Buying the right farm machinery when switching to a new system
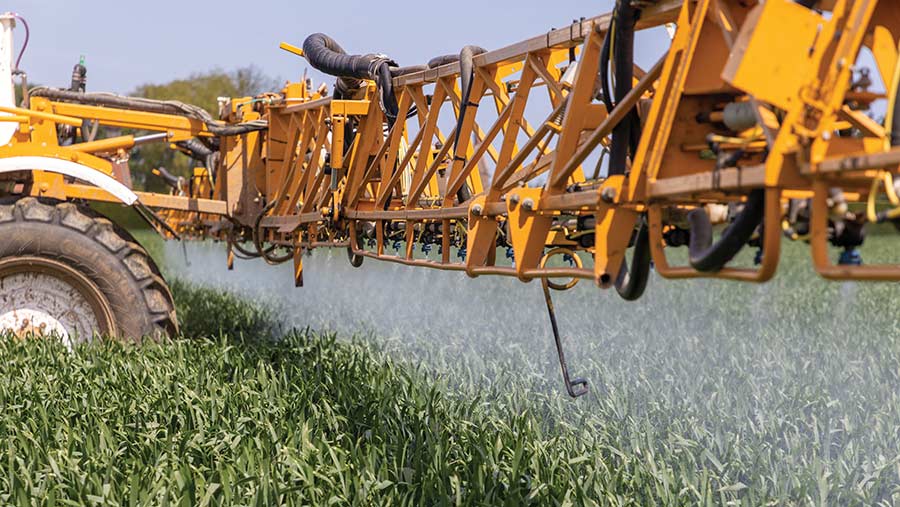
Buying kit to switch to more sustainable systems, without first assessing its true cost and suitability, could waste thousands of pounds and damage land.
According to consultants and machinery experts, there is a rising number of cases where growers have bought equipment that is over-specced or too large for their farm’s needs.
In many of these cases, the equipment is returned to the dealer or sold on the second-hand market, at a huge depreciation cost to the business.
See also: Steep price rises put focus on machinery costs
So why are so many farmers buying inappropriate equipment, and what are the key steps to take to buy the right machine to make a profit under a new regime?
Adviser Strutt & Parker, equipment manufacturer Claydon and the AHDB offer some insights on common investment pitfalls, and give tips on how growers can spend wisely.
Pitfalls to avoid
Misuse of grants
Grants such as those from the Farming Equipment and Technology Fund provide funding for a proportion of the retail price of equipment.
Used correctly, this can be hugely beneficial in reducing the capital outlay when upgrading to more efficient machinery and making otherwise out-of-reach equipment affordable, says Mike Bywater, southwest territory manager at Claydon.
But some have seen the grant system as a way of buying bigger, higher spec equipment than their budget would have otherwise have covered.
Only later has it become apparent that the upgraded machine does not meet their needs, says AHDB knowledge exchange technical manager Harry Henderson.
In addition, the list of qualifying equipment set out under the grant rules may not cover the right machine for the farm, meaning there is a degree of compromise.
The on-off, open-shut style of government grant funding is a further influencing factor. Funding is often competitive and application windows open for only short periods, adding pressure on farmers to make a decision.
Strutt & Parker’s head of farming, Jonathan Armitage, says growers sometimes make a big investment decision because they are unsure whether the grant funding will be available for subsequent windows, or if it will be offered with less attractive conditions.
Then, even with a discounted price, buying new may not always be the most cost-effective approach for a business.
Cheaper and more appropriate alternatives for a system may be available on the second-hand market.
Inaccurate costing
Consultants have found that most farmers and growers are making investments without knowing the specific costs of growing a tonne of a crop under their existing or proposed systems.
This is a vital step, and missing it out creates huge potential to spend beyond the farm’s budget.
There is no way of evaluating whether a new machine is too costly, both as an initial outlay and in terms of running expense, without knowing the margins available, says Jonathan.
Unsuitable soil
Not all land is suited to a no-till approach, and too often growers are investing in equipment without admitting that the trend towards low-disturbance systems is not achievable on their farms.
Harry says it is important not to bow to peer pressure to move into a system that cannot work efficiently. From the outset, ask whether the soil is suitable for a min- or low-till setup.
A starting point is to assess the soil structure and condition, if it is not already known.
The tried-and-trusted method of digging a pit to determine structure and identify drainage and compaction issues is still the best approach, advises Harry.
Check the friability, worm count and topsoil and subsoil structure; all will dictate the likely success of a low-disturbance system.
A further consideration is labour. An effect of the current labour shortage is not just the availability of workers but the limited number of skilled operators, says Mike.
In situations like this, technology in the cab can help. Some modern machines have been simplified to a point where the operator needs far less experience than ever before.
