What’s in Your Livestock Shed? visits an £11m research unit
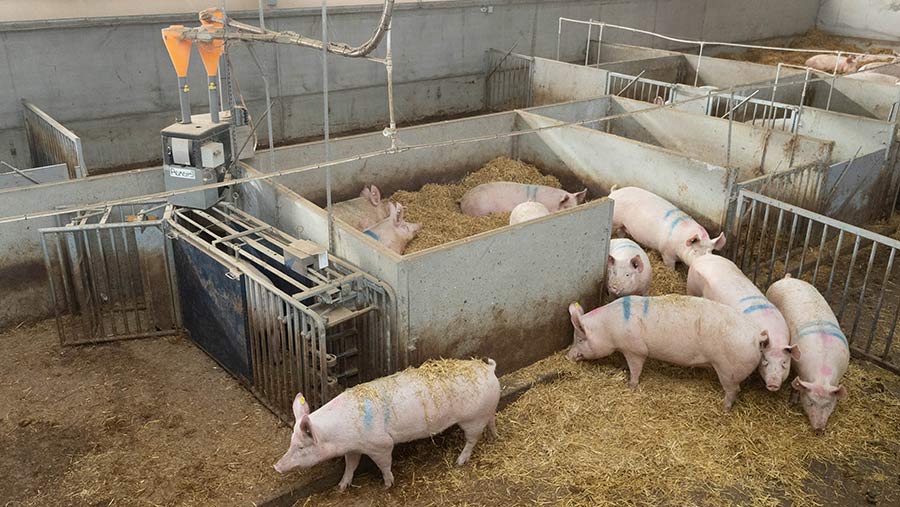
A multimillion-pound pig research unit has been designed to test the commercial value of new technology.
The £11m unit was the brainchild of Leeds University professor Helen Miller. Its aim is to be a “proofing-ground” for new technology in the pig sector.
Prof Miller collaborated with the Centre for Innovation Excellence in Livestock (Ciel), and a grant from Innovate UK helped turn the idea into reality.
See also: Environmental pig permits: Everything you need to comply
The university farm is run entirely on commercial grounds, so the research team can carry out trials in a real-life setting.
This ensures results and findings are entirely relevant for commercial producers.
Initial discussions began in 2015 and the National Pig Centre opened its doors officially in 2019.
Ryan Clarkson, facility platform manager, gave us a tour, starting in the farrowing house, which hosts up to 720 piglets every three weeks.

Piglets nursing in one of 120 individual farrowing pens © Tim Scrivener
Farm facts
Spen Farm, Tadcaster, North Yorkshire
- 440-head breeding herd
- Three-week batch system – up to 720 piglets every three weeks
- More than 5,000 growing pigs within the indoor herd at any one time
- All pigs are tagged individually and can be tracked from birth to slaughter
- 220-head outdoor herd, with piglets sold at weaning
What is the design specification?
The 1,489sq m farrowing house contains 120 individual, fully slatted farrowing pens equipped with opening crates for loose-nursing sows.
Each sow is fed through an air feed system according to her individual feed curve.
The 2,607sq m nursery building has nine rooms, with a total capacity for 2,160 weaner/grower pigs.
Rooms offer interchangeable pen sizes, so researchers have the option of housing pigs in pens of five, 10 or 20.
All nursery rooms have two separate water lines, allowing for water-based treatment trials.
Specialist rooms with automatic tracking of individual feed intake, water consumption and weight are also available.
