Contractor rates his £190,000 static Orkel baler
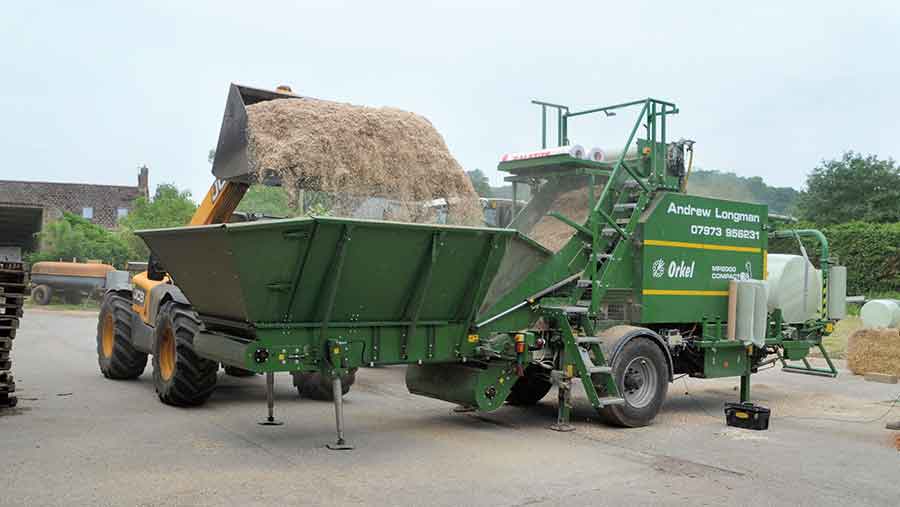
You need a keen eye to identify a niche contracting operation that has the potential to be successful. Farmers Weekly visits a Somerset contractor that has recently shelled out big money on an Orkel compactor baler.
Over the last 10 years Somerset contractor Andy Longman has made something of a name for himself specialising in unusual operations. Having given up dairying in 2004, he saw a niche crimping and milling home-grown grain for the region’s dairy and beef producers.
After developing that business he bought a Korte 2000-S mill and bagging chassis, which meant he could offer customers the option of storing crimped grain in mini Ag-Bags.
See also: NAAC farm contractor charges 2016-17
He could see the value in building a customer base for different crimped feedstuffs, having already undertaken a number of contract arable operations while offering a grain storage service in the farm’s converted dairy buildings. Soon he was harvesting almost all of his own cereals damp, crimping them and clamping them in the unit’s redundant covered silage clamps.
While this proved successful, he could see the potential in making the most of the West Country’s ideal growing conditions for maize.
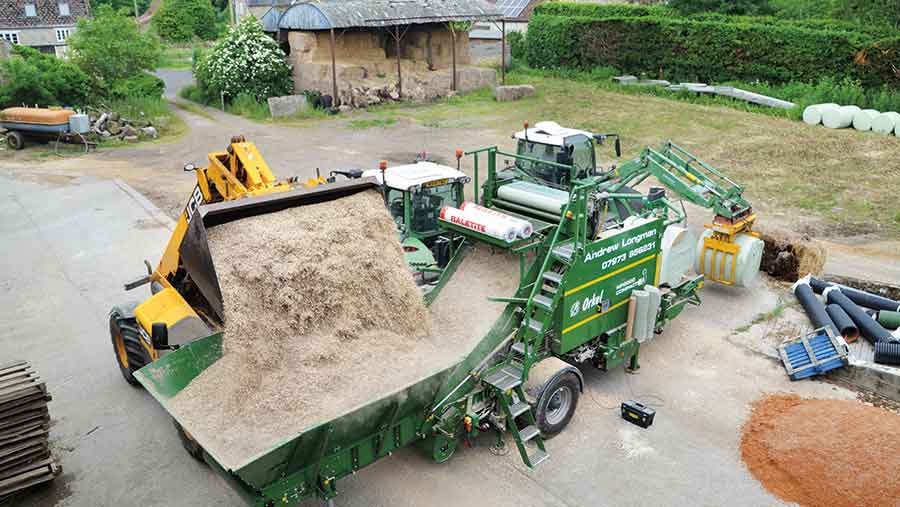
© Nick Fone
“We grow some pretty decent crops of forage maize here in the South West but there was a demand for a more concentrated source of starch,” explains Mr Longman.
