 20kg/ha.
Its six outlets are hosed up to the rear drop tubes on the row units and the product is blown into the trench to mix with the seed.
Early results
The drill immediately trimmed what was a four-pass system to just two. However, the current establishment method involves applying pig and poultry muck that has to be incorporated to adhere with cross-compliance rules, so it’s not possible to run a true strip-till approach.
That said, replacing muck applications with liquid digestate would make a single-pass system feasible.
So far it has covered 70ha and, in most places, the crop hit germination rates of close to 100% despite tricky post-drilling conditions that caused soil capping.
The singulator proved consistent, says Mr Leech, particularly as it was only working at 7-8kph – the equivalent of 12 seeds/sec on each row.
However, he does intend to change the existing 2in-wide press wheels to 4in concave-shaped versions so the ground around the seed is pressed but the area directly above it is left relatively loose.
This should reduce unnecessary compaction caused by the high downward pressure, which he applies to make sure the drive to the metering units is consistent.
The farm also plans to run trial plots for oilseed rape this autumn that will help determine whether small seeds are worth singulating.
He’s already developed a new singulation disc with microscopic holes to pick up the rape seed, with the aim of sowing them roughly 5cm apart at a rate of 40 seeds/sq m.
3D printing explained
The concept of printing plastic to form 3D structures may seem a funny one to fathom, but it has become an easy way for hobbyists and large-scale manufacturers alike to form relatively complex shapes from CAD drawings.
It works by feeding melted plastic through the nozzle tip of a robotised arm to build vertical layers and starts on a glass-covered base to prevent the workpiece from warping.
Mr Leech’s kit is one of the cheapest versions available – it was just £175 – and arrived in kit form.
However, budget models are limited by the range of plastics they can work with and lay thicker horizontal sheets (in this case, 0.2mm thick) so the end result tends to have a scratchy, unpolished finish.
These systems are perfect for prototyping as the plastic costs peanuts to buy, but the catch is that users must be comfortable with CAD modelling or be able to source their designs from elsewhere before loading them into the printer.
In the future, designers may offer their drawings for sale, which could allow farmers with a 3D printer to manufacturer their own replacement parts.