Custom OSR drill applies multiple products at variable rates
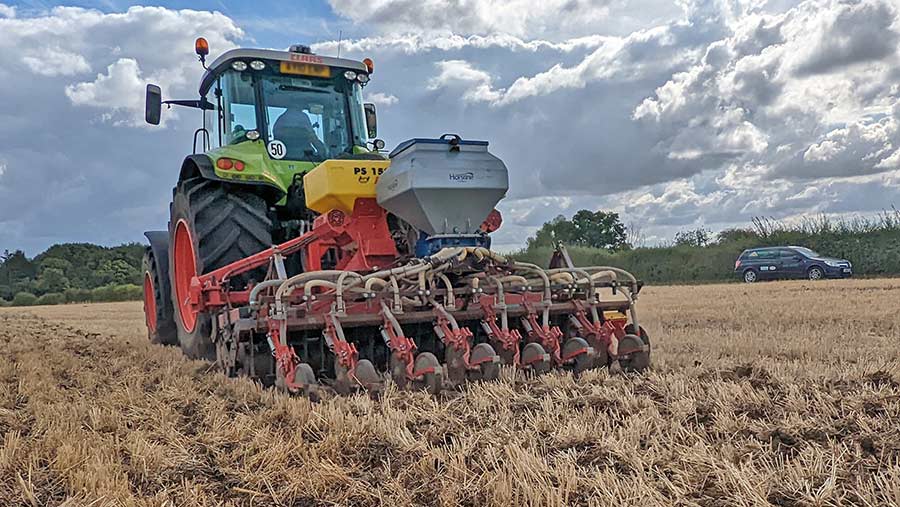
Growing a high-risk crop such as oilseed rape requires a reliable yet cost-effective method of getting seeds in the ground.
On the one hand, the plants need to be given the best possible start but, with the risk of failure ever present, it can’t be too costly and time-consuming.
Will Mumford, a Cambridgeshire farmer and founder of precision farming specialist AS Communications, found himself facing this dilemma.
For years he had been using a conventional method to establish the crop on his heavy clay soil, involving a Vaderstad Topdown and a couple of passes with a power harrow, before drilling with a Vaderstad Rapid.
See also: Bespoke Stripcat drill expands companion cropping options
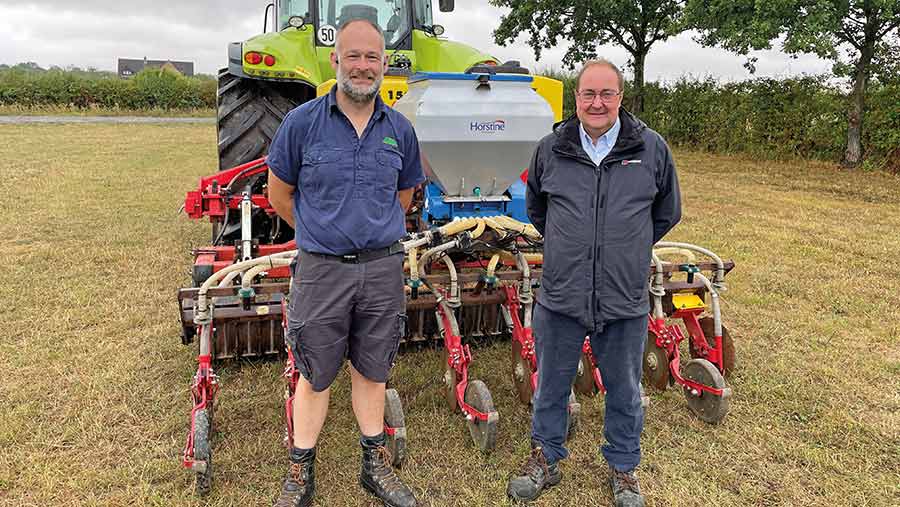
Tom Carnell and Will Mumford © James Andrews
It was a laborious and expensive technique, but it used to give decent results. However, after having two crop failures back-to-back and a poor result the year after, he decided to switch to a single-pass system.
His plan was to use a low-disturbance subsoiler to loosen the ground but, rather than scatter seed on the surface, sow it accurately with a coulter.
