Contractor Comment: Hedge work maintains winter cashflow
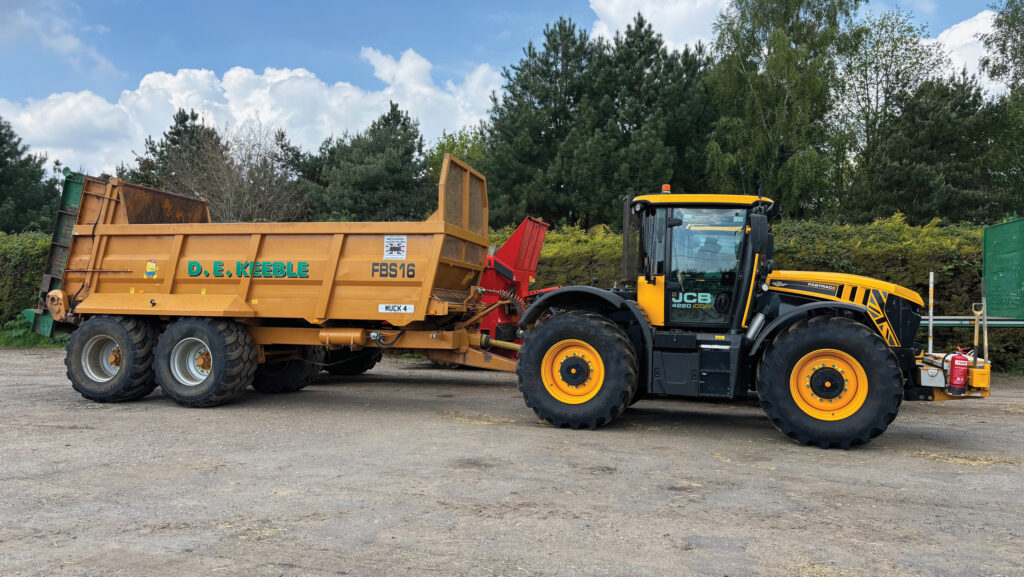
Big square baling might be the cornerstone of Derek and Linda Keeble’s business, but a carefully selected tranche of other services is key for maintaining cashflow throughout the year.
Each of these is chosen based on their ability to turn a profit, fit around other work and avoid stepping on the toes of fellow contractors.
See also: Contractor Comment: Tractor prices force switch to hiring
As soon the dust settled behind their army of Massey Ferguson/Hesston balers and Heath Super Chasers last September, they moved neatly onto the task of covering carrots with straw to protect against frost.
About the contractor
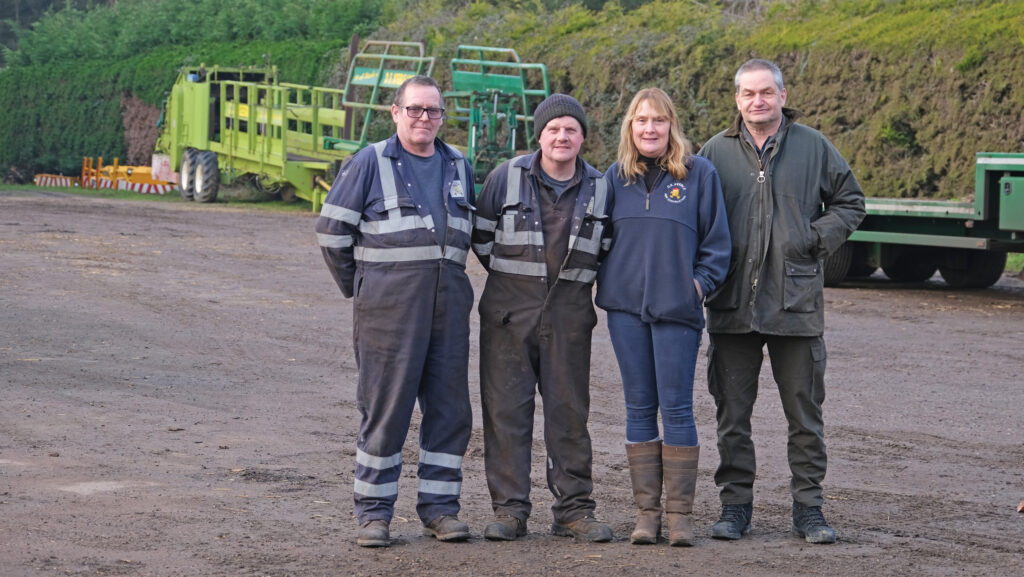
The DE Keeble team: Martin, Mark, Linda and Derek © James Andrews
Straw is the core of Derek and Linda Keeble’s Suffolk-based contracting business, with 25,000t baled each year for a range of outlets including power stations, livestock and covering overwintered vegetables.
