Why a poultry and arable unit uses ‘circular feeding’
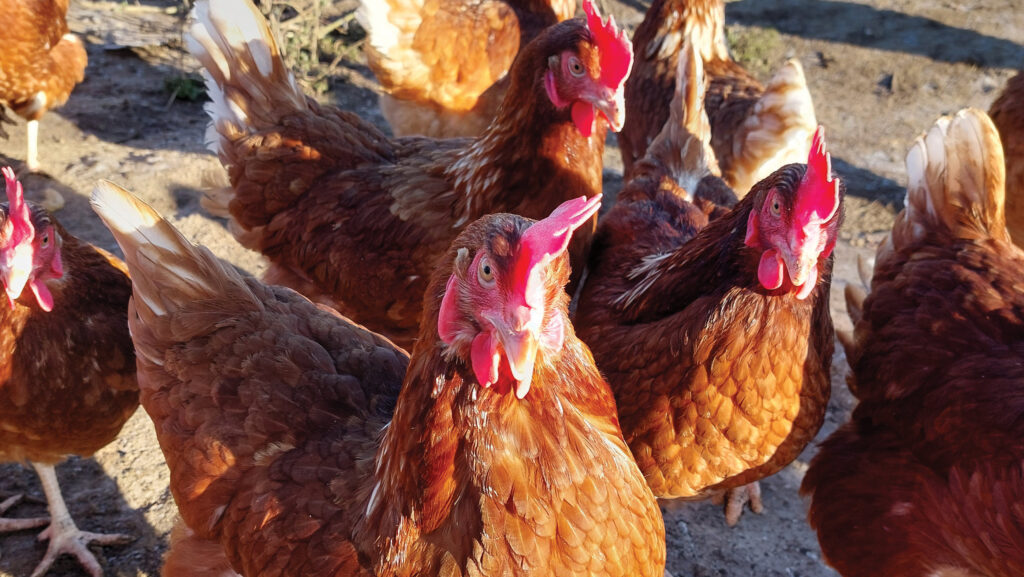
Poultry and arable enterprises complement each other well at Nun Monkton Farm, near York, where the Throup family have farmed for nearly 40 years.
“Everything we grow on the arable side is fed back to the chickens. We have a mill, which adds value to the arable operation, while allowing us to home-mill feed.
“There is also a reduced cost when it comes to road haulage because it’s all done on the farm.”
See also: How nutraceuticals can aid poultry nutrition and health
David’s parents, Stephen and Tricia, and his uncle and aunt, David and Jenifer, are all active in the family business.
His brother John runs the 486ha (1,200-acre) farm’s 300-cow dairy, while their cousin Andrew runs the arable enterprise, and his brother James oversees all the enterprises.
“We all get along because we all have our own enterprises,” says David.
Farm facts: Nun Monkton Farm, near York
- Poultry, dairy and arable enterprises
- 486ha
- 78,000 Hy-Line brown free-range hens across three sites
- Morrisons and Chippendale contract
- 300 milking cows, five milking robots, with milk supplied to Arla
- Arable rotation of wheat, barley, oats and oilseed rape, with grassland in the rotation for the dairy cows
The family first branched into free-range egg production in 1998.
“The first shed was a free-range 9,000-bird flat deck system made up of nesting boxes and slatted floors; this was considered to be large at the time,” he says.
“We packed eggs by hand without any automation.”
This has since developed into three sites with multi-tier systems housing 26,000 birds in each, producing 60,000 eggs/day.
Mortality averages 4% and age at depopulation is 76-78 weeks, but David is aiming for 80 weeks.
“This requires getting the basics right, from water to feed quality. Routine worming and breed genetics help too – having a strong, robust bird to start with,” he says.
Until 2023, the family were also rearing pullets, however, it was becoming difficult to manage the site with staffing, and further investment in infrastructure was becoming necessary, says David.
“Pullet rearing gave us control of the birds from day one, but more recently we have had Country Fresh Pullets rearing for us and the quality has been good.
“We decided to focus on the core business of eggs; we weren’t big enough to make it viable to continue as pullet rearers,” he explains.

© MAG/Shirley Macmillan
Nutrition
When it comes to feeding the poultry, a ration including home-grown wheat, barley and oats is formulated by a nutritionist and mixed in the home mill.
“I can’t do the medicated feed myself, which is a challenge, but the concept of circular feeding works very well for us.
“We grow 70% of the ration on the farm – the only crop that leaves the farm is oilseed rape,” he says, adding that none was drilled in 2024 after disappointing yields from the previous crop.
David only buys in soya, minerals, sunflower, soya oil and limestone, allowing almost complete control over the feed.