At the same time, he wanted options for applying a liquid starter fertiliser, sowing a companion crop in the inter-row and applying slug pellets or sulphur granules.
Due to his precision farming background, he was also keen for it to be Isobus-controlled, with the ability to apply variable rates and produce application maps that could be loaded into his farm management software.
To bring the complex machine to life, he enlisted the services of Tom Carnell from Tramline Tec, who specialises in putting electronic systems together on agricultural machinery, as well as carrying out traditional fabrication work (see “Tramline Tec”).
Tramline Tec
After years of working as an engineer in agriculture, food processing and pharmaceuticals, Tom Carnell set up his own business called Tramline Tec in 2021.
Through this he specialises in fitting and modifying electronic systems on agricultural equipment, as well as undertaking more traditional fabrication.
Precision farming systems, Isobus and Canbus – things that cause most people to break out in a cold sweat – are his bread and butter. This means he can upgrade older equipment to new standards, simplify complex controls to make them more user friendly, and fit out new machinery.
As an agent for MC Electronics, he also rigs up plenty of blockage sensors and seed-counting systems to drills, particularly John Deere’s 750A.
These alert the operator as soon as the flow starts to drop in one of the outlets, so blockages can be spotted before they cause a real problem.
The counting function also gives an accurate basis for planting seeds by the square metre, rather than working it out from the thousand grain weight.
Prices start at about £2,000 for the ECU and ancillaries, with blockage sensors costing about £130 each and counting units about £150.
Building it
The starting point for the project was a 3.2m Quivogne Pluton subsoiler with six legs set at about 50cm.
This was wider than Mr Mumford likes for seeding oilseed rape on his clay soil, so Mr Carnell set about adding two extra legs and reducing the spacing to 40cm.
To do this, he designed some mounting brackets using CAD that allowed the extra legs to be fitted and the spacings adjusted without having to cut or weld the frame.
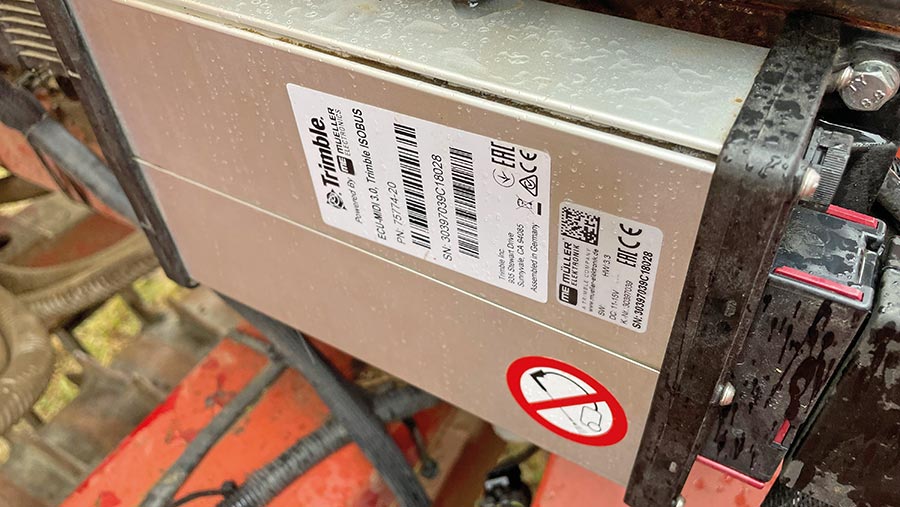
Muller ECU ©James Andrews
In a bid to reduce soil heave and disturbance at the surface, the original legs were replaced with low-disturbance alternatives from Pan Anglia.
These came with a 6in (152mm) wing, but initial tests showed that they moved too much soil, so they were nipped down to 5in (127mm).