This is carried out using a pair of Larrington spreaders, which have been modified to improve performance.
The concept of these machines is simple enough: seven full-size Hesston bales are loaded on the bed and a belt winds them toward a set of horizontal beaters that chop and lay the straw over the rows.
However, the timing of the various components is crucial for them to work effectively.
When they were new the bed belt and drums were not in tune, which caused the rotors to bung up.
So, they spent considerable time playing around with the gearing to get them just right.
Since then, larger driven wheels and polythene cutters have been added.
Straw spreader upgrade
They’ve given years of faithful service, but Derek was never keen on the fact that the strings would get shredded with the straw and end up wrapped around the beaters.
Drivers would keep contamination to a minimum by going to the trouble of removing five of the six strings during loading, leaving just one holding them together.
But this was still seven strings passing though per fill.
“Every six loads we had to cut it off with a cordless angle grinder which wasn’t much fun,” says Derek.
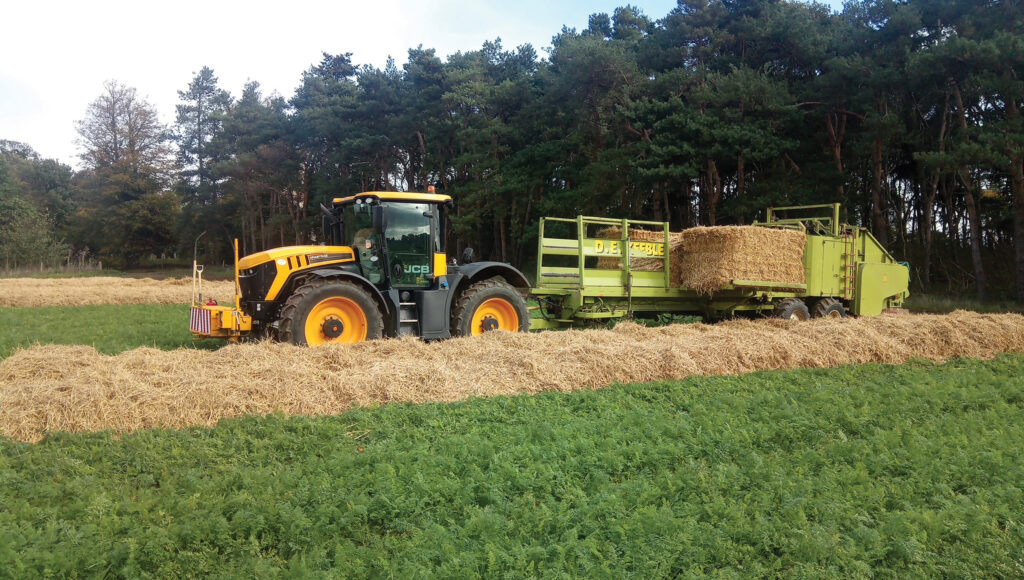
Modified Larrington spreaders are used to cover carrots with straw © James Andrews
Their latest solution was to fashion an ingenious cutting and collecting device.
This consists of a U-shaped frame that lowers over each bale with a knife on one side and a hook on the other.
In one deft motion, it grabs and cuts the strings before lifting them into a hydraulic winder that bundles them up and drops them into a bucket.
It works largely automatically, but a camera is trained on the device so the operator can check it’s behaving.
The modification helped streamline this year’s operations, which were already made simpler by a slightly reduced workload and good weather.
This meant they could run mostly with just one machine, and they were sewn up by the end of the month.
Business facts
DE Keeble, Blaxhall, Suffolk
- Main services 25,000t big square baling, straw covering carrots, rear-discharge muckspreading, hedgecutting/coppicing and verge mowing
- Staff Derek and Linda Keeble plus two full-time members of staff, one full-time lorry driver and five seasonal helpers
Excavator coppicing tool
A far bigger undertaking has been miles of tree and hedge coppicing, which is carried out using a home-made saw head and grab fitted on a 14t Doosan excavator.