Buying bigger than necessary
There is a belief that a bigger machine is better because it can cover more ground, more quickly.
But farmers often have too much spare capacity and AHDB assessments have found that machines such as seed drills can be 50% bigger than the farm needs.
It is the same for cultivations, spraying and harvest equipment, says Harry.
The thinking behind buying big is that it is useful to exploit gaps in bad weather and wrap up cultivations or drilling within a tighter time period.
However, while a bigger machine may carry out the work faster, it will not be able to access land as early in the spring or after bad weather, Harry points out.
Likewise, in the autumn a heavier machine will have to quit earlier or risk damaging soil.
So access to land may well be limited where a smaller tractor and drill would have a longer season.
Where they do work, they may still fail to bring an improvement in margins.
For example, the extra horsepower needed to pull the new kit will use more fuel, adding to costs.
It may also necessitate additional investment in more powerful tractors.
Generally, larger machines will see a higher depreciation than their smaller counterparts and the brunt of that cost is borne by the farm.
Over-specced equipment
Higher spec is only beneficial to profit margins if it is useful.
It is possible that new technology can generate higher returns by increasing yields or saving time and labour. It will be a worthwhile investment if it more than covers its costs.
However, the lure of an extra electronic gadget can encourage a grower to part with more cash and yet that additional expense may not produce increased returns.
Often high-spec machines come with functions that are hardly used and, again, the grower pays for the depreciation on the investment.
Peer pressure
All too frequently decisions are swayed by branding, press reviews or social media videos of kit working in ideal conditions.
It is naturally persuasive when a fellow farmer or grower can demonstrate amazing results with a piece of equipment.
But it is worth bearing in mind that the results for another soil type and system might be very different.
Few people will post their disasters, poor decisions and financial losses, and they rarely confess to buying the wrong equipment, Harry suggests.
Key steps to buying the right machinery for a new system
Before investing in machinery and equipment to transition to a new system, farm managers should undertake a rigorous planning process.
This should include a review of the long-term strategy, finances available, the individual farm characteristics, calculations of the size of equipment required, and the level of technical specifications.
Overall aims
The cost of new equipment is considerable, so it will have a long-term effect on the farm business.
Regardless of whether the investment is to replace a worn out machine or a fundamental switch to a new system, the first step is to look at the higher-level strategy of the business, advises Jonathan.
Where will it be in the next five years and what role will the investment make? Will it reduce labour dependency, improve animal welfare or perhaps change cultivations and cropping?
Review the existing situation
The first key step in putting together a purchase plan is to accurately assess the costs and margins of producing a tonne of crop under the current system.
Volatility in input costs has been extreme over recent years, making calculations more difficult.
The best approach is to review historic production costs, and compare them with yields of crops or livestock and the resulting margins.
It is possible to make an estimate but assumptions will have to be included over the potential for input price changes, says Jonathan.
Benchmarking is also helpful in the process. The AHDB’s Farmbench service is available to all levy-payers.
The service provides access to production costs, by region and for the top, middle and lower thirds in performance terms.
For more detailed data, it is possible to join a benchmarking group that more closely matches a specific farm, allowing a clearer picture to be developed.
The more specific costs of the business can then be added and no stone must be left unturned during this part of the process.
Fuel, seed, fertiliser, pesticide, labour, storage and machinery costs must all be included and then worked out to a per-hectare basis.
Estimate costs of the new system
The next step is to work out what the new system will look like with an honest appraisal of the costs of buying equipment and the savings possible under a switch to a longer-rotation, low-soil-disturbance system.
This will help point to likely margins and guide the machinery purchasing process to ensure a profit can still be made.
Fuel costs associated with low-soil-disturbance systems can be considerably lower than conventional, inversion setups.
Fuel use required to grow winter wheat |
|
System | Fuel (litres/ha) |
Plough and cultivation | 100 |
Min-till | 75 |
No-till | 50 |
Note: Includes crop establishment, sprays, fertiliser, harvest, trailers and pushing up. The AHDB has worked out a range of likely costs based on prices in the late spring/early summer of 2023. These can be factored into calculations. Source: AHDB. |
Typical costs across a range of operations |
||
Operation | Machine | Cost |
Ploughing | 390hp, 7 furrow | £40/ha |
170hp, 5 furrow | £31.82/ha | |
Min-till drilling | 234hp, 4m tine | £82.50/ha |
215hp, 6m tine | £32.50/ha | |
No-till drilling | 210hp, 6m drill | £45.70/ha |
Rolling | 190hp, 12.4m | £16.10/ha |
Potato de-stoning | 135hp, trailed de-stoner | £166/ha |
Potato bed-forming | 150hp, bed-forming | £57.70/ha |
Potato harvesting trailed | 195hp, 2-row | £366/ha |
Fertiliser spreading | 124hp, 24m | £8.97/ha |
Spraying trailed (inc tractor) | 30m | £6.06/ha |
Spraying self-propelled | 36m | £10.98/ha |
Grass mowing | 4m fully mounted | £16.10/ha |
Combining | 2016, 9m header | £123/ha |
2004, 6m header | £119/ha | |
Carting | 234hp and 14t trailer | £96/hr |
Materials handling | Telehandler | £37/hr |
Note: Costs include fuel, driver, depreciation and repairs. Source: AHDB |
Savings in fuel and labour time can also be made in a longer rotation by perhaps introducing grass leys to let, or a root crop that could be outsourced under contract to a specialist grower.
