British firm develops tracked electric ATVs
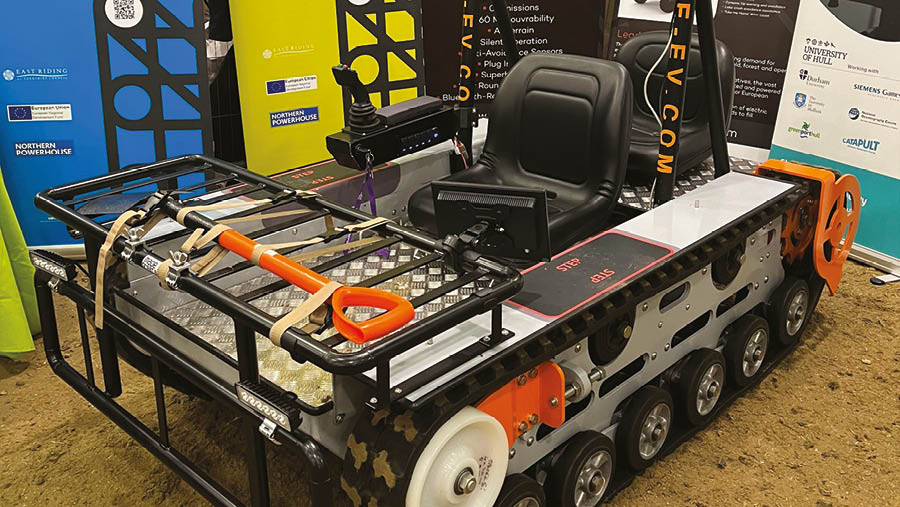
Farmers on the hunt for an electric farm get-around are now faced with more choice than ever, as a host of new UTVs have hit the market in the past year.
But, for those willing to consider something a little different, there’s a new machine on the block, which has been designed and built by British firm Pulse-EV.
See also: ATV buyer’s guide 2022-23
Resembling a small tank, the eTrak is an electric ATV that has been produced using low carbon methods and 3D printing as part of a joint venture involving students at the University of Hull.
The concept started life with a petrol engine, and was used as a hire vehicle for thrill seekers on off-road circuits.
“We started receiving a lot of interest from the farming industry and land management sector,” says director Brendan Taylor.
“We saw a gap in the market after farmers were complaining that they were struggling to place orders with competitor brands, facing long waits and import delays.”
Battery power
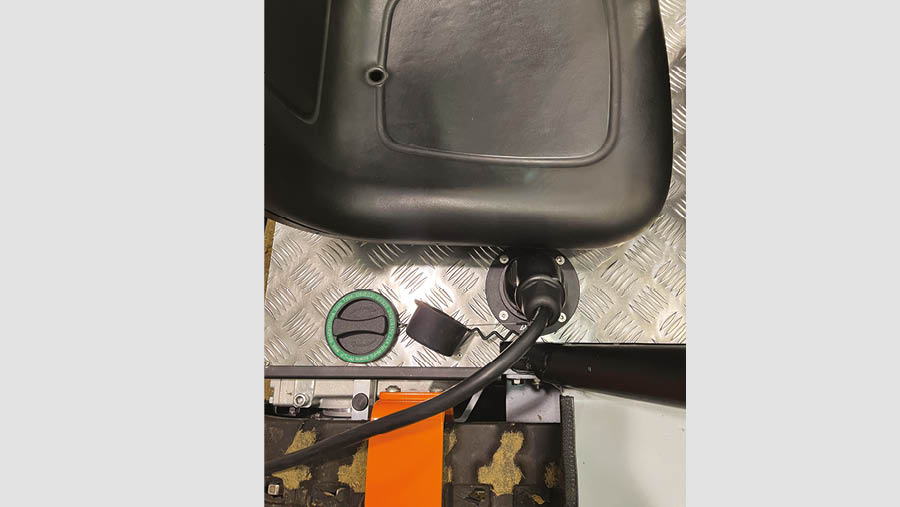
Onboard charger © MAG/Oliver Mark
Since starting Pulse-EV, the eTrak has undergone an electric metamorphosis, and essentially acts as a compact power bank, hiding a whopping 32 lithium-ion prismatic cell batteries beneath the floor within the chassis.
“Battery technology has moved on so much now,” says Mr Taylor. “These batteries are roughly half the size of what they would have been in the past, which means that we can pack more power into a much smaller space.”