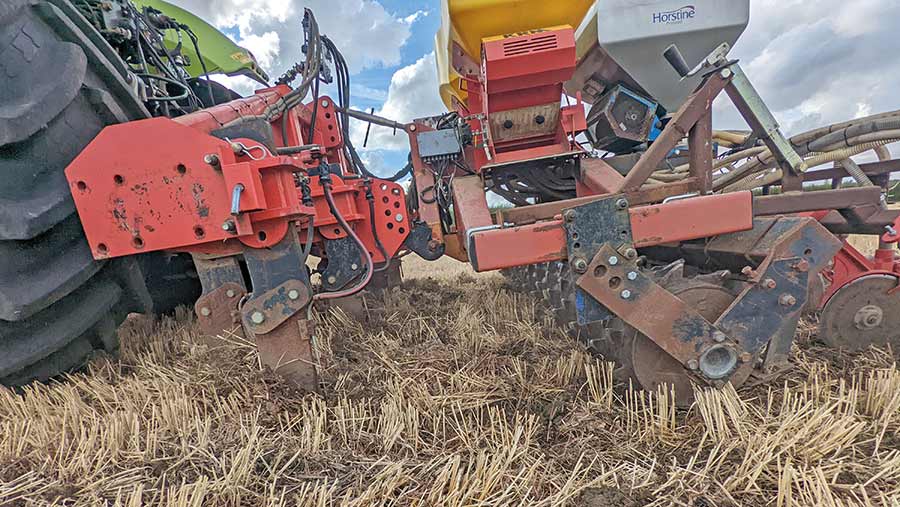
Seeder in work © James Andrews
The Pluton’s factory-fitted Flexi-Coil was also swapped for a toothed packer roller after it blocked solid during its first few outings.
For seed placement, they sourced a set of Weaving double-disc coulter assemblies with integrated press wheels, six of which they managed to find second-hand, and two they had to buy new.
These were mounted on a bar at the rear of the packer roller – in line with the subsoiling legs – which has a turn adjuster for altering seeding depth.
With three solid products to apply, separate electro-pneumatic seeder units were mounted on the top of the chassis.
A Horstine Proseed meters out the oilseed rape and pipes it to the disc coulters, while one APV unit sends companion crop seed to spreader plates mounted in the middle of the inter-row.
The other is piped to some straight delivery tubes, which dribble slug pellets or sulphur fertiliser just to the side of the crop row.
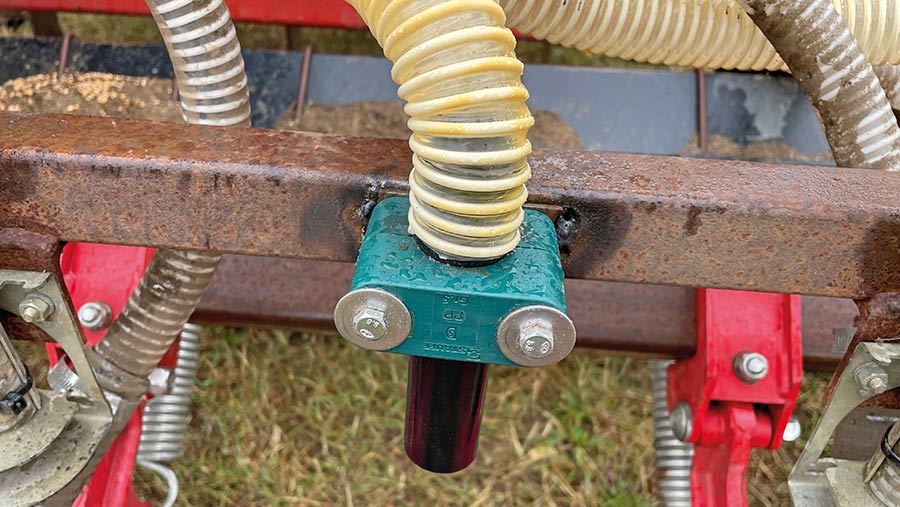
Delivery tube © James Andrews
The final part of the setup is the liquid fertiliser system, which uses a 1,250-litre Hardi front tank connected to pencil jets mounted on the back of the subsoiler legs.
These are set so they place the fertiliser just below the seed, meaning roots can grab hold of it as soon as they start to grow.