“We don’t have to worry about running out of feed, and we can tailor the ration to what we grow.
“For example, we have added oats to the ration, which a lot of commercial mills won’t do because they’re difficult to transport – but they’re a very good source of fibre.”
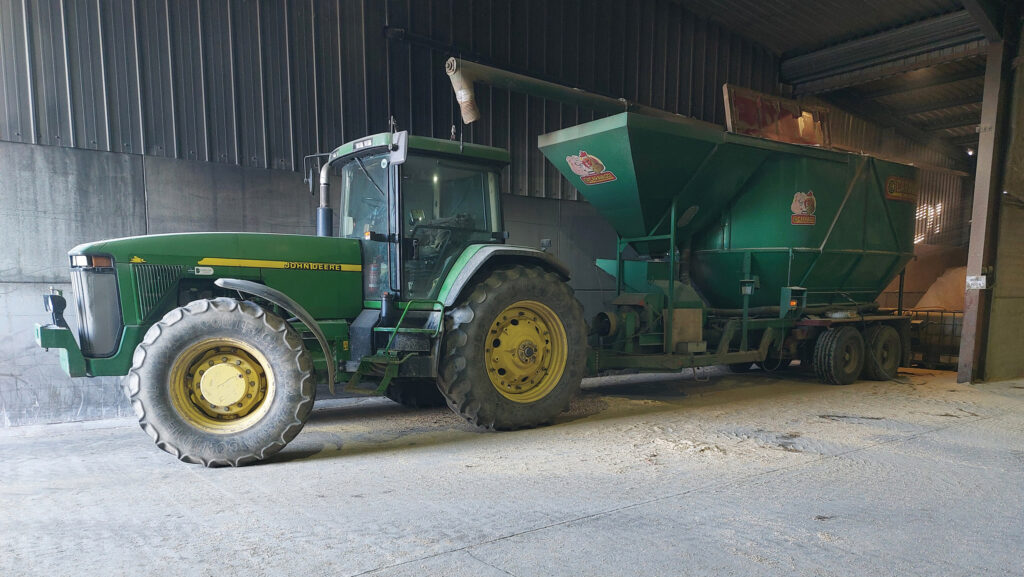
© MAG/Shirley Macmillan
Carbon footprint
David has used Eggbase to calculate the poultry enterprise’s carbon footprint. This stands at 1.69kg of carbon dioxide equivalent/kg egg, despite using soya.
“Unfortunately, there isn’t a market for net-zero eggs at the moment, but I have done a lot of modelling to understand our emissions, and we have offset a lot through trees and renewables,” he explains.
Completing the circular system, the poultry manure goes onto the arable ground.
“Using manure has saved us up to 50% on fertiliser in some areas. We sample all of the manure, so we know exactly what we’re dealing with.”
Although there is an opportunity to use the straw from the arable enterprise as bedding, David has opted for wood shavings instead.
“It’s easy for us to handle and manage, with low risks to biosecurity,” he explains.
“We don’t want to potentially be bringing in outside infections with straw – particularly with bird flu being such a risk.”
Manure studies
David recently completed a Nuffield scholarship investigating poultry manure, which took him to Austria, Slovenia, New Zealand and the Netherlands.
“The main reason for choosing the subject is because knowing what to do with manure can be difficult,” he says, adding that the farm’s soils have been affected by repeated manure applications.
“After 25 years of spreading poultry manure, we have high phosphorus in the soil, so we regularly soil sample, and avoid spreading phosphate in high-phosphate areas. I’m also looking into exporting the manure.
“I’ve tried mixing it with straw and gypsum to make it a stable product, but I want to make it a transportable product [for selling to other farmers] because it’s a very good source of nitrogen.”