Calculations should also factor in the longer rotation which can relieve some of the time pressures on machinery traditionally associated with cereal growing.
Barley and wheat will usually be combined within a two- or three-week period on an individual farm. But this window of operation can be extended with a longer rotation.
Including roots or beans lengthens both the harvesting and drilling windows, making it possible to get around the jobs with smaller equipment and a lower investment.
Calculate the size of implement required for your farm
It is important to note that investing in a no-till drill that is unnecessarily big will wipe out the potential cost reductions from a switch to a more sustainable system, says Harry.
The farm will have spent a lot of money to, at best, stand still. To avoid this and identify the correct scale of machinery, growers can carry out relatively simple calculations.
Step-by-step calculation process
- How much area do you have to cover in the given time?
- What timeframe or window do you have to complete the task? Use hours, so 20 days with a 10hr working day = 200hr.
- What is the speed of operation? Use kilometres per hour (kph) and be realistic.
- What is the field efficiency (see below)? That is, out of 100% of the time spent in a field, what percentage of time is spent turning around and re-filling or unloading?
Field efficiency explained
Field efficiency figures show a range of work expected under practical working conditions that should be added to the calculation.
- Ploughing 65%. Add 3-5% if average field size is greater than 10ha
- Min-till cultivation 65%. Add 3-5% if average field size is greater than 10ha; reduce by 5% if no GPS guidance
- Drilling 55%. Add 3-5% if average field size is greater than 10ha; reduce by 5% if no GPS guidance
- Spraying 50%. Add 3-5% if average field size is greater than 10ha; reduce by 3% if no GPS guidance; increase if bowser used. Farm efficiency can be below 50% if travel time is taken into account. Consider a bowser
- Fertiliser spreading 60%. Add 3-5% if average field size greater than 10ha; reduce by 3% if no GPS guidance
- Combining 80%. Add 3-5% if average field size is greater than 10ha; reduce by 10% if no GPS guidance, reduce if not unloading on the move
Use equation
Plug the figures into this equation to identify the appropriate machinery size:
ha/hr x 10
kph x field efficiency
Example: Crop sprayer
- Required machine width: 430ha to spray in 36 operating hours.
- Average speed 12kph at 70% field efficiency (therefore multiply by 0.7)
- Required coverage: 430ha divided by 36hr
= 12ha/hr spraying time
Width needed
Plug into the equation:
12 x 10 = 120
12 x 0.7 = 8.4
120 / 8.4 = 14.28
Round down to 14m, therefore 18m sprayer required
Drill size requirement by output |
||
Drill width |
Average output (ha/day) |
|
Grain only |
Grain and fertiliser |
|
3m | 21 | 18 |
4m | 28 | 24 |
6m | 42 | 35 |
9m | 63 | 54 |
Note: Expected work rate for a 10-hour day. Average speed 10kph at 70% field efficiency, grain only. At 60% field efficiency, grain and fertiliser. Source: AHDB |
Avoid depreciation
Depreciation costs are low and almost nil in the current market.
However, the replacement cost is comparatively higher; some would be shocked at replacement costs, so that must be factored in, says Harry.
Are you replacing too early? British farmers and growers often trade in machinery at 5,000-6,000 hours, but well-maintained modern equipment is capable of operating to 10,000 hours and beyond.
There will be a point where the risk of breakdowns becomes unacceptably high and that is down to the individual farm situation. Growers should ask:
- Would hiring a machine be more economical for the hours it does?
- Would a contractor do a better job at the same cost?
- Would sharing a combine with a neighbour, which may deliver cheaper costs, be logistically possible?
Buying second-hand, rather than new, is a cheaper option
Research and advice
When looking for the right machine for a completely new system, consult widely, advises Mike.
Ask neighbours and use social media to gauge opinions of how a machine works in real-farm conditions. At Claydon, advisers will help guide buyers through the entire process.