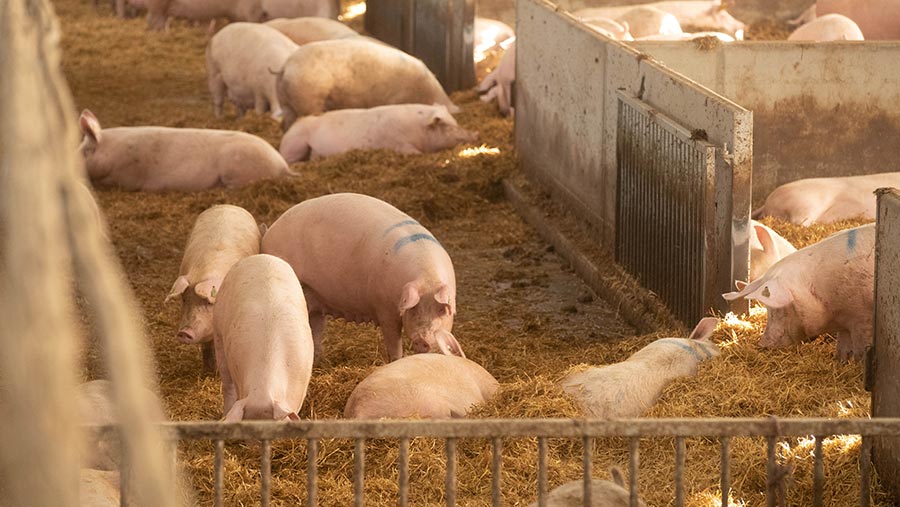
© Tim Scrivener
There are 2,880 finisher spaces across four separate buildings. These are fully slatted and can house pigs in groups of 10 or 20.
Again, some rooms have specialist equipment for individual monitoring, and one is equipped with individual slurry pits to allow for comparative analysis.
The 1,732sq m sow unit houses sows and gilts on a straw-based system and feeds individually from electronic sow feeders supplying a choice of six diets or specific blends.
Electronic tagging enables the full tracking of sows and their piglets.
The automated feeding and pig weighing technology spans each stage of production, so the entire life of the pig can be monitored.
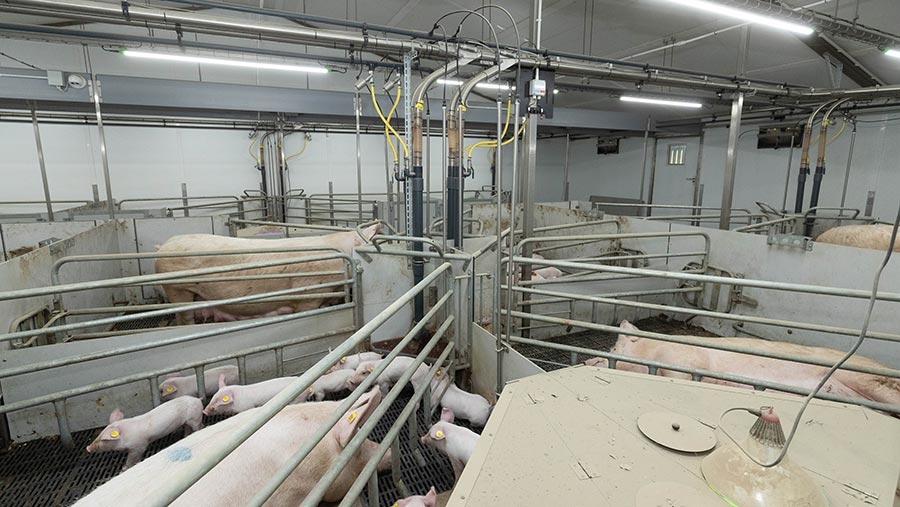
Adjustable, temporary farrowing crates allow for loose nursing © Tim Scrivener
Who designed and built the unit?
AM Warkup designed the buildings, and Hall Construction was responsible for the build.
How much did it cost?
The collaboration with Ciel brought with it a £4.5m grant from Innovate UK and the university provided the rest. The total came in at about £11m.
The unit also includes the Nigel Bertram visitor centre, funded by an alumni donation.