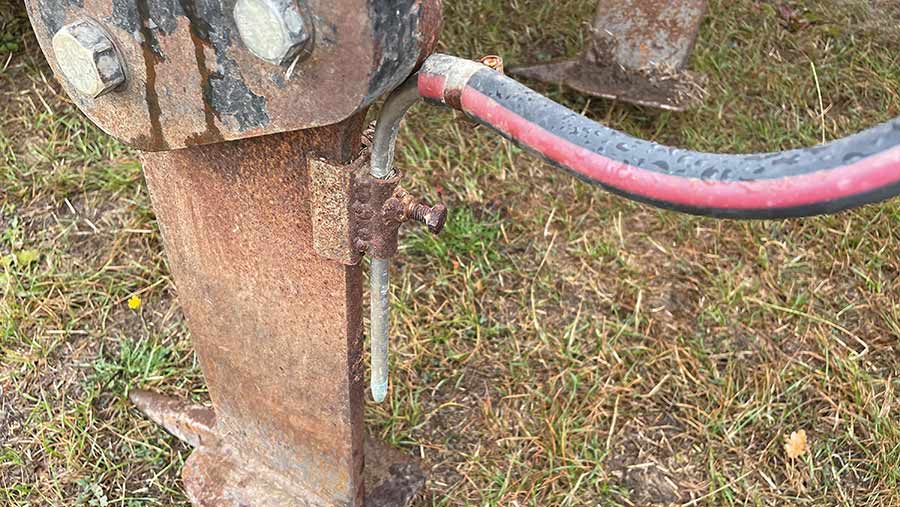
Liquid fertiliser jets © James Andrews
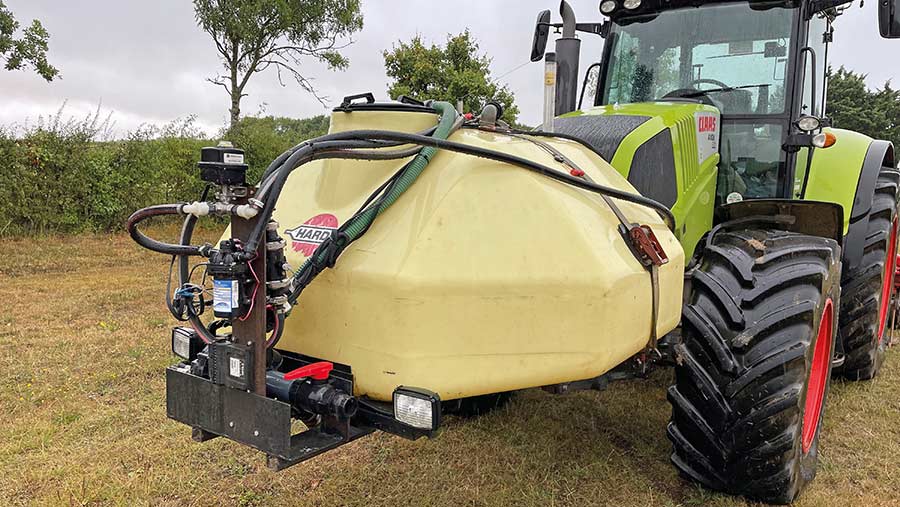
Liquid fertiliser tank © James Andrews
Electronics
The electronics are what makes this drill stand out from most other home-made seeders of this kind.
Typically, small-seed applicators come with their own simple control system, but Mr Carnell has bypassed this, connecting the drive motor and speed controller for each unit to a Muller Isobus ECU.
The result is that all three can be set up and monitored from a single Trimble GFX-750 screen in the tractor cab.
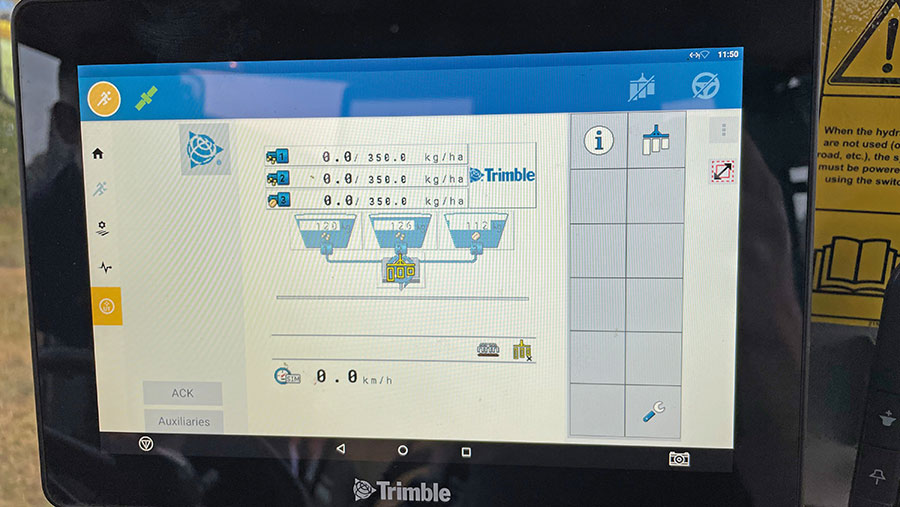
Trimble GFX-750 © James Andrews
Thanks to the fact that seed is individually metered to each outlet, these units give more accurate delivery than a conventional drill with a single distribution head.
