What’s In Your Livestock Shed? Comfort for 50-point rotary
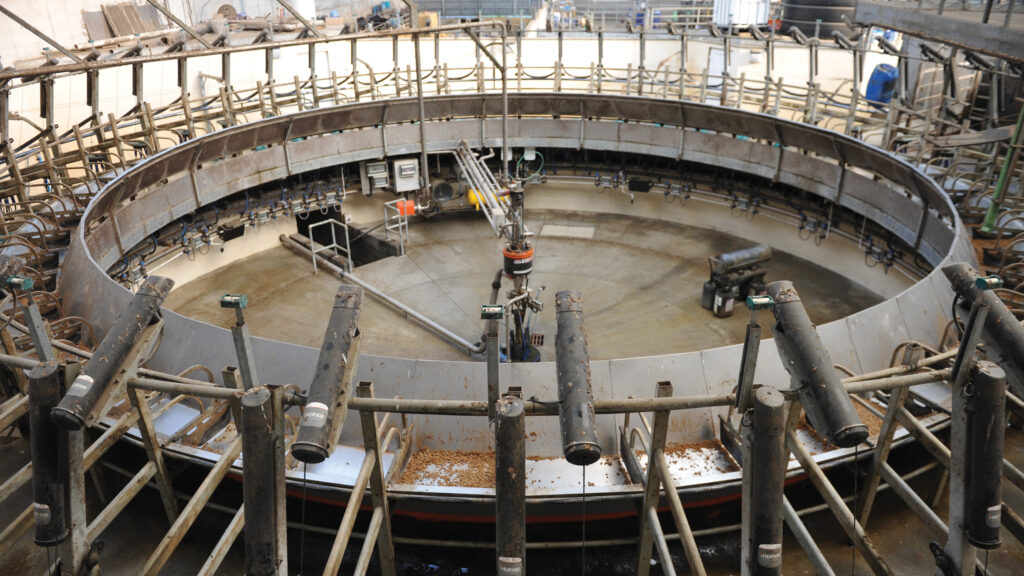
Prioritising cow comfort and wellbeing in the design of new housing has boosted average annual milk yield by 1,000 litres a head at a Welsh dairy farm.
Features include waterbeds, flexible cubicles and slatted flooring with slots shaped for good grip.
These, together with a robot feed wagon and UV-treated polycarbon roofing sheets that let in light but deter heat, have helped increase lying times and virtually eliminated white line disease.
See also: 5 ways to fine-tune cubicle housing for udder health
Farm facts
Drefach Farm, Whitland, Carmarthenshire
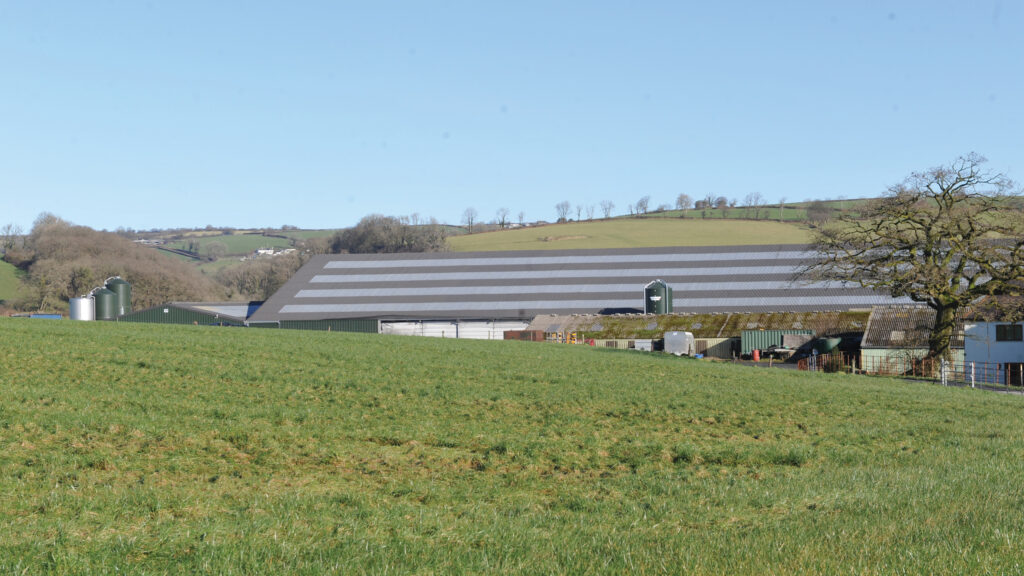
© Debbie James
- 223ha owned and farmed
- 350 pedigree Holstein Friesians
- Average yield 9,600 litres at 4.3 % butterfat and 3.4 % protein
- 2.75t concentrates fed a cow a year
- Milk sold to Leprino
- Flock of pedigree Charollais sheep
- Five-cut silage system
- 20ha maize grown followed by hybrid barley and triticale
- One full-time employee plus three relief milkers
- 50kW roof-mounted solar array
- 500kW wind turbine
A 50-point rotary milking parlour with a 30,000-litre milk tower has replaced a 16/32 swingover.
