How a Wiltshire dairy makes better use of slurry
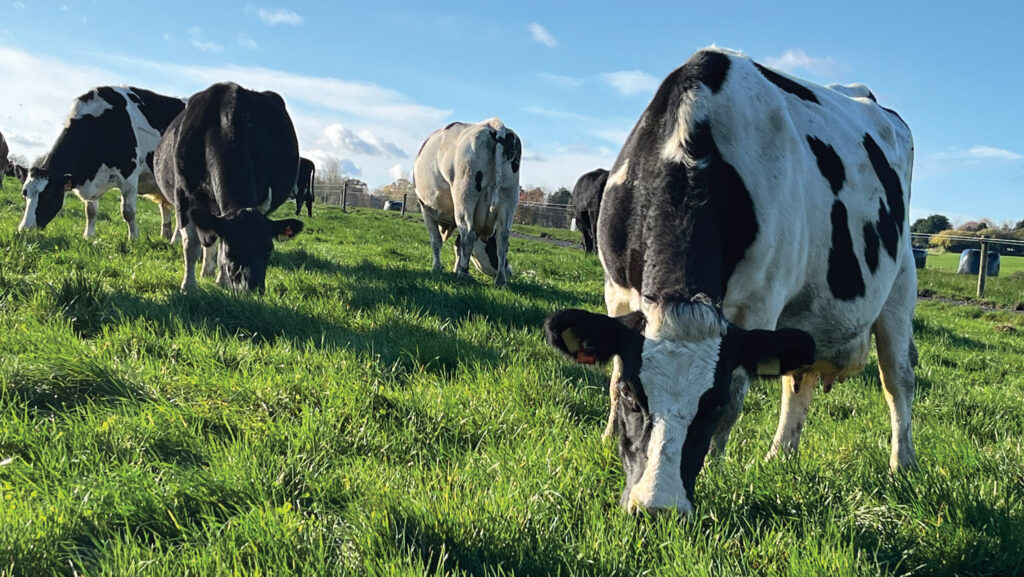
Investment in a new slurry system on a Wiltshire dairy farm has resulted in a drop in bagged nitrogen use of more than 100kg/ha a year on the grazing platform.
Herd expansion in the past decade, from 150 high-yielding Holsteins to 600 crossbred cows, had put pressure on the old slurry setup at Wolfhall Farm, Marlborough.
See also: 5 ways to cut nitrogen use on grazing ground
With confirmation from the Environment Agency in 2022 that the old earth bank lagoon serving the split block-calving herd was no longer compliant, farmer Tom Blanchard decided it was time to invest in new storage, separating and handling facilities.
Once compliant with legislation, his aim was to reduce the need for bagged fertiliser on grassland and explore the benefits of using slurry on the 160ha (395-acre) milking platform, rather than directing it mainly to the arable and beef enterprises.
This has been successful, reducing the artificial nitrogen (N) used from 250kg N/ha to 140kg N/ha, topped up with 45kg N/ha from slurry.
However, while growing 16t/ha of grass a year, with a huge focus on profit through grass utilisation, the change in approach for this AHDB strategic dairy farm has not been without its challenges.
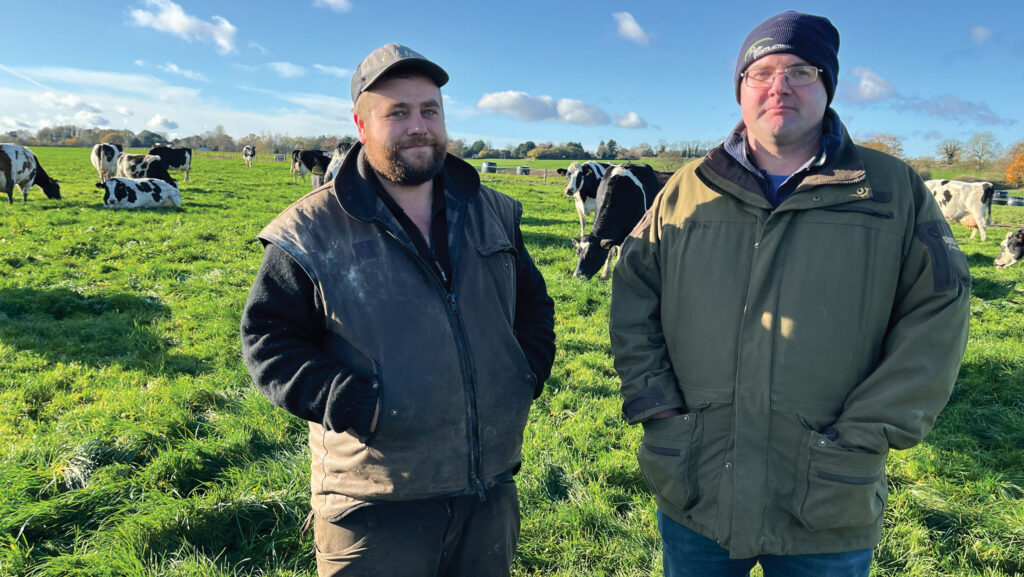
Antony Miller (left) and Tom Blanchard © Hayley Chapman
Farm facts: Wolfhall Farm, Marlborough, Wiltshire
- 600 cows, calved in a split block
- Supplying Wyke Farms
- Milk yield of 5,800 litres at 4.7% butterfat and 3.8% protein
- Grass-focused system with autumn calvers fed 1.2t concentrate a cow a year and spring calvers fed 500-800kg a cow a year
- Grass leys, fodder beet and maize grown in rotation on 160ha grazing platform
What does the new system look like?
