New slurry tech for storage and handling benefits pig farm
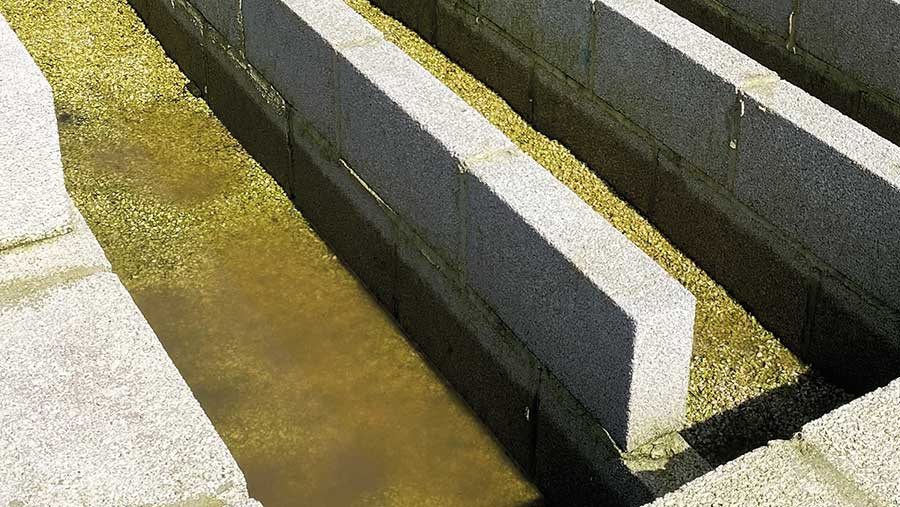
A seaweed-based prebiotic treatment is dramatically reducing the volume of slurry to be stored and handled on a South West pig farm.
The treatment results in water that – subject to permit – will be clean enough to be returned directly to watercourses.
The process, which is being used for cleaning waste water elsewhere in Europe, also produces an added-value solid product that can be used as a natural fertiliser with highly available nutrients, or as a feedstock for anaerobic digestion (AD).
This will help the farm – the first in the UK to use the technology for livestock slurry treatment – in its overall aim to build a circular farm economy.
See also: New tech to treat farm slurry and produce fertiliser trialled
Farmers Weekly spoke to the farmer, who asked not to be identified, David Cosford, director of Ekogea UK, which developed the technology, and Jonathan French, director of Green Circle Feeds, which is working with Ekogea.
The indoor breeding unit sells 7kg piglets. It is a closed herd and feeds home mill-and-mix diets using locally sourced cereals and beans.
About 20cu m of slurry/day is produced by the unit, and early indications are that the Ekogea concentrator’s processing capacity is about 45cu m/day.
Key benefits of slurry treatment system
- Reduces volume of slurry to store and transport
- Cuts ammonia emissions
- Produces a low-volume, nutrient-rich feedstock for AD plants or a nutrient-rich biofertiliser
- Nutrients can easily be tailored to crop demand
- Technology is energy-efficient
The process and outputs
1. The slurry goes through a conventional slurry separator, leaving a solid fraction (about 5% by volume) and liquid slurry.
2. This liquid slurry then goes into an Ekogea concentrator tower, where a mixture of flocculant and coagulant further separates the slurry.
This creates a pumpable solid containing about 10% dry matter that retains the majority of the phosphate (P), and a liquid (about 85% of total slurry volume) containing the nitrogen (N), known as grey water.
3. N can be recovered in the solid fractions if desired by adding the seaweed-based prebiotic BioComplex before the concentrator process.
Currently, 85% of the liquid is consistently being removed from the liquid slurry on the farm, leaving 15% in solid form.
The solid can be used or sold as a nutrient-rich biofertiliser or as an efficient AD feedstock. This producer has no arable or grassland demand for fertiliser, so is looking to secure contracts to supply local AD plants.
If there is a requirement for N on owned or nearby land, the grey water can be retained and spread as N-rich fertiliser, without adding excess P or potassium (K) to the soil.
In this case, the producer has no need for the N and has begun cleaning the grey water using BioComplex.
4. A dosing pump automatically adds the prebiotic to the grey water before it flows under gravity into the Ekogea H2e waste-water treatment plant.
The H2e plant is a concrete basin full of Cristobalite, a pumice-like gravel, and the BioComplex “seeds” the biology onto the Cristobalite.
Once the plant is seeded and operational, the grey water circulates through the plant until the BioComplex, and the beneficial microbes it supports, have removed the N and other contaminants to the permitted levels.
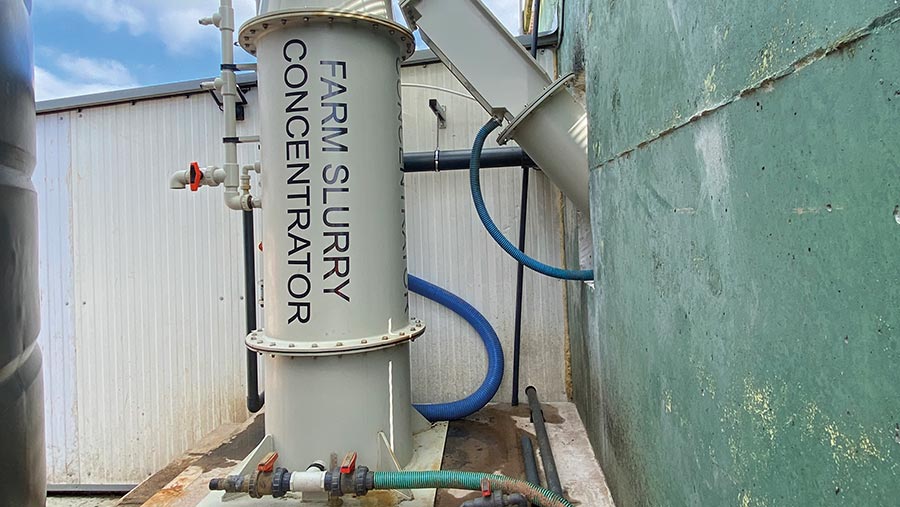
The concentrator tower © Helen Brothwell
The system is sized to suit each application. The H2e waste-water treatment has been working for two months on this farm and the water looks visibly clear.