The shed and associated infrastructure at Drefach Farm, near Whitland, Carmarthenshire, resulted partly from necessity because pressure on housing meant heifer replacements had to be wintered off-farm.
This increased costs and labour time, as feed and straw had to be hauled to the heifers daily.
For farmers Gethin and Eleri Gibbin, removing that cost and time added weight to the business case for developing more housing.
“The cows go out to graze, but we leave the shed open, and once they have had their fill of grass they mostly wander back in – even without the prospect of feed – because it is around 6C cooler and they can rest and cud and be more comfortable,” says Gethin.
The couple gave Farmers Weekly a tour of the building housing their 350-cow Llangan herd of pedigree Holstein Friesians.
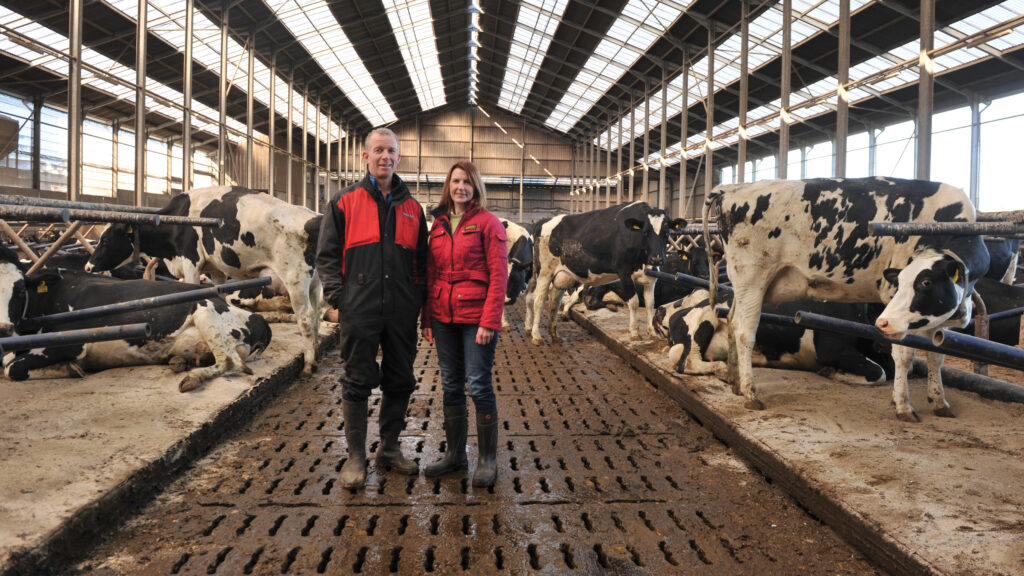
Drefach Gethin and Eleri-Gibbin © Debbie James
What informed the design?