The new setup at Wolfhall, which provides eight months’ storage (11,000cu m), sees:
- Twice daily scraping of sheds
- Slats transferring manure and parlour washings to a Sperrin Optiflow separator, producing nearly 10t of solid material a day (20% dry matter (DM)), which is stored in field heaps for use on arable ground
- Liquid separated into a 1,387cu m plastic-lined lagoon, with overflow storage for a further 1,221cu m
- No separate fouled water store because water is needed for the separator to work efficiently and to produce a dilute slurry
- Slurry pumped 1km to field lagoons near grazing paddocks in winter months.
Spreading on the grazing platform
“Previously, everything went to one lagoon, but this year we had a full amount of liquid control, so we are spreading more now on the grazing platform,” said Antony Mitchell, dairy farm manager.
The grazing platform is predominantly ryegrass/clover leys, with chicory and plantain added in recent reseeds. These are stocked at a rate of 3.6 cows/ha.
Slurry has been spread, when ground conditions have allowed, on residual grass covers of 1,500-2,000 kg DM/ha, depending on when cows left the paddock.
A total of 16,000cu m has been spread this year (monitored by flow meter), at rates of 30-50cu m/ha, using an umbilical system and dribble bar.
Nutrient considerations
A lagoon composition of 43% parlour washings, 37% rainwater and 20% slurry at Wolfhall means the liquid slurry is very thin.
This makes pumping and spreading easier, reducing the risk of increasing potassium (K) levels in the soil and contamination.
“A dilute slurry will help to reduce bagged nitrogen without compromising yields, sward quality and animal intakes,” says independent consultant Chris Duller.
He advises that 50cu m of dilute slurry contains 15kg N and 50kg K, Tom needs to consider if that is enough N for a mid-season grazing round and whether grazing paddocks will become high in potash.
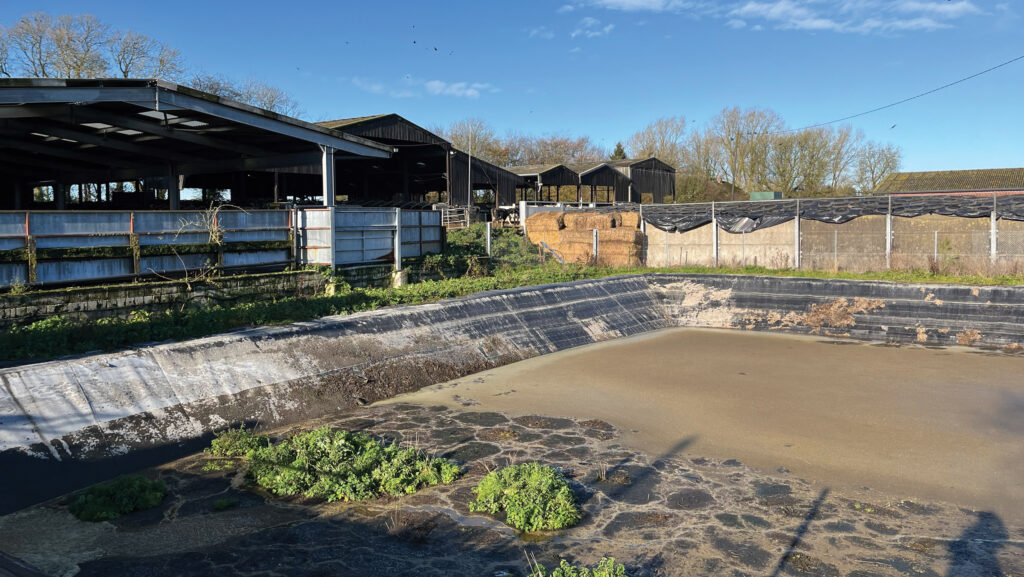
© Hayley Chapman
Utilisation challenges
The grazing platform at Wolfhall measures index 2-3 for potassium and phosphate, with ex-arable ground scoring slightly higher than permanent pasture.