Regular testing of the outputs is now under way, and the farm has applied for the necessary discharge permit to release the processed water into a stream.
Some of the water will be used on the farm for washing down pig accommodation and equipment.
The whole system is highly energy efficient, using less than 1kWh of electricity to process 1cu m of slurry through the concentrator tower and pumps, while the H2e waste water system is gravity-fed and the BioComplex additive is organic.
Biofertiliser value
For use as a fertiliser, separation of the N from the P and K helps tailor nutrients to crop demand.
Evidence indicates the biofertiliser is richer in nutrients that are more “plant-available”, so less is needed to deliver the same quantity of P and K as untreated slurry.
The biofertiliser has also proven to be a valuable feedstock for AD.
This is because the water and ammonia are removed from the slurry and the same level of gas-producing dry matter is available in only about 15% of the original volume.
This gives it a big advantage over untreated pig slurry, which contains levels of ammonia that inhibit biogas production, and the biofertiliser can replace crops as feedstock for biodigestion.
The farm is awaiting the results of nutrient analysis of the solids produced so far.
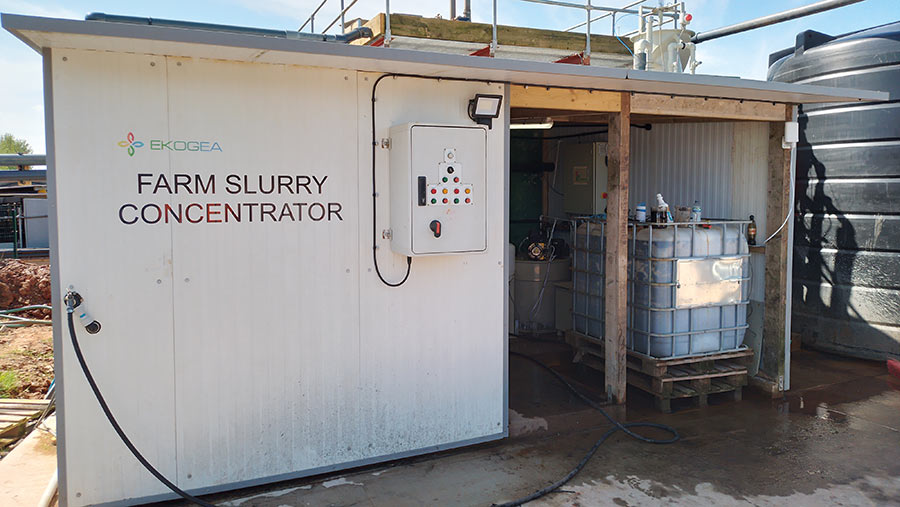
A shed houses pumps as well as dosing and monitoring equipment © Helen Brothwell
Cost benefit
The whole investment, including slurry separator, concentrator tower and H2e waste-water treatment plant, came to just under £150,000.
The payback period will differ by farm but is expected to be within three to four years, through savings in slurry handling bills based on a contractor rate of £50-£60/hour.
For a new build, installation would avoid the need for a slurry lagoon, at a cost of about £250,000, or the need to cover an existing one.
As well as the cost savings, the farmer hopes to benefit from selling feedstock to AD, which is worth about a third of the value of maize feedstock.
Troubleshooting
The consistency of the slurry input is important, so the separation of larger particles and pig hairs from slurry is completed by the initial separator and screen.
The whole system is automatically monitored from a control panel located in the equipment shed or remotely from the farm office.
This means if there is a clogged pipe or fault, the system will stop automatically and clear the blockage before restarting.
Next steps
Over the coming months, the farm will continue to work with Ekogea to adjust the concentration process to see how much liquid can be removed from the dirty water. Potentially, this could reach 90%.
The producer is confident the Ekogea BioComplex system will reduce ammonia emissions and carbon footprint, avoiding the need for multiple tractor and slurry tanker trips.
At the same time it will produce a valuable asset from waste, with longer term potential to provide energy and fuel via AD production.
Wider application
The slurry treatment system can be applied to dairy slurry in the same way, and BioComplex is also being used as a prebiotic additive in pig and poultry diets.
This provides another route to improve pig health and performance, reduce ammonia emissions and improve slurry management on farm.
BioComplex explained
BioComplex is a natural prebiotic activator made from seaweed, which is sustainably harvested from the Sea of the Hebrides waters.
During processing, the seaweed cell structure is broken open to release higher levels of oligosaccharides and polyuronic acid.
Polyuronic acid makes the nutrients bioavailable and removes odours, while oligosaccharides provide energy to boost populations of beneficial microbes.
In the liquid removed from slurry, polyuronic acid converts volatile ammonia into crystalline ammonium.