We visited 25-30 dairy farms with slatted sheds in the UK, Belgium and the Netherlands.
It was apparent that comfort doesn’t revolve around one thing – it’s all very well having one component, but if the others don’t marry up, any benefit is minimal.
We wanted to create the ideal environment that promoted the needs of the cow, to allow them to express their potential. We took any ideas that worked in the old setup and replicated them.
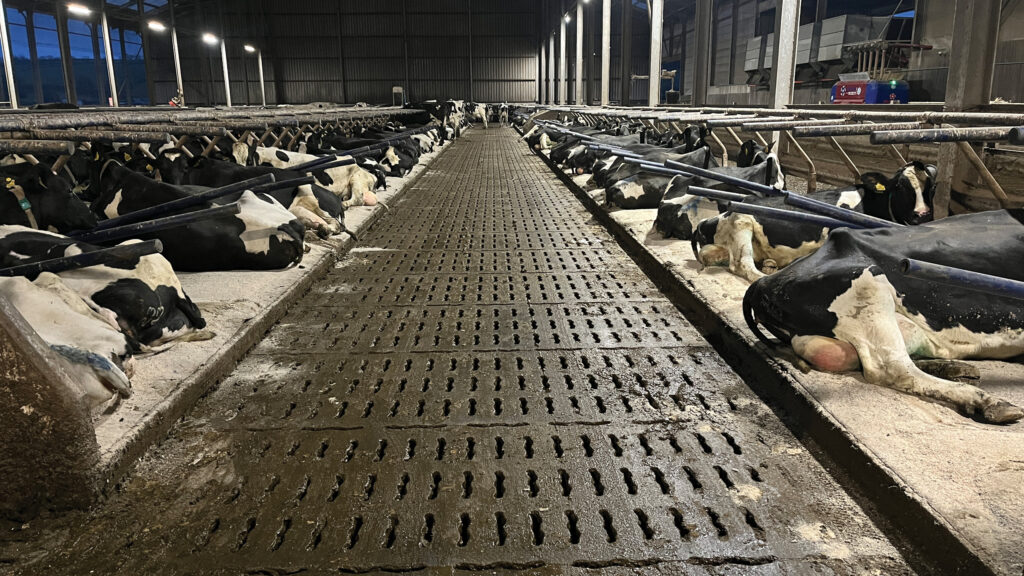
© Debbie James
What was your initial budget, and did you stick to it?
Originally £1.2m, but after the visits we revised it to £1.5m.
We scratched our heads for hours trying to work out ways of cheapening the job, but it is a shed that is used 24/7, 365 days of the year, so it had to be right.
Experience tells us jobs that don’t get done right in the first place never get done, so it is better to do everything well, and do it once.
Who constructed it?
Local contractors were used for all elements of the build.
What are the dimensions?
The shed is two portal frame buildings totalling 105x37m, and 18m at the highest point, with a 20deg roof pitch instead of the more usual 12.5deg.
The ventilation is so good that even in very hot weather we never feel any need for fans.
