How a dairy farm is using a straw dryer to reduce waste
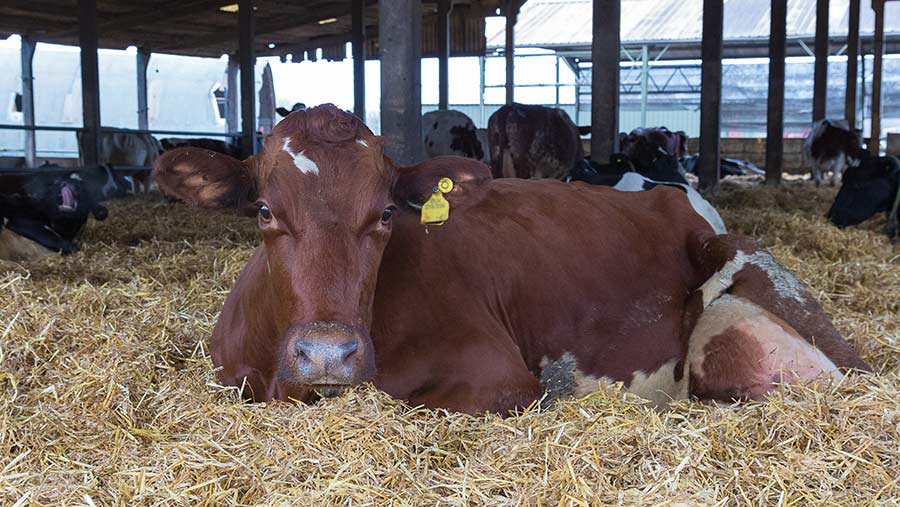
Farmer Jonny Wyatt is using waste heat from the anaerobic digester (AD) plant on his mixed farm near Thetford, Norfolk, to dry out-of-spec straw to make drier bedding for his livestock.
The resulting farmyard manure is then fed to the AD plant to produce energy for the farm and digestate to fertilise the grass for the dairy herd.
The aim is to improve the environmental sustainability of the farm business, reducing waste and making the best use of the “waste” that is produced while lowering somatic cell counts (SCCs).
See also: How a dairy farm is using renewable energy to reduce fixed costs
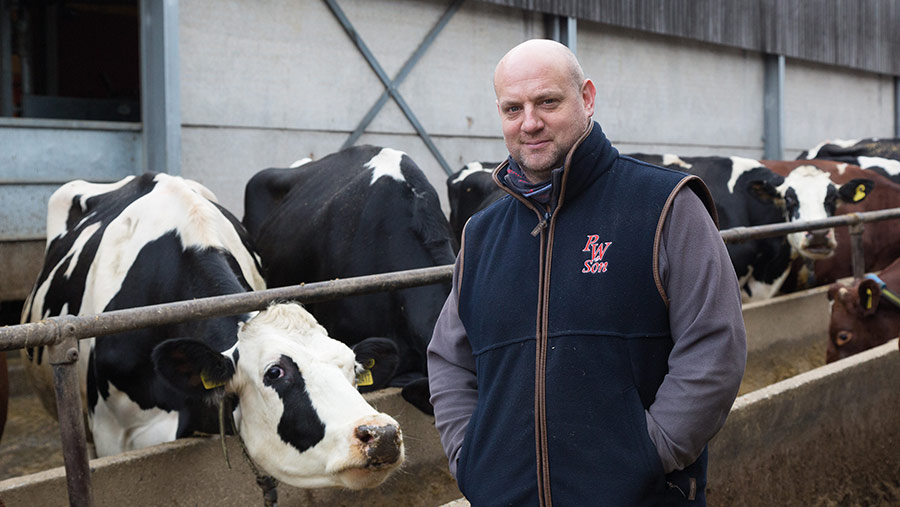
© MAG/Judith Tooth
Farm facts
- 240 pedigree Holstein and Shorthorn cows
- Autumn-biased calving
- Average lactation 8,500 litres, with 3.4% protein and 4.25% butterfat
- Milk supplied to Arla Morrisons
- 303ha (750 acres) arable rotation, growing grass, maize and sugar beet, with land let for potatoes and onions
- 10ha (25 acres) let for outdoor pig production
- On-farm anaerobic digester taking slurry, muck and some maize
- 14 HGV lorries used for sugar beet, grain and straw haulage
Reducing waste
Mr Wyatt has agreed a contract with next-door Snetterton Renewable Energy Plant to take straw bales that fail its criteria for quality.
The energy plant has a 43MW power output produced from straw and woodchip.
He sells straw produced on-farm to the energy plant and replaces it with the energy plant’s out-of-spec straw. This is usually straw with too high a moisture content, or missing strings.
Instead of a lorry load of straw being rejected and returned to the farm of origin (even if it contains only one out-of-spec bale), he now dries it and uses it to bed down his cows. This reduces road miles and makes use of an otherwise wasted product.