With roughly the same dimensions as a Cornflakes box, the company is able to add more batteries to customise orders for farmers who need to achieve a longer running time. The current model can achieve more than six hours of continuous work, which is usually ample for most buyers’ needs.
However, as with all electric vehicles, the range will deplete at a faster rate when carrying out more strenuous work and, so far, one of the most common customer concerns has been range anxiety and charging times.
A full charge on the eTrak will take around eight hours to complete with its onboard charger, so it is best to plug it in overnight or top it up between jobs throughout the day.
A swappable battery set is currently in production to counter some of the machine’s limitations, with the hope that its working hours can be significantly extended.
Despite this large battery count, the eTrak weighs roughly 350-400kg, and Pulse-EV says that its low centre of gravity makes it much safer to operate when compared with traditional ATVs.
“You’re not going to tip this over,” says Mr Taylor. “In my 12 years with these machines not one has been tipped over – and we’ve had them in some really severe terrain.”
Working credentials
The eTrak can be fitted with carry racks on the front, rear, and sides to transport hay bales, silage, or even livestock, with capacity for up to a tonne on the platform.
It also has impressive towing credentials, with the maker claiming it will pull 2.5t with ease.
In terms of maintenance, Mr Taylor says it is a simple tracked format. “Any farmer would recognise the system. There’s nothing on there that you need any special skills to be able to look after – like changing the wheels or the tracks. It can all be self-managed.”
Operator space and handling
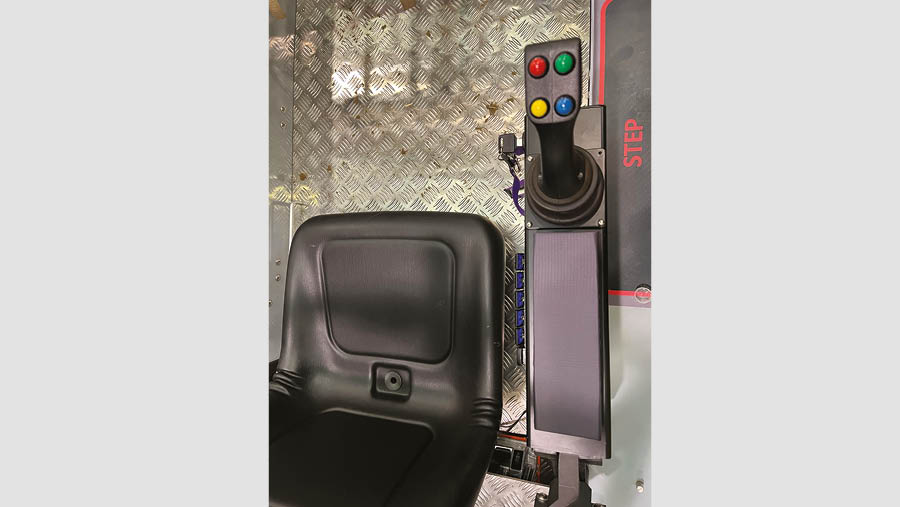
© MAG/Oliver Mark
The cab space is simple, comprising only a seat or two, an armrest and a controller.
An old telehandler-style joystick is the chosen method of control for the eTrak, with the goal that any operator can jump in and drive it.
The joystick is mounted to the right-hand armrest, which has been designed and 3D printed by the University of Hull. It is simple to operate with a push/pull speed control and forward and reverse motion, and side-to-side steering. For farmers using the machines for a specific purpose, the manufacturer can also programme the angle and severity of the turning motion to suit the job at hand.
It can be controlled remotely via a mobile app too, with a “big red button” that can be pressed to mimic the motion of the joystick to trigger forward and reverse, and to change direction.