The Horstine goes a step further than the APV units, as it has a fixed-displacement metering system that maintains accuracy at low seed rates. That’s why it was put in charge of oilseed rape placement.
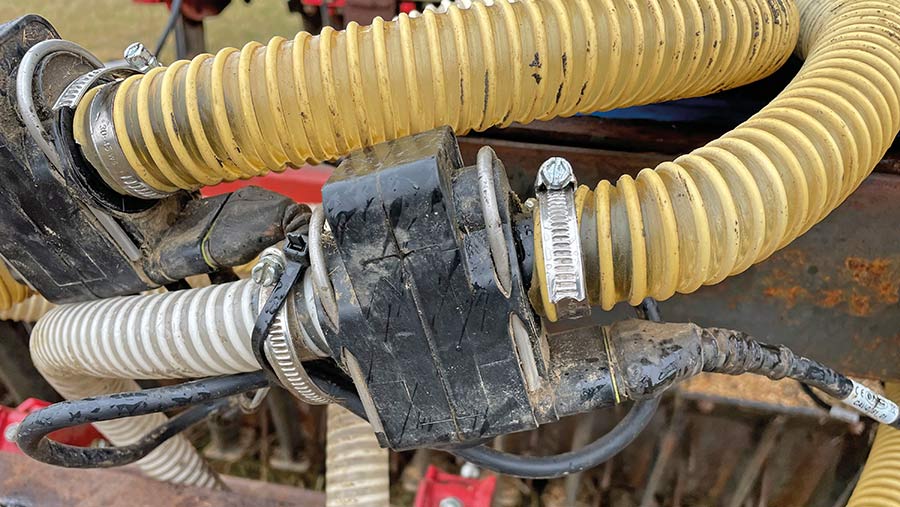
Counting sensor © James Andrews
The liquid fertiliser is also controlled through the GFX-750 using a Raven flow meter and another Trimble system called Field IQ.
Thanks to the Isobus setup, all four products can be applied at variable rates and application maps can be generated, ready to upload into farm management software for analysis.
In Mr Mumford’s case this is Trimble’s My Connected Farm system.
On top of this, Mr Carnell has fitted blockage and seed-counting sensors from MC Electronics.
As well as letting Mr Mumford know if seed isn’t coming out of one of the coulters, this tells him precisely how many seeds a square metre he’s applying.
“I used to work it out from the thousand grain weight, but it’s far more reliable using the information from the counter,” he says.
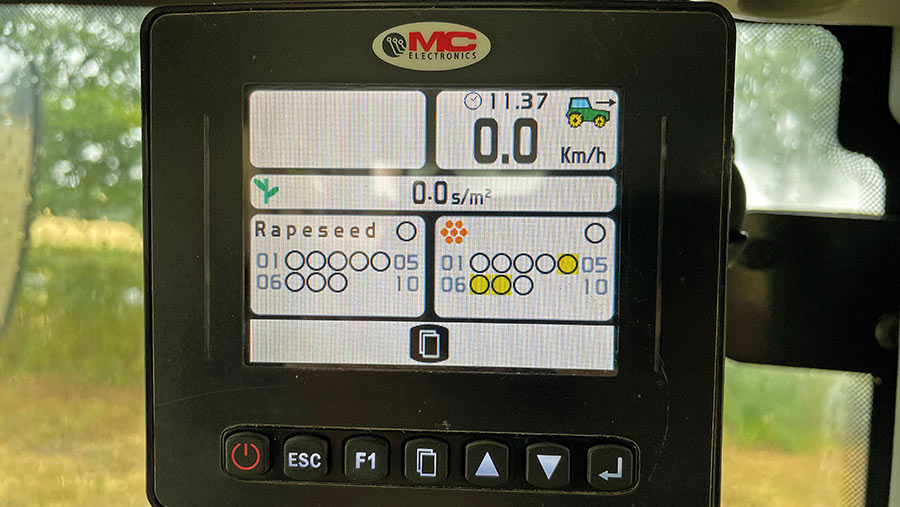
Blockage sensor control screen © James Andrews
Using it
The drill is pulled by a 220hp Claas Axion 810 and, with the legs set to work at about 20cm deep, it’s got just enough power for the job.
