Why LED lighting can improve layer and broiler margins
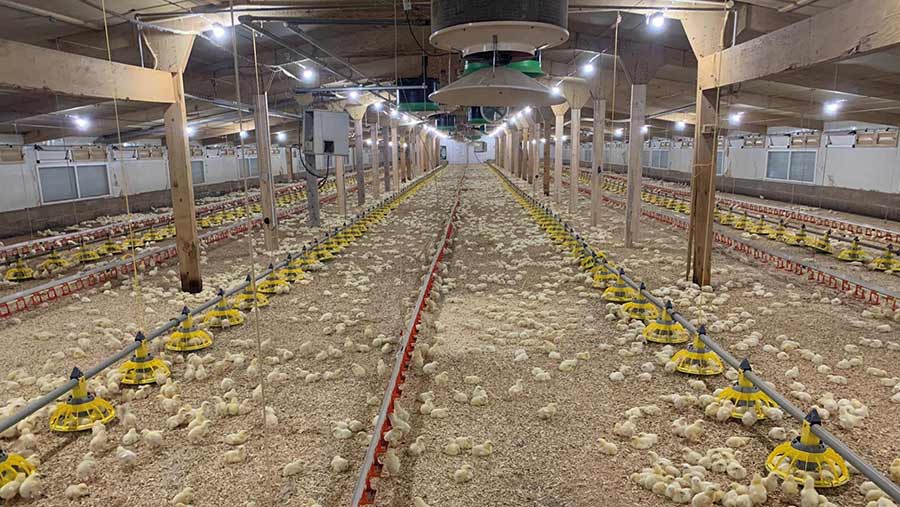
© Greengage Lighting
Research work has shown modern lighting systems can increase layer production by up to 38 eggs a hen and gross margins by 0.87p/kg on broiler units.
But lighting often slips down the list of potential performance inhibitors because flock-keepers assume systems are effective as long as they are functioning.
Correct lighting will stimulate the birds’ natural day/night behaviour in a housed environment, in the following ways:
- Bird placement
- Feed intake
- Water consumption
- Excretion
- Behaviour
- Interaction with other birds
- Performance
One reason for the improvements in these areas is that poultry have a greater sensitivity to colours and vision on the ultraviolet spectrum, explains Greengage Lighting’s Glynn Kent.
See also: A guide on how to improve water quality on poultry units
How much of each colour is present, light intensity, and periods of light will all influence how the birds behave and perform. Getting it wrong can have implications that last the length of the productive cycle.
Light requirements also vary depending on breed, age of bird and system. Broilers perform best with a warm, white light with more wavelengths of blue light keeping birds calm, allowing for better weight gains.
In contrast, layers benefit from a warm, white light with more red, which improves rates of sexual maturity and egg production.
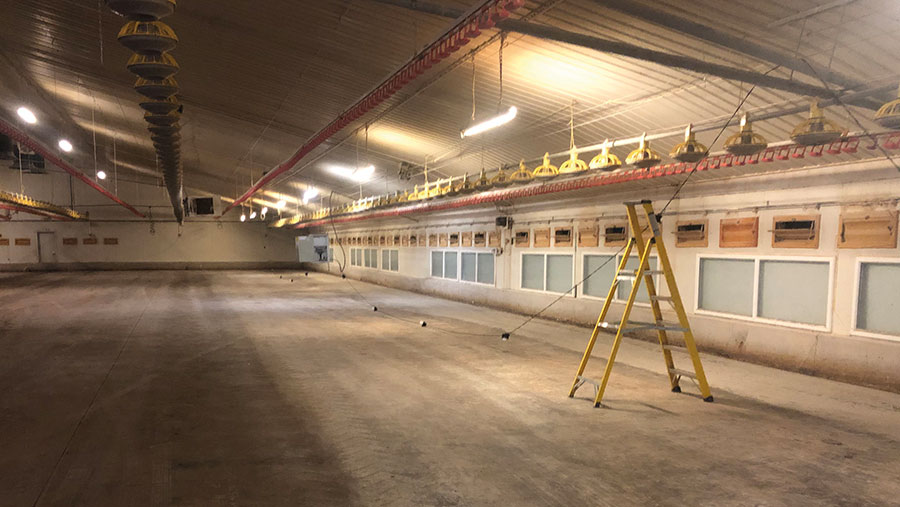
The shed before the new lighting was installed © Greengage Lighting
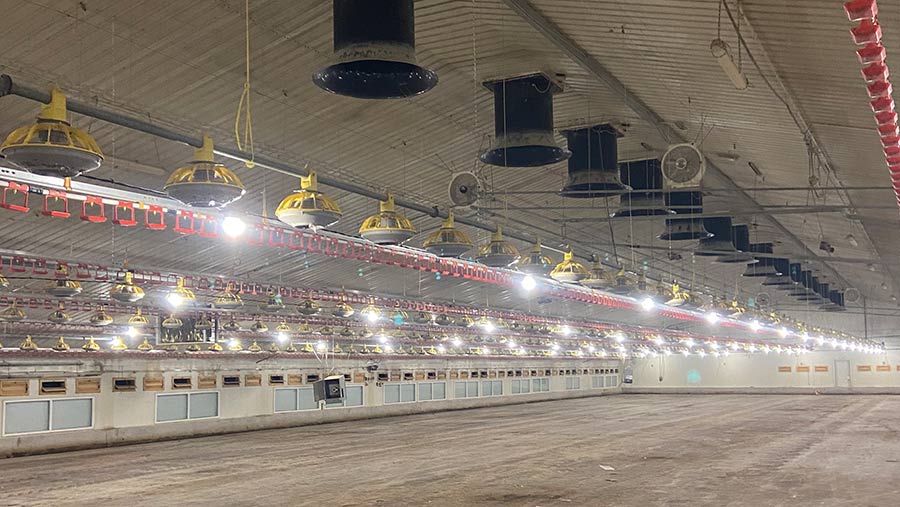
The shed after the new lighting was installed © Greengage Lighting
Conventional lighting
Fluorescent and incandescent lighting are low frequency, producing limited spectrum and light spread with a flickering effect.
This means birds must work harder to navigate their environment, which increases stress and incidences of:
- Skin scratching
- Cannibalism
- Floor eggs
- Excessive water consumption
- Wet litter
Conventional lighting systems have limited dimming ability and require manual inputs at each end of the day.
The running and maintenance cost of older lighting systems is also considerable, with annual bills of ÂŁ1,016 in an average house (see “Comparison of energy use” below).