This tool has been in the Keebles’ arsenal for several years and, like much of their equipment, is different to anything available off the shelf.
They fabricated it themselves, mostly from second-hand parts, which means the work it carries out can be both profitable and good value to customers.
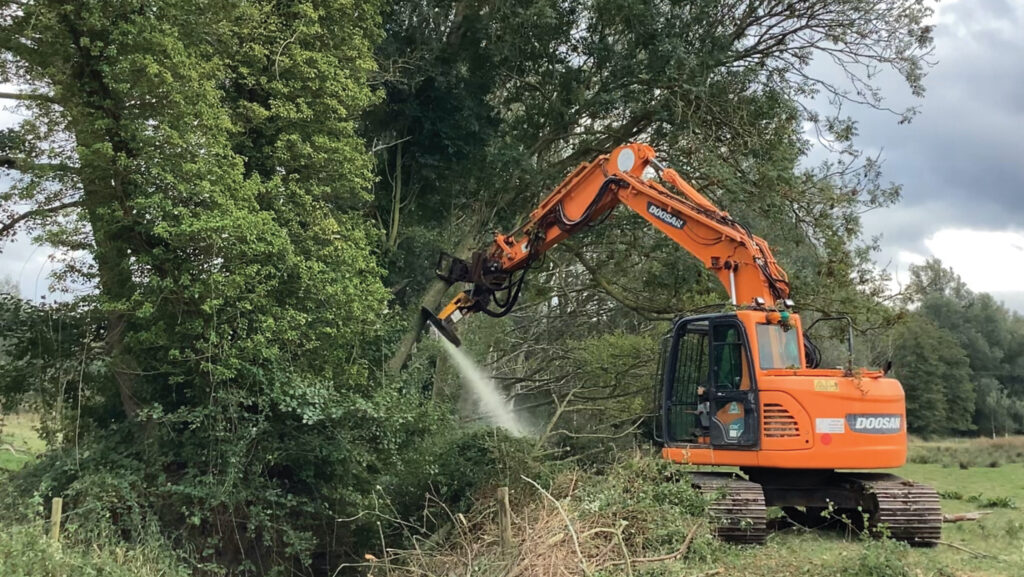
A Doosan excavator carries the Keebles’ home-made saw head and grab © James Andrews
The starting point for the build was a hydraulic saw with a 1m blade, to which they grafted a grab that can grip a 1.2m-diameter trunk.
Crucially, the saw can pivot independently of the grab, giving a wide range of movement for tackling awkward branches.
“It’s much more precise than a tree shear and you leave a really tidy finish as it cuts cleanly rather than severing the timber.
“It also copes equally well with small branches and large trunks,” says Derek.
“I can even turn it on its side and cut timber into logs, ready for customers to load into their trailer.”
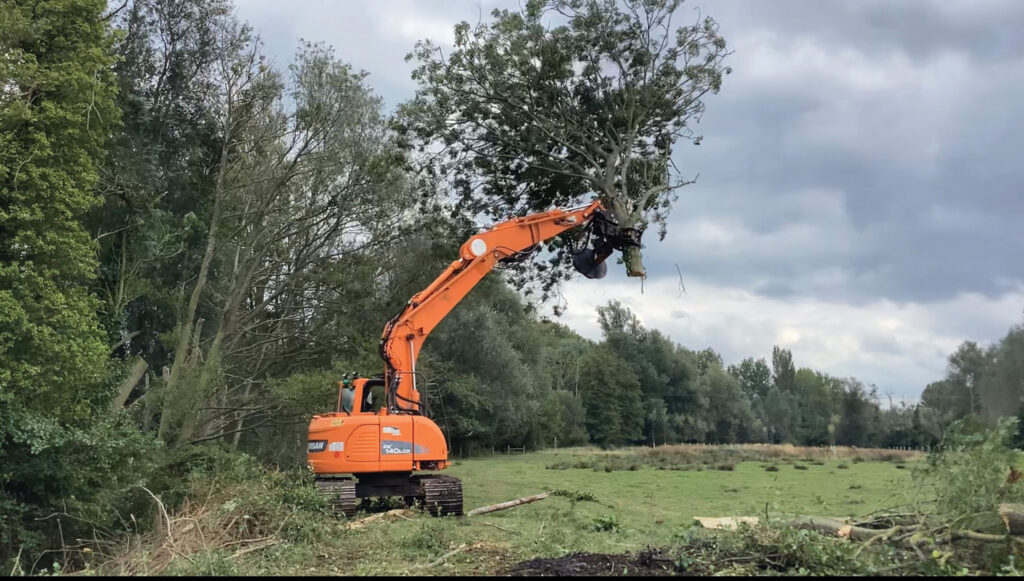
© James Andrews
The volume of work the saw carries out means they keep two blades in reserve.
