Farmer converts Simba Freeflow to low-disturbance drilling for £7,500
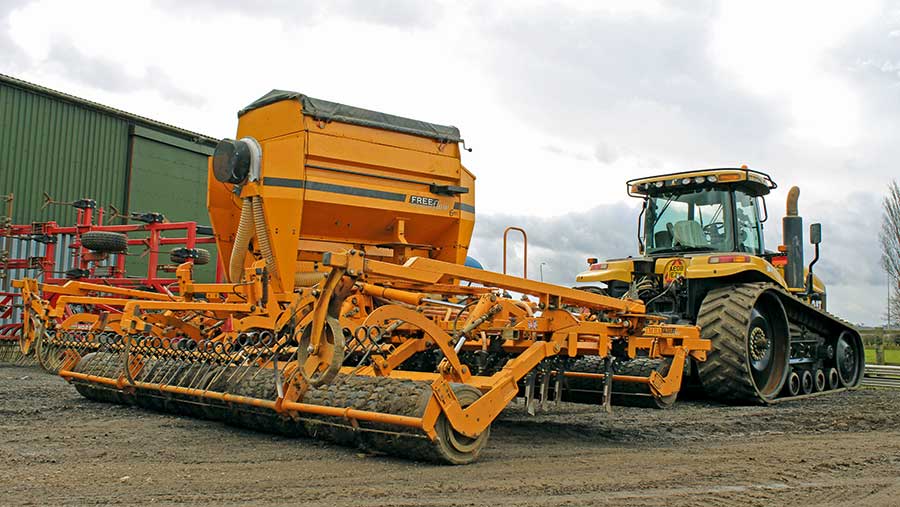
Faced with a rising battle against herbicide-resistant blackgrass, Lincolnshire farmer Nick Wade decided that a switch to low-disturbance drilling was his best bet for getting the troublesome weed under control.
But with price tags for suitable 6m drills running into the tens of thousands he was starting to go off the idea, particularly with current cereal prices.
However, after going to view one of Weaving Machinery’s Sabre Tine drills – and liking the look of it – he wondered if he would be able to modify his trusty, nine-year-old 6m Simba Freeflow to work in a similar way.
See also: Farmer builds £24,000 strip-till drill from scratch
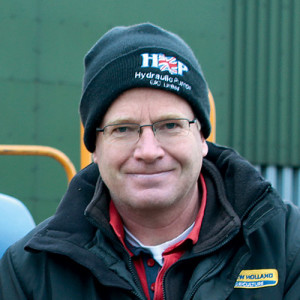
Nick Wade
“The Simba has been a brilliant drill with rock-solid build quality and my only real complaint was that it moved too much soil,” says Mr Wade. “But after a chat with Simon Weaving we realised it would be relatively easy to convert the drill to run Sabre Tine coulters.”
Back at the farm workshop, the first job in the conversion process was to unbolt all 48 of the Simba’s original pigtail tines and come up with some bracketry to hold the Weaving replacements.
Because these were considerably shorter than the originals, Mr Wade and driver Steve Loomes decided to fabricate a sub-frame that would be welded under the drill’s original chassis.
This was made up using flat steel for the side plates with a diagonally-mounted box section running between them for the rubber-mounted tines to clamp on to.
After a bit of thought, they also decided to drop the number of coulters from the original 48 to 36 and mount them in three rows rather than four.
“That gave us a 0.5m spacing between coulters on each row, meaning soil disturbance was kept to a minimum,” says Mr Wade.
The drill’s front row of loosening tines was also removed so that the drill wouldn’t work the ground at all before the coulters passed through.
Once the tines were sorted, the next step was to get the metering and control systems up to date. This involved fitting a new RDS seed roller drive motor, a GPS speed sensor (to replace the old metering wheel) and an RDS Artemis control box.
“All this has put it up there with a lot of the latest drills on the market and we can now do variable-rate seeding if we want to,” says Mr Wade.
“The RDS drive motor is also much tougher than the original so it can cope when we are drilling beans at 300kg/ha to try to smother the blackgrass.”
In total, the conversion tipped the balance at about £7,500. That included £3,200 for the tines, £3,000 for the RDS kit, £500-worth of steel and about £800 in labour and sundries.
The project was completed ready for last autumn and its first job was to plant 600ha of cereals and 80ha of oilseed rape into ground that was prepared by a brace of Horsch Terrano cultivators.
Abbey Farm, Sedgebrook, Lincolnshire
- Farmed area: 1,000ha
- Soil type: Mainly heavy clay
- Cropping: Wheat, barley, oilseed rape
- Tractors: Caterpillar MT865B plus John Deere 8345, 7530 and 6820
- Drill: 6m Simba Freeflow with Weeving low-disturbance tine conversion
- Combine: New Holland CR9090 on tracks with 35ft header
- Sprayer: Sands Vision with 4,000-litre tank and 30m booms
- Telehandlers: JCB 531-70 and John Deere 3400
The results were much better than expected. “The drill sits dead level, pulls really straight and doesn’t move the soil anywhere near as much as it did before,” he says. “And because there’s only about 30% of the metal we used to have in the ground, it burns a lot less fuel.”
At the moment the drill is still being pulled by the farm’s hefty 550hp Cat MT865B, even though a 200hp machine would probably be up to the job. That’s party because the Challenger is needed for higher-horsepower cultivation jobs and it’s not worth investing in another tractor, says Mr Wade.
“When we bought the Challenger it was a bit of a bargain, so we would probably end up spending more money to get a lesser machine,” he says.
“Even though it’s heavy it makes very little mess (once you work out how to turn neatly on the headlands) and because it’s under no strain whatsoever, fuel use is pretty low, too.”
In dry conditions the Challenger has been burning around 6 litres/ha of diesel when pulling the converted drill, rising to 10 litres/ha in the wet.
That’s about 25% less than it was using before the conversion. Mr Wade says the difference in fuel used in the wet is largely due to the scrapers acting like a big handbrake when they gum up with sticky soil.
Dale Simba conversions
- Converting cultivator drills such as the Simba Freeflow to low-disturbance drilling isn’t a new concept.
- For several years direct-drilling specialist John Dale has been offering kits to convert existing machines to run on to zero-till seed-knife coulters or its Eco Drill coulters.
- On a 3m drill, these reduce the power requirement to about 60hp, rising to about 160hp for an 8m machine.
- Dale sells the kits for farmers to do their own conversion – but for those less familiar with spanning, it will do the full conversion.