Working speeds of up to 10kph are possible, but to avoid moving too much soil, they opt for a more sedate pace of 5-6kph, giving a work rate of approximately 1.7ha/hour.
Fuel use is about 30 litres/hour, which is less than one-third of the amount used when Mr Mumford was putting in multiple cultivation passes and planting with his Vaderstad Rapid.
The drill was completed ready for planting oilseed rape in late August/early September 2021, all of which established well.
However, one of the later-drilled fields was obliterated by flea beetle. “We started to see damage on a Thursday and by the Sunday the whole crop was gone,” says Mr Mumford.
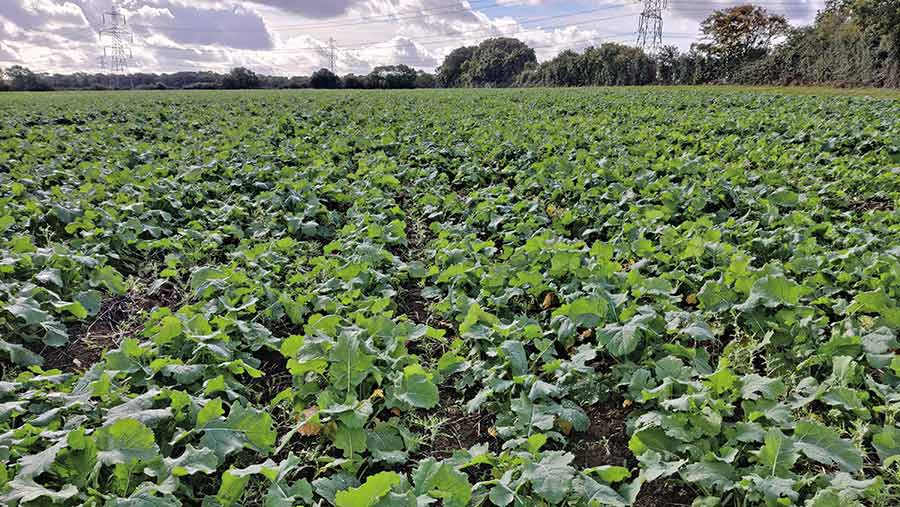
Crop established with the seeder © James Andrews
“That would have been a big loss with the old system, but with our lower labour and establishment costs it wasn’t so hard to stomach – we redrilled on 23 September, when the flea beetle had calmed down, and it ended up being one of our better-yielding fields.”
Crops planted with the drill returned an average of almost 5t/ha, with just one that suffered heavy pigeon damage coming in at about 2.9t.
“It was a good year for oilseed rape in general, but the drill helped it get off to a good start, particularly where we put some nitrogen down with the seed,” says Mr Mumford.
Modifications
Despite its success, the drill is set to receive a few modifications. The first of these will be to replace the Weaving double disc coulters with something more robust.
“They worked well last year, as the ground was soft, but because they’re designed to work in a cultivated seed-bed, coulter pressure generally isn’t high enough to work directly behind a subsoiler,” says Mr Carnell.
In a bid to find a suitable replacement, he did some seed placement trials with Bourgault, JJ Metcalfe and Vaderstad Rapid discs.
The latter gave the most consistent results and, due to their solid rubber mounts, they could exert plenty of pressure on hard soils.