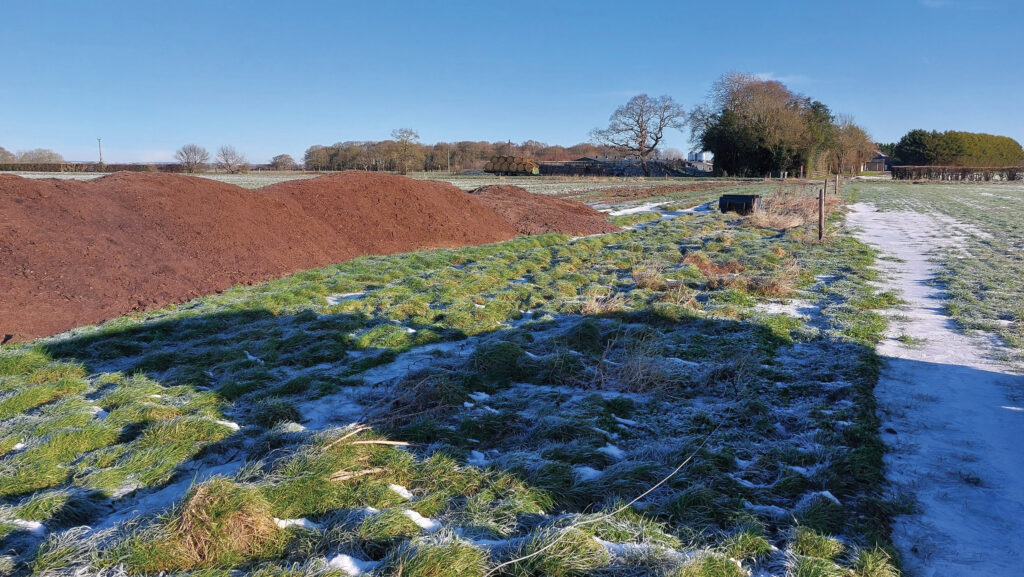
© MAG/Shirley Macmillan
This means drying the manure to 70% from 30% dry matter when it comes out of the sheds (twice weekly, year round). Drying it will reduce any smell, retain the same nutrients and reduce volume by 25%, he explains.
His Nuffield studies inspired him to look for ways to add value to the manure and create a cost-effective, on-farm approach for easier manure handling.
He plans to make use of the old pullet-rearing shed, where he is making a drying floor for this purpose.
“Any equipment I have looked into either to dry or compost soon adds up, and I struggle to justify the cost as it only works on a much larger scale. I want an on-farm solution that I would be in control of.”
Renewable energy
The farm has made significant investment in renewable energy, with 30kW of solar panels on one poultry site, which provides most of the energy required for daytime running.
Solar power lends itself particularly well to the poultry enterprise, says David.
“When it’s hot, we need more fans running, and we use more energy in the summer than the winter.”
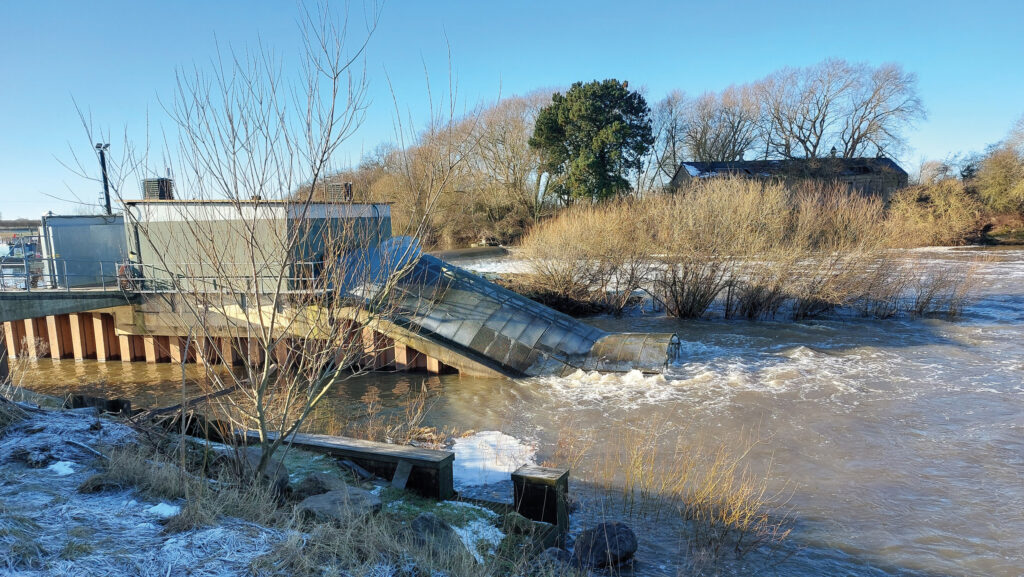
© MAG/Shirley Macmillan
A hydro-electric plant generates power from the River Ouse to provide 80% of the energy demand of the other two sites.
“The only issue with it is when there is not enough water in the river or when it’s flooded – that’s why they are only 80% powered by hydroelectric.”
He also plans to use a biomass boiler, previously used for heating the sheds for pullet rearing, to dry manure.
David is constantly looking to improve the system. “I have recently invested in automated pallet stackers to take the heavy lifting out of the job,” he says.
“I’m always aiming to become more efficient and make life easier.”
Manure results
Nutrient results from poultry manure with dry matter of 29% were taken from muck belts at Nun Monkton Farm in spring 2024:
- Nitrogen 14.39
- Phosphorus 7.21
- Potassium 6.87
- Magnesium 1.92