Bristol Vet School gets welfare-friendly building
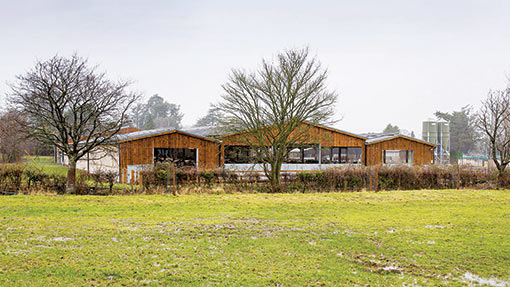
Building a new dairy unit presents a great opportunity for farmers to get everything right. But it requires a team approach and considerable planning, as Olivia Cooper reports
Many dairy farmers are making do with 50-year-old buildings and ancient parlours. But there comes a time when a complete revamp is required and, as with any large investment, it’s important to get it right first time.
This was exactly the situation that Bristol University’s Veterinary School found itself in five years ago, with an aging infrastructure that was compromising cow health and productivity.
“The old shed was originally designed for around 40 cows, with a three-a-side tandem parlour,” says David Barrett, professor of bovine medicine, production and reproduction.
“Like many farms, it was expanded over the years, ending up with 77 cubicles and straw yards housing 110 cows that were milked through a 30-year-old 12:12 herringbone. There were a lot of health problems, and it simply wasn’t commercially viable.”
So in 2009 the university invested in the first phase of the project, erecting a new slurry store and four silage clamps. Although planning permission was already in place for the new shed, a change of academic team and the introduction of farm management company Velcourt in 2010-11 led to a complete redesign.
“We wanted sand beds so had to modify the slurry system, and we included a lot of features to enhance animal welfare, safety and ease of handling,” says Prof Barrett.
Working closely with Velcourt farm manager David Hichens and design and project manager Roger Stewart, Prof Barrett continued to tweak the design to ensure it would be fit for purpose. “The site is bounded by residential properties so considerable consultation was undertaken to provide an acceptable design,” says Mr Stewart.
He lowered the roof profile and used a broken roofline with an eaves oversail and coloured sheeting materials to soften the visual impact, and also included extensive landscaping and planting around the buildings.
All about airflow
“The original design was for a high apex to improve ventilation, but you don’t need a high roof to do that. It’s all about the airflow through the sides and up through the ridge,” he says.
One side of the 115m long x 33.4m wide building is open above cow height, with the other side space boarded. The air is drawn up through a protected open ridge, with every second roof sheet standing 50mm proud to create a breathing roof. About 10% of the sheets are clear, to ensure a light and airy environment.
Wyndhurst Farm, Langford
- • 197 cows, 150 youngstock, 100 ewes, 600 vet students
- • Three farm workers including farm manager
- • 100ha (250-acre) farm bordered by houses and a main road
- • Redevelopment cost was about £2m, including sand cubicles in a 115m x 33.4m building
The building was designed to accommodate 202 cubicles, a central feed passage, a bull pen, calving pens, loafing areas and the new 24:24 parlour (which can be expanded to 28:28), all under one roof. To make it easy for students and workers to move around the building, squeeze gaps were put in next to gates, large enough for people but not cows to pass through. There is also a viewing gallery, office and washing facilities.
The new milking parlour has a 2.5m wide pit, extra space either side for access, and a motorised backing gate, plus a 14,000 litre bulk tank. “We put vacuum lines into the calving pens so that we can milk the fresh cows without them having to walk to the parlour,” says Prof Barrett. “It sounds like a luxury, but it’s very low cost compared with a cow going down or doing the splits.”
All the calving pens have locking yokes, and a gate that can swing round as a crush, with removable bars to enable veterinary work to be carried out. In the bull pen there is a guillotine gate and – more recently installed – a locking yoke.
Animal-friendly features
Other animal-friendly features include rubber matting around the parlour and collecting yard, and a 2m wide strip along the entire feed face, which also has locking yokes along most of its length.
“It makes life so much easier for me – I can vaccinate the whole herd quickly and easily, without having to chase animals around to get them into the crush,” says Mr Hichens. “Also, if the students need to work on a cow, she’s happy eating and standing on a soft surface.”
To make for easy management, the parlour has a three-way segregating exit gate with automatic identification, and a built-in footbath. All water troughs can be easily rolled over for emptying – with flip-down covers to keep them clean when bedding up in the straw calving area.
Electric cow brushes have proven extremely popular among the stock, which are mostly housed year-round in three management groups: high and low yielders, and dry cows. They are bedded on sand cubicles over sandsaver mats – thick perforated rubber with six inches of sand on top of it.
“We opted for high neckrail cubicles which are cantilevered, so that we can easily use a tractor-mounted rake to level the sand each day,” says Mr Hichens. Heavy round timber poles form the brisket rail.
Slurry channels
Due to the abrasive nature of sand, the team decided not to install automatic scrapers, and had to alter the slurry channels to improve the flow. “We have got slats at the end of each passage, into which the slurry is scraped, and we designed a U-shaped base to the channels, which allows the slurry to run down to the tank without getting blocked up with sand,” says Mr Stewart.
Because of the high water table in the area, the slurry store is concrete-panelled, and the slurry is distributed around the farm with an umbilical system. “We laid pipes under the roads, to save haulage and tracking mud over the main road,” he adds. “At the moment, the sand is loaded out twice a year, but we’re looking at agitating the slurry so that more sand remains in suspension.”
Mr Stewart and the team held monthly meetings during the planning and construction stages of the project, each bringing their own expertise to the fore. “It’s important to involve your vet, as vets visit lots of farms and see the best and worst of design,” says Prof Barrett. “We also drew on expertise from Velcourt, as well as my own experience in helping to design a farm animal hospital at Glasgow Veterinary School before moving here.”
Naturally, an eye always had to be kept on fulfilling the students’ needs, as well as those of the cows and herdsman. “Veterinary work is no longer just about treating sick cows, it’s about preventative medicine, and the vet school should be practising what it preaches,” says Prof Barrett. “To continue as leaders in farm animal veterinary medicine, the university needed to have a cutting-edge facility, with a strong focus on research and animal welfare – and now we have something we can be proud of.”
Extra luxuries
Of course, few farmers have a university behind them to foot the bill. But all the little extra luxuries – locking yokes, rubber matting, and so on – have only cost an extra £20,000; 1% of the overall project cost. And Prof Barrett is convinced they will pay for themselves many times over through improved health and productivity.
“In the old system, over 50% of the cows could be lame at any one time; now it is hard to find a lame cow in the herd. Less than 10% have a mobility score two, and mobility score three cows are exceedingly rare,” he says.
“Our milking times have halved, and mastitis rates have dropped considerably to around 15 quarter cases per 100 cows each year, with a cell count of around 140,000 cells/ml. Now that the farm has returned to profitability, it can continue to reinvest for a more sustainable future.”
And that reinvestment is already under way, with the refurbishment of the calf housing. “We put in an insulated roof with improved drainage and ventilation, as well as automatic heat lamps for when it’s cold,” says Mr Hichens. “As a result we’re seeing a significant improvement in calf health, which is vitally important, as they are the future of the herd.”
Results table | 2010 | 2014 |
---|---|---|
Cows in herd | 113 | 197 |
Litres/cow/year | 8,559 | 9,249 |
Mastitis % | 68 | 15 |
Lameness % | >50 | <10 |
MOPF £/cow | 1,380 | 2,158 |