“The feed industry was already importing grain maize as cattle feed and a number of people had started combining their own with good results. With a bit of investment in a torpedo header, I could see an opportunity to set up growing and harvesting it as well as processing it, storing it and delivering it out.”
Alongside that, the outlay on the specialist kit to do the job was offset by contract work to cut and process farm’s own crops of maize not destined for the forager.
“We’ve built a bit of a name for ourselves milling, rolling and crimping home-grown feeds as well as doing the grain maize but I wanted to push that further and spread our workload,” he says.
“The obvious move for a contractor in such a livestock-dominated area is to go down the silage route but with the hassle and investment required to pull together a team, it wasn’t something I wanted to get into.
“I wanted something that was just a one or two-man operation and not so weather dependent.”
Orkel baler
“It was about 10 years ago that I first saw Orkel’s compactor baler working at a show and wondered if it would complement the feed supply side of the business. I mulled it over for a while and then, after almost a decade of contemplation and speaking to a few interested customers, I decided to take the plunge and shelled out £190,000 on a brand-new machine.”
The baler he plumped for was Orkel’s MP2000 – a stationary, road-towable round-baler capable of producing packages of material 80%-100% denser than a standard round baler.
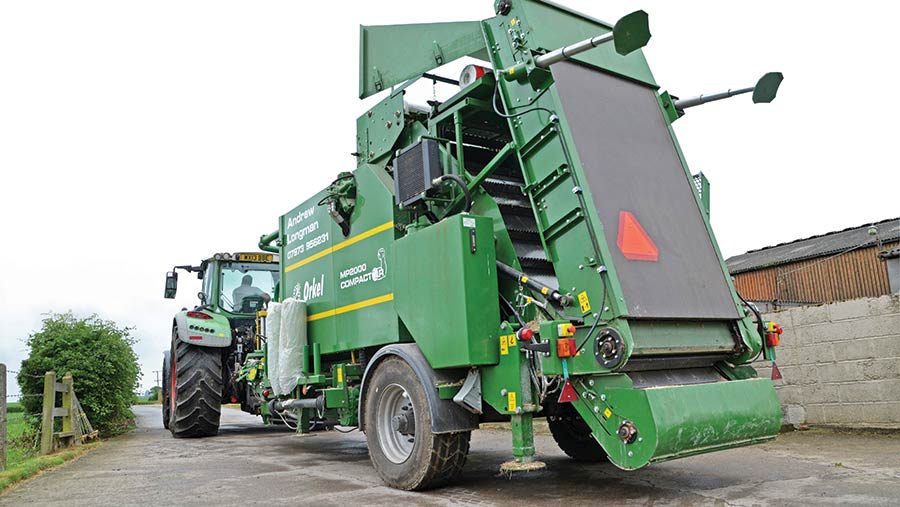
© Nick Fone
At its core is a 120cm wide, 115cm diameter chamber enclosed by a series of rollers and two full-width rubber belts. On the intake side there’s a fold-down hopper with a chain-and-slat conveyor that propels material up to the intake opening at the top of the bale chamber.
As crop is fed in a sprung tensioner roller creates the initial pressure for the belt to begin forming the centre of the bale. As the diameter increases, hydraulic pressure control takes over to maintain density for the outer layers of material. This can be varied from 120bar to 180bar depending on the density of the product, resulting in bale weights that can range from 260kg up to 1,400kg.
With the pre-set pressure achieved the computer control box shuts off the feed-in conveyor and a layer of film – rather than netwrap – is applied around the circumference of the bale. With this done the chamber door opens allowing the formed package to drop on to the wrapping table. Here, twin satellite arms apply however many layers of film are required before the table lowers the bale on to the floor ready for stacking.
Getting it set up
Once on farm set-up doesn’t take long. Inserts need to be fitted to the fold down hopper and the telescopic drawbar is retracted hydraulically under the wrapper table. With this done the towing tractor is then coupled up to a pto shaft midway along one side of the machine. Most baler functions are oil-driven and the on-board hydraulic power-pack is driven off the pto.