Straw dryer
The straw is dried in a new barn measuring 66x27m. This includes a 12x27m bay at one end for machinery storage.
At the other end is a Kongskilde Ventus 2400 straw dryer. In-between is an area large enough to store undercover all the straw the farm needs – 3,000t a year for the farm’s 240 dairy cows and youngstock.
A teleporter is used to feed bales onto an eight-bale conveyor belt which moves them towards the dryer. This is repeated three times a day.
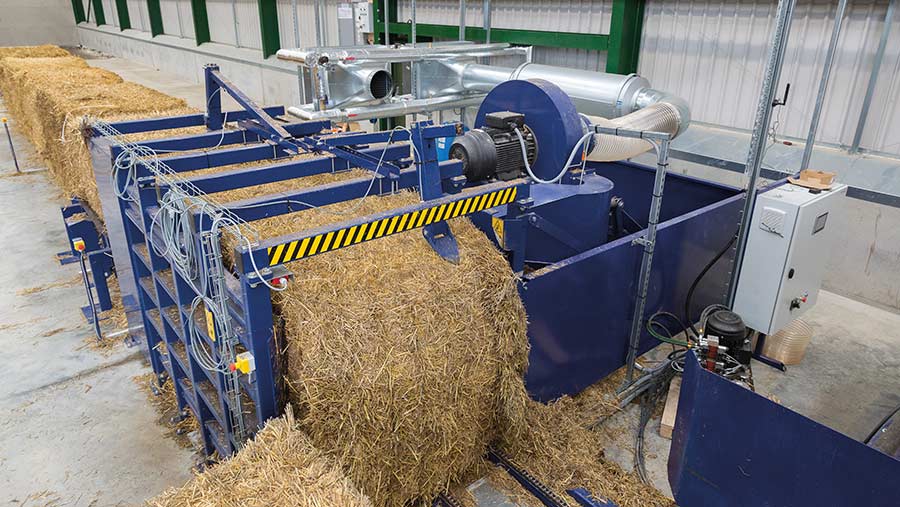
© MAG/Judith Tooth
The straw is dried using heat generated from the on-farm AD plant. The plant, installed in 2016, generates 0.5MW of electricity.
This is enough for all the farm’s needs, with excess sold to the grid.
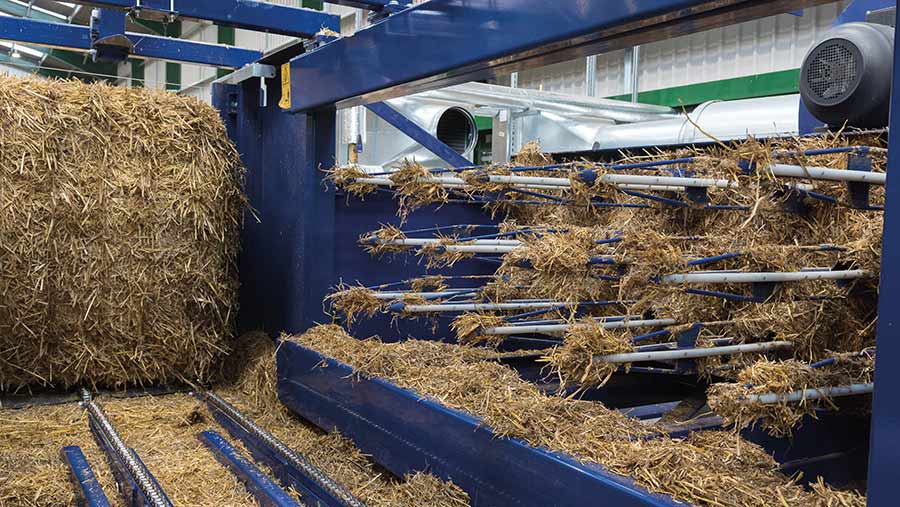
© MAG/Judith Tooth
An underground pipe brings hot water, produced from cooling the engine that runs the AD plant, to the new barn.
Here, it enters a heat exchanger at 86C and the hot air produced is blown by a fan into a tube. From here, it is forced through a series of probes into the straw bale for a pre-determined number of minutes.
The bale is then pushed off the dryer ready for stacking.
So far, the bales are arriving at the farm with an average moisture content of more than 25%.
“We carry out a visual assessment and then take a moisture reading using a hand-held probe,” says Mr Wyatt. “The target for the dried bales is less than 15% moisture, and it’s taking about 45 minutes for each one.”
Dry bedding
Previously, straw had to be stored outside. At times, this meant damp straw had to be used as cow bedding, leading to potential rises in SCCs in the milk.
“Bacteria thrives in a damp environment, and this can contribute to high SCCs,” he says. “Because we run deep-littered yards, we want to bed with straw that’s as dry as possible.”