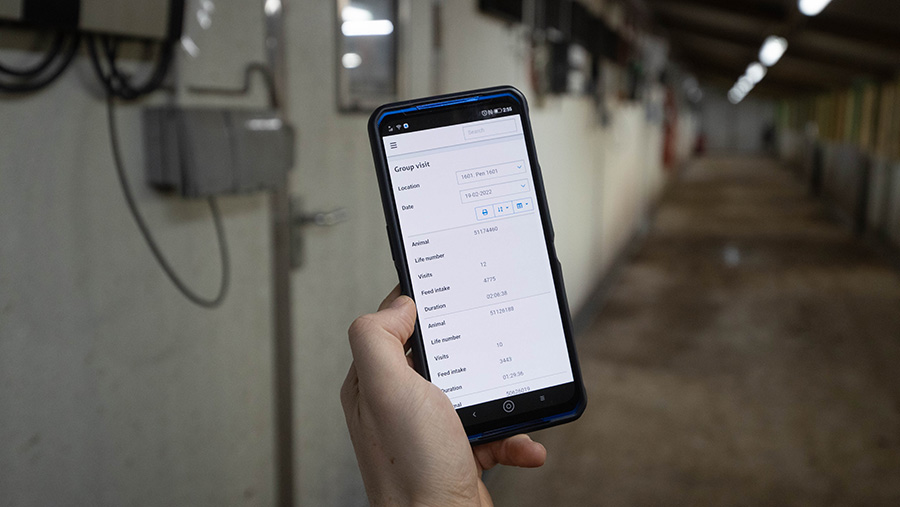
Data are gathered and held on a cloud-based recording system © Tim Scrivener
What is your favourite feature and why?
The sow shed, because it has a lot of really beneficial, commercially viable technology.
We have about 440 dams in total and five batches gestating at any one time. Individual tagging means the sows can be kept in one dynamic group.
Every time a sow feeds, a separator on the feeding bank can be triggered to draft her out to a separate area within the shed, if she has been programmed to do so.
This is useful if certain batches are due a routine vaccination or if they need to be moved into the farrowing house, for example.
It is as easy as a click of a button and the rest is done automatically. This is better for the pig, but also for the stockperson, from both a labour and safety perspective.
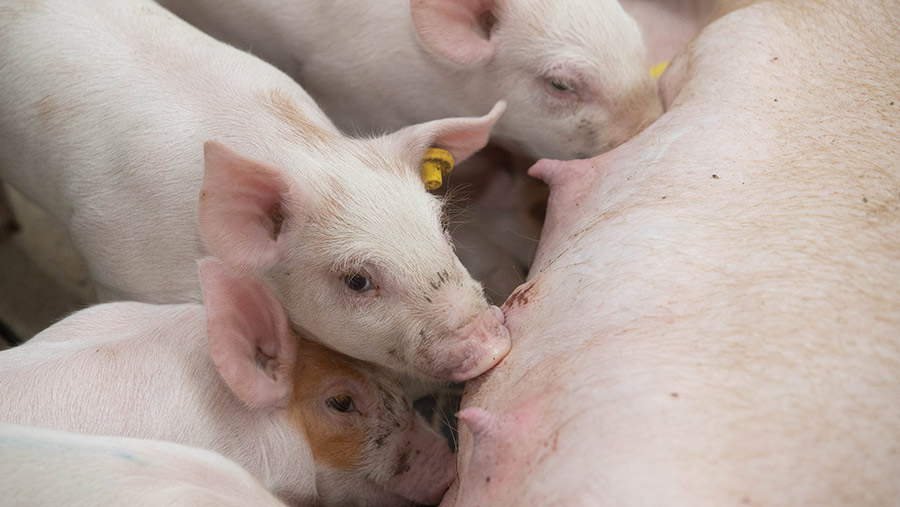
© Tim Scrivener
It is even possible to set this to draft out an individual sow if she needs closer monitoring.
The drawbacks of housing sows in a dynamic group are mitigated by the technologies.
For example, competition for feed is negated as sows have free access to feed stations which restrict access while a sow is consuming her daily ration.
The automatic monitoring benefits have been extended to a boar pen, where a device records visits by a sow to a hole in the pen where she can see the boar.
An algorithm monitors how frequently the sow visits, and for how long, and is set up to alert the farm team of three sustained visits to the boar – which has proven to be an accurate indicator that the sow is not in pig.
If she is suspected not to be pregnant, she will be automatically be drafted and integrated within the next service group to reduce empty days.
Feeding diets and curves are also automated, meaning the diet can be tailored accordingly to parity, sow condition and seasonal changes such as temperature.