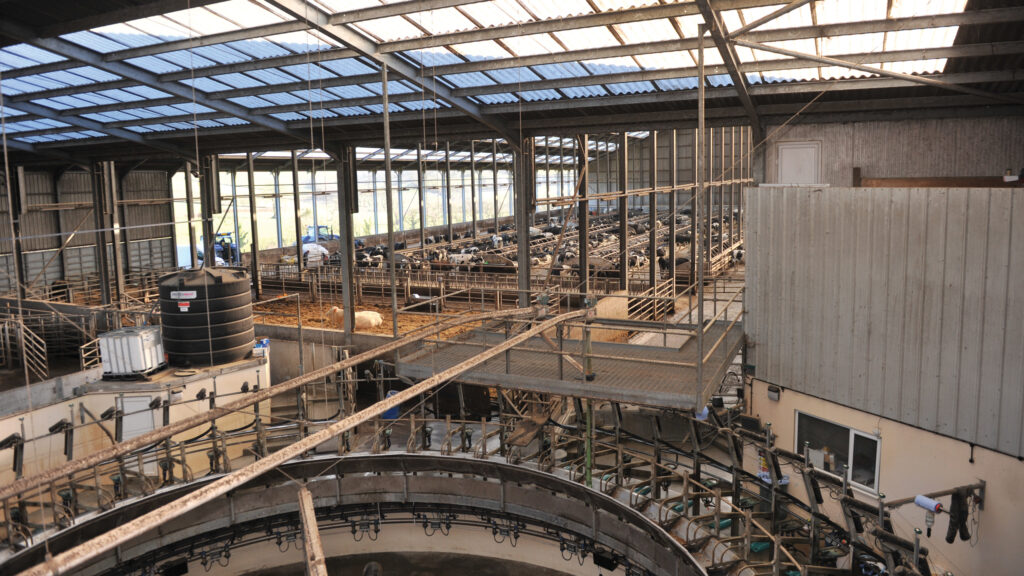
© Debbie James
What is your favourite feature?
The Van Hessche Beton slatted flooring. We have always favoured slats, but these have S-shaped slots rather than straight ones, so feet don’t roll into them, and the shape prevents slippage.
They are far more comfortable for cows, much better for their feet – we hardly ever get white line disease.
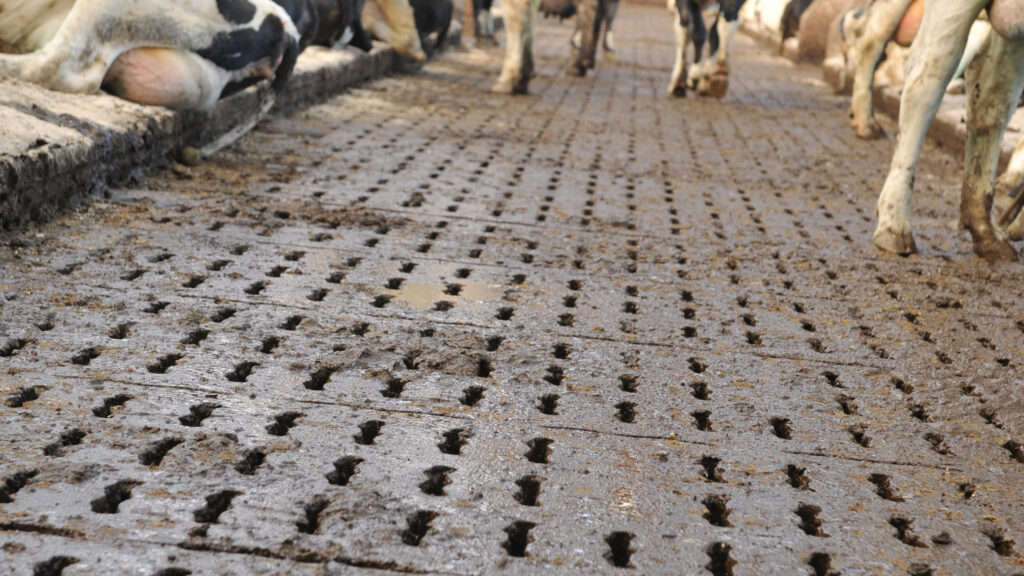
© Debbie James
Regular foot trimming has played a part, too, but the new environment has definitely helped.
The cows are happier moving around the shed and we see more bulling activity.
A Lely robot scraper cleans the passages twice every 24 hours, which keeps the cows’ feet clean and dry.
The tank beneath the slats, which operates on a slalom system, has helped us comply with Nitrate Vulnerable Zone regulations because it has given us 4,546cu m of extra slurry storage and that, coupled with our existing 9,092cu m lagoon, provides storage for nine months.
What could you not live without?
The robot feeder is the icing on the cake because it has taken away a mundane but very important job.
The principal reason for buying it was because cows weren’t getting fed as quickly as we would have liked when we were calving in the autumn.