See also: 4 ways a robotic dairy got mastitis under control
The herd’s current SCC average has been running at 170,000 cells/ml since the straw dryer began operating. The dairy team’s aim is to get this down to 100,000 cells/ml, and it is hoped bedding with consistently dry straw will help reach this target.
Renewable energy
Yards are bedded with the straw daily and mucked out every four weeks. The muck is then fed to the AD plant, along with a mix of maize and crop residues such as sugar beet waste, and any very poor-quality straw.
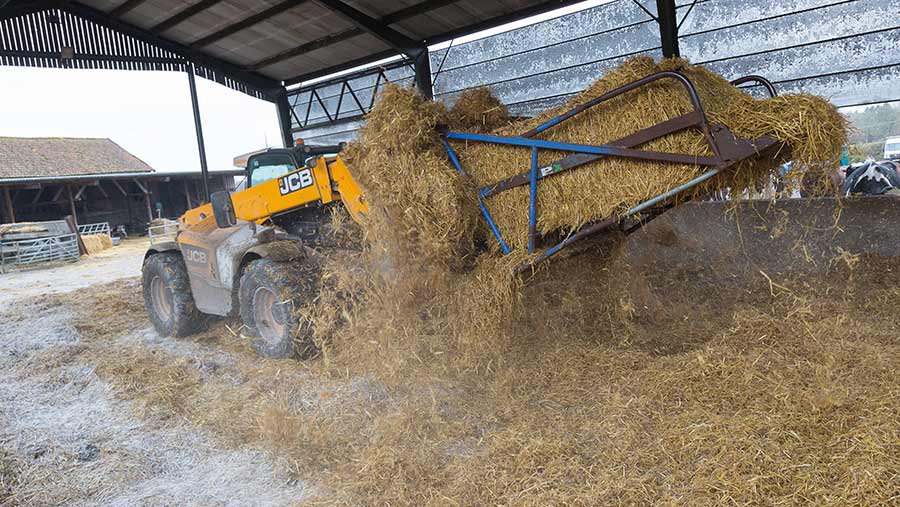
© MAG/Judith Tooth
The system suits the cows and the AD plant. “The cows need to be mucked out regularly and the plant works best with fresh muck because it produces more gas,” says Steve Bailey, who manages the plant.
“The majority of the gas comes from the straw content of the muck. If the straw starts to break down, aerobic – rather than anaerobic – decomposition is taking place,” he says,
“If we were further north or west, we would probably have cow cubicles, but here we have access to straw, so it makes sense to bed with deep litter – which we’ve then used to improve our sandy soils,” adds Mr Wyatt.
“The AD plant isn’t a bolt-on for a bit of cash – it is an integral part of our farming system, and everything rotates around it,” he says.
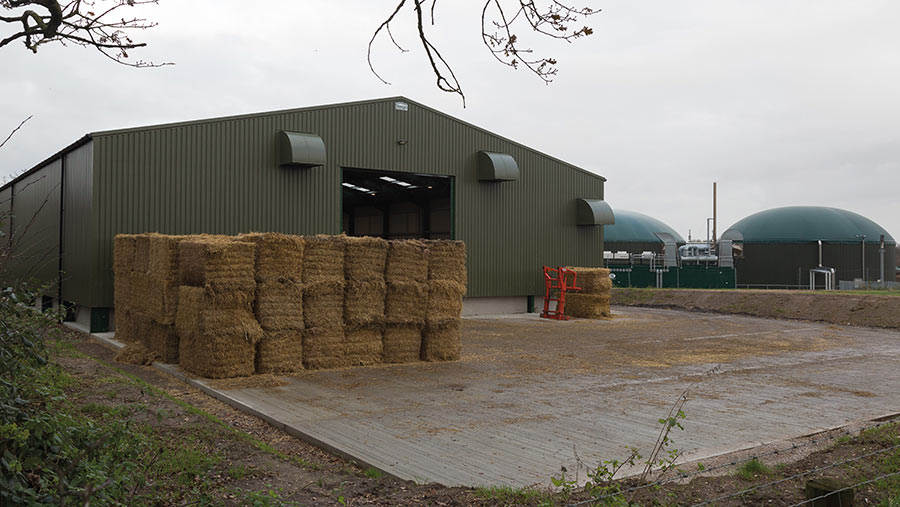
© MAG/Judith Tooth
Fertiliser
Before the AD plant was installed, farmyard manure was tipped in fields and spread. Now it is used to feed the plant, and the resulting digestate is spread instead.
“With the price of fertiliser, I’m very glad I’ve got it,” says Mr Wyatt. “This season, I have bought in one load of 29t, but that’s all. We’ll use dirty water and digestate.”
An umbilical system is used on the fields around the farmyard, while a new tanker will spread digestate on land further away.
Cost
The cost to build the barn and buy and install the straw dryer was £600,000. A grant of £160,000 from the Rural Development Programme for England helped towards the project and two members of staff have been taken on to operate the dryer.