Additional labour costs are incurred because bulbs are sensitive to dust, ammonia and moisture, and require replacing because of water damage during deep cleaning.
LED lights
Poultry-specific LED lights give a better spread, eliminating dark spots when placed correctly, reducing bird stress.
LED lighting will give the producer better control over settings, allowing automatic and smoother transitions from light to dark.
“In laying systems this is of particular importance to drive the birds up to nest boxes while maintaining underlighting to discourage floor eggs,” Mr Kent points out.
Use of AgriLamp Induction System (Alis) LEDs has seen floor eggs reduced from 7.2% to 3% at peak production.
Labour requirements are also reduced by 90 minutes/day, equating to ÂŁ5,145 of savings in a typical flock.
Energy savingsÂ
Induction lighting uses 90% less energy than conventional lighting, while standard LED technology uses around 50% less.
Installation
LED lighting systems range in price and cost of installation.
- Standard LED system plus installation ÂŁ5,500-ÂŁ6,000, four- to five-day installation
- Induction LED system plus installation ÂŁ8,500-ÂŁ9,000, two-day installation
An electrician will be needed to install standard LED lighting, while an Alis induction LED system requires an electrician only for the control room panel. Farmers should be able to install the lights themselves.
Comparison of energy use |
|||
|
Conventional (fluorescent) |
LED (Beken LED lamp) |
Induction LED (Alis) |
Average house lighting needs |
40x58W bulbs |
40x30W bulbs |
40x11W bulbs |
Energy load |
2.32kW |
1.2kW |
0.44kW |
Average lifetime |
10,000 hours |
50,000 hours |
100,000 hours |
Average yearly operation |
2,920 hours (eight hours x 365) |
2,920 hours |
2,920 hours |
Annual running cost at 15p/kWh |
ÂŁ1,016.16 |
ÂŁ525.60 |
ÂŁ192.72 |
Case study: Shadwell Farm, Clun, Shropshire
Tom Bright and his father, John, upgraded their lighting system in late 2019 – and have seen a uniform 4g increase in chick growth at day seven as a result.
The pair have a 210,000-broiler bird enterprise at Shadwell Farm, and performance has always been a focus alongside high health – with particular attention on chick growth in the first seven days.