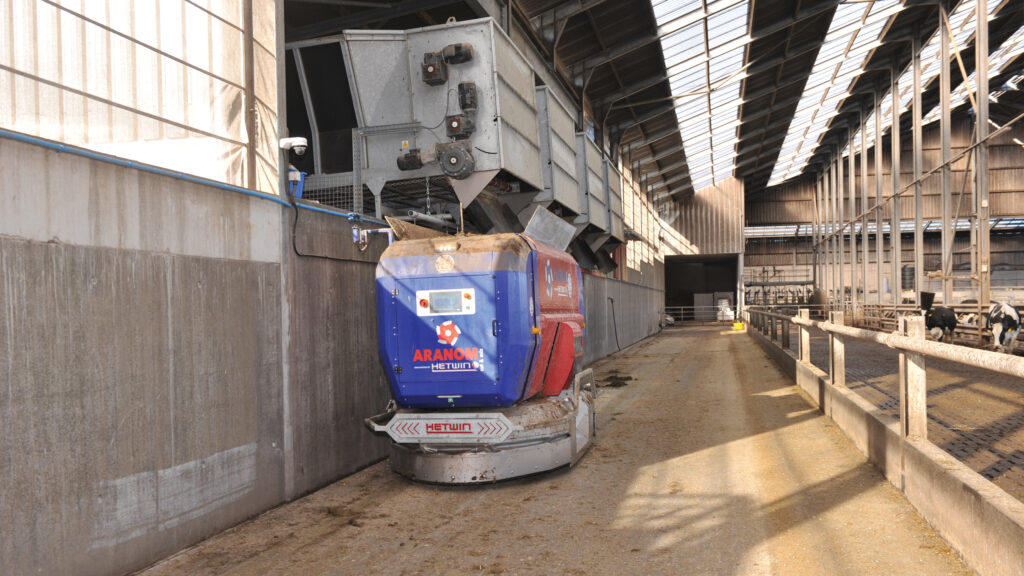
© Debbie James
There are two people on duty at milking: one in the parlour, and the other feeding and overseeing the calves.
During calving, the priority is to get colostrum into the calves, but that meant cows – hungry fresh calvers – sometimes had to wait two hours to be fed.
There was a feeling of guilt came with that; we were also losing out on production, and stress was probably hitting health and fertility.
Options were either to employ someone to feed (but it was unlikely we would get someone willing to come in at 5am for an hour’s work) or get a machine to feed for us.
We looked at quite a few makes, but they didn’t have sufficient capacity for our number of cows, as most had 2cu m capacity. The one we bought – a Hetwin, the first in the UK – has 4cu m capacity.
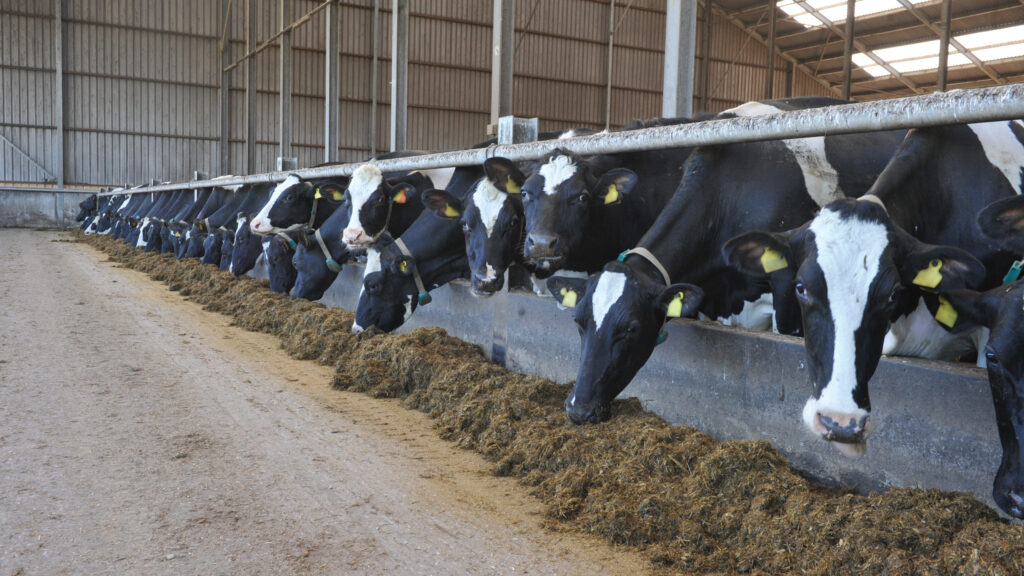
© Debbie James
It moves around the perimeter on magnets powered by batteries from our solar array and works with our layout without interfering with cow traffic, because the feed passages are outside the living area.