These are used in rotation and they refurbish them in-house by making and welding on replacement teeth.
In the early days these were made from Hardox, but this wasn’t tough enough.
Tungsten carbide tiles came next, which were as hard as glass, but sadly chipped like it too.
Finally, they settled on stainless-steel, which strikes a balance somewhere between the two.
These are arc welded in place using dissimilar rods and have a leading edge to improve cutting ability.
For mulching smaller branches, the digger can be fitted with a heavy-duty flail head.
This is a 1.2m unit built by Dutch firm Herder that features a powerful piston motor, wide hammer flails and a roller.
It’s far from standard though, as it has a 360deg rotator pilfered from a paper grab and a hydraulic tilt function.
Together, these allow the flail to be contorted into almost any position, including awkward vertical cuts tight to the machine.
Digger modifications
Both the saw and flail head require far more hydraulic output than the digger offers as standard, so some significant upgrades needed to be added.
Servicing the tilting functions and grab were relatively simple and involved adding a couple of extra slices to the original electro-hydraulic valve block.
Handily, each of the digger’s joysticks had an unused rocker switch on the top which they could wire up to control these services.
To give ample power for running the saw blade and flail, a secondary hydraulic pump was fitted which is purely dedicated to this task.
All in, the saw blade, flail and hydraulic upgrades cost them about £9,000 in 2015, with the digger coming in at £30,000.
This was a rough ex-hire model – they didn’t want to chop a tidy one about – that came from Mervyn Lambert Plant in Diss.
“They run a huge fleet of diggers and when they sell them off in big numbers you can just walk round the yard and pick the one you want,” says Derek.
“We chose a 14t Doosan with zero tail swing, as it was good value, had large oil flow, seemed reliable and was nice to drive.”
As the system was a success, they upgraded to a smarter 2014 machine a couple of years later which cost £40,000. “I’m hoping this one will see me out.”
Staff health checks
Although the winter has been busy, Derek and Linda have put the time and money aside for themselves and their two permanent members of staff to have private health checks.
These are carried out at the local Nuffield hospital at a cost of £700 each.
“We wouldn’t think anything of spending that sort of money fixing a machine and health is far more important – a bit like a person MOT,” says Linda.
“The tests are much more thorough than the standard NHS ones, there’s no waiting list and you get the results instantly – plus, it’s a smart place and they make it quite a pleasant experience.”
No new machinery
As for kit, high prices and a lack of confidence in the industry mean no new machinery has been added to the Keebles’ fleet since our last visit at the end of September.
Frontline tractors are still a trio of Fastrac 4220s – two 2023 models and one 2017 – and it still looks like they’ll be hiring rather than buying another three to join them for the baling campaign.
It’s the same story with implements, so instead they’re focusing on keeping the kit they’ve already got in good working order.
Currently receiving pre-match overhauls are their two 16t vertical beater muckspreaders – a Richard Western FBS16 running on tandem axles and single-axle Ktwo Evo 1600.
The former is the more versatile of the two as it’s been modified to spread all forms of muck, compost, beet sludge and LimeX.
This was achieved by lowering the rear beaters, fitting large bottom paddles and fabricating a removable hood.
It can spread these products to 12m and saves them having to have an additional horizontal beater model in reserve.
Both machines will be running flat out from February until the work comes to an abrupt halt in April.
“We’ve got a lot of sandy land in this area that goes into veg and sugar beet, so there’s a short but very busy window to get all the manures and composts on to give them a boost before drilling,” says Derek.
Once this is wrapped up, they’ll move onto verge mowing with their home-made trimmers running on yellow New Holland 8340s, before the balers and chasers are back in action.