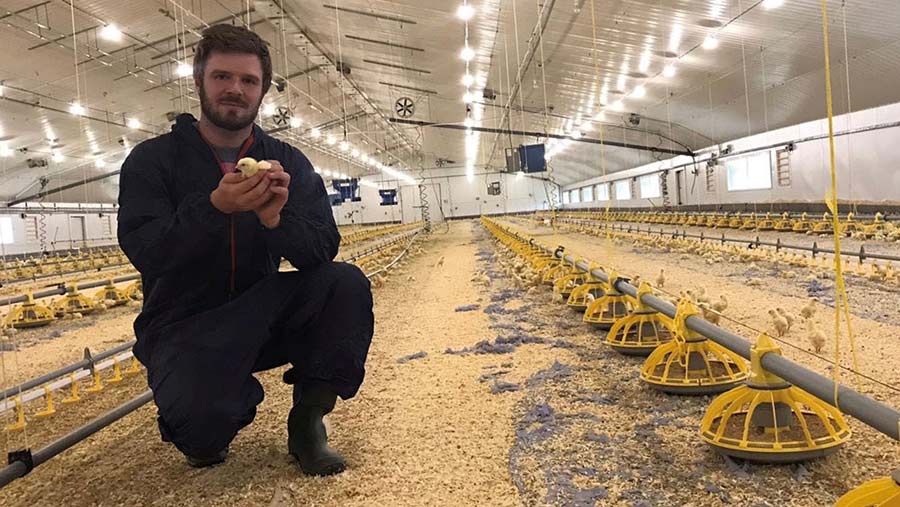
Tom Bright © Shadwell Farm
Farm facts
- 300ha
- 210,000 Ross 308 broilers
- 40-day flock cycle
- 194g: average chick weight at seven days
- Average kill weight of 2,625g
- Thin-out at 32-33 days
- Hook2Sisters contract: Chicks, feed, collection
“Research shows that every extra gram of growth in the first seven days roughly translates to 5-6g at the end of the crop,” explains Tom.
“It’s really important to get crop fill in the first 24 hours, with consistent feed intakes to improve end weights and uniformity.”
Challenge
In 2019, the Brights were achieving an average chick weight of 190g at day seven but with too much variation seen in the shed.
Assessing the sheds and observing the birds, they identified lighting as a limiting factor. “The placement and output of the conventional lights didn’t allow for even lighting, interfering with the natural bird behaviour,” explains Tom.
Each shed had 45 conventional HF fluorescent strip lights, controlled by a manual time dimmer – costing about £4,200 for the system and installation, with running costs of £250.56 a flock or £1,753 annually.
“In one of the sheds, a corner and one long side was particularly problematic – we would see the chicks congregating in these darker areas, leading to variable feed intakes and growth rates.”
Lighting swap
In autumn 2019, they decided to retrofit one of their five sheds with Alis induction LED lighting, after assessing shed design and lighting placement to eliminate dark spots.
The result was 140 wide-angled lamps controlled by a dusk-to-dawn digital dimmer, allowing greater control over dimming periods, lux output and spectrums.
“After installation we saw a visual improvement – the whole floor space was evenly covered by light, with brightness equal at both ends of the shed and no flickering,” says Tom.
“Most importantly, we saw an immediate improvement at chick placement, with a lot less clustering and chicks feeding more off the chick paper.”
Return on investment
On an individual flock basis, growth rates to day seven have increased by up to 8g a chick, with an average 4g increase over all flocks produced under new lighting. This translates to a 25g improvement at final kill, generating 1.87p a bird, or ÂŁ638.14 a flock, extra income.
The Brights have also seen their energy use drop by about ÂŁ719.04/shed a year.
The system took two days to install and cost ÂŁ8,800/shed. And the return on investment is strong: ÂŁ5,179.02/shed based on improved performance and energy savings, ensuring payback in under two years.
How the numbers stack up at Shadwell Farm |
||
 |
Conventional HF fluorescent tubes |
Alis LEDs |
Average house lighting needs |
45x58W |
140x11W |
Energy load |
2.61kW |
1.54kW |
Average lifetime |
10,000 hours |
100,000 hours |
Average hours of use per 40-day flock |
640 hours (16 hours/day x 40 days) |
640 hours |
Chick placement per shed |
35,000 |
35,000 |
Mortality (birds per flock) |
875 |
875 |
40-day running cost at 15p/kWh |
ÂŁ250.56 |
ÂŁ147.84 |
Total annual hours use |
4,480 hours |
4,480 hours |
Annual energy cost for lighting (seven flocks per year) |
ÂŁ1,753.92 |
ÂŁ1,034.88 |
Average chick weight at seven days |
190g |
194g |
Average kill weight |
2,600g |
2,625g |
Financial gain |
– |
1.87p/bird = ÂŁ638.14 per flock |
Initial investment |
£2,400 plus £1,800 install |
 £6,700 plus £2,100 installation |
Annual savings from bird performance and energy reduction |
–Â |
ÂŁ5,179.02 |
Return on investment |
 – |
Less than two years |
Source: Greengage Lighting and Shadwell Farm |