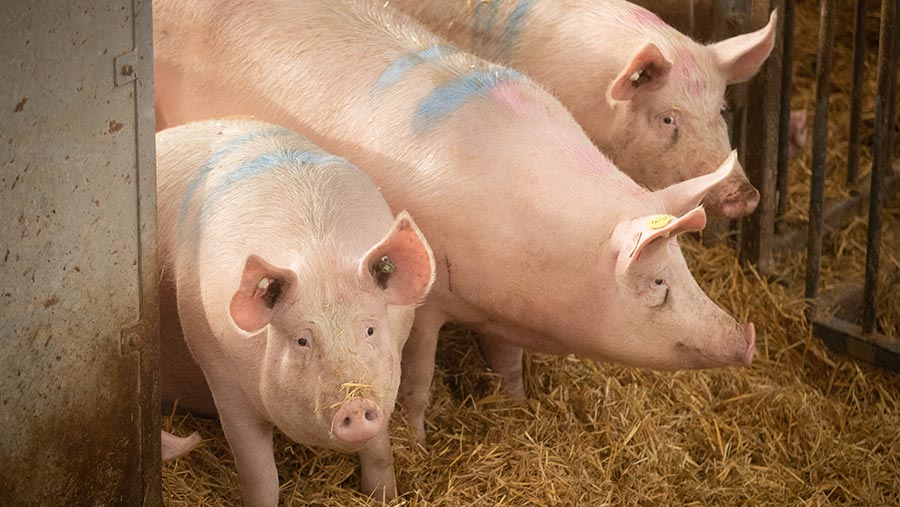
© Tim Scrivener
What would you do differently if you were to build it again?
Because of the nature of the unit, we were able to ensure the building design and technology encompassed the “best of the best”, so it is hard to really pinpoint something we would do differently.
However, we would like to introduce and integrate renewable energies. This would also fit in well with our ambitions to understand how pig production can be made as sustainable as possible.
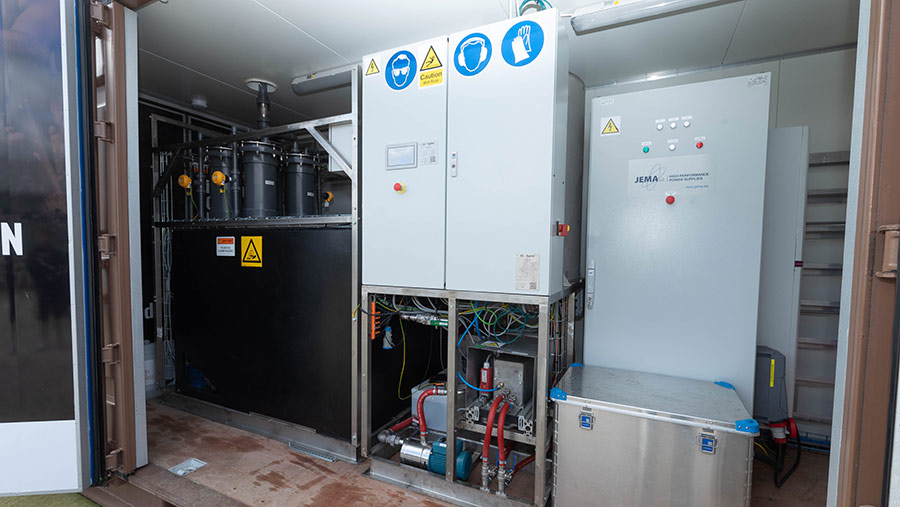
© Tim Scrivener
How affordable is an £11m unit for other farmers?
The whole ethos behind the unit is to look at new technology and test its worth as a commercial investment, explains facility platform manager Ryan Clarkson.
As such, the entirety of the unit is unlikely to be affordable for sole producers. However, within the unit, the individual technologies are on a more affordable scale.
Justifying the extent of this technology is something the research team is continuing to look at.
Technologies of interest within the unit include:
- 24/7 CCTV across the entire unit to allow remote monitoring/observations without disturbing the pigs’ natural environment
- Electronic tagging on every animal for automatic daily data collection
- Automatic feeding equipment that monitors individual animal intake
- A technical platform to identify individual pigs genetically via their DNA
- Open, adjustable, temporary farrowing crates
- A brand-new N2 applied unit for the conversion of slurry into fertiliser
- Different coloured lamps in the farrowing house (part of a current study into whether colour effects the time spent in the creep area).