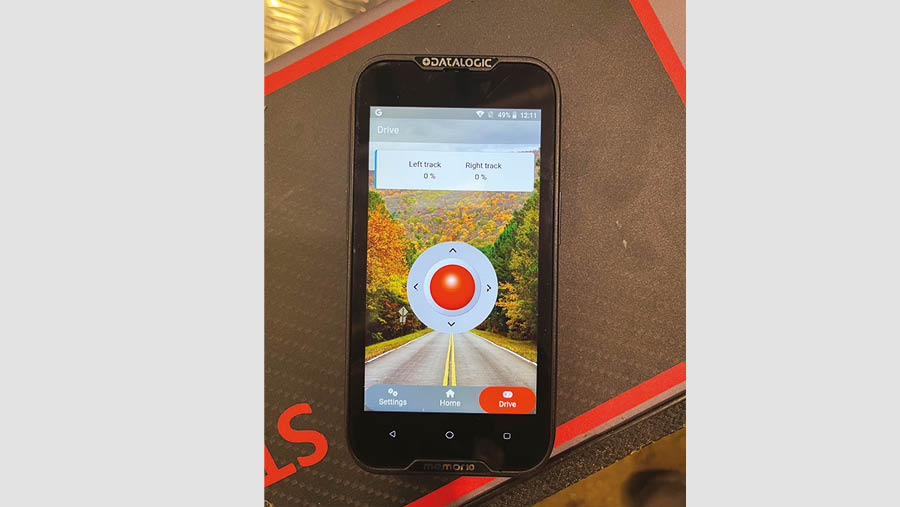
© MAG/Oliver Mark
Safety features
Lidar sensors are responsible for object detection, and will automatically shut down the machine if it picks up an obstacle or person within close proximity.
“We’re also working on a ‘take me home’ function as a safety feature for farmers working alone,” says Mr Taylor.
In the case of an emergency or injury, this system allows farmers to send an alert to family members, and can even be programmed so that the eTrak will follow the same path it has taken in order to return to the farmyard autonomously.
This is supported by a GPS mapping system, which can learn and store the boundaries and field data on the farm.
An anti-theft GPS tracker is also fitted to the machines, although Mr Taylor says would-be thieves will struggle to make away with it in the night, as it can’t be wheeled or pushed when it is turned off.
The on-board cameras can also be accessed via the mobile app, so that managers or family members can check that operators are safe and the machine can be remotely monitored.
What’s next?
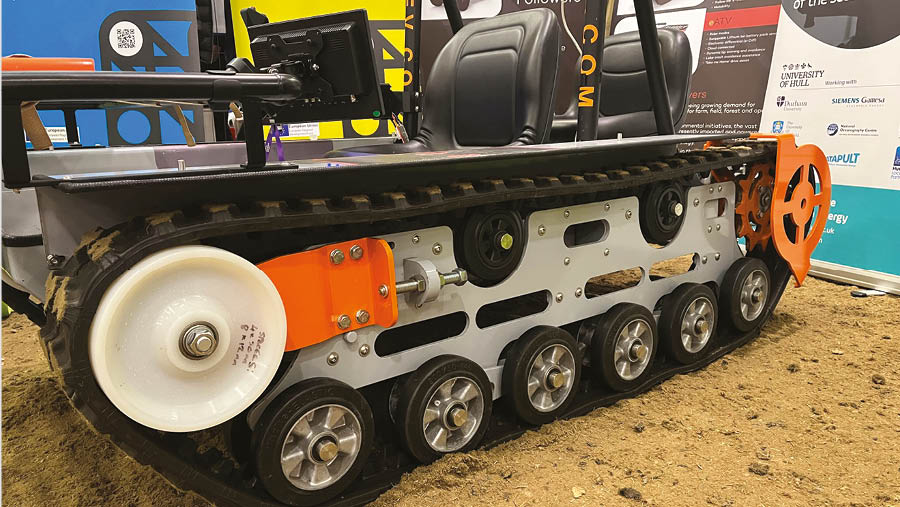
© MAG/Oliver Mark
The pre-production model of the eTrak is based on a chassis that is easy to tweak and adapt, and the firm has plans to increase its size in the near future.
“The motors at the back are independent and we are not tied to an axle, so we can make the platform wider to accommodate bench seats for more workers,” says Mr Taylor.
The current model of the eTrak will retail for between £16,000 and £17,000.
Proposals are also under way to add an electric UTV to the line-up – though this is dependent on getting funding approved.
Built from the ground up, Mr Taylor reckons this vehicle will have the edge over some competitor brands that have swapped out the combustion engine in favour of electric without redesigning the chassis.
If successful, the plan is to begin production of the UTV during the summer of 2023.
In the meantime, an electric ATV is also in the pipeline, with designs already being finalised ahead of a manufacture start date next year.
“The chassis for this is being designed already,” said Mr Taylor. “We are using a low carbon-bonding method instead of welding, which is hugely energy-intensive. We want to be able to produce this entirely in the UK, without the need for imported parts.”