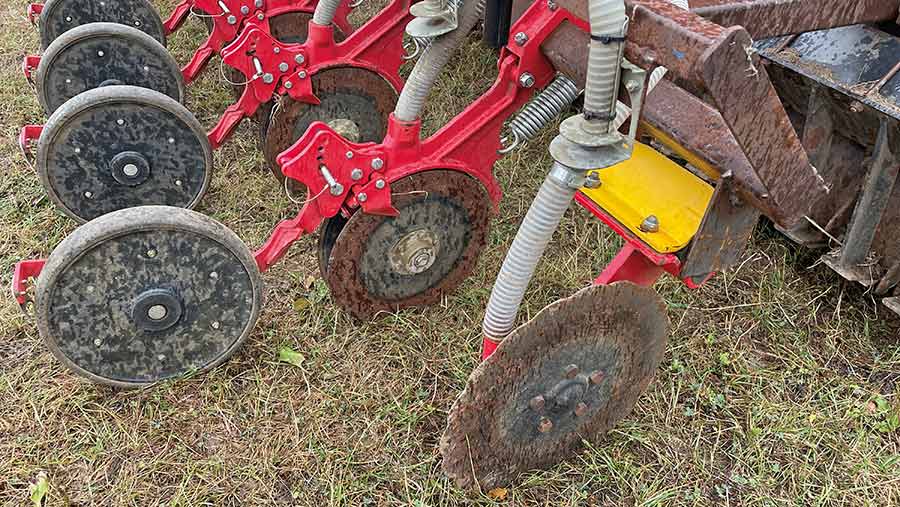
Vaderstad and Weaving discs © James Andrews
To find out if it’s worth the upgrade, Mr Mumford will be running the drill with one Vaderstad disc mounted alongside the Weaving units this season.
If it proves itself, he will look to source a second-hand set of coulters and recondition them, as new assemblies are so expensive. Individual rear press wheels might also be added to help close the slot and consolidate the seed-bed.
To alert the operator to any blockages in the liquid fertiliser system, Mr Carnell is adding a simple John Blue mechanical flow monitor.
This has a series of weighted balls suspended in a tube, which should sit in the centre at normal operating pressure.
If there’s a blockage, these will drop, giving a clear visual cue that something’s awry.
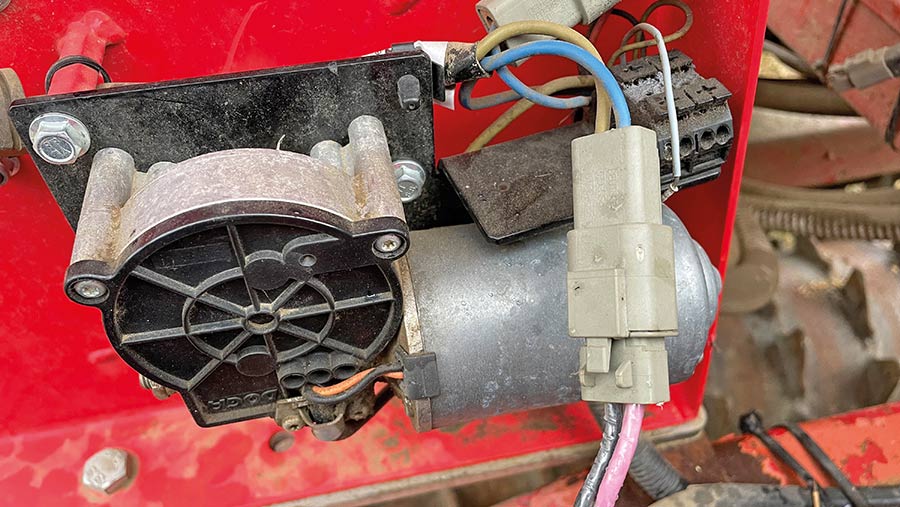
Applicator drive motor © James Andrews
Once the final design has been perfected, the drill will be stripped down and rebuilt to a factory-level finish. There are also plans to build more examples, which will be sold under the brand name Carford.
Coming season
For this season, Mr Mumford is planning to make full use of the drill’s features.
This includes applying variable-rate attractant slug pellets – should they be required – with higher rates in areas that are known trouble spots.
He will also experiment with cover crops such as buckwheat in the inter-row, with the hope they will reduce flea beetle pressure.