The robot feeds and pushes up the ration 15 times a day – we liken it to being on board a cruise ship with access to fresh food 24/7.
It has eliminated variation and waste because it weighs all ingredients with complete accuracy.
Cow behaviour has changed – cows used to chase the tractor and feed wagon around the shed to be the first to get feed.
Now, because they know feed is coming their way wherever they are in the shed, they just go to the nearest feed fence, and that has increased lying times.
What were your best buys?
DCC dual-chamber waterbeds.
All the cow mats we had previously eventually bottomed out around the hip and udder areas, and those hollows trapped milk creating issues with mastitis.
The waterbeds re-form every time the cow gets up, they never lose shape and any milk or urine runs away.
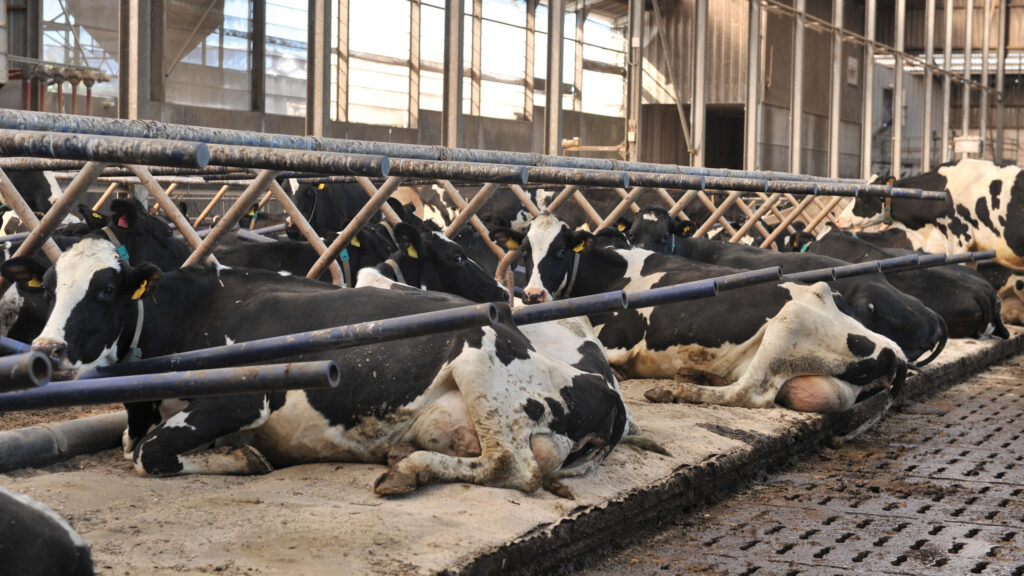
© Debbie James
There is the comfort of the bed itself, but we are also saving on bedding because we hardly need any sawdust – around 75% less than before.
Each bed cost an extra £30 over a standard mat, which is more than covered by savings on bedding, and cows don’t get swollen hocks.
The Agriprom flexible cubicles were also a good investment, as we don’t get rub marks, swelling or hair loss. The cubicles have enough give in them to move, but are not overly flexible.
They are plastic so are not cold like metal cubicles, so on a cold day we see cows lying against them, not drawing away.