What to consider before erecting a new poultry shed
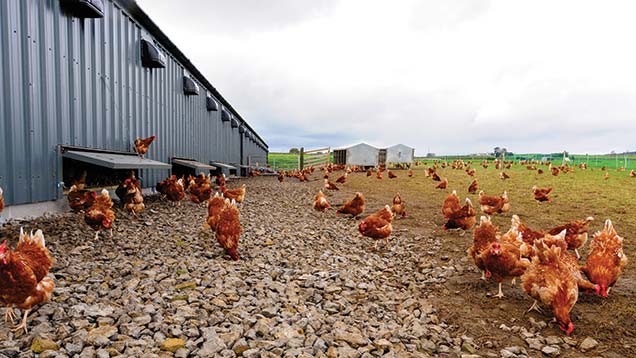
One of the foremost considerations with any building project is “future-proofing”, according to Simon Pelly of County Durham-based builder, Simpson and Allinson.
“When we arrive on site, a producer will usually have a fairly fixed idea of building location. Our job is to play devil’s advocate and look for any potentially negative aspects of his choice.
“In five or 10 years’ time, there may be a requirement to extend the shed, or the surrounding yard. Correct positioning is important, as it can be very expensive to accommodate any changes in the future.
“This is also the time to look at what is below and above the building that may influence location, including drainage and power, as well as the proximity of archaeological features, gas mains and overhead power cables.”
Design
The building design should be based around the mechanical equipment that will need to be housed, especially when it comes to layer sheds.
“All too often, the building is put up first and it is then a question of making the equipment fit inside. This is not the approach taken by many other industries, but for some reason it is a fairly common occurrence in agriculture,” says Mr Pelly, whose company is involved in a diversity of construction projects.
“The company supplying and installing the equipment should be brought into the discussion at an early stage; they are experts in their field and will be able to make a valuable contribution when decisions are being made. Once the bird stocking rate has been calculated, the building dimensions can be finalised.”
Planning
The next stage is to apply for planning permission, bearing in mind that specific regulations apply to the poultry industry.
While there is no longer any rule forbidding the siting of buildings less than 400m from residential housing (except for those where no planning permission is required), sufficient separation distance is still needed to comply with permitting requirements for odour and noise.
Applicants are frequently asked to submit proposals, detailing plans for the management and disposal of poultry manure generated by the unit.
See more: Poultry producers struggle to get planning permission
In cases where part of the building is to be sectioned off as a working area for egg packing, for example, further rules will apply, if the intention is for staff to work in the building for six or more hours a day.
Many poultry producers are looking to save money on energy bills and solar roof panels are growing in popularity. Mr Pelly urges anyone who is interested in this option to include it as part of the building proposal, as installing the panels retrospectively will be much more expensive.
The collection of rainwater from roof areas is another recent trend, but the water must be treated before it can be given to the birds to drink, although it is suitable for use in power washers or filling crop sprayers, he says.
He advises producers against taking action before planning permission has been granted. However this interim period offers an opportunity to obtain building quotations.
Tendering
“Most producers will commission three quotations and if all the companies are competitive and competent, these should not vary widely. It is important to scrutinise each financial breakdown, to ensure that like is being compared with like.
“References can be obtained from previous clients and the proposed structure must carry the CE mark. This outlines a minimum standard and buildings without this mark are illegal. The supplier should also be a member of RIDBA – the Rural and Industrial Design and Building Association.”
Once a quotation has been selected, it is a good idea to meet again with the builder.
“As building specialists, we are asked to put forward a large number of quotations each year and there is a limit on the amount of time we can allocate to this process,” explains Mr Pelly. “However once our price has been accepted, we can look at the project in more detail. In some instances, this will highlight areas where potential savings might be made.”
The selected building firm should be given as much notice as possible, in order for the project to run efficiently, he stresses.
“The more time we have to do a job, the more opportunity we have to find savings or look at alternatives that can improve the long-term operation of the building. Most producers have the expertise and the equipment to carry out some of the preparation work themselves, which can reduce costs. This can include stripping out topsoil and creating the stone base.
“Putting up a new building involves considerable expense and each stage must be managed carefully, if the project is to be a success and last for many years into the future,” says Mr Pelly.