“It’s not an overnight decision so we recognise the value of consultation and communication through a major purchasing process”, he says.
Claydon will organise on-farm demonstrations and follow-up visits after purchase.
These are important because it is often only when a machine is in the work situation that its suitability for the new system can be appreciated, Mike stresses.
Machinery costs: What makes the top 25% different?
The AHDB and Strutt & Parker carried out a review of machinery costs across 18 Monitor Farms from Cornwall to Moray.
1. Low depreciation
Depreciation is the largest cost in running a machine at 33% of the total, followed by fuel at 26%.
Among the top 25%, low depreciation a hectare was achieved in part by operating over a wider area and keeping machines longer.
Residual values were kept high through regular maintenance.
2. Low repair costs
Low repair costs were not exclusive to farms running newer equipment.
Farms with older machinery still achieved low repair costs through tactical hiring of key equipment or through employing experienced staff who could carry out basic maintenance and repair work on the machines.
3. Low diesel usage
As fuel is the second-largest cost of running a machine (26%), the top 25% were all using less than 100 litres/ha.
4. Low machine costs
While low machine costs an hour are linked to depreciation, they were also achieved by farms carrying out contract work.
On average, the top 25% were putting 900 hours/year on their owned tractors.
5. Low cost of combining
The top 25% were generally covering more hectares per metre of combine header than the rest, at 70ha on average.
A 10m header was, therefore, cutting at least 700ha.
The cheapest cost of combining was achieved by a 7.3m combine cutting 569ha (78ha/m of cutter bar).
6. Size
While there was no clear correlation between farm size and costs, the top 25% ranged from 500ha to 1,000ha in cropped area.
Economies of scale prevented some of the smaller farms (under 350ha) from obtaining the lowest-cost wheat production.
Transition Farmer: Kit Speakman
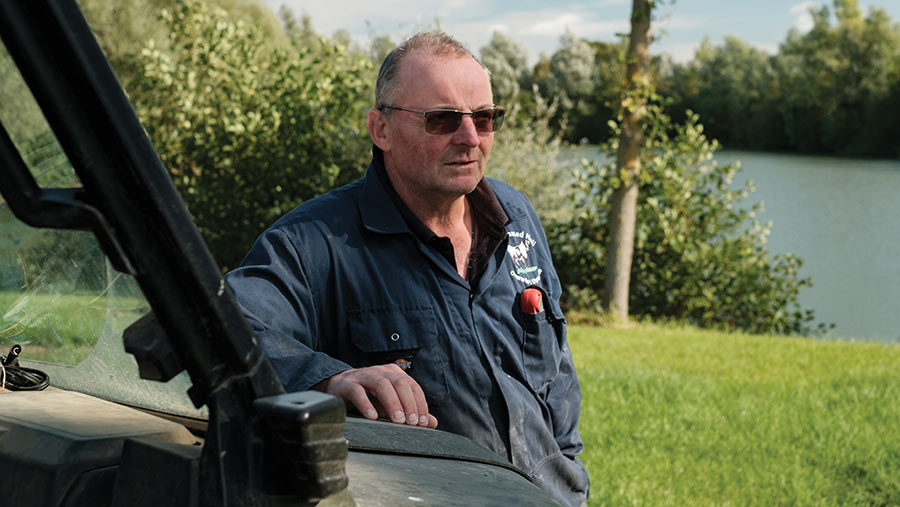
Kit Speakman © MAG/Colin Miller
Arable farmer Kit Speakman has opted to keep his machinery investments to a minimum.
The main reason for the strategy is to avoid depreciation costs which he said would have been crippling.
“We are not big enough at 685 acres to absorb the depreciation costs from a fleet of machines so we contract out arable work,” Kit says.
Land suitable for potato and sweetcorn growing is let while combinable crops are grown on a stubble-to-stubble contract.
“I pay for the inputs and the rest is down to the contractor. It also means that labour costs are kept down too,” he points out.
For the telehandler he owns, the aim is to minimise the impact of depreciation.
“We keep the telehandler while it is in its warranty period and then part-exchange it every three years,” Kit says.
That means any problems are dealt with under warranty and a service and maintenance package means there is no burden on the farm and its staff and downtime is minimised.
Purchase is made via three equal annual instalments which means machinery costs are constant and help with business planning.
Recently, however, Kit has invested in a new muckspreader.
Part of his transition strategy is to cut input costs and a nearby source of chicken manure was a good opportunity to reduce the amount of bought-in fertiliser.
The spreader includes a built-in weigh scale, adding greater precision to the process of spreading muck on grassland.
“Because we will use it to make collections, as and when the need arises, it made sense, in this instance to own the equipment,” Kit says.