“To keep the baler running at maximum output you need to have three machines – one tractor to run it, a loader to feed it and another to clear and stack the bales,” explains Mr Longman.
“We’ll generally average over 40-45 bales an hour but we can top 50-55, depending on the product.”
What can you bale with the Orkel?
According to the Norwegian manufacturer you can package up just about any product you can think of. Many are sold into the waste industry where they are used to compress and wrap sorted rubbish, which can then be transported to waste-to-energy incineration and pyrolysis plants.
Typical bale weights
- Miscanthus 260kg-330kg
- Grass silage 750kg-850kg
- Maize silage 1,100kg-1,200kg
- Apple pumice 1,200kg-1,300kg
- Crimped grain 1,200kg-1,400kg
Although Mr Longman has occasionally used his machine for wrapping rubbish, he sees the majority of its workload following the same lines as his existing feed processing business.
“Recently we’ve done some work baling chopped, dried miscanthus for horse-bedding. Previously it was loaded into bulk-bags which was a dusty, time-consuming job for the customer. When they were delivered out they couldn’t be moved without a loader and had to be stored under cover.
“In contrast the bales are weatherproof and because miscanthus isn’t very dense the bales only weigh 260-300kg. But because they’re solid and don’t slump they can be easily rolled to where they’re needed.”
In the main it’s feed-related products that are processed with the Orkel – crimped grain, maize silage, chopped grass and apple pumice.
“When feed is short in Wales and Scotland we can ship bales of silage, maize and grain to wherever it’s needed and the transport is efficient because the bales are dense enough that we can get full weights on to lorries.
“It also gives us the opportunity to produce a blend of products almost like a TMR.”
Has it been reliable?
“We haven’t done huge numbers of bales through the Orkel in the last year as we’re gradually building that side of the business.
“In that time we’ve had no major mechanical or electronic problems – only minor set-up issues. Whenever there has been any trouble we have just phoned the importer KS Baling and they’ve talked us through it.”
Being a relatively complex machine inevitably there are lots of sensors. But they’re all of all similar type so spares are kept in the workshop. A laptop is rarely required – the standard control box diagnoses most faults and identifies why a sensor has gone wrong.
The MP2000 can be fitted with a choice of three different rubber chamber belts – either smooth, chevron lugs or a rough velcro-type finish to suit the type of material being baled. When the Orkel first arrived at Snagg Farm the belt had to be changed for the chevron version that best suits agricultural crops.
“Just recently we’ve had a conveyor sprocket slide on a shaft but that was just a case of putting it back in position and tightening a grubscrew.
“Other than that it’s very easy on maintenance. There aren’t many bearings and the few that are used are serviced by an auto-greaser. The majority of the moving parts run on brass bushes that have auto-oilers. When they’re worn they’ll be straightforward to change.”
Business facts
Andrew Longman, near Castle Cary, Somerset
Services offered Crimping, rolling and milling grain for feed
Mini Ag-Bagging
Grain maize harvesting
Crimped and dry grain storage
All conventional arable operations
Spraying
Static compactor baling
Farmed area Maize 65ha (160 acres), red clover 8ha (20 acres), winter wheat 20ha (50 acres), grass leys 69ha (170 acres)
Machinery
Tractors – Fendt 720 and 724, JCB Fastrac 2170 with 3,500-litre Knight demount sprayer and 24m booms
Loader – Manitou MLT 627
Combine – New Holland CX 8040 with 6m (20ft) conventional cutterbar and 8-row Cressoni maize header
Drills – 6m Horsch Pronto and 3m Kuhn power-harrow combination
Static compactor baler – Orkel MP2000
Horsch Joker cultivator
Rabe 5-furrow plough
Korte 2000-S mobile feed mill and 1000 on bagging chassis
Staff Andy Longman plus one other full-time
Orkel MP2000 Compactor baler Tech Specs
Chamber size 120cm wide x 115cm diameter
Bale volume 1.25cu.m
Bale weights 260kg to 1,400kg
Capacity up to 55 bales per hour
Power requirement 120hp
Weight 7.8t
Base price £190,000 depending on spec