Antony is not keen on building up covers to take a cut of silage as a means of reducing potash, because of the risk to regrowth.
Instead, he hopes the standing hay, maize and fodder beet in the rotation will help keep potash indices from increasing too much.
He believes they have nearly reached their limit of reducing bagged fertiliser. When trialling slurry-only fertiliser on some grassland, utilisation was hit.
“We targeted one side of the platform with only slurry, and it had a negative effect on growth. The grass would grow, use all the nitrogen and then crash. It looked yellow.
“Whereas, on the side where we also used bagged nitrogen, there was steady, consistent growth and quality,” he explains.
The impact was more visible in older, mixed swards than in ryegrass reseeds: “Utilisation was very poor on the slurry-only side, with 60% rejection – the potash made it bitter.
“I’d recommend to others to spread it around the platform at lower applications because you need cows to graze [the grass grown]. The profit is in the grass utilisation.”
Financials and future
The infrastructure has been a significant expense, with the separator alone costing £65,000.
“[However,] the return on investment is the ability to keep dairy farming,” said Tom, adding that he hopes it will have a positive effect on carbon footprinting.
Antony says the plan is to continue to use slurry on the platform but to spread it at low rates and top it up with artificial nitrogen, so that grass can grow consistently and remain palatable.
Slurry will be targeted in a “mix-and-match” approach, spreading watery slurry on high-index grass and using thicker slurry towards the end of the lagoon on land with lower nutrient indexes.
Soil and slurry testing will remain key to this.
- Tom Blanchard, Antony Mitchell and Chris Duller were speaking at an AHDB strategic farm event at Wolfhall Farm.
The numbers
- £1.50 Pumping and spreading cost/cu m
- 11,000 Slurry storage capacity (cu m)
- 10 Solids produced by slurry separator (t/day)
- 1 Dry matter of slurry spread on grazing platform (%)
Expert advice on slurry management
Independent consultant Chris Duller says there can be a conflict between meeting regulations and best practice where slurry management on grazing ground is concerned.
There is a risk that too much slurry can go out ahead of the closed period in October as producers desperately try to empty stores (with high risks of nitrogen loss and potential damage to soil health).
And spreading in mid-January can easily lead to problems with sward contamination in early grazing situations.
He advised the following:
Slurry separation and storage
- Separation gives more flexibility, with dilute slurry better for spreading on grazing land (less leaf contamination and much easier to apply through a dribble bar/trailing shoe).
- Separation reduces the storage capacity required by about 10-15% and allows more nutrient targeting, especially with mixed enterprises. The solids contain most of the phosphate, which can be applied to cropping ground with significant demand for this.
- Field heaps of separated solids need to be located carefully because of the risk of slumping – and ideally covered.
Spreading and nutrient management
- Nitrogen recovery is more efficient when spreading material with low dry matter (DM), which soaks into the ground. Thicker slurries will lose more nitrogen as ammonia, as they stay on the surface longer and are more prone to washing off the land. This can be particularly problematic with phosphate.
- Nitrogen availability increases by 5-15% with incorporation or low-trajectory spreading.
- In a grazing system, the main nutrient concern is the build-up of potash, which reduces grass utilisation and affects cow health and fertility.
- Soil indexes should be monitored, and a cut of silage will help counter the build-up of potash in the soil.
- Lower DM slurries reduce the risk of rising potash indexes on grazing ground and help avoid sward contamination, however spreading costs rise with the extra water being stored.
- Consider ground conditions to limit potential damage to soil health. If soils are wet and marking up, application rates should at least be reduced. Ideally, applications should be delayed until conditions improve.
- Be aware of negative impacts on animal health, through nutrient build-ups and pathogen risk.
- Spreading 30cu m/ha of slurry will supply the same amount of water as 3mm of rain, which may be enough to rescue a droughted reseed.
- In autumn, soil nitrogen levels are already high because of mineralisation of organic nitrogen over the summer and clover fixation. This, coupled with low demand from grass, means that any autumn-applied slurry is likely to produce high nitrate leaching.
The financial value of slurry and farmyard manure |
|||||
|
Dry matter |
Available nitrogen (N) |
Available phosphorous (P) |
Available potassium (K) |
Value of available NPK |
Cattle slurry |
2% |
0.72 kg/cu m |
0.3 kg/cu m |
1.53 kg/cu m |
£1.87/cu m |
Cattle slurry |
6% |
0.91 kg/cu m |
0.6 kg/cu m |
2.25 kg/cu m |
£2.81/cu m |
Farmyard manure |
25% |
0.6 kg/t |
1.92 kg/t |
8.46 kg/t |
£7.30/t |
Source: Chris Duller |